Tagged: AIM tutotrial, discovery-aim, fluids
-
-
September 26, 2022 at 10:00 am
Watch & Learn
ParticipantThis example is taken from Cornell University’s ANSYS AIM Learning Modules
Learning Goals
In this tutorial, you will learn to:
- To determine the total pressure on the walls of the nozzle.
- To show the Mach number distribution along the cross-section of flow field using Ansys AIM.
Problem Specification
Compute the converging-diverging nozzle flow using AIM and plot the pressure and velocity (Mach number) graphs. The pressure at the inlet is 3 bar at 300 K.
Geometry
The geometry of the Nozzle can be downloaded from here .
The following video shows how to navigate through Discovery AIM to import the geometry.
Mesh
In this example, we will be using Automatic Physics-Aware Meshing. Automatic physics-aware meshing helps automate and simplify your problem setup. With automatic physics-aware meshing, the computational mesh is generated automatically based on the solution fidelity setting and the physics inputs.
Physics Setup
This video shows how to set up the Boundary Conditions for solving Compressible flow through the nozzle.
Results
This video explains how to determine the distribution of velocity vector through the nozzle volume and determine the pressure on the walls of the nozzle. It also explains how to determine the Mach number and produce a contour of it along the cross-sectional plane.
Hand Calculations
In quasi-one-dimensional flow for this converging-diverging nozzle, we expect that the Mach number at the inlet will be subsonic and accelerating until, at the minimum nozzle area (the throat), the flow becomes sonic with M = 1. Since the nozzle starts to diverge, the fluid will continue accelerating until the exit, where it continues as supersonic. The Mach number at the end of the nozzle can be calculated in the equations below. The diameters of the end and throat area were converted to Area using formula (1) and compared using formula (2) to find the Mach number using isentropic flow tables.
The resulting Mach number at the end of the nozzle is found to be 4.15, which confirms that the exit flow is supersonic.
Simulation Result
The Mach number contour confirms that the behaviour at the outflow is supersonic.  To sufficiently validate the results from the simulation, the maximum Mach number must be compared to the value from the hand calculations.  The maximum value from the simulation is shown in the ‘Summary’ section of the Mach Number results panel n Discovery AIM. The table below compares the calculated value to the value from the simulation. The percentage difference confirms that the simulation result is very accurate, within 5% of the hand calculation.
Pre-Analysis Value Simulation Value Percent Difference 4.15 4.11 0.96%
-
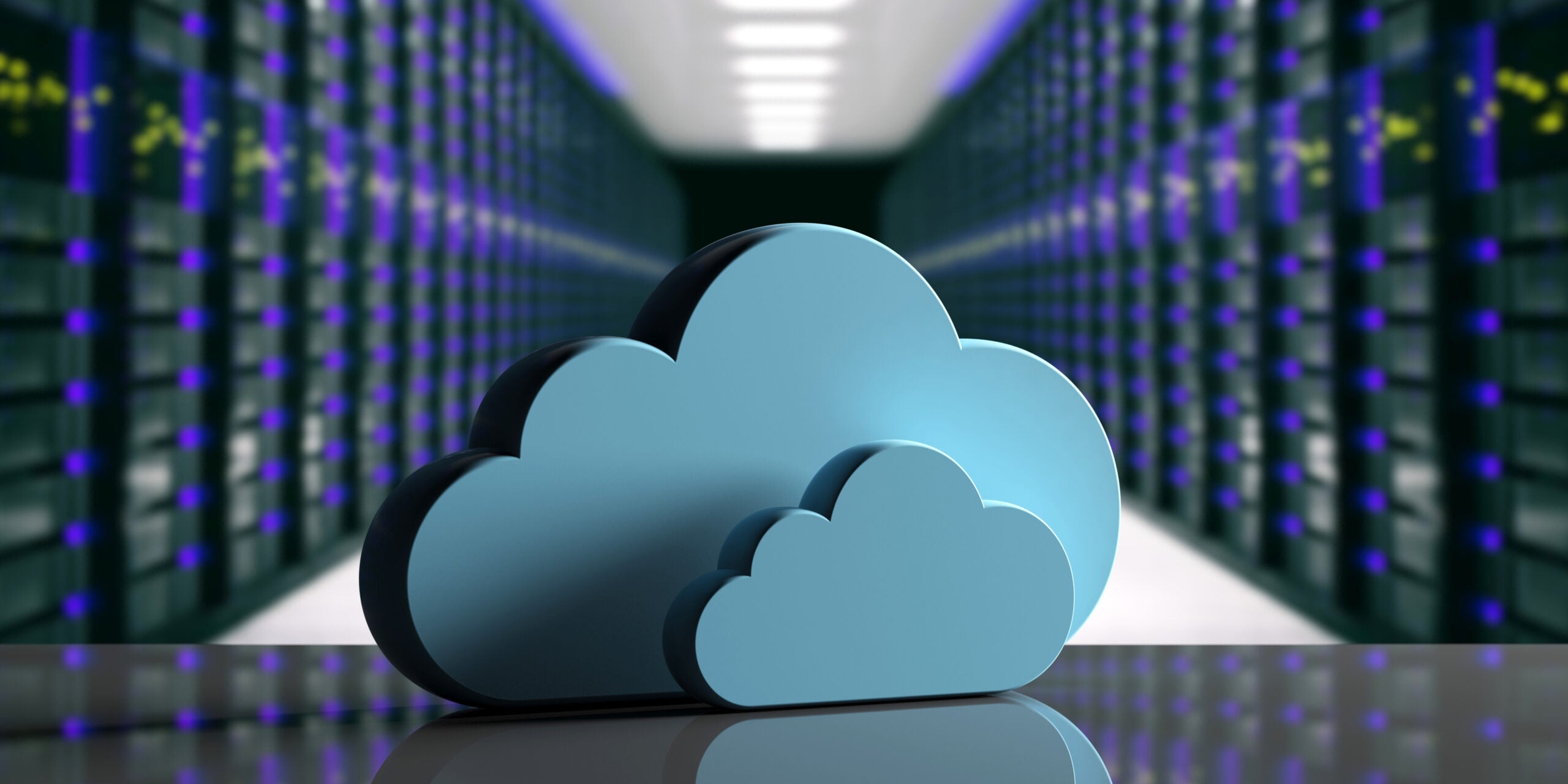
Introducing Ansys Electronics Desktop on Ansys Cloud
The Watch & Learn video article provides an overview of cloud computing from Electronics Desktop and details the product licenses and subscriptions to ANSYS Cloud Service that are...
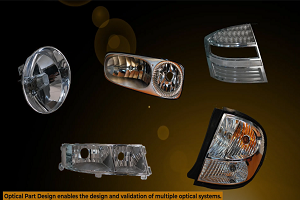
How to Create a Reflector for a Center High-Mounted Stop Lamp (CHMSL)
This video article demonstrates how to create a reflector for a center high-mounted stop lamp. Optical Part design in Ansys SPEOS enables the design and validation of multiple...
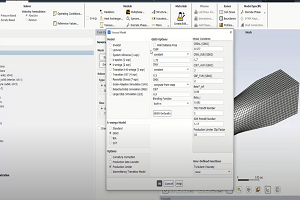
Introducing the GEKO Turbulence Model in Ansys Fluent
The GEKO (GEneralized K-Omega) turbulence model offers a flexible, robust, general-purpose approach to RANS turbulence modeling. Introducing 2 videos: Part 1Â provides background information on the model and a...
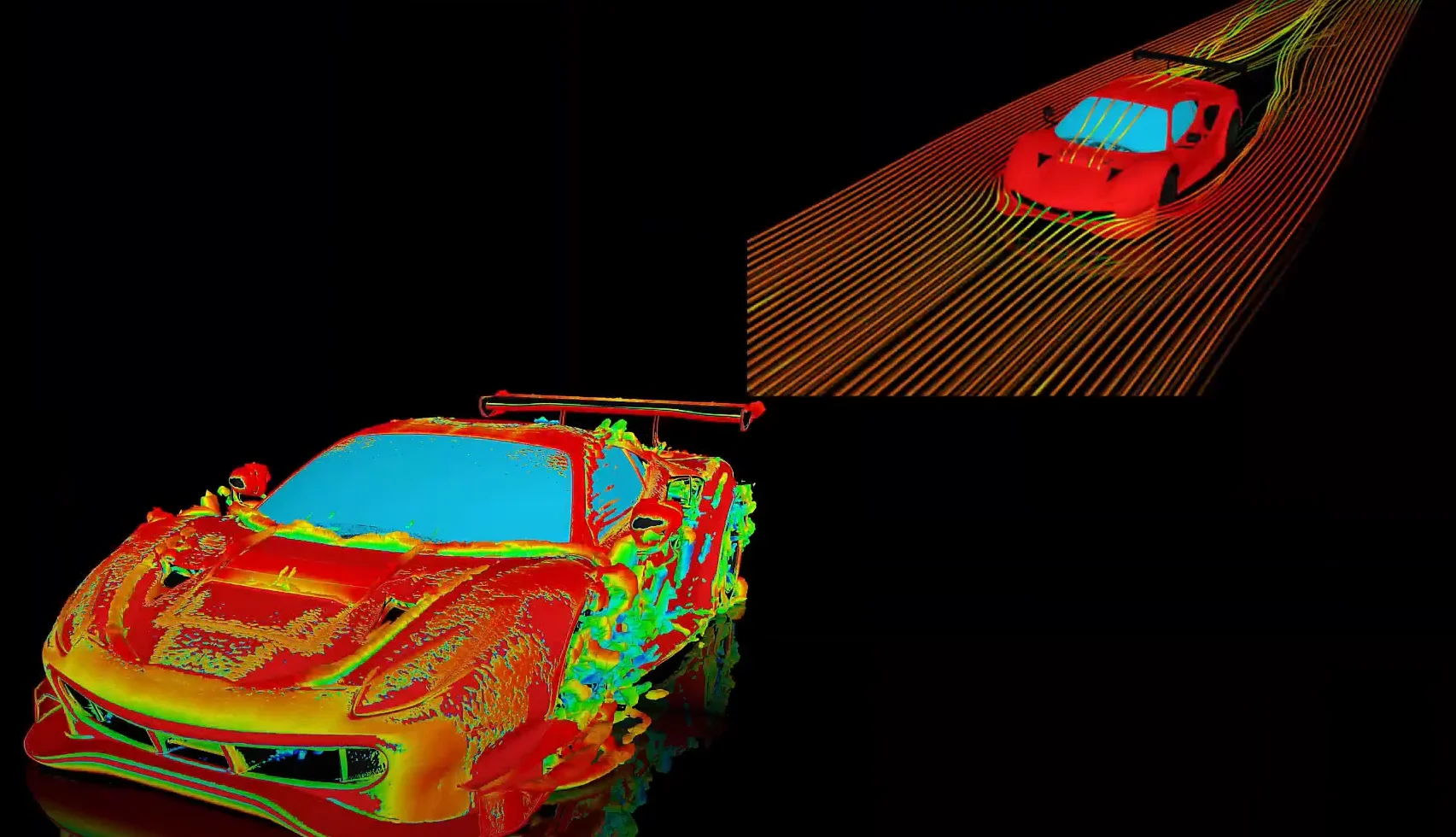
Postprocessing on Ansys EnSight
This video demonstrates exporting data from Fluent in EnSight Case Gold format, and it reviews the basic postprocessing capabilities of EnSight.
- Discovery Live: How to change units
- Discovery AIM tutorial – Analysis of cantilever beam with I cross-section
- Discovery AIM tutorial – 3D Finite-Element Analysis of a Bike Crank
- Discovery AIM – Scaling deformation contour results
- FAQ: Missing Areas of the User Interface in Discovery Live
- Discovery AIM tutorial – Structural Analysis of Plate with Hole
- Discovery SpaceClaim: Getting Started Tutorials
- Creating a Helical Geometry in SpaceClaim
- How to setup a Parameter Study
- Convert 2D Drawings to 3D Models in Minutes with SpaceClaim
© 2025 Copyright ANSYS, Inc. All rights reserved.