-
-
January 25, 2023 at 7:34 am
FAQ
ParticipantThe pressure-displacement curve of a gasket often starts with a low stiffness, making solver’s guess quite far from the final solution, and causing a number of iterations. But for gaskets, often a good approximation to the final displacement solution is known. So a few tricks may work to accelerate convergence by allowing the solver to start from a good first guess, or by forcing the analysis to follow certain displacement constraints during the iteration. 1) Model the gasket in an assumed loaded configuration and apply corresponding initial stresses. 2) Model the gasket in the undeformed configuration but position one flange relative to the other using displacement or velocity boundary conditions in order to achieve a good starting configuration for the Newton-Raphson algorithm. In the subsequent analysis step, the boundary condition is deactivated, the bolt loads are applied and the model is left to find equilibrium with small adjustments. 3) If a gasket acts as a stopper, with little or no pressure transmitted over some part of the stress-displacement curve, followed by a sharp bend and mostly linear, high stiffness behavior, you may see a negative impact on convergence. If you know beforehand that this kind of contact will be closed at the end of the bolt load analysis step, you may choose to force this contact to close by specifying a non-separation contact in combination with a contact interference that is ramped up over the analysis step. The bolt load is ramped up over the same step. 4) If a good assumption can be made for the deformation of certain parts of the gasket, the gasket may be pre-stressed using an additional no-separation contact between one side of the gasket and a layer of surface elements positioned between the other side of the gasket and the adjoining flange. This contact can then be used to apply a specified change in thickness to the gasket at that location. This displacement constraint is then released in the next step, in which the bolt load is applied.
-
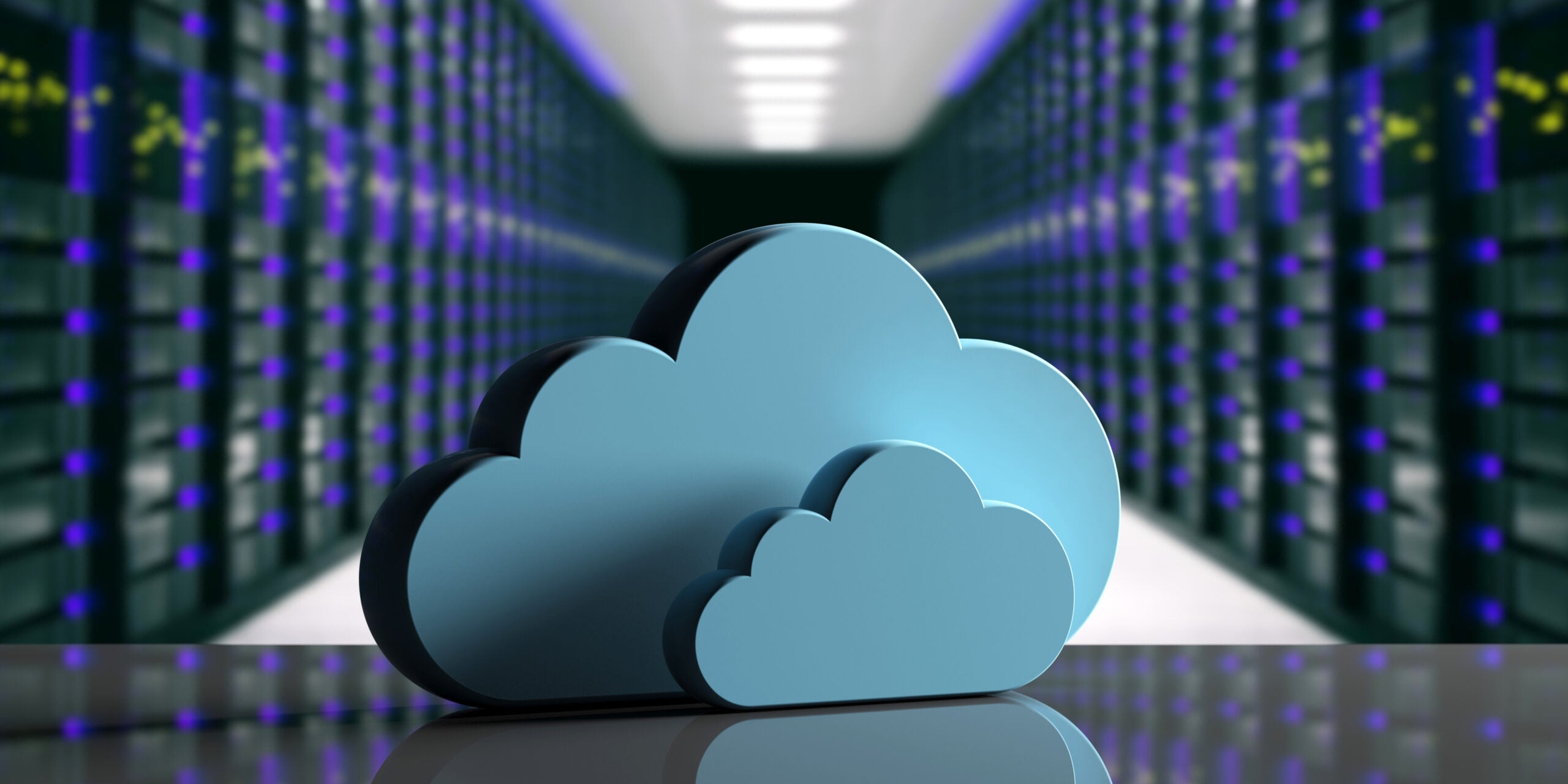
Introducing Ansys Electronics Desktop on Ansys Cloud
The Watch & Learn video article provides an overview of cloud computing from Electronics Desktop and details the product licenses and subscriptions to ANSYS Cloud Service that are...
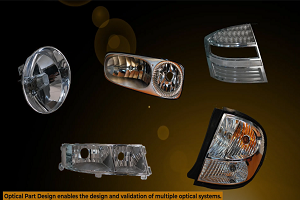
How to Create a Reflector for a Center High-Mounted Stop Lamp (CHMSL)
This video article demonstrates how to create a reflector for a center high-mounted stop lamp. Optical Part design in Ansys SPEOS enables the design and validation of multiple...
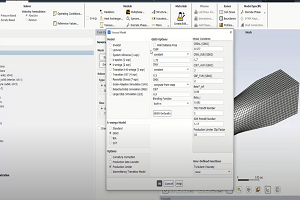
Introducing the GEKO Turbulence Model in Ansys Fluent
The GEKO (GEneralized K-Omega) turbulence model offers a flexible, robust, general-purpose approach to RANS turbulence modeling. Introducing 2 videos: Part 1Â provides background information on the model and a...
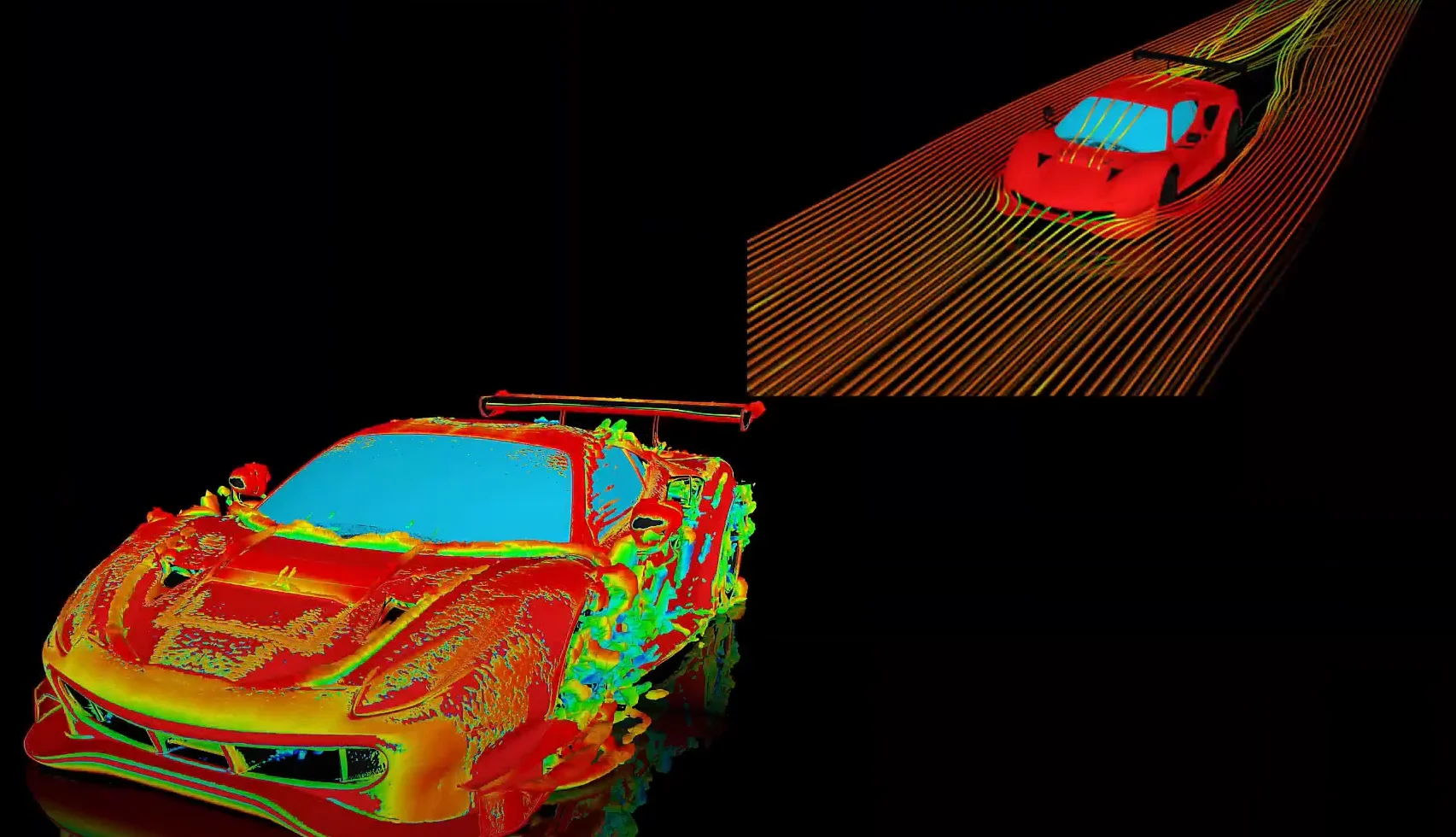
Postprocessing on Ansys EnSight
This video demonstrates exporting data from Fluent in EnSight Case Gold format, and it reviews the basic postprocessing capabilities of EnSight.
- Question: What is the difference between PLNSOL, EPPL, EQV and PLNSOL,NL,EPEQ?
- How to use layered section to simulate composites and post process the results in ANSYS Mechanical
- Guidelines of modeling a gasket.
- ANSYS Mechanical: Delamination Analysis using Contact Debonding
- For the stress-life fatigue method, how are the Goodman and Gerber mean stress theories used to modify the calculated stress amplitude in the Workbench Fatigue Module?
- Why is the unit of the elastic foundation stiffness N/m^3?
- How do I move a material property from Engineering Data to an existing Material Library?
- What are Isochronous stress-strain curves? How can they be used in ANSYS for modeling creep?
- How do I enter major Poisson’s ratio in ANSYS Mechanical?
- Hyperelastic Simulations
© 2025 Copyright ANSYS, Inc. All rights reserved.