Is it possible to identify a Contact element based on the Contact real ID or element ID which is shown in the solve.out file, in some warning messages, directly in Mechanical without looking at the ds.dat file?
Tagged: 19.2, contact, General, mechanical, structural-and-thermal, structural-mechanics
-
-
March 17, 2023 at 9:00 am
FAQ
ParticipantYes. It is possible. Contact IDs shown in the solve.out can correspond to either Contacts in the tree or Remote points. Contacts defined in Tree: If it corresponds to Contacts defined in the tree, you can use the real ID number reported in the solve.out. Insert a contact tool and get the initial information. Then you can sort the contacts based on “real constant” column and locate the contact corresponding to the real ID number in the solve.out. Then, RMB on this row –> Go to Selected item in the Tree. Contacts created during the solve due to created remote points: We can access them (plot them to identify where they are) in post-processing using scoping option –> result file item. Steps are as shown below. 1. Simply put a new result object, say Total Deformation 2. Change scoping method from Geometry selection to Result File Item 3. Visualizing an element (contact elements for example) based on Element ID or Element Type Number – Change the Item Type –> Element Type IDs or Element IDs – Provide the corresponding Element number or Type number in Solver Component IDs. – Evaluate results. Please have a look at the below link in help documentation for further reference. https://ansyshelp.ansys.com/account/secured?returnurl=/Views/Secured/corp/v192/wb_sim/ds_sol_comp_output.html?q=result%20file%20item
-
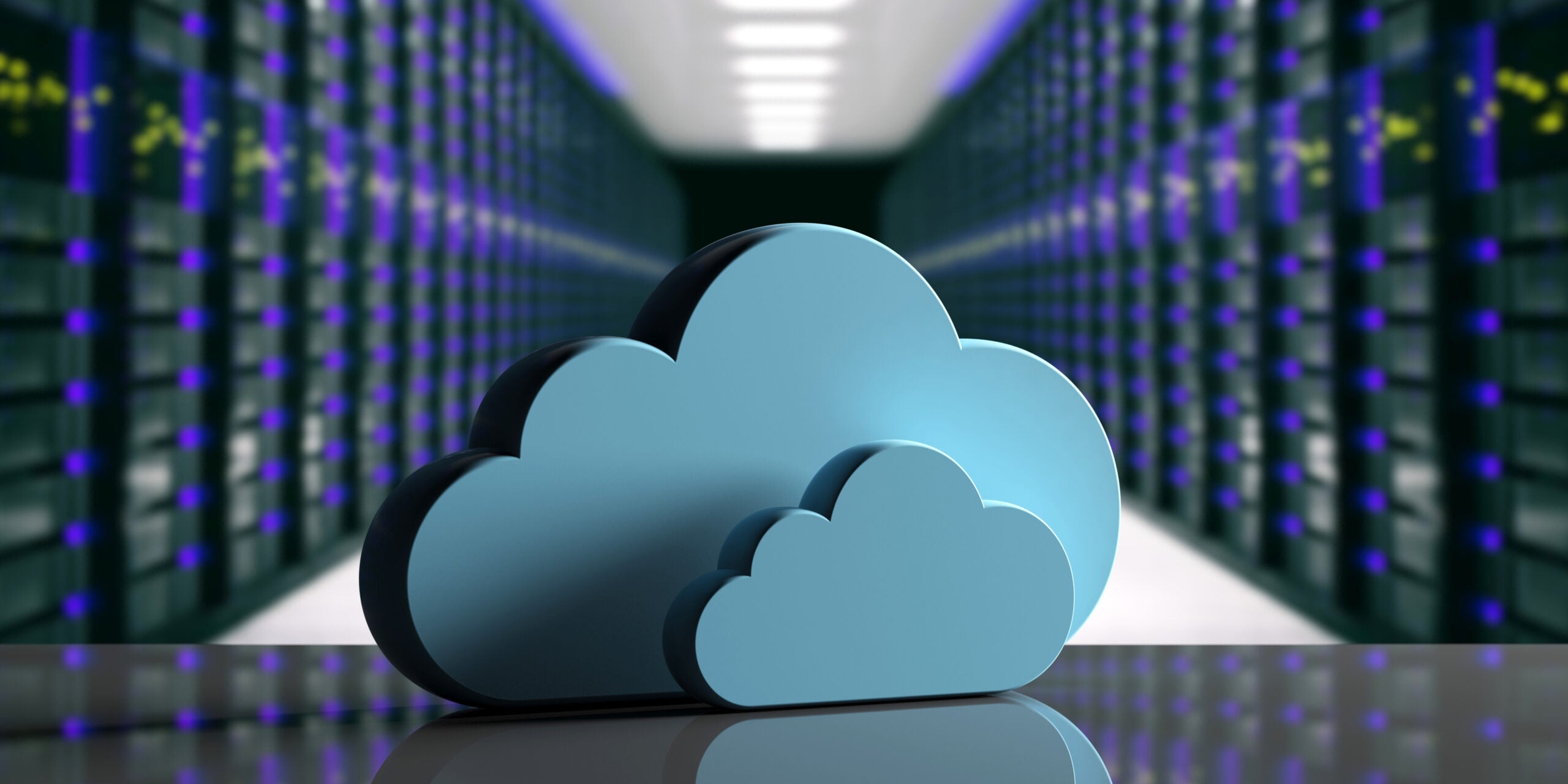
Introducing Ansys Electronics Desktop on Ansys Cloud
The Watch & Learn video article provides an overview of cloud computing from Electronics Desktop and details the product licenses and subscriptions to ANSYS Cloud Service that are...
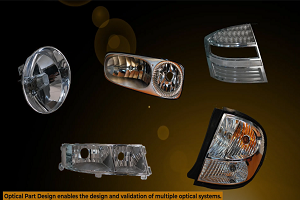
How to Create a Reflector for a Center High-Mounted Stop Lamp (CHMSL)
This video article demonstrates how to create a reflector for a center high-mounted stop lamp. Optical Part design in Ansys SPEOS enables the design and validation of multiple...
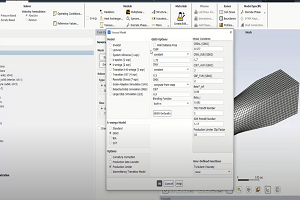
Introducing the GEKO Turbulence Model in Ansys Fluent
The GEKO (GEneralized K-Omega) turbulence model offers a flexible, robust, general-purpose approach to RANS turbulence modeling. Introducing 2 videos: Part 1 provides background information on the model and a...
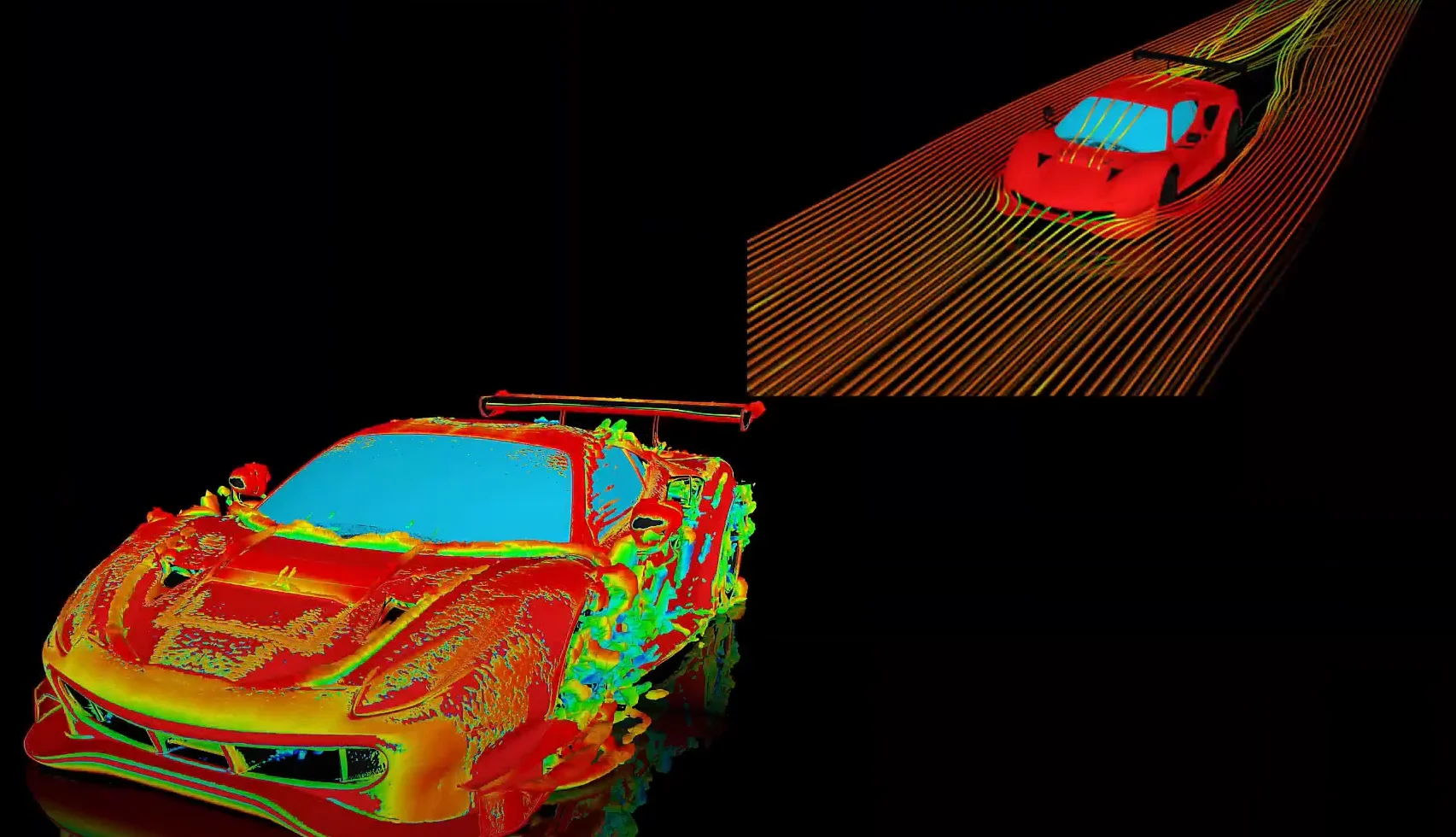
Postprocessing on Ansys EnSight
This video demonstrates exporting data from Fluent in EnSight Case Gold format, and it reviews the basic postprocessing capabilities of EnSight.
- How to reduce contact penetration?
- How to decide which side should be Contact and which should be target in Contact definition?
- What is the difference between secant and instantaneous coefficients of thermal expansion (CTE)?
- Does ECAD trace mapping support more than one type of trace material (usually copper) in the same layer?
- How to use the Newton-Raphson residuals option under Solution Information?
- How to plot stresses of a beam connection in Workbench?
- How can I understand Beam Probe results?
- How to find total heat flowing through a surface in Mechanical?
- Difference Between Environment Temperature and Reference Temperature in Mechanical
- How can I apply a controlled rotation in ANSYS Mechanical
© 2025 Copyright ANSYS, Inc. All rights reserved.