Why are the linearized stresses different in a 3D solid cylinder model compared to a 2D axisymmetric model?
-
-
January 25, 2023 at 7:34 am
FAQ
ParticipantThe stress linearization equations are described in the Ansys Help: Mechanical APDL Theory Reference Chapter 17: Postprocessing 17.4. POST1 – Stress Linearization or: https://ansyshelp.ansys.com/account/secured?returnurl=/Views/Secured/corp/v195/ans_thry/thy_post4.html The main point here is that there is a ‘thickness’ assumed (integral of -t/2 to t/2) in the calculations. If the material is at the centerline, this becomes invalid, which explains the ‘incorrect’ results you get since you are going from 0 (center) to radius. When we perform stress linearization, we are typically considering a thin structure, so we are aware from the centerline (see Figures 17.6 and 17.7 in the page above). We don’t perform stress linearization on a solid tube. Because of this, the solid tube case is not considered or discussed in the documentation. The application of stress linearization to an axisymmetric solid cylinder is not appropriate, so that is why it doesn’t match. If you had a 3D vs 2D axisymmetric hollow cylinder, and you are performing stress linearization through the thin-walled cylinder, the results should match more closely between 3D and 2D axisymmetric.
-
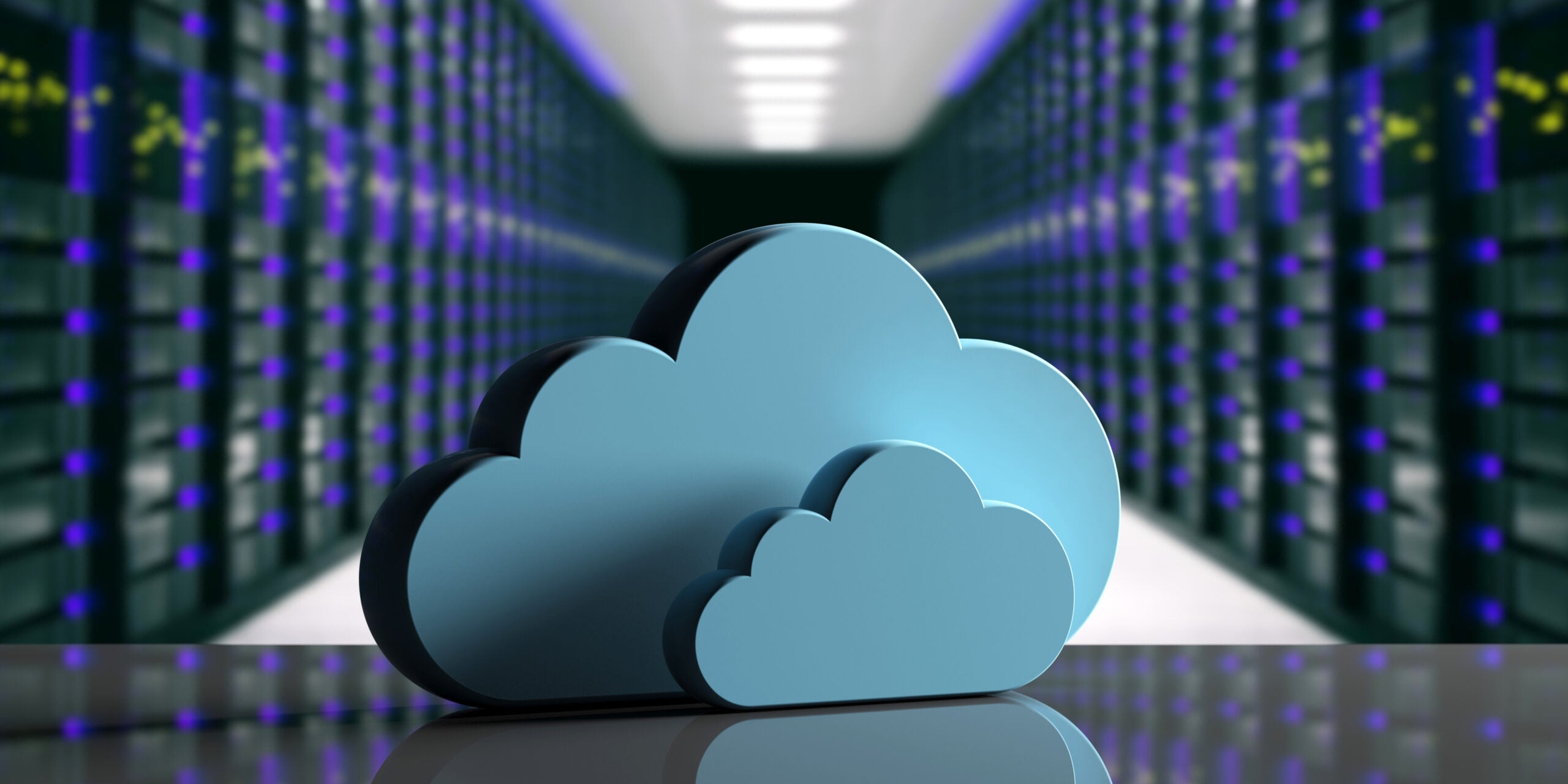
Introducing Ansys Electronics Desktop on Ansys Cloud
The Watch & Learn video article provides an overview of cloud computing from Electronics Desktop and details the product licenses and subscriptions to ANSYS Cloud Service that are...
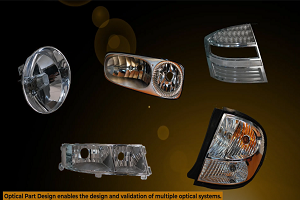
How to Create a Reflector for a Center High-Mounted Stop Lamp (CHMSL)
This video article demonstrates how to create a reflector for a center high-mounted stop lamp. Optical Part design in Ansys SPEOS enables the design and validation of multiple...
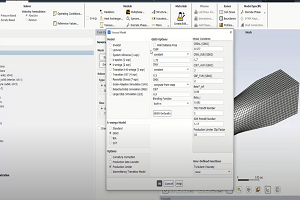
Introducing the GEKO Turbulence Model in Ansys Fluent
The GEKO (GEneralized K-Omega) turbulence model offers a flexible, robust, general-purpose approach to RANS turbulence modeling. Introducing 2 videos: Part 1Â provides background information on the model and a...
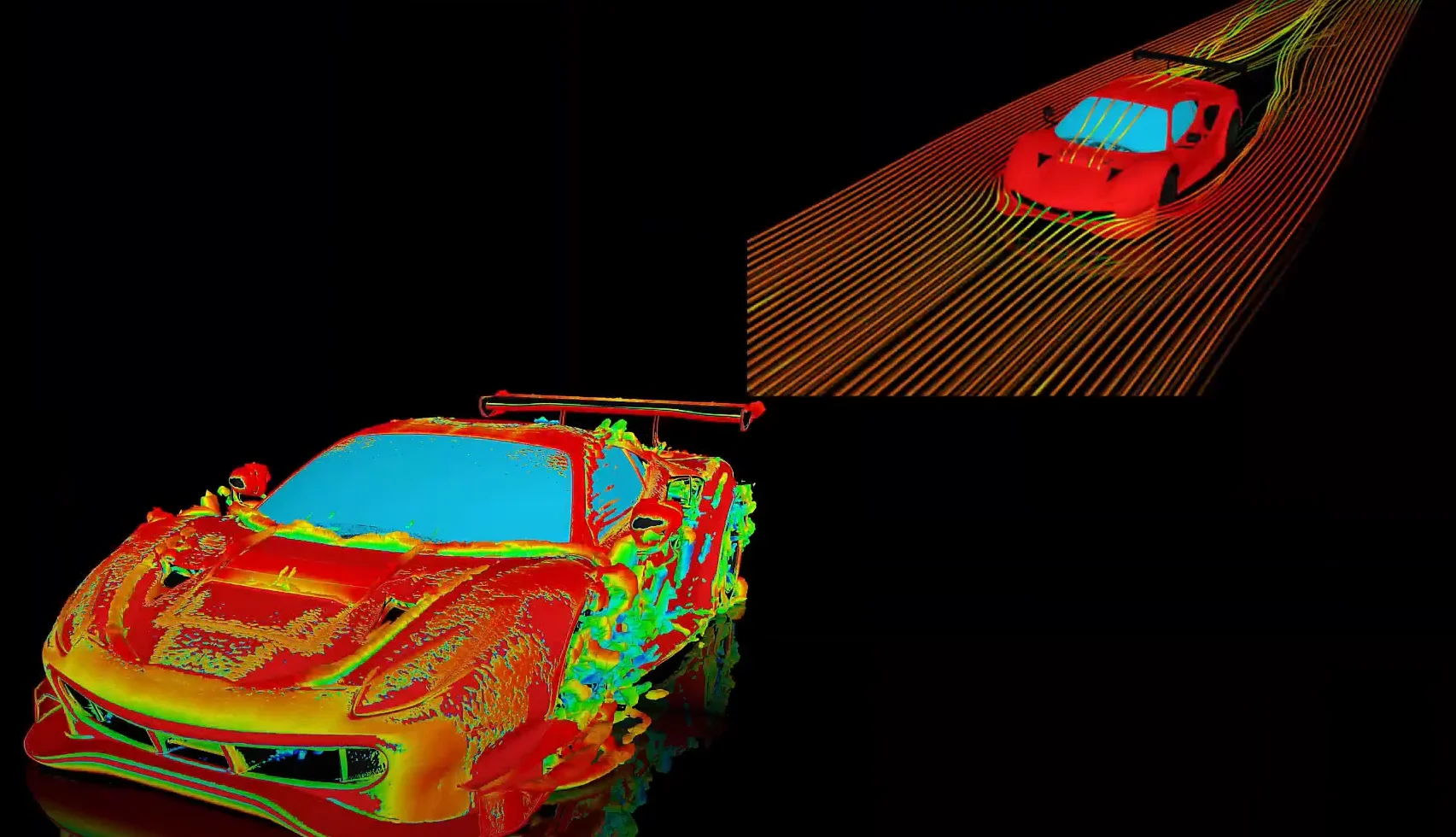
Postprocessing on Ansys EnSight
This video demonstrates exporting data from Fluent in EnSight Case Gold format, and it reviews the basic postprocessing capabilities of EnSight.
- How to reduce contact penetration?
- How to decide which side should be Contact and which should be target in Contact definition?
- What is the difference between secant and instantaneous coefficients of thermal expansion (CTE)?
- Does ECAD trace mapping support more than one type of trace material (usually copper) in the same layer?
- How to use the Newton-Raphson residuals option under Solution Information?
- How to plot stresses of a beam connection in Workbench?
- How can I understand Beam Probe results?
- How to find total heat flowing through a surface in Mechanical?
- Difference Between Environment Temperature and Reference Temperature in Mechanical
- How can I apply a controlled rotation in ANSYS Mechanical
© 2025 Copyright ANSYS, Inc. All rights reserved.