Why is the temperature higher than the melting temperature for the first step of the transient thermal phase of an Additive Simulation?
-
-
March 17, 2023 at 8:59 am
FAQ
ParticipantThat is often due to the fast application of a temperature boundary condition. This is a known theoretical limitation of thermal transients using the FEA method; see the MAPDL Thermal Analysis Guide->Transient->Applying Loads (https://ansyshelp.ansys.com/account/secured?returnurl=/Views/Secured/corp/v192/ans_the/Hlp_G_THE3_5.html) for a description of how element size and thermal diffusivity relate to the maximum time step size that can be used. Basically, the time step must be small enough for the heat to travel from one side of the element to the other. If the time step is too large, then you get oscillations in the temperature solution leading to some nodes above melt and some below ambient. When we apply the temperatures to a new layer, the time step used respects this condition for the *layer* thickness, so we rarely see oscillations above the build plate. However, for the first layer where the build plate is composed of much larger element sizes, we can see these fictitious temperatures. Since we are taking relatively large time steps in additive (in order to keep the run times reasonable), we violate this condition. They can be safely ignored as they have no influence on the overall deformations and stresses in the part.
-
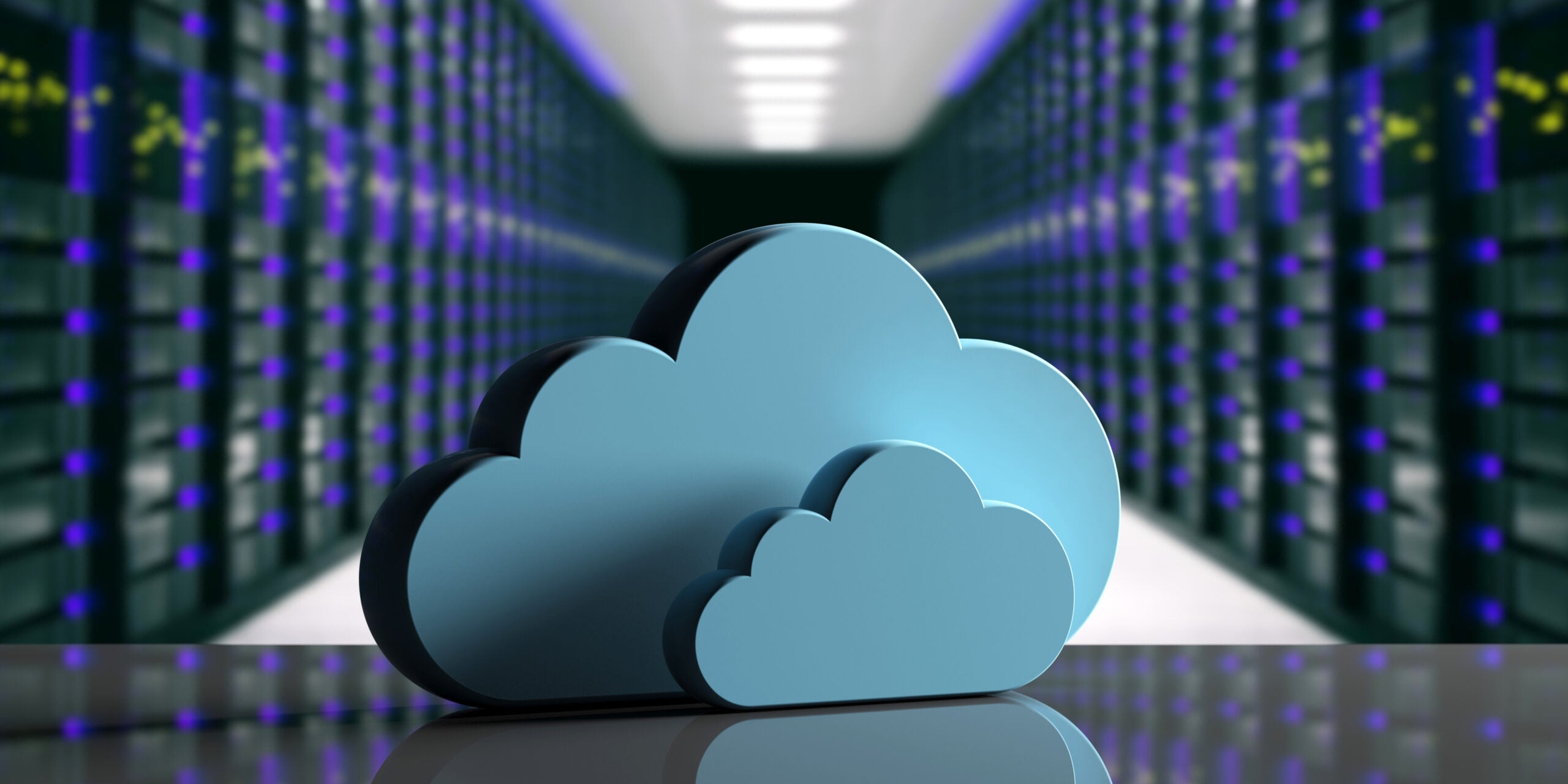
Introducing Ansys Electronics Desktop on Ansys Cloud
The Watch & Learn video article provides an overview of cloud computing from Electronics Desktop and details the product licenses and subscriptions to ANSYS Cloud Service that are...
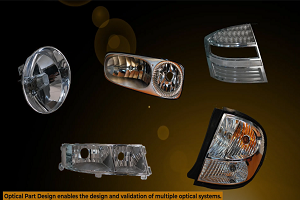
How to Create a Reflector for a Center High-Mounted Stop Lamp (CHMSL)
This video article demonstrates how to create a reflector for a center high-mounted stop lamp. Optical Part design in Ansys SPEOS enables the design and validation of multiple...
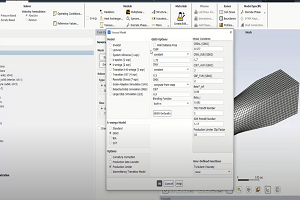
Introducing the GEKO Turbulence Model in Ansys Fluent
The GEKO (GEneralized K-Omega) turbulence model offers a flexible, robust, general-purpose approach to RANS turbulence modeling. Introducing 2 videos: Part 1 provides background information on the model and a...
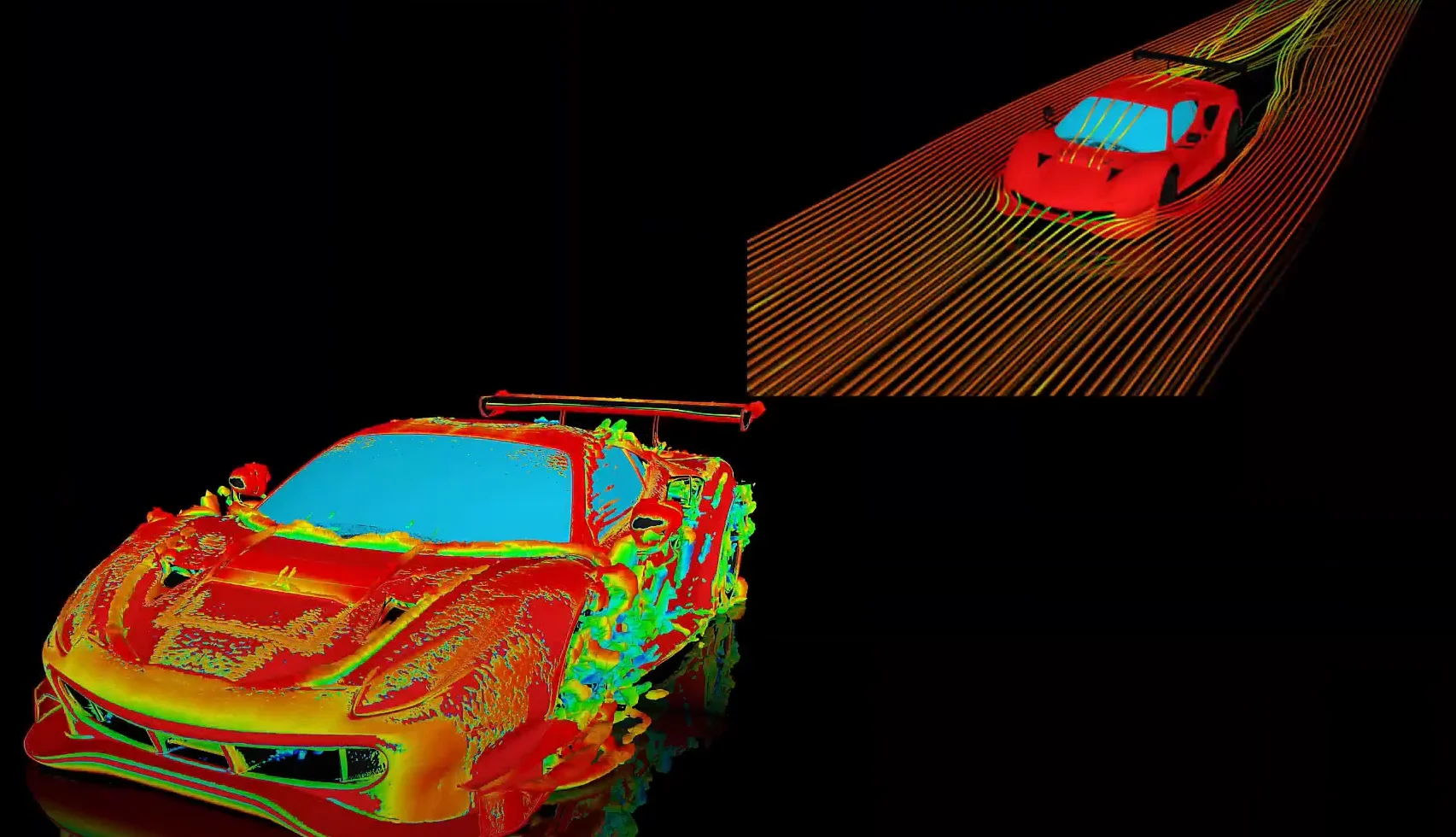
Postprocessing on Ansys EnSight
This video demonstrates exporting data from Fluent in EnSight Case Gold format, and it reviews the basic postprocessing capabilities of EnSight.
- How do I request ANSYS Mechanical to use more number of cores for solution?
- How to restore the corrupted project in ANSYS Workbench?
- How to deal with “”Problem terminated — energy error too large””?”
- Contact Definitions in ANSYS Workbench Mechanical
- How can I change the background color, font size settings of the avi animation exported from Mechanical? How can I improve the resolution of the video?
- There is a unit systems mismatch between the environments involved in the solution.
- How to transfer a material model(s) from one Analysis system to another within Workbench?
- How to obtain force reaction in a section ?
- What is the reason for this error message when mesher fails – “A software execution error occurred inside the mesher. The process suffered an unhandled exception or ran out of usable memory.”?
- How to change color for each body in Mechanical?
© 2025 Copyright ANSYS, Inc. All rights reserved.