Tagged: 16, fluid-dynamics, General, polyflow, Viscoelastic Flow Simulation
-
-
March 17, 2023 at 8:58 am
FAQ
ParticipantShould one always select a viscosity ratio of 1/9 for a viscoelastic fluid model? Actually, it is not always necessary. A bit of historical and rheological background may help for this. – First simulations of 2D extrusion flow (free surface) were carried out with a Maxwell model (thus an Oldroyd model without this viscosity ratio), results were obtained at a modest level of elasticity. – Simulations were then carried out with a single mode PTT model originally without viscosity ratio, it gave rather poor results but improvement was found when a ratio of 1/9 was introduced. Actually, this value 1/9 guarantees that the shear stress remains a monotonic increasing function of shear rate. A non-zero value of this ratio is also needed for a single mode Giesekus model when alpha is larger than 0.5. – This ratio 1/9 has been subsequently applied to the Oldroyd model, results were obtained at a higher level of elasticity. As can be seen, for the PTT model, this viscosity ratio was needed for reasons of rheological stability. It provided some stability of the solver for the Oldroyd model. If one focuses on the stability from the point of view of rheology, this ratio may decrease when the number of modes increase, as the limit of stability (or the onset of instability in the viscosity curve) is pushed towards large shear rates. From the point of view of the momentum equation, things that are viscous are interesting (diffusive term in the momentum equation). The EVSS method helps for that but one must also make sure that the rheology is stable. POLYMAT does not consider stability issues but the user may decide a particular value for this ratio.
-
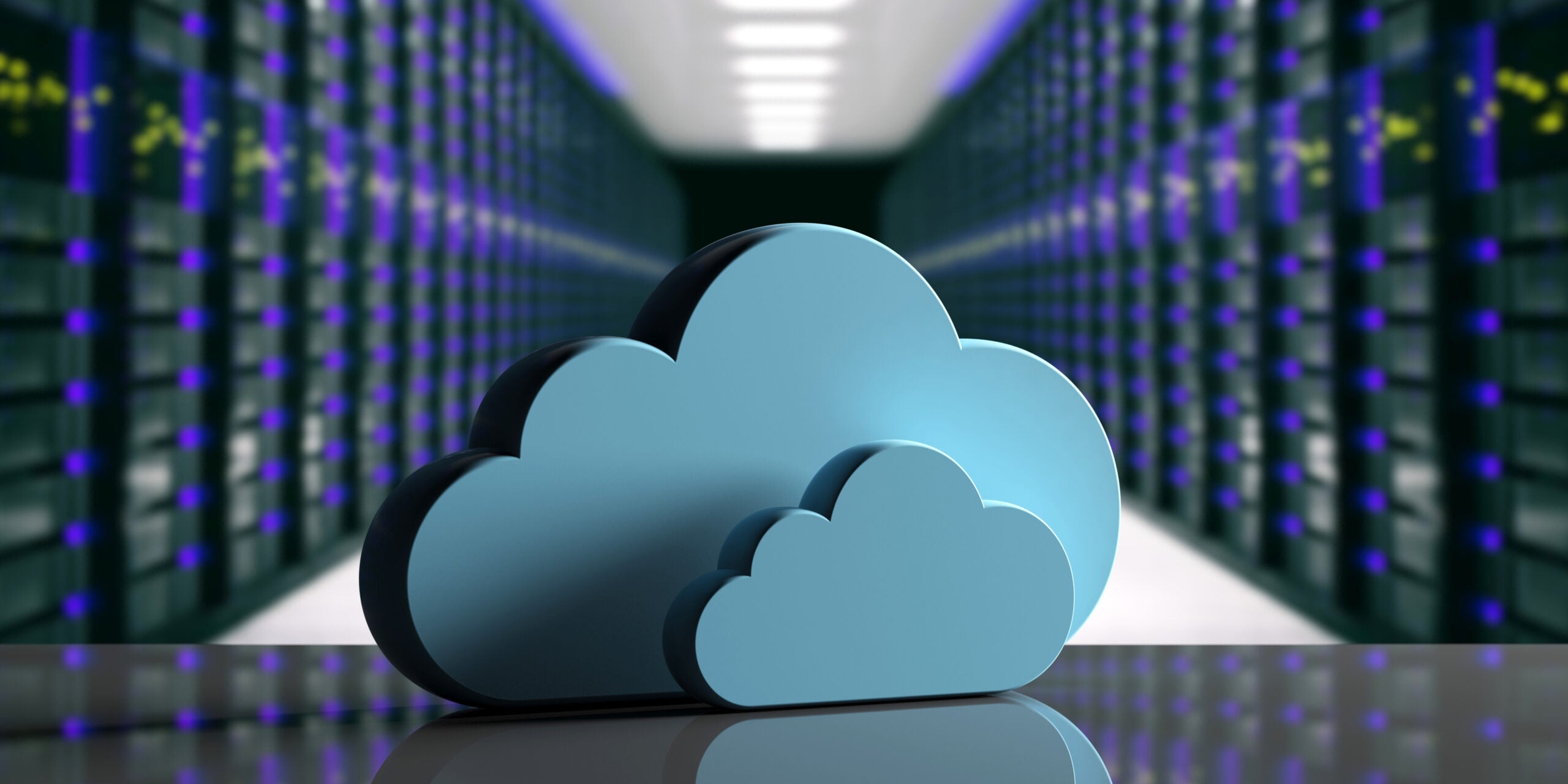
Introducing Ansys Electronics Desktop on Ansys Cloud
The Watch & Learn video article provides an overview of cloud computing from Electronics Desktop and details the product licenses and subscriptions to ANSYS Cloud Service that are...
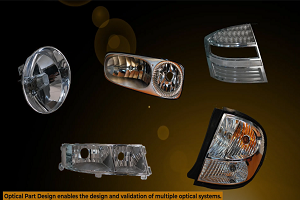
How to Create a Reflector for a Center High-Mounted Stop Lamp (CHMSL)
This video article demonstrates how to create a reflector for a center high-mounted stop lamp. Optical Part design in Ansys SPEOS enables the design and validation of multiple...
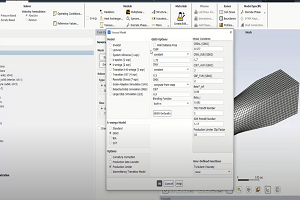
Introducing the GEKO Turbulence Model in Ansys Fluent
The GEKO (GEneralized K-Omega) turbulence model offers a flexible, robust, general-purpose approach to RANS turbulence modeling. Introducing 2 videos: Part 1Â provides background information on the model and a...
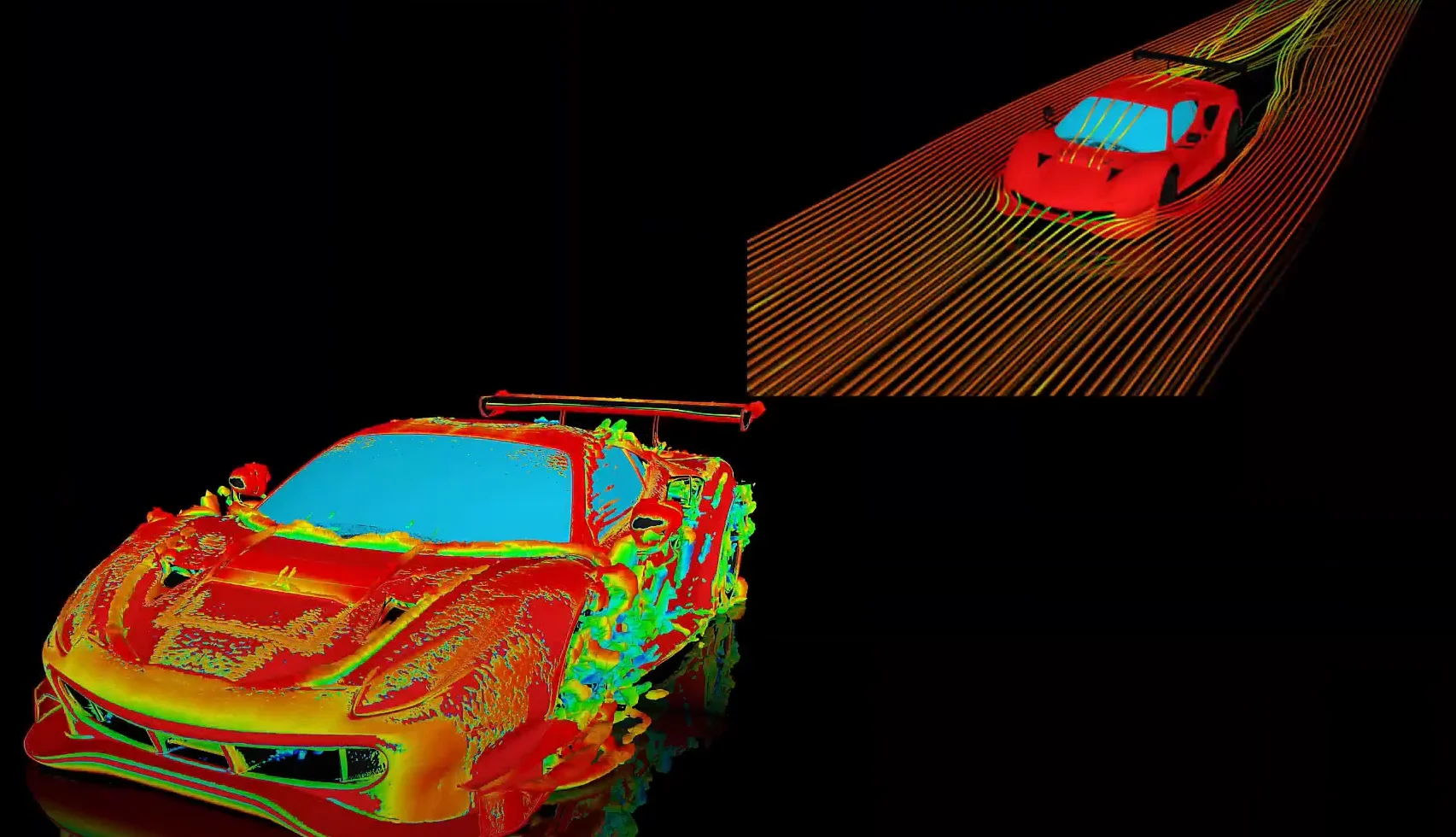
Postprocessing on Ansys EnSight
This video demonstrates exporting data from Fluent in EnSight Case Gold format, and it reviews the basic postprocessing capabilities of EnSight.
- How to overcome the model information incompatible with incoming mesh error?
- What are the requirements for an axisymmetric analysis?
- Skewness in ANSYS Meshing
- How to create and execute a FLUENT journal file?
- What is a .wbpz file and how can I use it?
- How can I Export and import boxes / Systems from one Workbench Project to another?
- What are pressure-based solver vs. density-based solver in FLUENT?
- Is there a way to get the volume of a register using expression ?
- How can I select interior faces and other entities that are inside the model?
- How to get information about mesh cell count and cell types in Fluent?
© 2025 Copyright ANSYS, Inc. All rights reserved.