Is it better to update FKN (contact stiffness in the normal direction) at each equilibrium iteration, at each substep, or to never update it?
-
-
January 25, 2023 at 7:34 am
FAQ
ParticipantThe answer to the above should be evaluated by reviewing the amount of contact penetration–specifically, one should compare penetration values (in units of length) compared to the local and overall deformations in that direction. (In general, when using penalty-based methods like “Pure Penalty” or “Augmented Lagrange,” reviewing the amount of penetration as well as contact pressure distribution is needed.) The contact stiffness update algorithm may increase *or* decrease FKN, depending on the solution progress. The contact stiffness update algorithm looks at a “maximum allowable penetration” parameter FTOLN (which is automatically set by default, based on mesh density – a finer mesh has a smaller allowable penetration [more accuracy] than a coarser mesh), along with convergence behavior and current contact pressure values to determine whether to increase or decrease contact stiffness. One can override the default FTOLN value through the use of real constant #4. In Workbench Simulation, under the “Solution Information” branch, you can also track contact stiffness, contact penetration, etc. during the course of the solution using the “Result Tracker” feature. That helps to see what the contact algorithm is doing. While using the contact stiffness update algorithm is generally useful to balance accuracy and computational cost, it is unfortunately not substitute for evaluating the contact penetration that is present to determine whether or not the contact stiffness was too low.
-
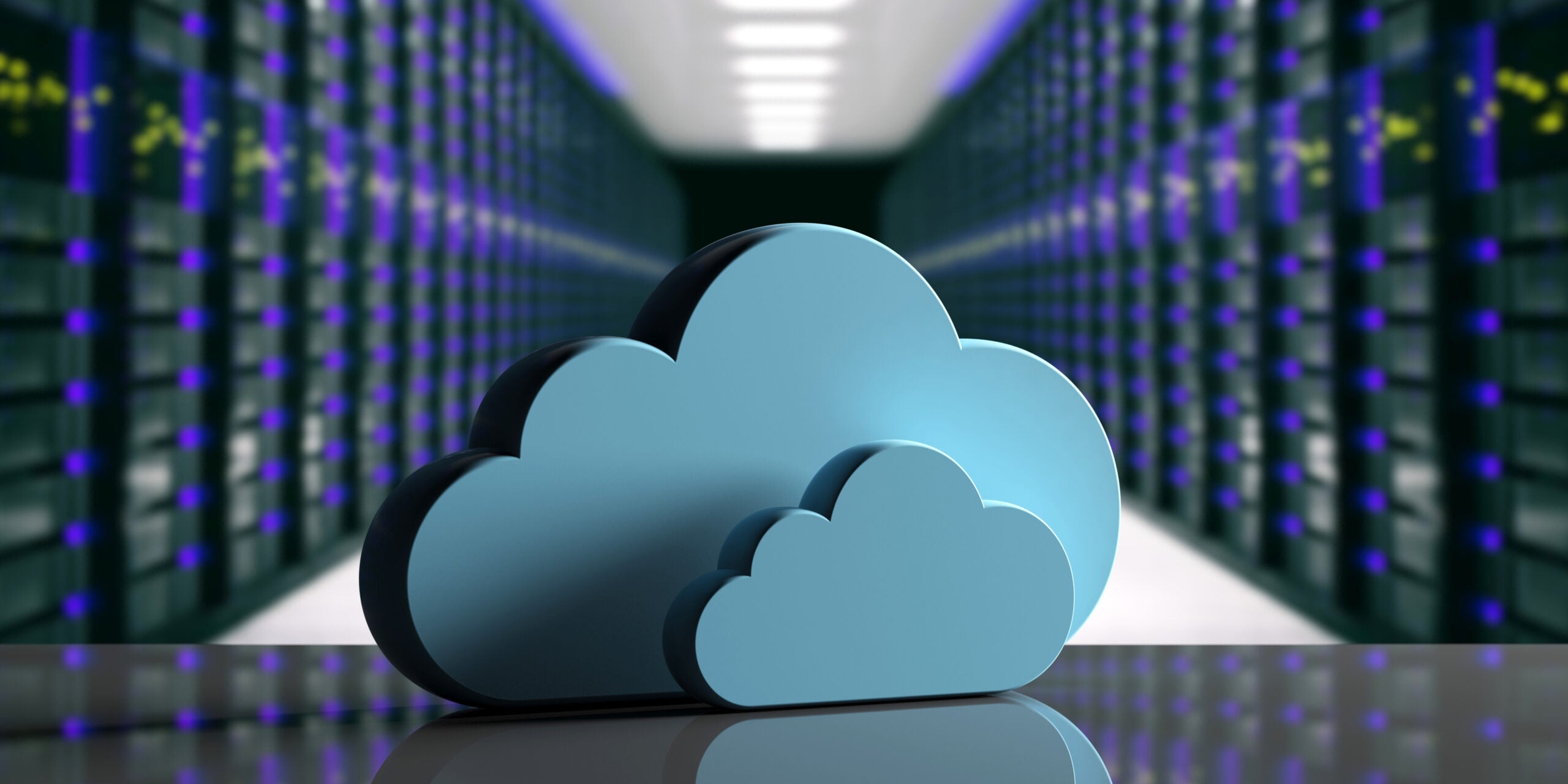
Introducing Ansys Electronics Desktop on Ansys Cloud
The Watch & Learn video article provides an overview of cloud computing from Electronics Desktop and details the product licenses and subscriptions to ANSYS Cloud Service that are...
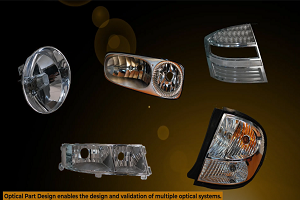
How to Create a Reflector for a Center High-Mounted Stop Lamp (CHMSL)
This video article demonstrates how to create a reflector for a center high-mounted stop lamp. Optical Part design in Ansys SPEOS enables the design and validation of multiple...
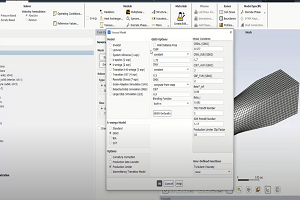
Introducing the GEKO Turbulence Model in Ansys Fluent
The GEKO (GEneralized K-Omega) turbulence model offers a flexible, robust, general-purpose approach to RANS turbulence modeling. Introducing 2 videos: Part 1 provides background information on the model and a...
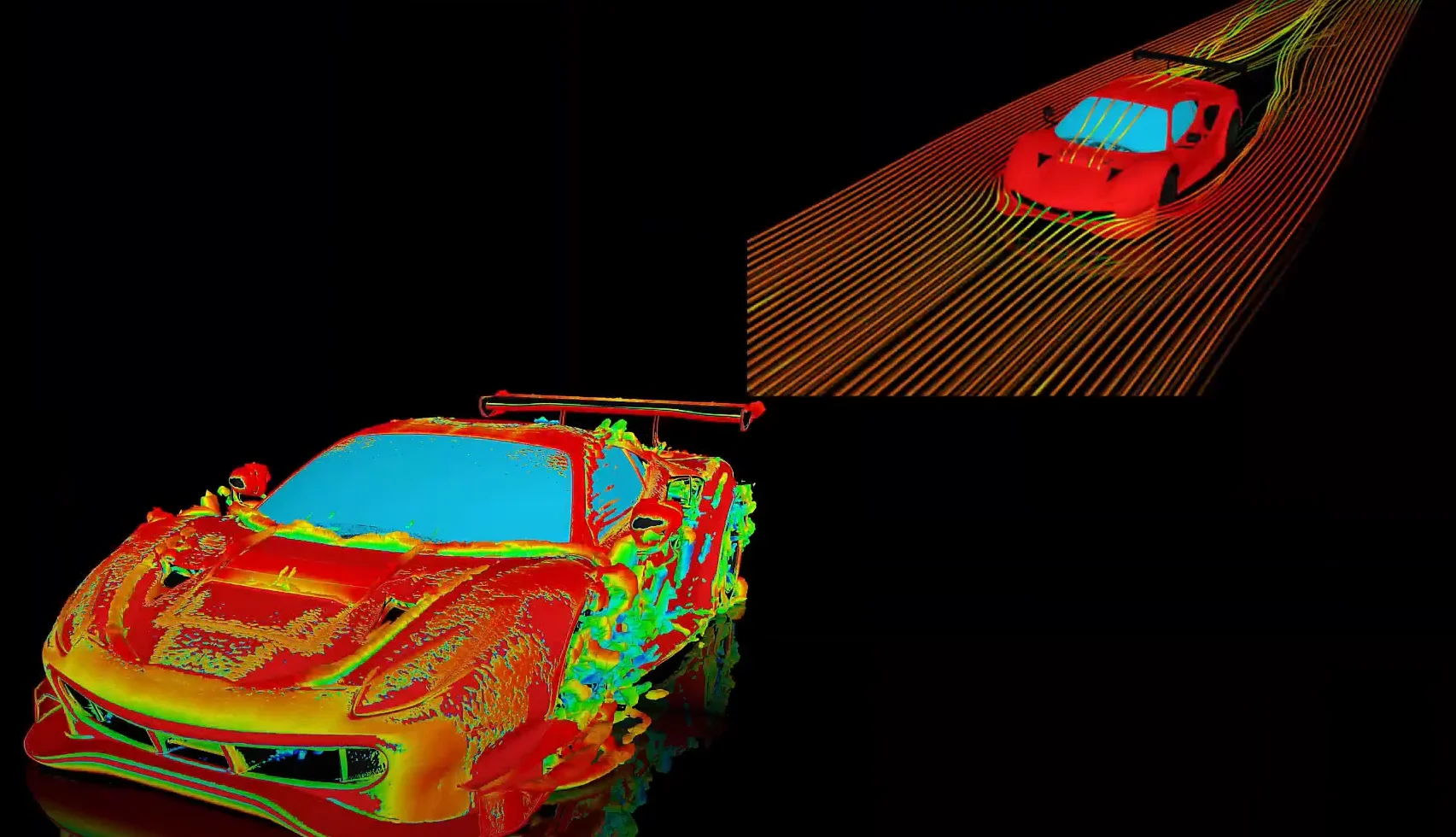
Postprocessing on Ansys EnSight
This video demonstrates exporting data from Fluent in EnSight Case Gold format, and it reviews the basic postprocessing capabilities of EnSight.
- How do I request ANSYS Mechanical to use more number of cores for solution?
- How to restore the corrupted project in ANSYS Workbench?
- How to deal with “”Problem terminated — energy error too large””?”
- Contact Definitions in ANSYS Workbench Mechanical
- How can I change the background color, font size settings of the avi animation exported from Mechanical? How can I improve the resolution of the video?
- There is a unit systems mismatch between the environments involved in the solution.
- How to transfer a material model(s) from one Analysis system to another within Workbench?
- How to obtain force reaction in a section ?
- What is the reason for this error message when mesher fails – “A software execution error occurred inside the mesher. The process suffered an unhandled exception or ran out of usable memory.”?
- How to change color for each body in Mechanical?
© 2025 Copyright ANSYS, Inc. All rights reserved.