Tagged: ls-dyna, LS-DYNA Suite, lsdyna, structural-mechanics
-
-
March 17, 2023 at 8:59 am
FAQ
ParticipantIt is not uncommon to obtain different results from different LS-DYNA releases. The code is constantly evolving. Defects are fixed, and very rarely, defects are introduced as intended improvements to algorithms are made. If the difference in results is soley attributable to changes in source code, it may be possible, through a series of runs, for us to identify the precise change in code that triggers the change in results. This is a laborious process which is not guaranteed to be fruitful. Unrelated to changes in source code, a model which is marginally stable or not robust promotes inconsistency of results. Robustness is often improved by following a few modeling guidelines. Explicit guidelines: https://ftp.lstc.com/anonymous/outgoing/support/PRESENTATIONS/Crash_Guidelines.pdf Implicit guidelines: https://www.lstc.com/sdb/361 In problems with well-defined or analytic solutions, e.g., where test results are easily repeatable, there would likely not be any issue of inconsistency in computational results. On the other hand, some events by their very nature, particularly dynamic events involving nonlinear material behavior (material damage and failure), are simply prone to inconsistent behavior. For those events, an infinitesimal deviation in the results early in the event can lead to a large deviation as the event progresses. This is true not only of computational results but of experimental results as well. SMP and MPP can also produce different computation results, even if the same version of the code is used. This is primarily due to contact algorithms in MPP being coded differently than those in SMP. Also, the number of cores used in MPP can affect the solution due to the change in domain decomposition. Solution 2064151 speaks to this in greater detail.​ It is recommended that the analyst: – Decide whether to use SMP or MPP, and stick with that decision. – If using SMP, set CONST=1 in *CONTROL_PARALLEL (or equivalently, set ncpu to a negative value on the execution line). – If using MPP, decide on a particular core count to use and don’t deviate from that. Also include the keyword *CONTROL_MPP_IO_LSTC_REDUCE in the input file.
-
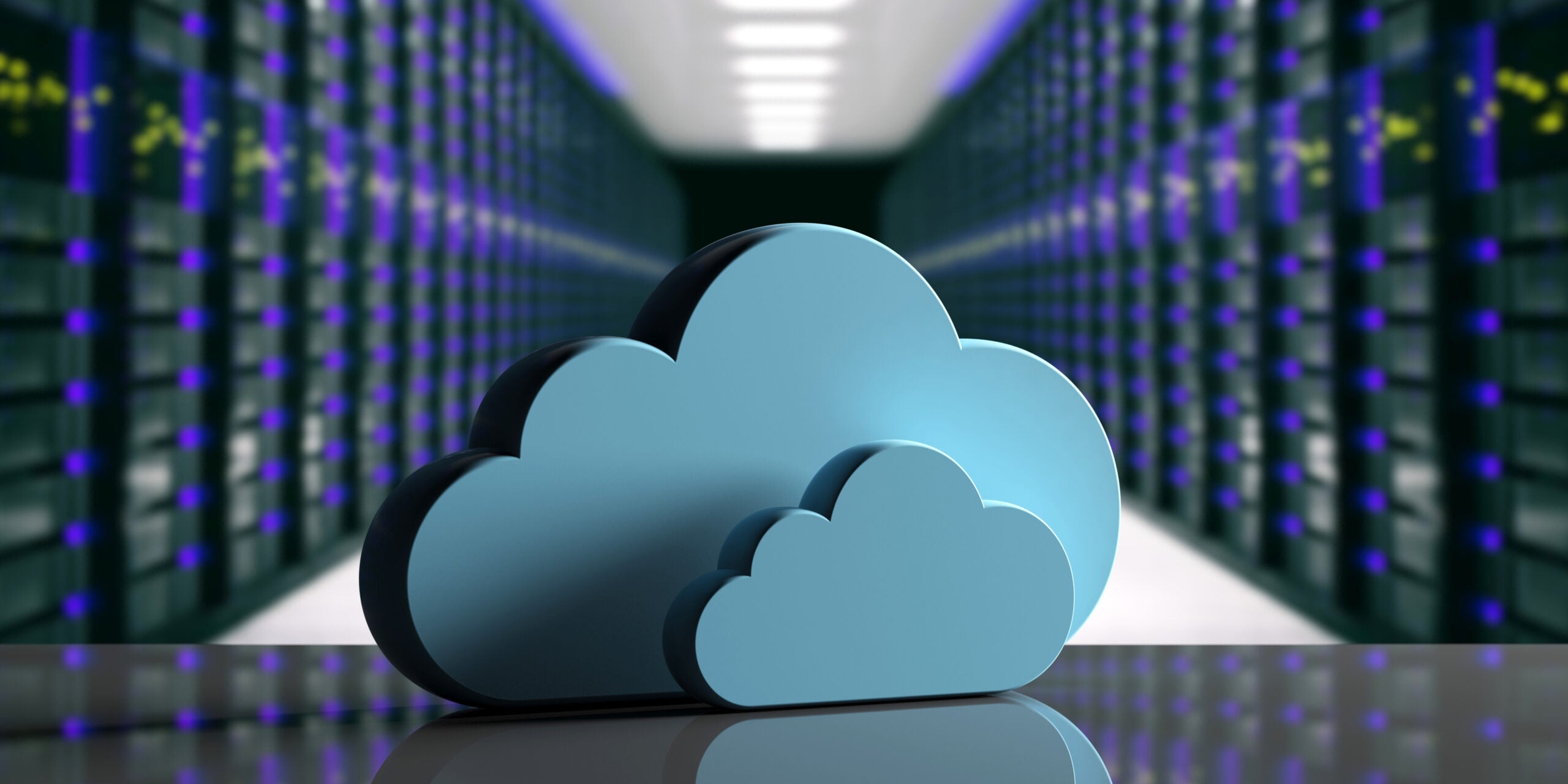
Introducing Ansys Electronics Desktop on Ansys Cloud
The Watch & Learn video article provides an overview of cloud computing from Electronics Desktop and details the product licenses and subscriptions to ANSYS Cloud Service that are...
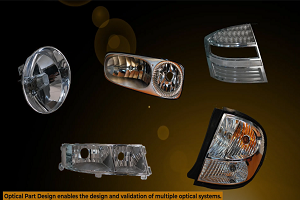
How to Create a Reflector for a Center High-Mounted Stop Lamp (CHMSL)
This video article demonstrates how to create a reflector for a center high-mounted stop lamp. Optical Part design in Ansys SPEOS enables the design and validation of multiple...
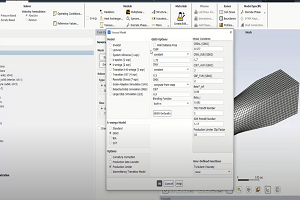
Introducing the GEKO Turbulence Model in Ansys Fluent
The GEKO (GEneralized K-Omega) turbulence model offers a flexible, robust, general-purpose approach to RANS turbulence modeling. Introducing 2 videos: Part 1 provides background information on the model and a...
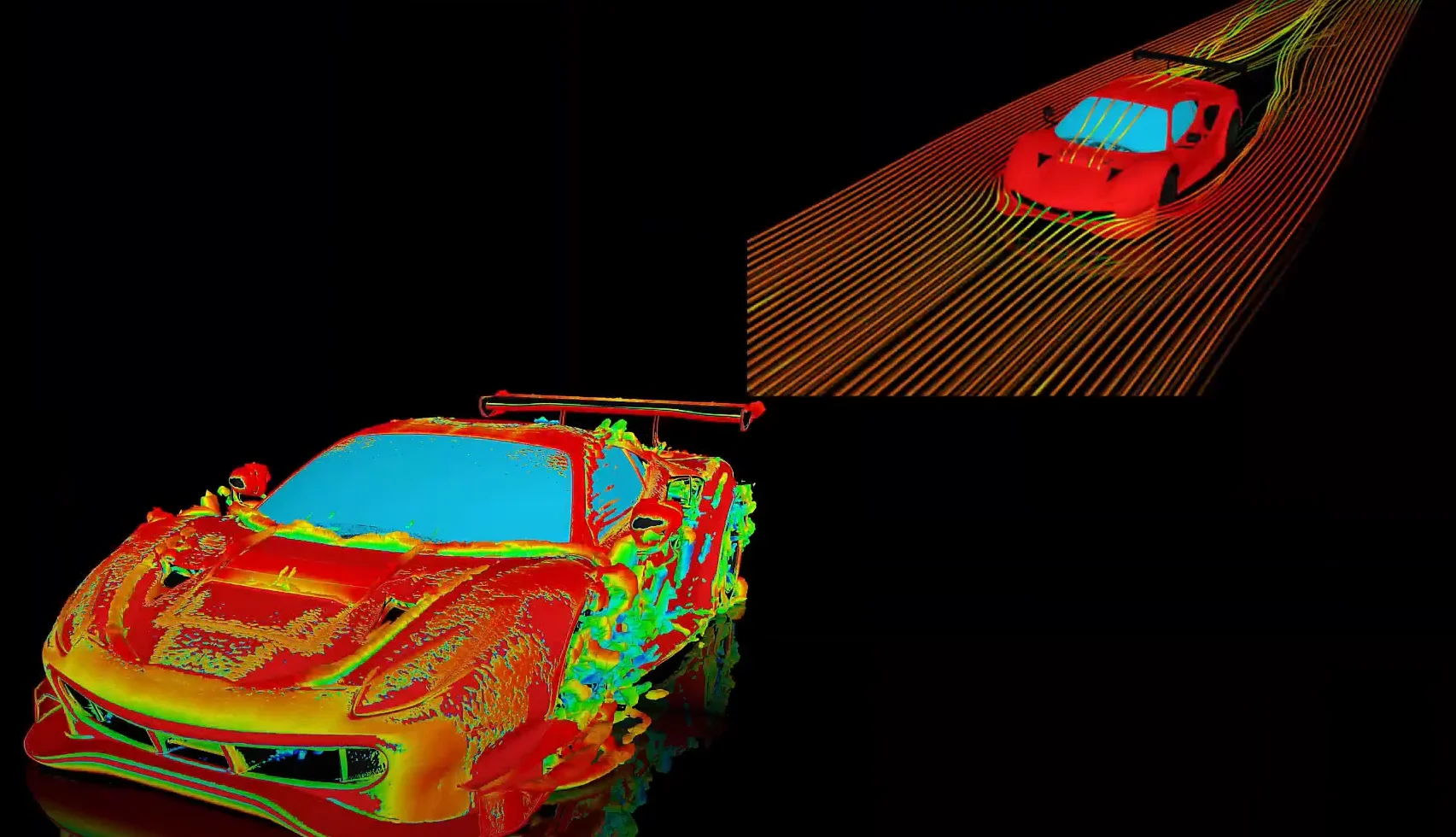
Postprocessing on Ansys EnSight
This video demonstrates exporting data from Fluent in EnSight Case Gold format, and it reviews the basic postprocessing capabilities of EnSight.
- How do I request ANSYS Mechanical to use more number of cores for solution?
- How to restore the corrupted project in ANSYS Workbench?
- How to deal with “”Problem terminated — energy error too large””?”
- Contact Definitions in ANSYS Workbench Mechanical
- There is a unit systems mismatch between the environments involved in the solution.
- How can I change the background color, font size settings of the avi animation exported from Mechanical? How can I improve the resolution of the video?
- How to transfer a material model(s) from one Analysis system to another within Workbench?
- How to obtain force reaction in a section ?
- How to change color for each body in Mechanical?
- How to resolve “Error: Invalid Geometry”?
© 2025 Copyright ANSYS, Inc. All rights reserved.