Tagged: 15, autodyn, explicit-dynamics, General, structural-mechanics
-
-
January 25, 2023 at 7:34 am
FAQ
Participant“”Time step too small”” is shown when the current time step is less than 10% of the initial time step. You can always decrease the minimum time step to continue the calculation. After loading your problem, go to the Controls panel and select Timestep Options. Change the Minimum Time Step to a very small number, or zero. Zero Minimum Time Step means that the minimum time step size is calculated automatically by the code. The variables affecting the time step are the smallest cell size, gap size, velocity, and sound speed. For Lagrangian type parts, you need to examine the geometry of the parts to see if there are distorted cells. For Eulerian type parts, you need to examine the velocity and sound speed of the parts to see if there are abnormal velocity or sound speeds. If Lagrange-Lagrange interaction is involved in the calculation, you need to check the gap size and gap type. If internal gap is used, the time step is usually calculated from the gap size because it is the smallest. The internal gap size decreases with the decreasing cell length and thus causes the smaller time step size. So the best type of gap is EXTERNAL GAP. Change the gap type to EXTERNAL and run the model again. For Euler calculations, following the instructions help you to prevent a small timestep: 1. Use Internal Energy Transport. This is set in the Controls panel under Transport, by selecting internal for the ALE/Euler Energy option. The default in AUTODYN is Total Energy Transport. In Euler calculations of shaped charges or detonation of explosives where the detonation products escape into a void at high speed, a better result will be achieved using internal energy transport as this provides a more accurate determination of the internal energy in a cell, which in turn is used in the explosive equation of state. 2. Use large relative density cutoffs 1.0E-4 instead of default 1.0E-6. This is set for each material and can be changed in the Material panel by selecting the relevant material from the list and pressing the Modify button. The escaping detonation products are typically at very low density. It is useful to limit the diffusion of extremely small masses which can causes very small time step by increasing this cutoff value. 3. Use a Maximum velocity cutoff of ~10,000 m/sec. Very small masses of explosive escaping into Void can sometimes achieve unrealistic velocities which results in verysmall time step This should be limited by setting the Maximum velocity cutoff in the Controls panel under Global Cutoffs.”
-
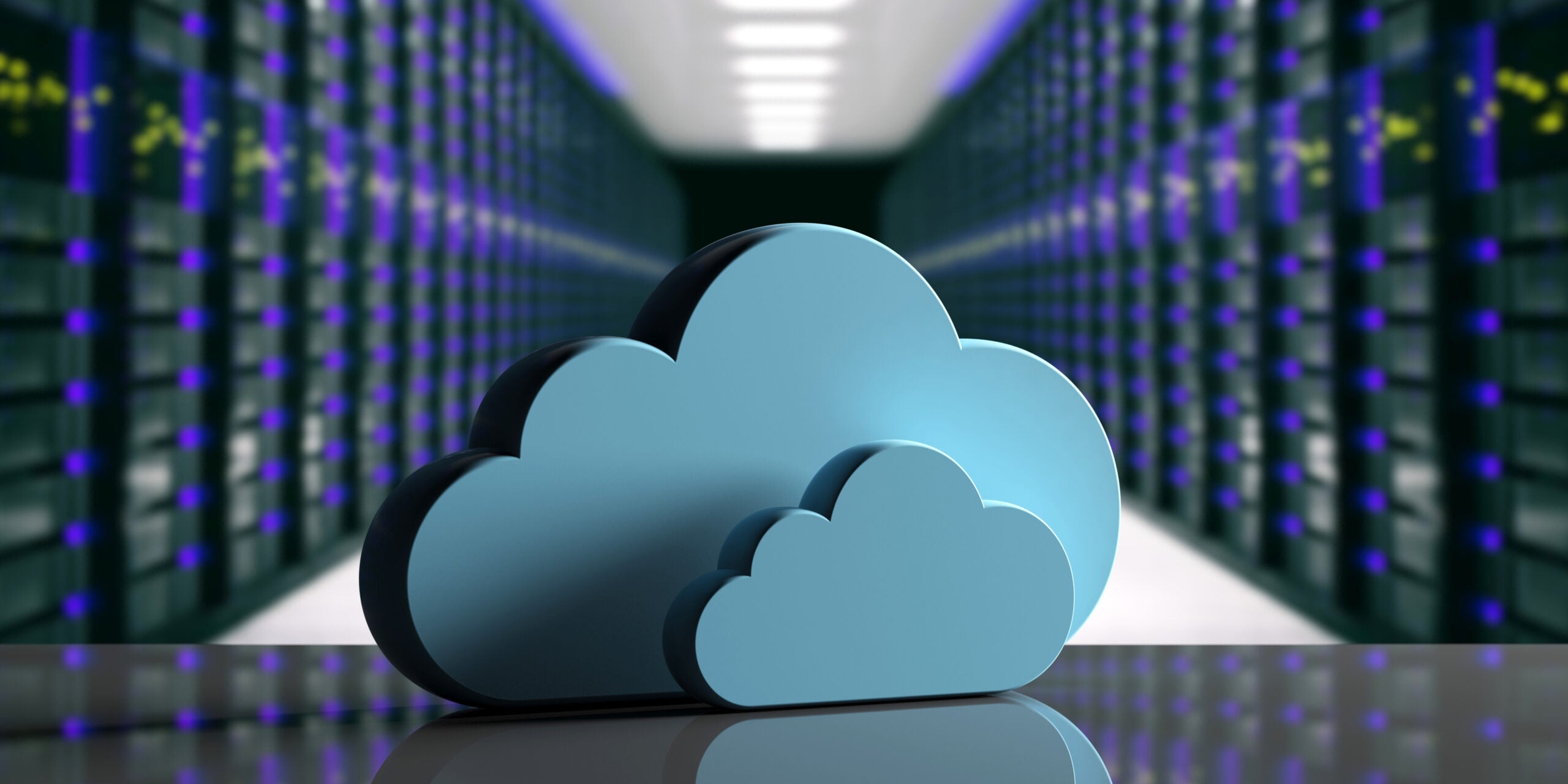
Introducing Ansys Electronics Desktop on Ansys Cloud
The Watch & Learn video article provides an overview of cloud computing from Electronics Desktop and details the product licenses and subscriptions to ANSYS Cloud Service that are...
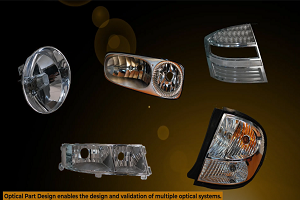
How to Create a Reflector for a Center High-Mounted Stop Lamp (CHMSL)
This video article demonstrates how to create a reflector for a center high-mounted stop lamp. Optical Part design in Ansys SPEOS enables the design and validation of multiple...
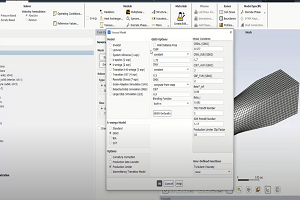
Introducing the GEKO Turbulence Model in Ansys Fluent
The GEKO (GEneralized K-Omega) turbulence model offers a flexible, robust, general-purpose approach to RANS turbulence modeling. Introducing 2 videos: Part 1 provides background information on the model and a...
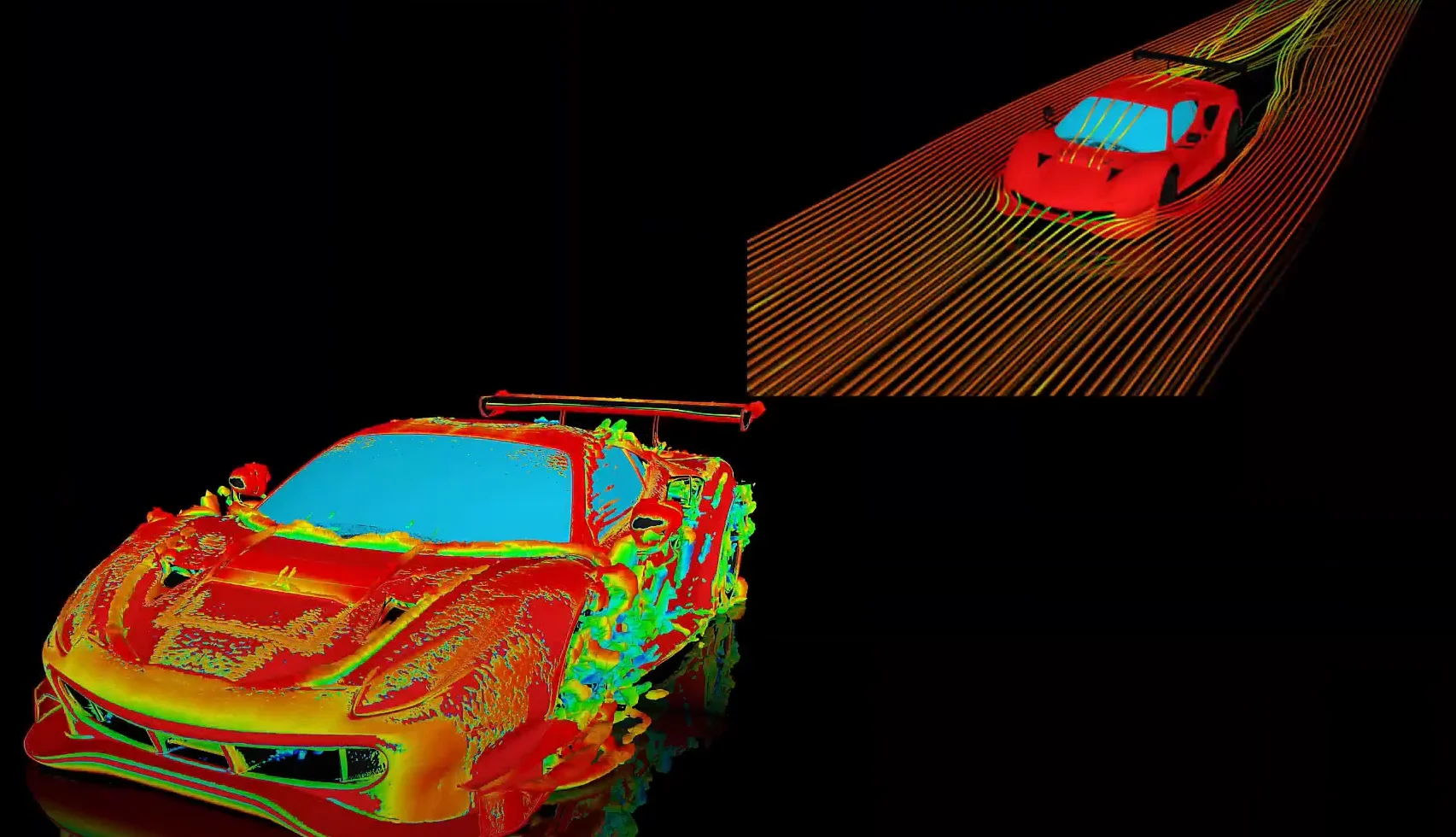
Postprocessing on Ansys EnSight
This video demonstrates exporting data from Fluent in EnSight Case Gold format, and it reviews the basic postprocessing capabilities of EnSight.
- How do I request ANSYS Mechanical to use more number of cores for solution?
- How to restore the corrupted project in ANSYS Workbench?
- How to deal with “”Problem terminated — energy error too large””?”
- Contact Definitions in ANSYS Workbench Mechanical
- There is a unit systems mismatch between the environments involved in the solution.
- How can I change the background color, font size settings of the avi animation exported from Mechanical? How can I improve the resolution of the video?
- How to transfer a material model(s) from one Analysis system to another within Workbench?
- How to obtain force reaction in a section ?
- How to change color for each body in Mechanical?
- How to resolve “Error: Invalid Geometry”?
© 2025 Copyright ANSYS, Inc. All rights reserved.