Tagged: 16.2, General, mechanical-apdl, structural-mechanics
-
-
January 25, 2023 at 7:34 am
FAQ
ParticipantRegarding the differences between SOLID45 and SOLID185, the main difference is element formulation. As you may know, we encounter 2 main ‘locking’ type of problems with lower-order continuum elements: shear locking and volumetric locking. A) Shear locking is a function of the geometry, and it occurs because lower-order bricks cannot ‘bend’ since they have linear sides. Hence, parasitic shear strains develop, and the traditional formulation is too stiff in bending. B) Volumetric locking is a function of the material, and it occurs when the effective Poisson’s ratio approaches 0.5 (nearly-incompressible). Since hydrostatic_press = volumetric_strain * bulk_modulus, if volumetric_strain -> 0, then bulk_modulus -> infinity. This is a problem for higher- and lower-order elements when dealing with nearly-incompressible materials (e.g., hyperelasticity or plasticity when plastic strains >> elastic strains). To alleviate these 2 problems, we have different formulations which either reduce the integration points (hence relaxing the internal constraints) or add extra degrees of freedom. 1) Simplified Enhanced Strain or Extra displacement Shapes (a.k.a. Incompatible Modes): This is the default formulation for SOLID45 (KEYOPT(1)=0 and KEYOPT(2)=0). This is set on SOLID185 with KEYOPT(2)=3. The idea here is that we add internal ‘bending’ type of DOF to make the element more flexible in bending to alleviate shear locking. This type of formulation does not directly address volumetric locking. 2) Uniform Reduced Integration: This can be set with SOLID45 (KEYOPT(2)=1) and SOLID185 (KEYOPT(2)=1). This makes volumetric and deviatoric integration points from 2x2x2 to 1. This basically reduces the internal constraints in the element, but the problem is that ‘hourglassing’ can occur since there are some zero-energy modes that may be excited by point loads or point contact. This addresses shear and volumetric locking but generally requires a finer mesh to preventhourglassing and to capture stress gradients accurately since it only has 1 integration point per element for stress/strain calculations. 3) B-bar (a.k.a. Selectively Reduced Integration): This is NOT available with SOLID45. This is the default behavior for SOLID185. This addresses volumetric locking but does *not* address shear locking. The idea here is that for volumetric term, 1 integration point is used (to help reduce volumetric locking). However, for deviatoric term, 2x2x2=8 integration points are still used, so it does not address shear locking. 4) Enhanced Strain: This is NOT available with SOLID45. This is available for SOLID185 with KEYOPT(2)=2. The idea here is that it is like incompatible modes (#1 above), but in addition to extra internal ‘bending’ DOF, we also add some internal DOF to alleviate volumetric locking, so this addresses both shear and volumetric locking. Just like with #1 above, these are internal DOF. They are condensed out during element matrix formulation, so the user never sees these extra DOF. 5) Mixed u-P: This is NOT available for SOLID45. This is available for SOLID185 with KEYOPT(6)=1 and is used in conjunction with any of the above 4 formulations. This addresses volumetric locking for fully- or near-incompressible materials. The above items #2, 3, and 4 only address nearly-incompressible cases. If the effective Poisson’s ratio is 0.5, the above formulations cannot deal with this since volumetric strain = 0, so bulk modulus would be infinite. Hence, this Mixed u-P formulation adds an extra DOF (hydrostatic pressure), so hydrostatic pressure is calculated directly as a retained DOF rather than calculated from volumetric strain. The difficulty with this option is that the sparse direct solver must be used because of ill-conditioning of the matrix (and possibly zeros along the diagonals). The above formulations assume use of hexahedral elements, so the formulations such as Enhanced Strain are not applicable when elements are in tetrahedral form. Lower-order tetrahedral elements will *always* be too stiff (constant-strain tetrahedra), whether it is SOLID45 and SOLID185, and should always be avoided. As one can see, SOLID185 includes all of the SOLID45 element formulations, but it has additional formulations, especially those to address volumetric locking. That is one reason why SOLID185 can be used with a wide range of nonlinear constitutive models, including hyperelasticity, viscoelasticity, in addition to plasticity and viscoplasticity. In general, if one is dealing with thin geometry with some plasticity, I would recommend using Enhanced Strain to alleviate both shear and volumetric locking. (You can also set SOLID185 to Simplified Enhanced Strain to make it act similar to SOLID45 default option.) Note that the default SOLID185 behavior is B-Bar, so it will be susceptible to shear locking. Similar arguments to the above apply for comparisons of PLANE42 and PLANE182. Note that ANSYS also has the ETCONTROL command to let ANSYS decide which element formulation to use. This is only applicable for the 18x elements, not SOLID45.
-
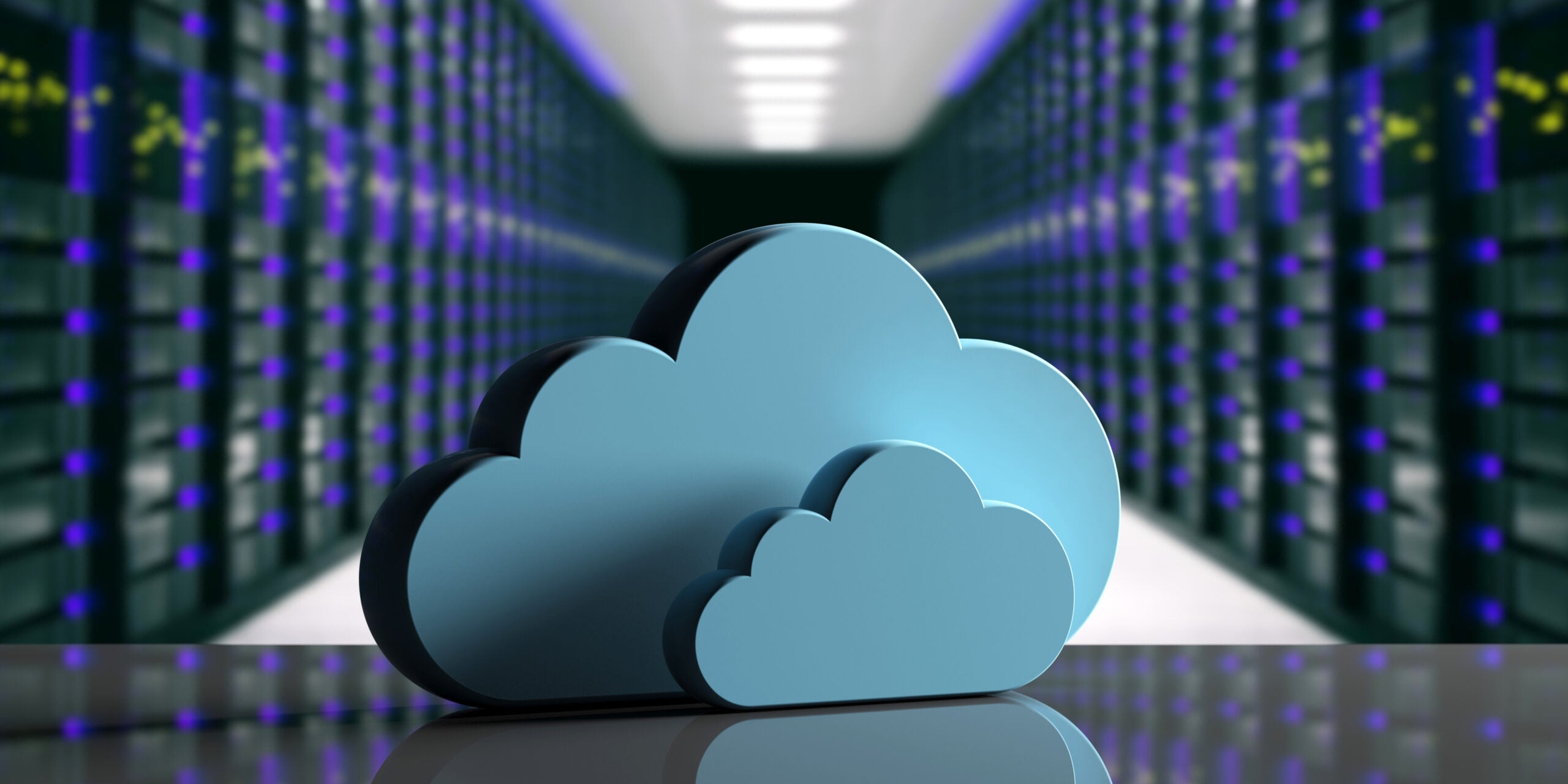
Introducing Ansys Electronics Desktop on Ansys Cloud
The Watch & Learn video article provides an overview of cloud computing from Electronics Desktop and details the product licenses and subscriptions to ANSYS Cloud Service that are...
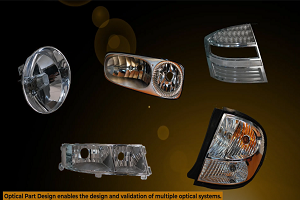
How to Create a Reflector for a Center High-Mounted Stop Lamp (CHMSL)
This video article demonstrates how to create a reflector for a center high-mounted stop lamp. Optical Part design in Ansys SPEOS enables the design and validation of multiple...
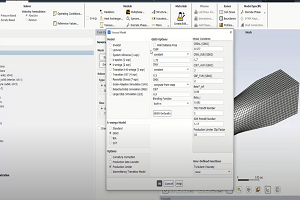
Introducing the GEKO Turbulence Model in Ansys Fluent
The GEKO (GEneralized K-Omega) turbulence model offers a flexible, robust, general-purpose approach to RANS turbulence modeling. Introducing 2 videos: Part 1Â provides background information on the model and a...
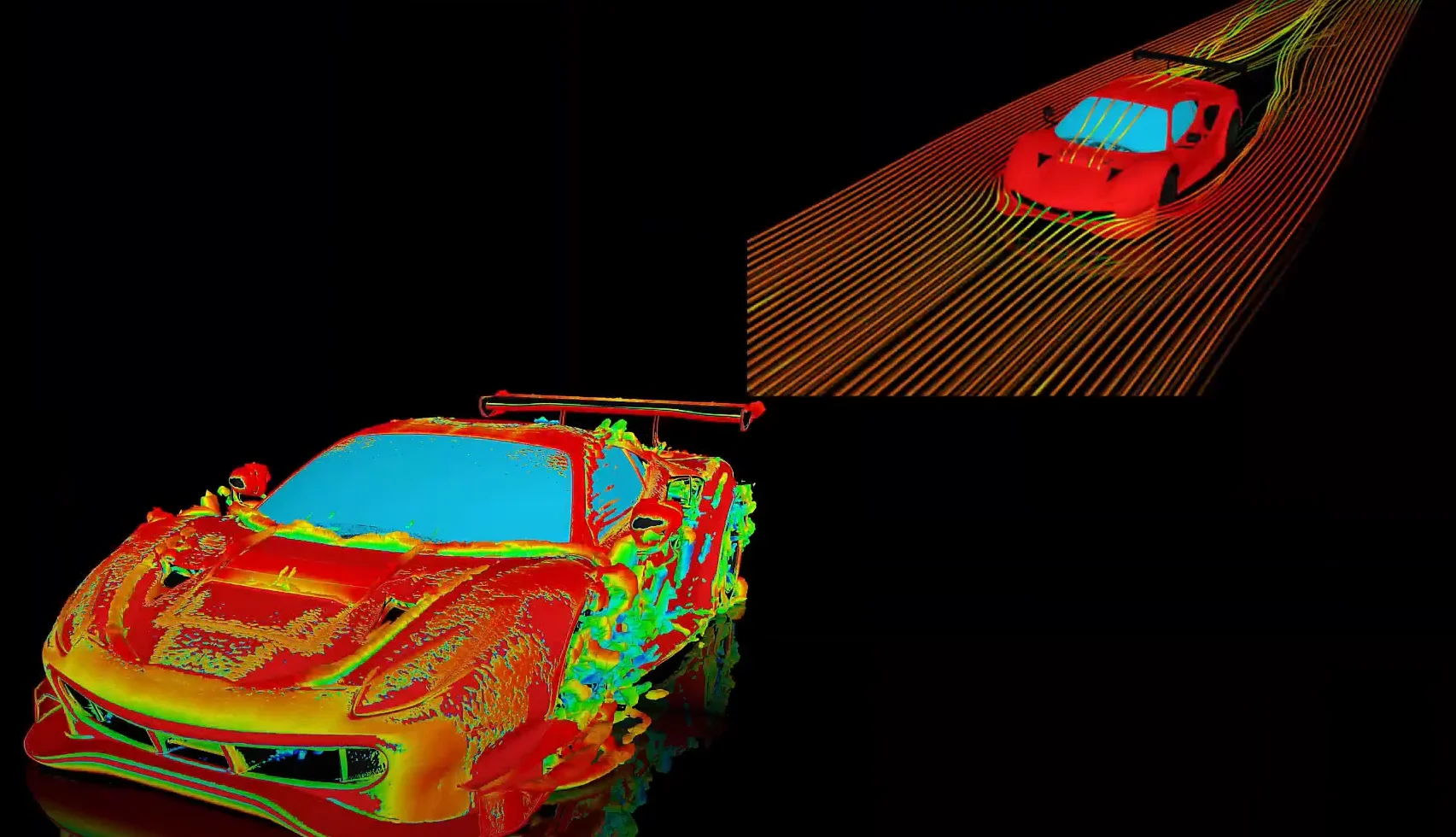
Postprocessing on Ansys EnSight
This video demonstrates exporting data from Fluent in EnSight Case Gold format, and it reviews the basic postprocessing capabilities of EnSight.
- How do I request ANSYS Mechanical to use more number of cores for solution?
- How to restore the corrupted project in ANSYS Workbench?
- How to deal with “”Problem terminated — energy error too large””?”
- Contact Definitions in ANSYS Workbench Mechanical
- There is a unit systems mismatch between the environments involved in the solution.
- How can I change the background color, font size settings of the avi animation exported from Mechanical? How can I improve the resolution of the video?
- How to transfer a material model(s) from one Analysis system to another within Workbench?
- How to obtain force reaction in a section ?
- How to change color for each body in Mechanical?
- How to resolve “Error: Invalid Geometry”?
© 2025 Copyright ANSYS, Inc. All rights reserved.