-
-
March 17, 2023 at 8:59 am
FAQ
ParticipantIn LS-DYNA, contact energies are reported in the SLEOUT file. Therein, four different values can be found: 1) slave energy (SE) 2) master energy (ME) 3) frictional energy (FE) 4) sum of slave/master and frictional (SoSMF) = SE + ME + FE The ‘Sliding Energy’ included in the GLSTAT file equals the sum of slave, master and frictional energy (SoSMF) from the SLEOUT file. Note: The frictional energy is included in the sum of slave/master energy. If friction is defind, e. g. in the *CONTACT_… via FS and FD, the resulting energy can be found in the database variable frictional energy (FE). Thus, one gets the energy needed to prevent penetration between the contact partners by subtracting the frictional energy from the sum of slave/master energy (SoSM). In the absence of friction the slave and master side energies should be close in magnitude but opposite in sign. The sum of slave/master energy (SoSM) should equal the stored energy. Positive contact energy: When friction is included in a contact definition, positive contact is to be expected. Friction SHOULD result in positive contact energy. In the absence of friction, you would hope to see a small net contact energy (net = sum of slave side energy and master side energy). “Small” is a matter of judgement — 10% of peak internal energy might be considered acceptable for contact energy in the absence of contact friction. Negative contact energy: Abrupt increases in negative contact energy may be caused by undetected initial penetrations. Care in defining the initial geometry so that shell offsets are properly taken into account is usually the most effective step to reducing negative contact energy. Refer to sections 23.8.3 and 23.8.4 in the LS-DYNA Theory Manual (May 1998) for more information on contact energy. Negative contact energy sometimes is generated when parts slide relative to each other. This has nothing to do with friction. I’m speaking of negative energy from normal contact forces and normal penetrations. When a penetrated node slides from its original master segment to an adjacent though unconnected master segment and a penetration is immediately detected, negative contact energy is the result. If internal energy mirrors negative contact energy, i.e., the slope of internal energy curve in GLSTAT is equal and opposite that of the negative contact energy curve, it’s possible that the problem is very localized with low impact on the overall validity of the solution. You may be able to isolate the local problem area(s) by fringing internal energy of your shell parts (Fcomp > Misc > internal energy in LS-PrePost). Hot spots in internal energy usually indicate where negative contact energy is focused. If you have more than one contact defined, the sleout file (*DATABASE_SLEOUT) will report contact energies for each contact and so the focus of the negative contact energy investigation can be narrowed. Some general suggestions for combating negative contact energy are as follows: A) Eliminate initial penetrations (look for Warning in messag file). B) Check for and eliminate redundant contact conditions. You should NOT have more than one contact definition treating contact between the same two parts or surfaces. C) Reduce the time step scale factor. D) Set contact controls back to default except set SOFT=1 and IGNORE=2 (Optional Card C). E) For contact of sharp-edged surfaces, set SOFT=2 on Optional Card A. SOFT=2 is also referred to as segment-based contact and so is not applicable to any NODE_TO_SURFACE type contacts. Two important companion variables to SOFT=2 are SBOPT and DEPTH. Two important companion variables to SOFT=2 are SBOPT and DEPTH. SBOPT: Unless sliding between surfaces is prevalent, set SBOPT=3. When sliding is prevalent, set SBOPT=5. DEPTH: DEPTH=13 or 23 is recommended unless shell edge-to-edge contact must be considered, in which case set DEPTH=25 or 35. Please note that SOFT=2 contact carries some additional expense as compared to SOFT=0 or 1, particularly using nondefault values of SBOPT or DEPTH.
-
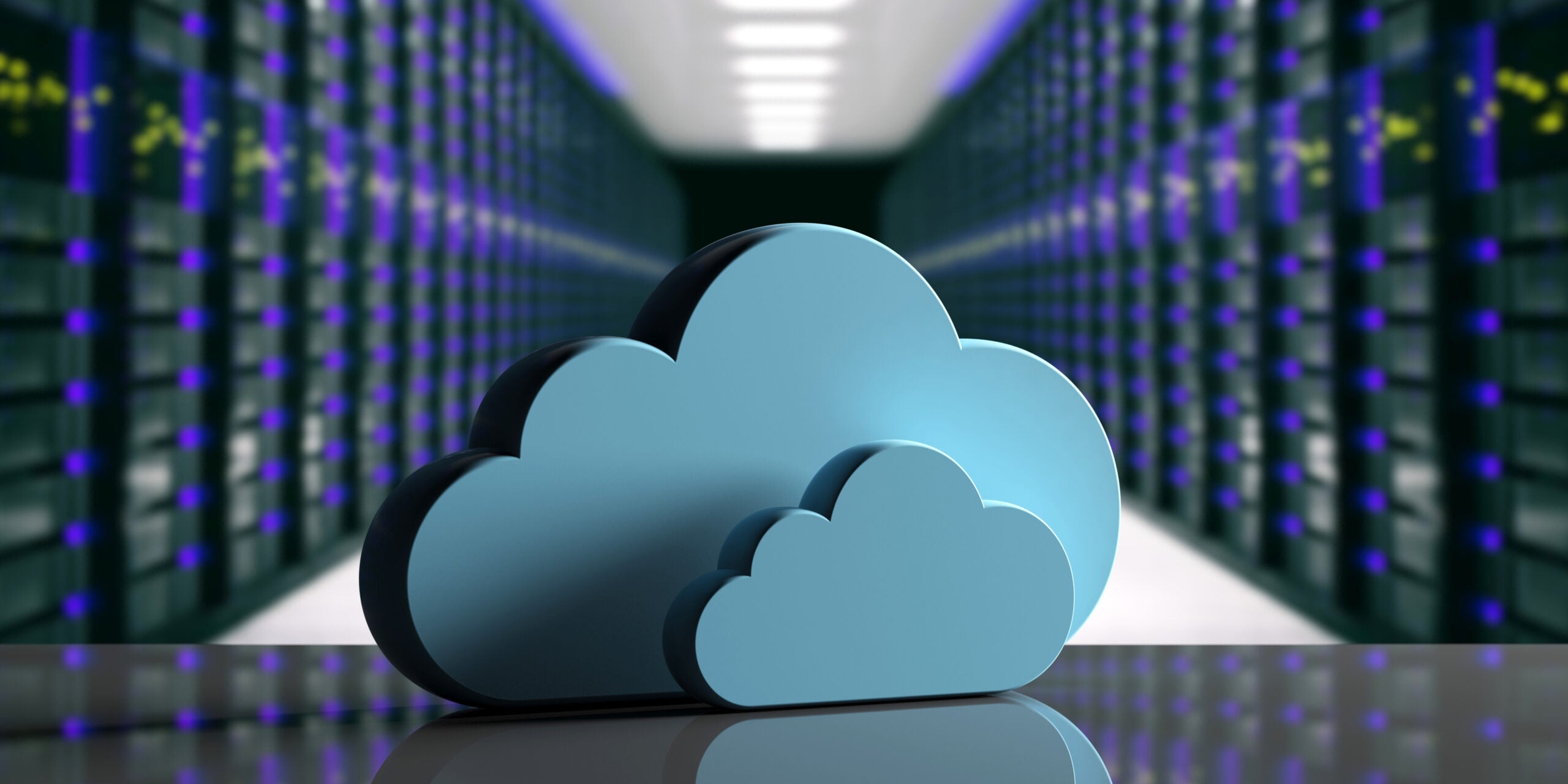
Introducing Ansys Electronics Desktop on Ansys Cloud
The Watch & Learn video article provides an overview of cloud computing from Electronics Desktop and details the product licenses and subscriptions to ANSYS Cloud Service that are...
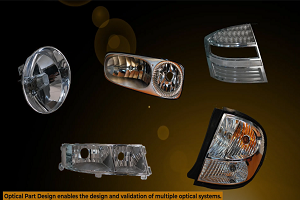
How to Create a Reflector for a Center High-Mounted Stop Lamp (CHMSL)
This video article demonstrates how to create a reflector for a center high-mounted stop lamp. Optical Part design in Ansys SPEOS enables the design and validation of multiple...
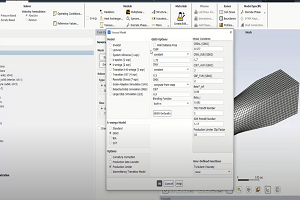
Introducing the GEKO Turbulence Model in Ansys Fluent
The GEKO (GEneralized K-Omega) turbulence model offers a flexible, robust, general-purpose approach to RANS turbulence modeling. Introducing 2 videos: Part 1 provides background information on the model and a...
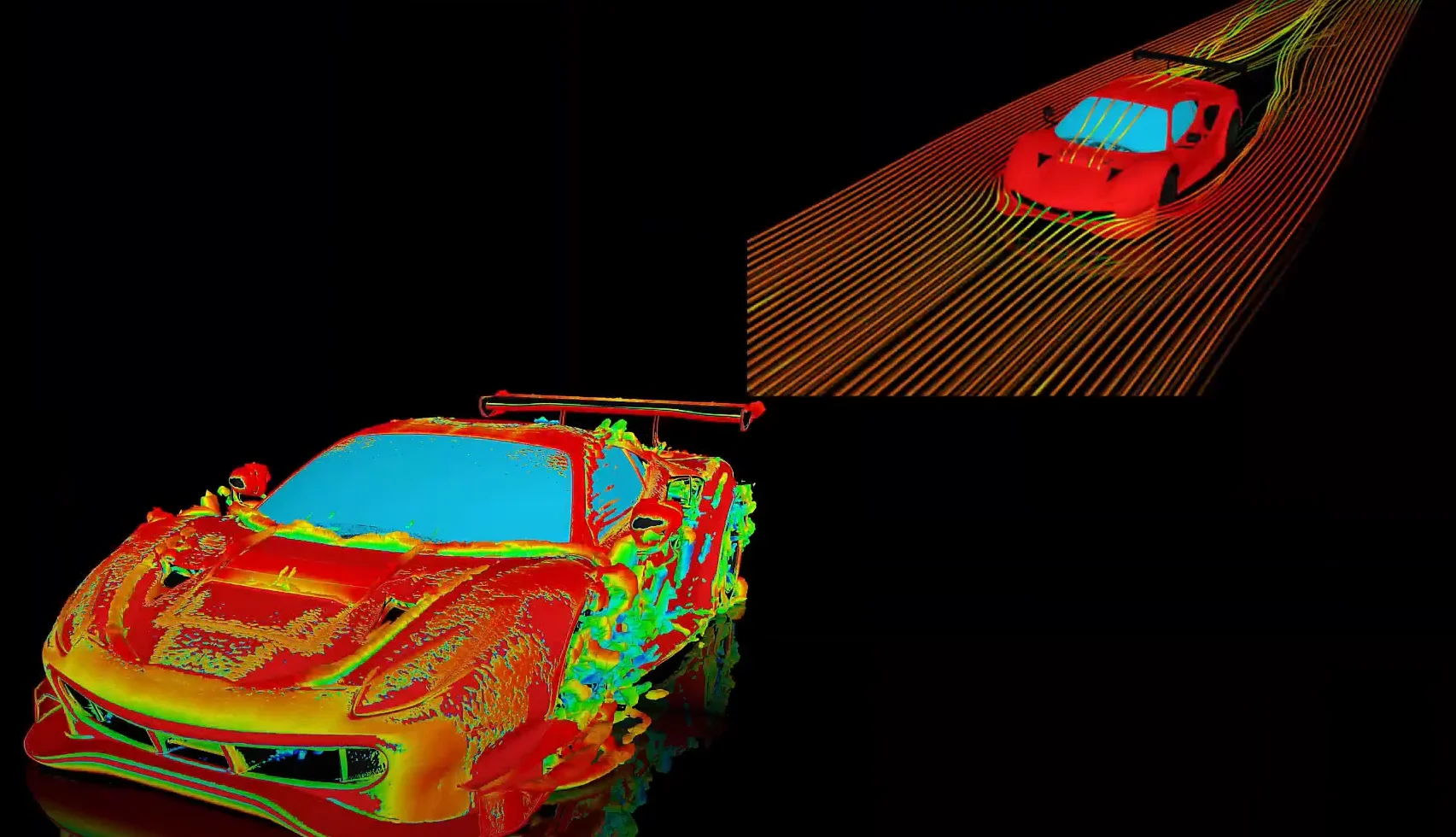
Postprocessing on Ansys EnSight
This video demonstrates exporting data from Fluent in EnSight Case Gold format, and it reviews the basic postprocessing capabilities of EnSight.
- How do I request ANSYS Mechanical to use more number of cores for solution?
- How to restore the corrupted project in ANSYS Workbench?
- How to deal with “”Problem terminated — energy error too large””?”
- Contact Definitions in ANSYS Workbench Mechanical
- There is a unit systems mismatch between the environments involved in the solution.
- How can I change the background color, font size settings of the avi animation exported from Mechanical? How can I improve the resolution of the video?
- How to transfer a material model(s) from one Analysis system to another within Workbench?
- How to obtain force reaction in a section ?
- How to change color for each body in Mechanical?
- How to resolve “Error: Invalid Geometry”?
© 2025 Copyright ANSYS, Inc. All rights reserved.