How to apply application-based settings to improve the performance and robustness of transient structural analyses?
-
-
January 25, 2023 at 7:34 am
FAQ
ParticipantMany transient dynamic analysis settings can be automatically set by the program based on the intended application. When you specify an application type on the TINTP command, the program automatically defines the time-integration constants (GAMMA parameter on TINTP) and several solver settings. Listed below are the application-based settings you can choose from. Impact Simulation Use the command TINTP,IMPA if the intended application is an impact simulation and you do not want any numerical dissipation. The program follows the time-integration method that you specify via the TRNOPT command (Newmark or HHT) and sets GAMMA = 0, resulting in no numerical dissipation. High Speed Simulation Use the command TINTP,HISP if the intended application is a high speed simulation. The program follows the time-integration method that you specify via the TRNOPT command (Newmark or HHT) and sets GAMMA = 0.005, resulting in a small numerical dissipation. The Impact Simulation (IMPA) and High Speed Simulation (HISP) options result in little or no energy dissipation. Therefore, it might be hard to achieve convergence under these settings. However, they can accurately capture the dynamic response of a structure. For example, the IMPA and HISP options are recommended in the following cases: analyzing high frequency vibrations in a structure; and studying the wave propagation in a structure during impact. Moderate Speed Simulation Use the command TINTP,MOSP if the intended application is a moderate speed simulation. The program follows the time-integration method that you specify via the TRNOPT command (Newmark or HHT) and sets GAMMA = 0.1, resulting in a moderate numerical dissipation which helps to achieve convergence without significant energy loss. This setting can be used for most transient dynamic simulations. Low Speed Simulation Use the command TINTP,LOSP if the intended application is a low speed simulation. The program follows the time-integration method that you specify via the TRNOPT command (Newmark or HHT) and sets GAMMA = 0.414, resulting in a high numerical dissipation. The automatic time incrementation is changed such that only one point per cycle is required per integration time step, therefore allowing use of much larger time increments. For the LOSP option, the mid-step convergence check is ignored, overriding the MIDTOL command. The impact constraints for contact elements defined using KEYOPT(7) = 4 are also ignored. These settings help to achieve convergence and larger time increments in a nonlinear transient dynamic simulation. However, because of the higher numerical dissipation, the LOSP option is recommended for low-speed applications where the high frequency vibrations of structures are not of interest; for example, simulating metal forming processes like rolling or extrusion. Quasi-Static Simulation Use the command TINTP,QUAS if the intended application is quasi-static. For this option, the program uses backward Euler time-integration. The high numerical dissipation in this time-integration scheme can help to achieve convergence in some problems that are quasi-static in nature but fail to converge in a quasi-static analysis.
-
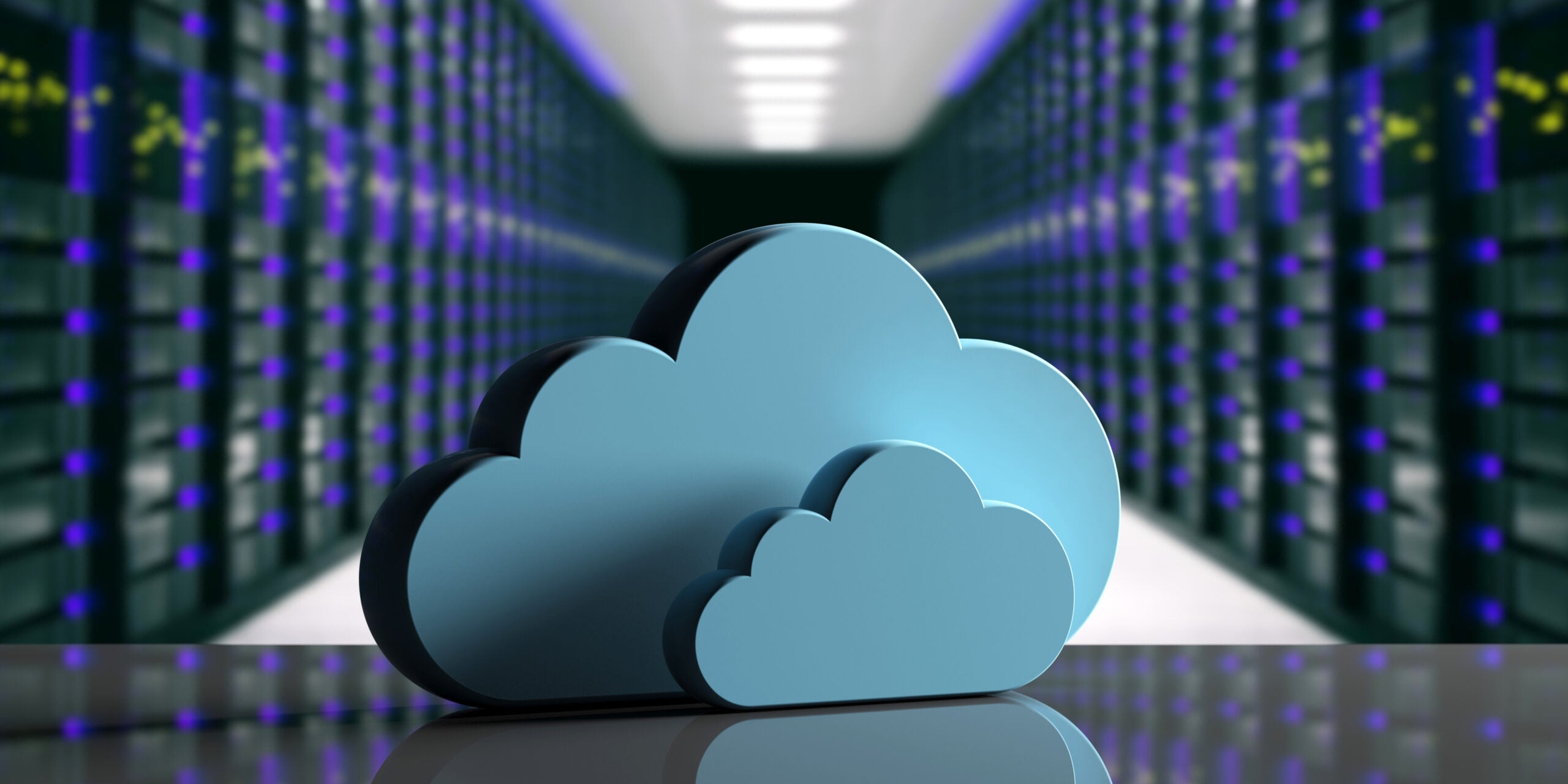
Introducing Ansys Electronics Desktop on Ansys Cloud
The Watch & Learn video article provides an overview of cloud computing from Electronics Desktop and details the product licenses and subscriptions to ANSYS Cloud Service that are...
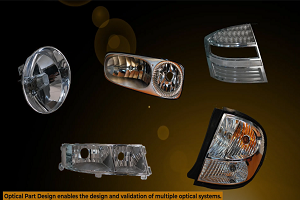
How to Create a Reflector for a Center High-Mounted Stop Lamp (CHMSL)
This video article demonstrates how to create a reflector for a center high-mounted stop lamp. Optical Part design in Ansys SPEOS enables the design and validation of multiple...
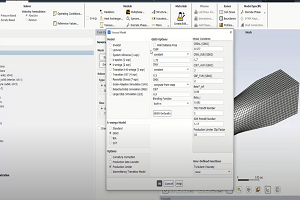
Introducing the GEKO Turbulence Model in Ansys Fluent
The GEKO (GEneralized K-Omega) turbulence model offers a flexible, robust, general-purpose approach to RANS turbulence modeling. Introducing 2 videos: Part 1Â provides background information on the model and a...
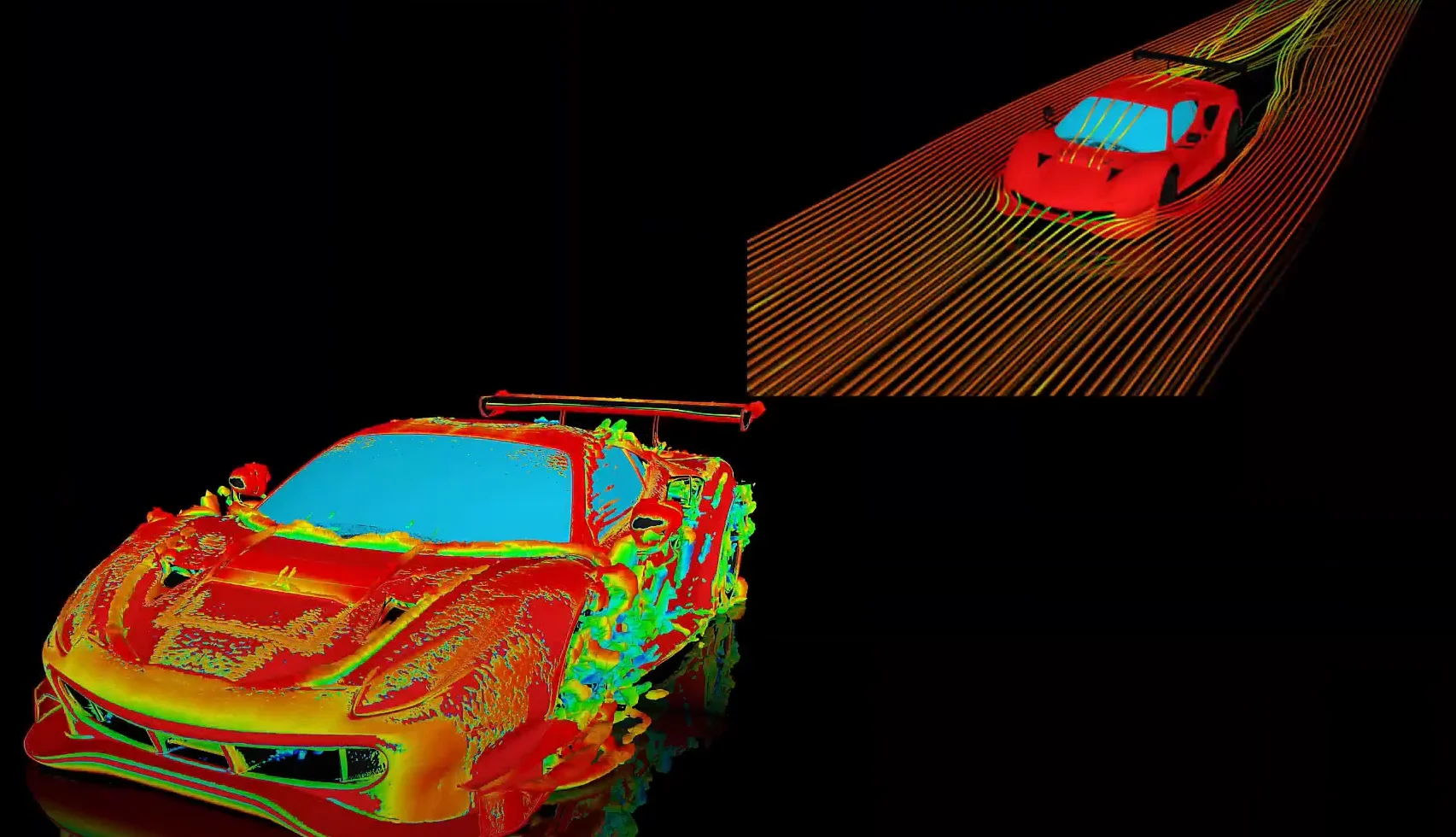
Postprocessing on Ansys EnSight
This video demonstrates exporting data from Fluent in EnSight Case Gold format, and it reviews the basic postprocessing capabilities of EnSight.
- How to setup Initial, Minimum and Maximum time step in Transient analysis?
- How to define variable thickness shell elements in ANSYS Mechanical? Is there any verification example of the variable thickness shell modal analysis available?
- In Workbench Mechanical, how can I obtain strain energy output for Modal analysis?
- How to apply application-based settings to improve the performance and robustness of transient structural analyses?
- Why is damped frequency is lower than undamped frequency with viscous damping but larger with structural damping?
- In a random vibration analysis, what is “GRMS” and how can it be calculated?
- In the results of a modal analysis, how can I define that a frequency is an output parameter ?
- How to include effect of bolt pretension in a modal analysis?
- How can I specify acceleration at a node? Could I use the ‘big mass method’?
- Presentation on shock analysis using response spectrum and transient dynamics
© 2025 Copyright ANSYS, Inc. All rights reserved.