Solver message during DPM calculation: “number of stepsize underflows during particle integration step is x”. What does it mean and how to get rid of it?
-
-
January 25, 2023 at 7:17 am
FAQ
ParticipantThese messages are thrown when the ODE is being solved under the coupled heat mass option. It is a counter to monitor how many times, the integration error stayed above the default tolerance. They typically show up, when the Runge-Kutta solver we are using is taking too much steps to integrate the underlying ODEs for a given particle integration time step. Since this message has been issued in the past for each integration step which fails we are collecting them now and issuing only once per DPM Iteration. One workaround is to use a different ODE solver. If you are running multi-component droplets then there is an rpvar which must be set to #f. (rpsetvar ‘dpm/rkmulticomponent? #f) For pure droplets you must set (rpsetvar ‘dpm/rkvaporization? #f) After that you must issue the command (dpm-parameters-changed) These RPvars switch to an Eulerian integration of the ODEs. Another workaround is trying to understand what is causing these messages. Typically this also indicates wrong settings, either of the DPM properties or of the numerical settings. Therefore, user should check thermodynamic consistency of DPM properties like latent heat of vaporization, specific heat capacities of gas and liquid, vapor pressure, etc. Another workaround might be to reduce the particle integration time step by disabling accuracy control and automated tracking scheme selection. In some cases this might lead to large integration time steps which might be efficient for the hydrodynamics but not for integrating the heat and mass transfer equations. By the way, since v14.0 we do not need to use these rpvars anymore. They are behind the Coupled Heat Mass solution in the numerics tab of the DPM panel model.
-
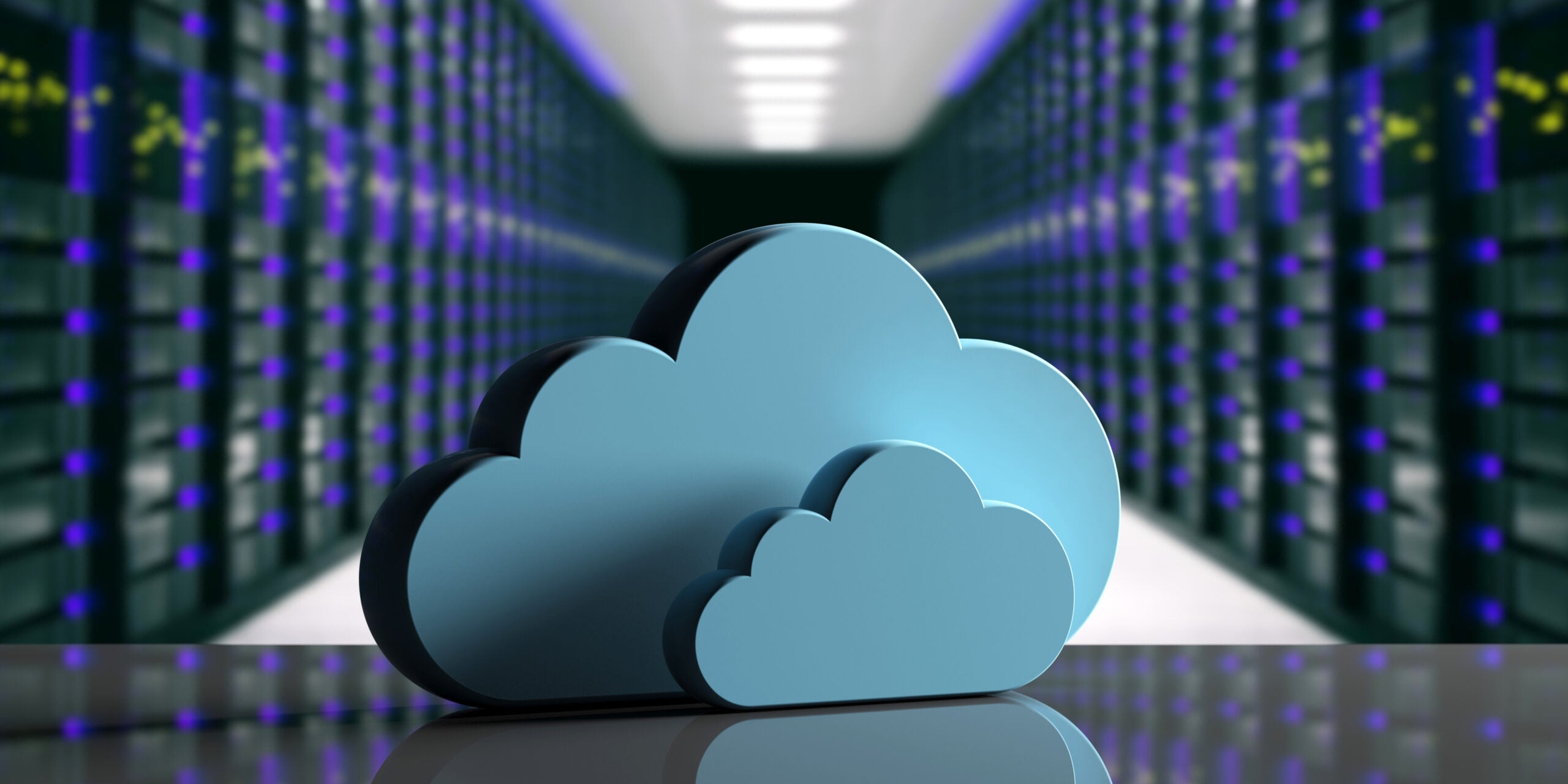
Introducing Ansys Electronics Desktop on Ansys Cloud
The Watch & Learn video article provides an overview of cloud computing from Electronics Desktop and details the product licenses and subscriptions to ANSYS Cloud Service that are...
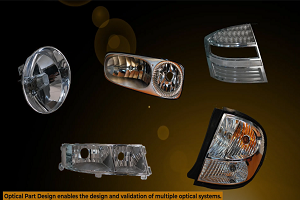
How to Create a Reflector for a Center High-Mounted Stop Lamp (CHMSL)
This video article demonstrates how to create a reflector for a center high-mounted stop lamp. Optical Part design in Ansys SPEOS enables the design and validation of multiple...
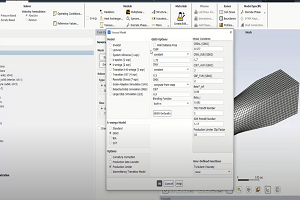
Introducing the GEKO Turbulence Model in Ansys Fluent
The GEKO (GEneralized K-Omega) turbulence model offers a flexible, robust, general-purpose approach to RANS turbulence modeling. Introducing 2 videos: Part 1 provides background information on the model and a...
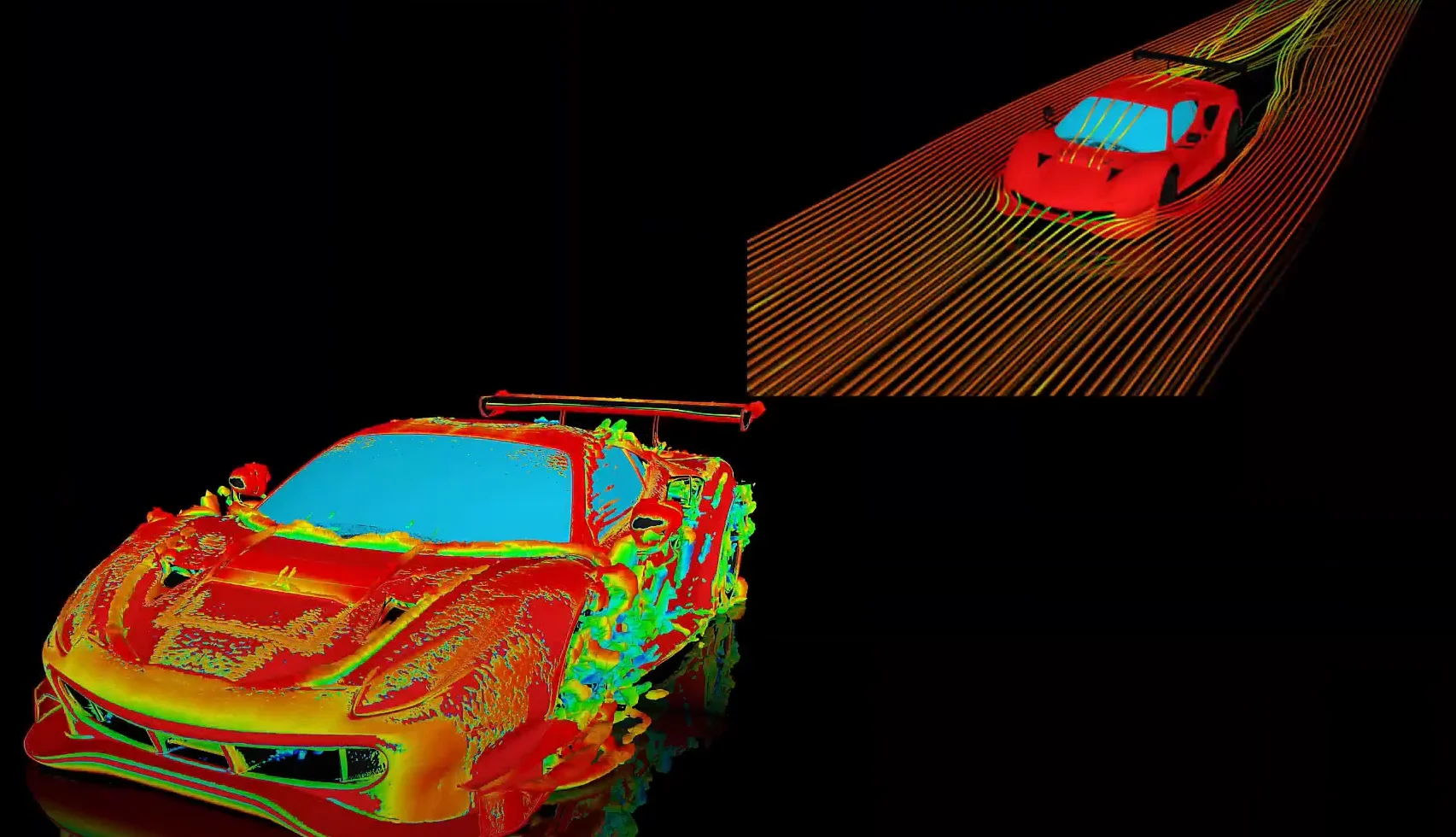
Postprocessing on Ansys EnSight
This video demonstrates exporting data from Fluent in EnSight Case Gold format, and it reviews the basic postprocessing capabilities of EnSight.
- Solver message during DPM calculation: “number of stepsize underflows during particle integration step is x”. What does it mean and how to get rid of it?
- What is the difference between the VOF model and the Eulerian model?
- ANSYS Fluent – Eulerian & Mixture Multiphase Models & Applications – Tips and Tricks
- ANSYS Fluent: Efficient Modeling of Spray Breakup using VOF-to-DPM Transition
- Mixing Tank Modeling in ANSYS Fluent
- What is the superficial velocity in multiphase flows?
- Hydrodynamics and Wave Impact Analysis
- ANSYS Fluent: Describing Cavitation in a Centrifugal Pump
- How do I use porous media in a multiphase flow?
- What is the meaning of VOF courant number and Global courant number in ANSYS Fluent Multiphase Model and how are they related?
© 2025 Copyright ANSYS, Inc. All rights reserved.