Tagged: fluent, fluid-dynamics, General, General - FLUENT, Other
-
-
January 25, 2023 at 7:16 am
FAQ
ParticipantThe following restrictions exist for the macro heat exchanger models: 1. The core must be a 3D mesh with a cross-section that is approximately rectangular in shape. 2. The primary fluid streamwise direction (see Equation 6–1 in the Theory Guide) must be aligned with one of the three orthogonal axes defined by the rectangular core. 3. The pass-to-pass plane must be perpendicular to the primary fluid streamwise direction. 4. The two dimensions of the pass-to-pass plane can each be discretized into multiple macroscopic cells (macros), but in the direction perpendicular to this plane the macros cannot be subdivided. 5. It is highly recommended that the free-form Tet mesh is not used in the macro heat exchanger model. Instead, evenly distributed Hex/Wedge cells should be used for improved accuracy and a more robust solution process. 6. Flow acceleration effects are neglected in calculating the pressure loss coefficient. 7. For the simple effectiveness model, the primary fluid must have a capacity rate that is less than that of the auxiliary fluid. 8. Auxiliary fluid phase change cannot be modeled using the NTU model. 9. The macro-based method requires that an equal number of cells reside in each macro of equal size and shape. 10. The auxiliary fluid flow is assumed to be 1D. 11. The pass width has to be uniform. 12. Accuracy is not guaranteed when the mesh is not structured or layered. 13. Accuracy is not guaranteed when there is upstream diffusion of temperature at the inlet/outlet of the core. 14. Non-conformal meshes cannot be attached to the inlet/outlet of the core. An extra layer has to be created to avoid it.
-
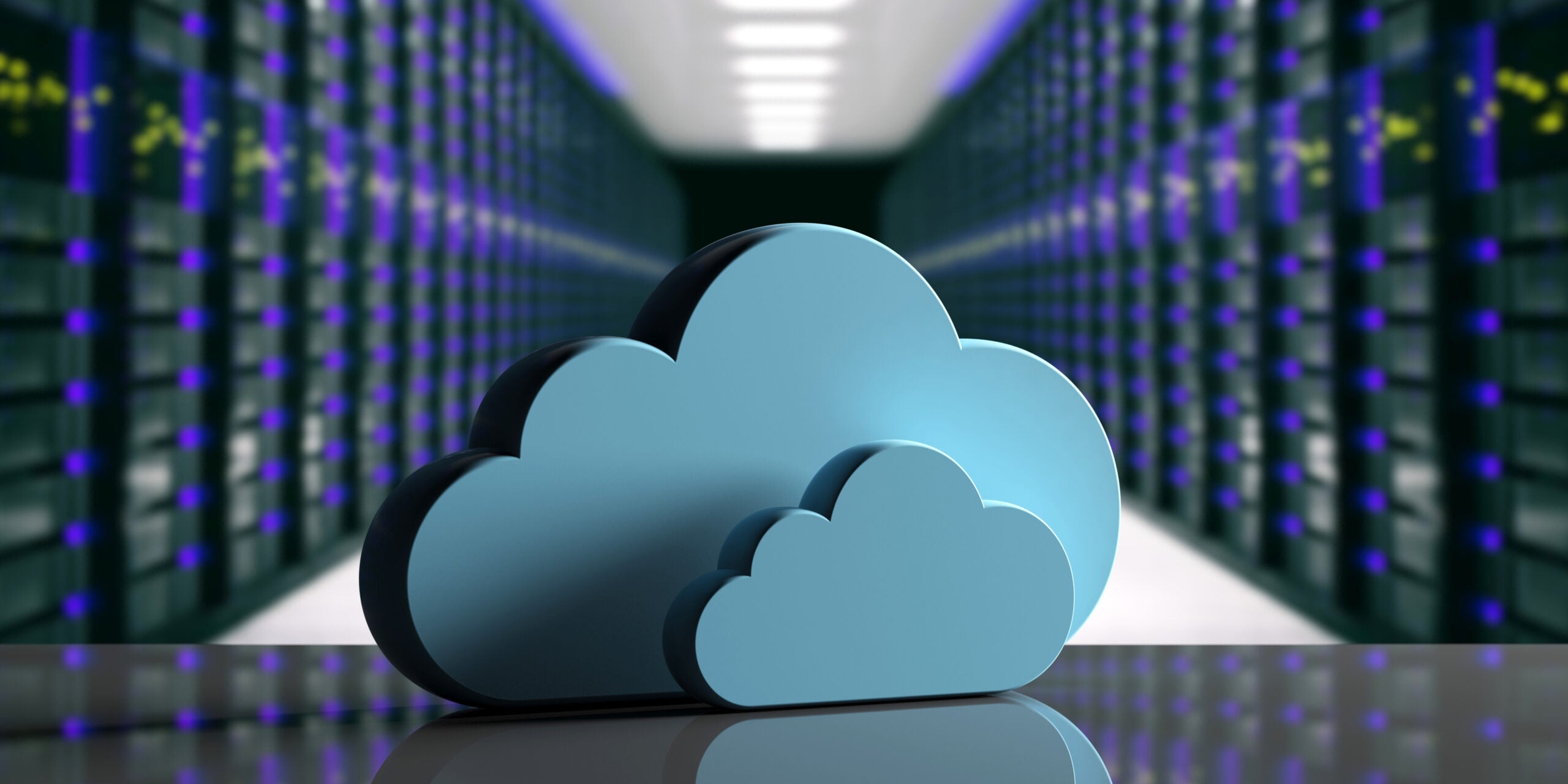
Introducing Ansys Electronics Desktop on Ansys Cloud
The Watch & Learn video article provides an overview of cloud computing from Electronics Desktop and details the product licenses and subscriptions to ANSYS Cloud Service that are...
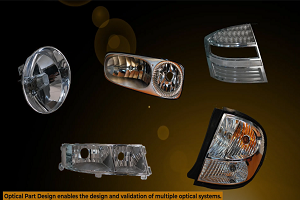
How to Create a Reflector for a Center High-Mounted Stop Lamp (CHMSL)
This video article demonstrates how to create a reflector for a center high-mounted stop lamp. Optical Part design in Ansys SPEOS enables the design and validation of multiple...
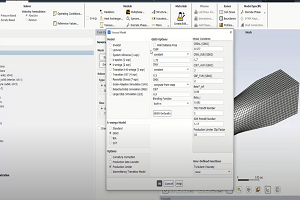
Introducing the GEKO Turbulence Model in Ansys Fluent
The GEKO (GEneralized K-Omega) turbulence model offers a flexible, robust, general-purpose approach to RANS turbulence modeling. Introducing 2 videos: Part 1Â provides background information on the model and a...
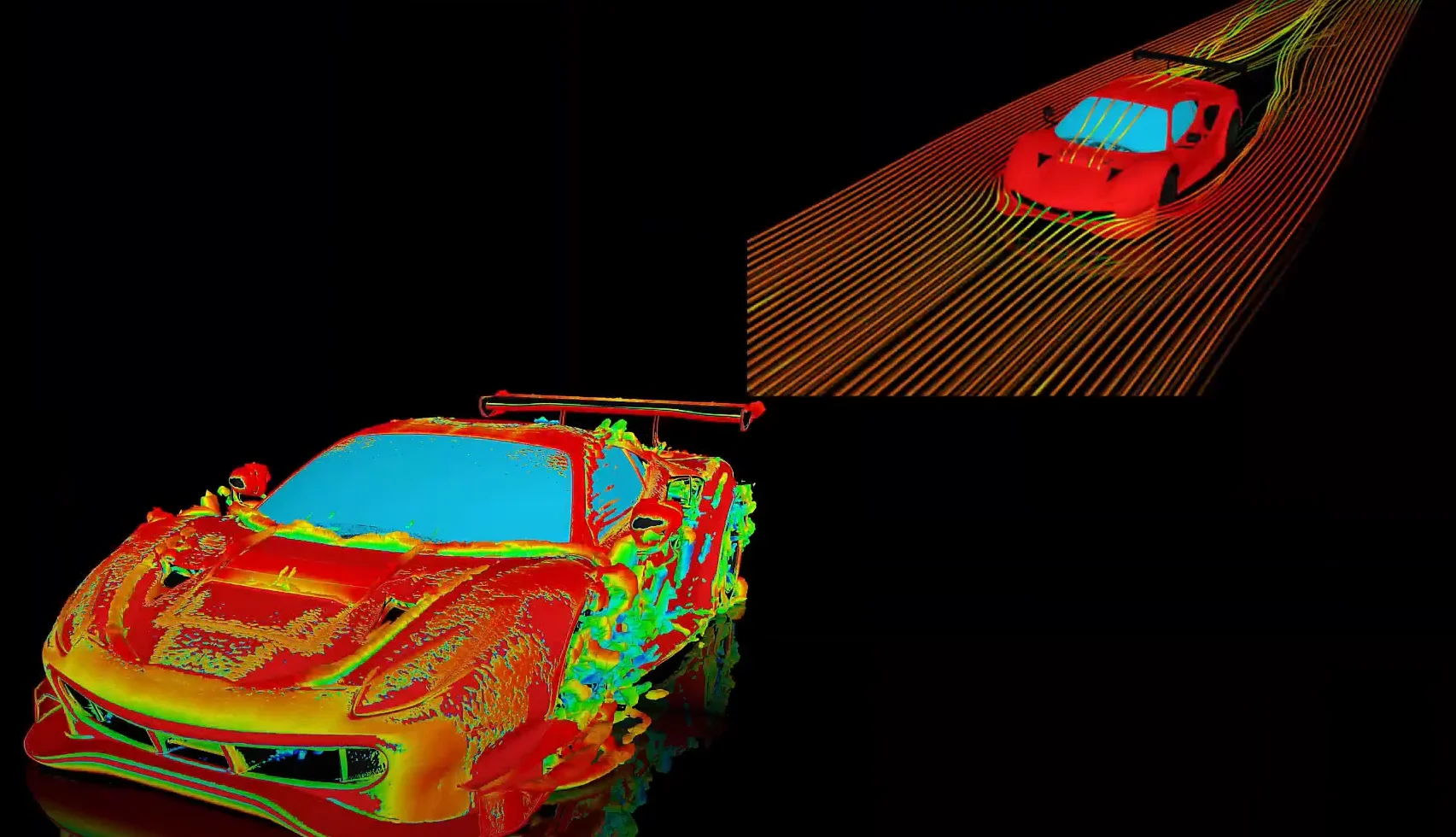
Postprocessing on Ansys EnSight
This video demonstrates exporting data from Fluent in EnSight Case Gold format, and it reviews the basic postprocessing capabilities of EnSight.
- How to overcome the model information incompatible with incoming mesh error?
- Skewness in ANSYS Meshing
- What are the requirements for an axisymmetric analysis?
- Ansys Fluent GPU Solver FAQs
- Is there a way to get the volume of a register using expression ?
- How to create and execute a FLUENT journal file?
- What are pressure-based solver vs. density-based solver in FLUENT?
- What is a .wbpz file and how can I use it?
- How to get information about mesh cell count and cell types in Fluent?
- How can I Export and import boxes / Systems from one Workbench Project to another?
© 2025 Copyright ANSYS, Inc. All rights reserved.