-
-
January 25, 2023 at 7:16 am
FAQ
ParticipantIt is a common problem in underhood environments to become very congested, causing the MRF used to model the cooling fans to become very small. A common question to ask is how small one can make the MRF. Some facts about MRF: 1. Non-axisymmetric stationary walls cannot touch or be inside the MRF. Otherwise, it will produce false velocities. 2. If an axisymmetric stationary wall does touch and is inside the MRF (e.g. part of the shroud), you must explicitly declare it as stationary in absolute reference frame in the wall boundary condition. This includes wall-shadows as well. MRF Size: MRF in general works OK provided that the flow is either: (1) Circumferentially uniform at the interface or (2) If circumferential non-uniformities in the flow exist, but the flow must primarily passes one way through the interface. In the real underhood situation, the fan is inserted partially or fully inside the cylindrical portion of the shroud. Since the cylindrical portion of the shroud is axi-symmetric, we can make its walls touch the cylindrical portion of the MRF interface. Thus, the cylindrical portion of the MRF will be a wall. It will have wall and wall-shadow—make sure the one adjacent to the MRF cell zone is declared as stationary in absolute reference frame. Making the cylindrical portion of the shroud a wall will prevent any flow passing it. If that portion of the shroud is not fully axi-symmetric in reality, one could—in the preprocessor—change it to be. By doing this, we are moving away from reality, so make sure that the modification is not significant. In the case of a plane shroud, which is typically used in the experiment when the fan curve is obtained, there is a significant recirculation near the fan tip. If you increase the radius of the MRF boundary away from the recirculation, you will see better prediction. But in the circular faces of the MRF boundary, the flow is only one directional—there are no recirculation at any of these two circular faces. Thus, the accuracy is not degraded as you decrease the MRF size in the axial direction.
-
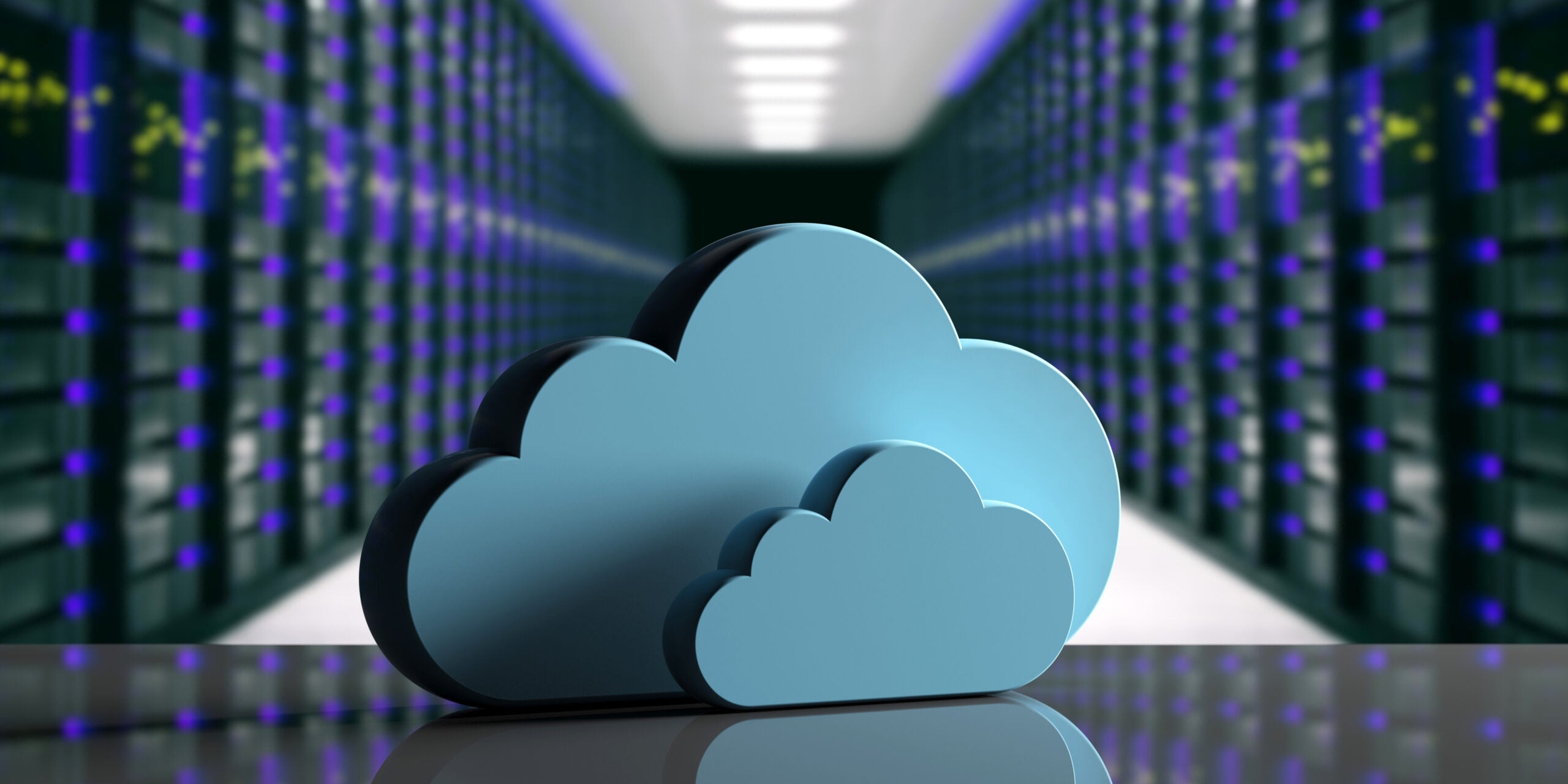
Introducing Ansys Electronics Desktop on Ansys Cloud
The Watch & Learn video article provides an overview of cloud computing from Electronics Desktop and details the product licenses and subscriptions to ANSYS Cloud Service that are...
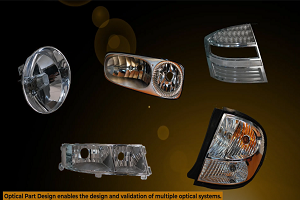
How to Create a Reflector for a Center High-Mounted Stop Lamp (CHMSL)
This video article demonstrates how to create a reflector for a center high-mounted stop lamp. Optical Part design in Ansys SPEOS enables the design and validation of multiple...
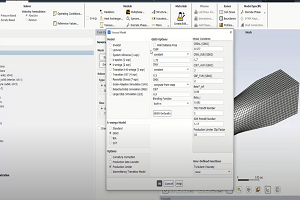
Introducing the GEKO Turbulence Model in Ansys Fluent
The GEKO (GEneralized K-Omega) turbulence model offers a flexible, robust, general-purpose approach to RANS turbulence modeling. Introducing 2 videos: Part 1Â provides background information on the model and a...
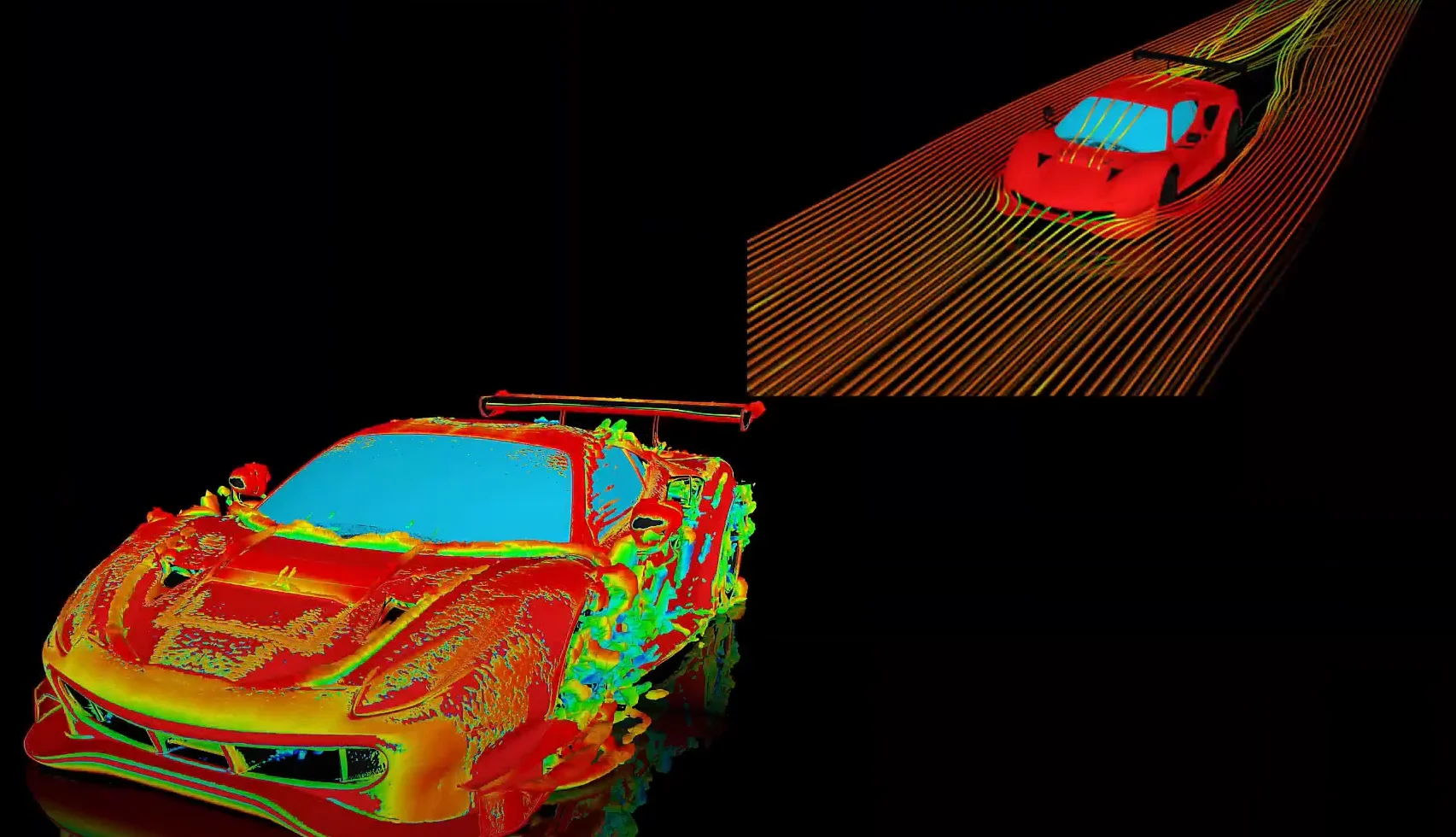
Postprocessing on Ansys EnSight
This video demonstrates exporting data from Fluent in EnSight Case Gold format, and it reviews the basic postprocessing capabilities of EnSight.
- How to overcome the model information incompatible with incoming mesh error?
- Skewness in ANSYS Meshing
- What are the requirements for an axisymmetric analysis?
- Ansys Fluent GPU Solver FAQs
- Is there a way to get the volume of a register using expression ?
- How to create and execute a FLUENT journal file?
- What are pressure-based solver vs. density-based solver in FLUENT?
- What is a .wbpz file and how can I use it?
- How to get information about mesh cell count and cell types in Fluent?
- How can I Export and import boxes / Systems from one Workbench Project to another?
© 2025 Copyright ANSYS, Inc. All rights reserved.