I imported an assembly from my CAD system into DesignModeler. I turned the assembly into a multibody part and transfered it to Simulation. Simulation created contact elements between the parts even though it was a multibody part. I found that if I change the facet quality in DM from the default 5 to 10, Simulation recognized the multibody part and no contact is created (Tools > Options > DesignModeler > Graphics > Facet Quality). What’s wrong?
- Options > DesignModeler > Graphics > Facet Quality). What’s wrong?" target="_blank" rel="nofollow" title="LinkedIn">
- Options > DesignModeler > Graphics > Facet Quality). What’s wrong?" target="_blank" rel="nofollow" title="whatsapp">
- Options > DesignModeler > Graphics > Facet Quality). What’s wrong?" target="_blank" rel="nofollow" title="reddit">
- Options > DesignModeler > Graphics > Facet Quality). What’s wrong?" target="_blank" rel="nofollow" title="facebook">
Tagged: 10, General, Mechanical (f. Simulation), structural-mechanics
-
-
March 17, 2023 at 9:00 am
FAQ
ParticipantThe contact detection algorithm in Simulation is based on the tessellation of the geometry. The contact detection runs even when a multibody part is imported. If the topology between parts differs beyond a certain extent Simulation will place contact at the interface since continuous meshing is not possible. Most CAD systems have controls over the topology (or tessellation) that they use. Often this is a setting under the graphics controls. CAD users sometimes set this resolution to a lower value for faster graphics controls but don’t realize this will actually affect the resolution of the parts that are exported. Increasing the tessellation from the CAD source should result in expected behavior for other multibody parts.
-
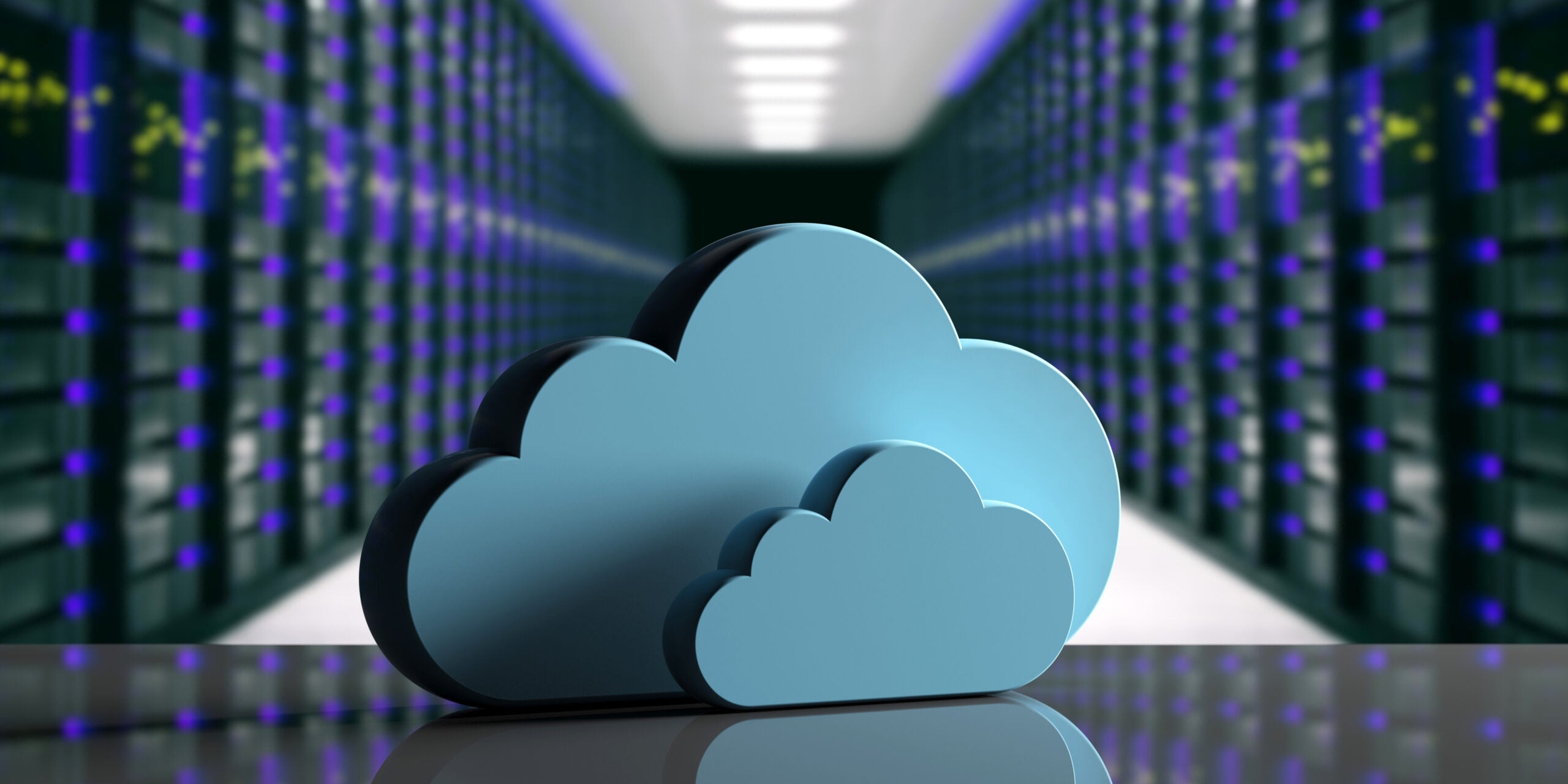
Introducing Ansys Electronics Desktop on Ansys Cloud
The Watch & Learn video article provides an overview of cloud computing from Electronics Desktop and details the product licenses and subscriptions to ANSYS Cloud Service that are...
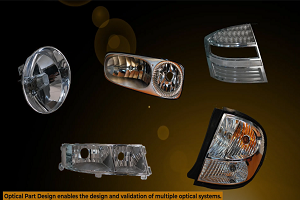
How to Create a Reflector for a Center High-Mounted Stop Lamp (CHMSL)
This video article demonstrates how to create a reflector for a center high-mounted stop lamp. Optical Part design in Ansys SPEOS enables the design and validation of multiple...
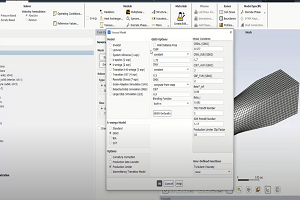
Introducing the GEKO Turbulence Model in Ansys Fluent
The GEKO (GEneralized K-Omega) turbulence model offers a flexible, robust, general-purpose approach to RANS turbulence modeling. Introducing 2 videos: Part 1Â provides background information on the model and a...
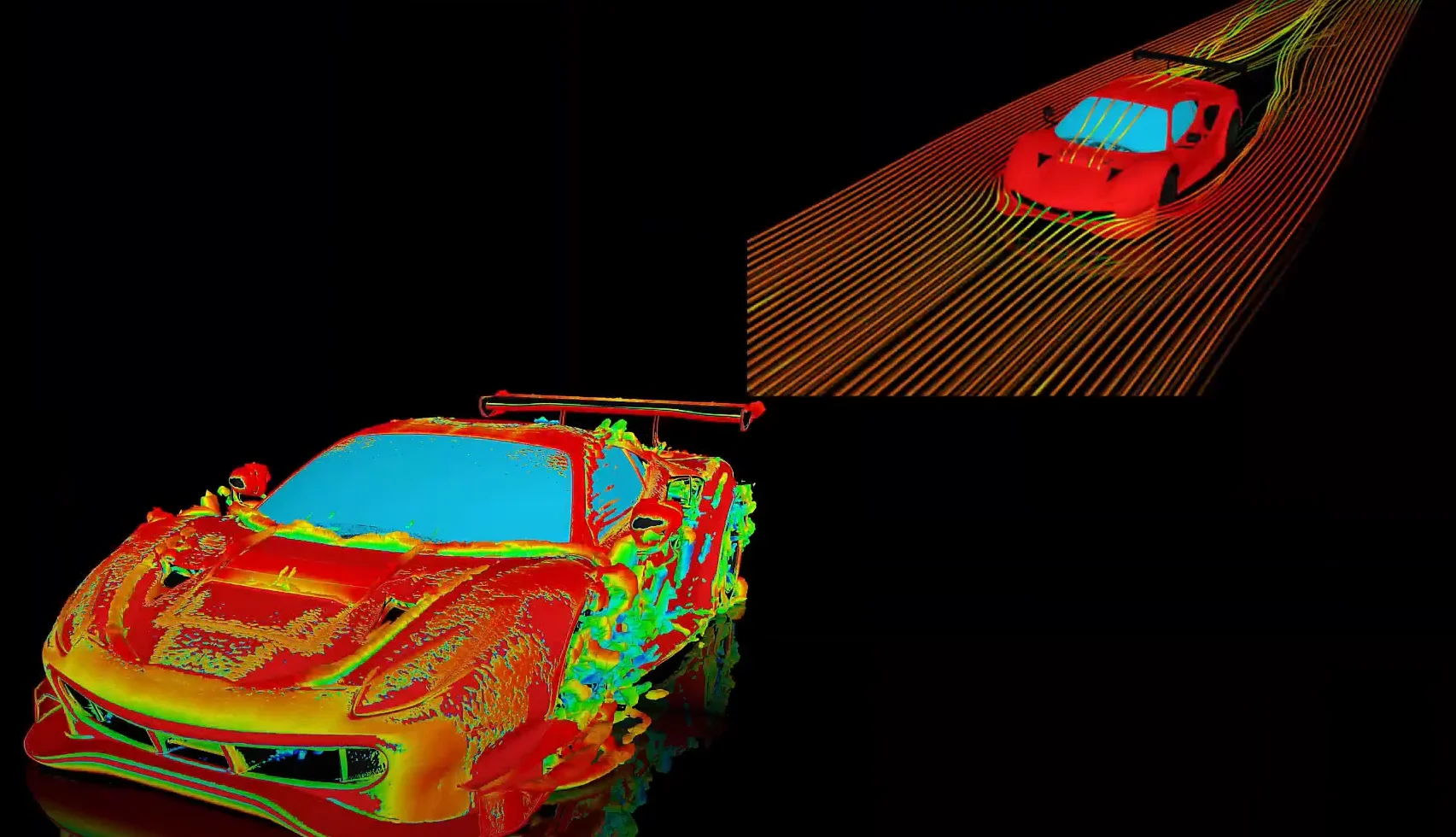
Postprocessing on Ansys EnSight
This video demonstrates exporting data from Fluent in EnSight Case Gold format, and it reviews the basic postprocessing capabilities of EnSight.
- How do I request ANSYS Mechanical to use more number of cores for solution?
- How to restore the corrupted project in ANSYS Workbench?
- How to deal with “”Problem terminated — energy error too large””?”
- Contact Definitions in ANSYS Workbench Mechanical
- There is a unit systems mismatch between the environments involved in the solution.
- How can I change the background color, font size settings of the avi animation exported from Mechanical? How can I improve the resolution of the video?
- How to transfer a material model(s) from one Analysis system to another within Workbench?
- How to obtain force reaction in a section ?
- How to change color for each body in Mechanical?
- How to resolve “Error: Invalid Geometry”?
© 2025 Copyright ANSYS, Inc. All rights reserved.