Additive Print: What is the logic behind the thermal strains calculated in Workbench Additive vs Additive Print?
-
-
April 5, 2023 at 2:32 pm
FAQ
ParticipantIn Workbench Additive, there is no heat flux or heat source input. We essentially just say that the thermal stress starts building when the material begins to solidify. So we set the temperature of the layer to melting temp. A parallel would be in Mechanical rather than apply a force to a face, you specify a displacement that you know will happen we are essentially setting the DOF to a known value rather than solving for it. The only variable we use here is to modify the time between layers by (element size/layer thickness)^(2/3) to make sure we get more consistent temperatures across different element sizes. In additive print, the only place where heat flux would be used would be in the thermal strain simulation during the thermal solve process. In that case, we actually trace the path of the laser so there is no averaging being done at all. First, we solve just for the temperature history of the whole build independent from displacement or stress that’s where the heat flux equations would be involved in the thermal solver. Then once we have the temperature history of every element in the model a static structural analysis is performed using an assumed strain model but we also calculate a ratio of the strain in all three directions (parallel to the laser, perpendicular to the laser, in the depth of the part) based on the scan pattern as well along with the temperature history of that particular element in the stress calculation.
-
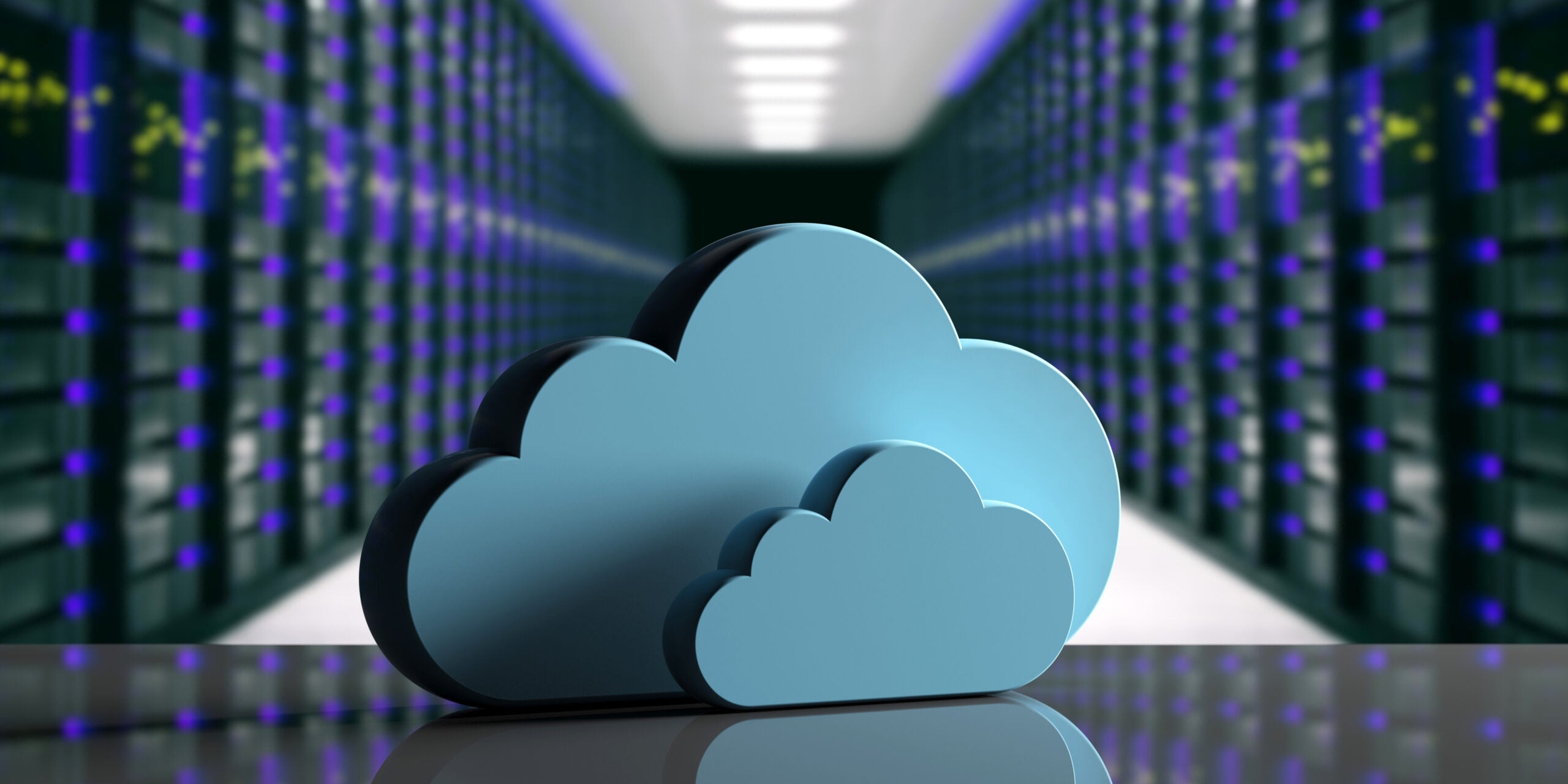
Introducing Ansys Electronics Desktop on Ansys Cloud
The Watch & Learn video article provides an overview of cloud computing from Electronics Desktop and details the product licenses and subscriptions to ANSYS Cloud Service that are...
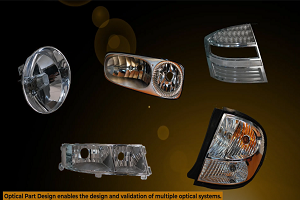
How to Create a Reflector for a Center High-Mounted Stop Lamp (CHMSL)
This video article demonstrates how to create a reflector for a center high-mounted stop lamp. Optical Part design in Ansys SPEOS enables the design and validation of multiple...
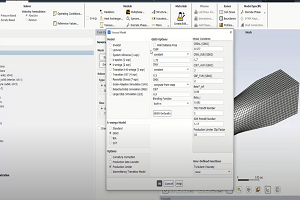
Introducing the GEKO Turbulence Model in Ansys Fluent
The GEKO (GEneralized K-Omega) turbulence model offers a flexible, robust, general-purpose approach to RANS turbulence modeling. Introducing 2 videos: Part 1Â provides background information on the model and a...
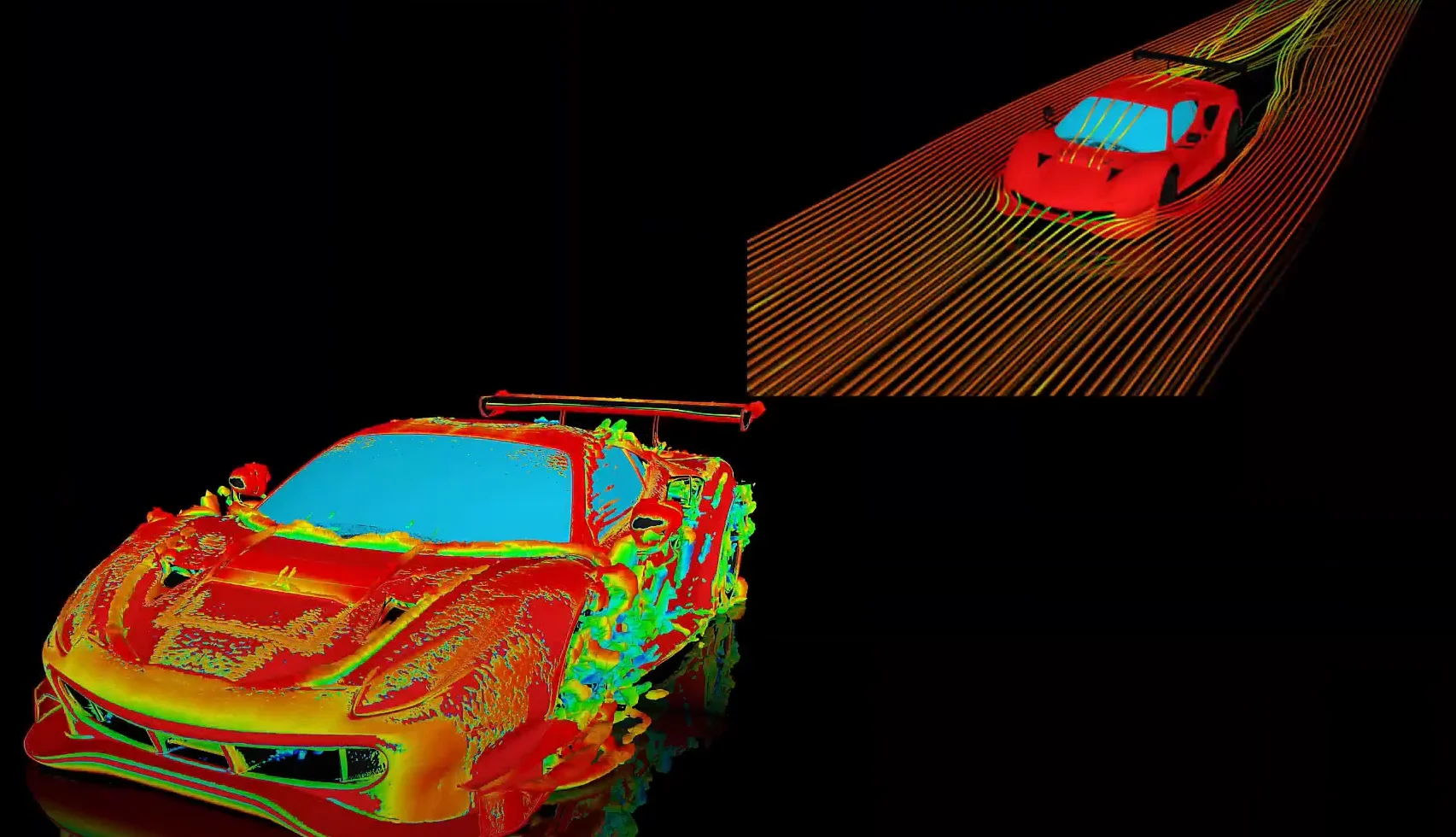
Postprocessing on Ansys EnSight
This video demonstrates exporting data from Fluent in EnSight Case Gold format, and it reviews the basic postprocessing capabilities of EnSight.
- How do I request ANSYS Mechanical to use more number of cores for solution?
- How to restore the corrupted project in ANSYS Workbench?
- How to deal with “”Problem terminated — energy error too large””?”
- Contact Definitions in ANSYS Workbench Mechanical
- There is a unit systems mismatch between the environments involved in the solution.
- How can I change the background color, font size settings of the avi animation exported from Mechanical? How can I improve the resolution of the video?
- How to transfer a material model(s) from one Analysis system to another within Workbench?
- How to obtain force reaction in a section ?
- How to change color for each body in Mechanical?
- How to resolve “Error: Invalid Geometry”?
© 2025 Copyright ANSYS, Inc. All rights reserved.