I am running a simulation in Forte with the spray model active. Beyond a certain Crank Angle, the simulation gets slower and slower (timestep reduction and solution recycling) Finally the solver stops with the error: Error occurred in wallfilm vaporization: The sum of fuel vapor mole fractions is zero at the surface of parcel # … What does this error mean? How can I prevent it from occurring?
Tagged: 19.2, Boundary/Initial Conditions, fluid-dynamics, Forte, Inlet/Outlet
-
-
June 5, 2023 at 7:06 am
FAQ
ParticipantThe error generally means that the area in the vicinity of the wall film has become flooded with liquid fuel. Usually, this is because the liquid fuel mass flow rate is too high, or because the spray parameters are preventing the droplets from evaporating quickly enough. Setting spray parameters in the absence of experimental data can be very difficult, so this error may be hard to prevent without a change in the modelling approach. The details of the spray are often secondary to the simulation, and spray modelling is quite computationally expensive. Since Forte simulations are already lengthy, a fuel vapor mass flow boundary condition has been introduced at Forte V 19.2 as an alternative to spray injection. The fuel vapor mass flow inlet provides a stable alternative to spray injection for simulations where spray data is insufficient/not the focus of the analysis. Using the new fuel vapour massflow inlet boundary condition should resolve the error and prevent the solution from recycling at a tiny timestep.
-
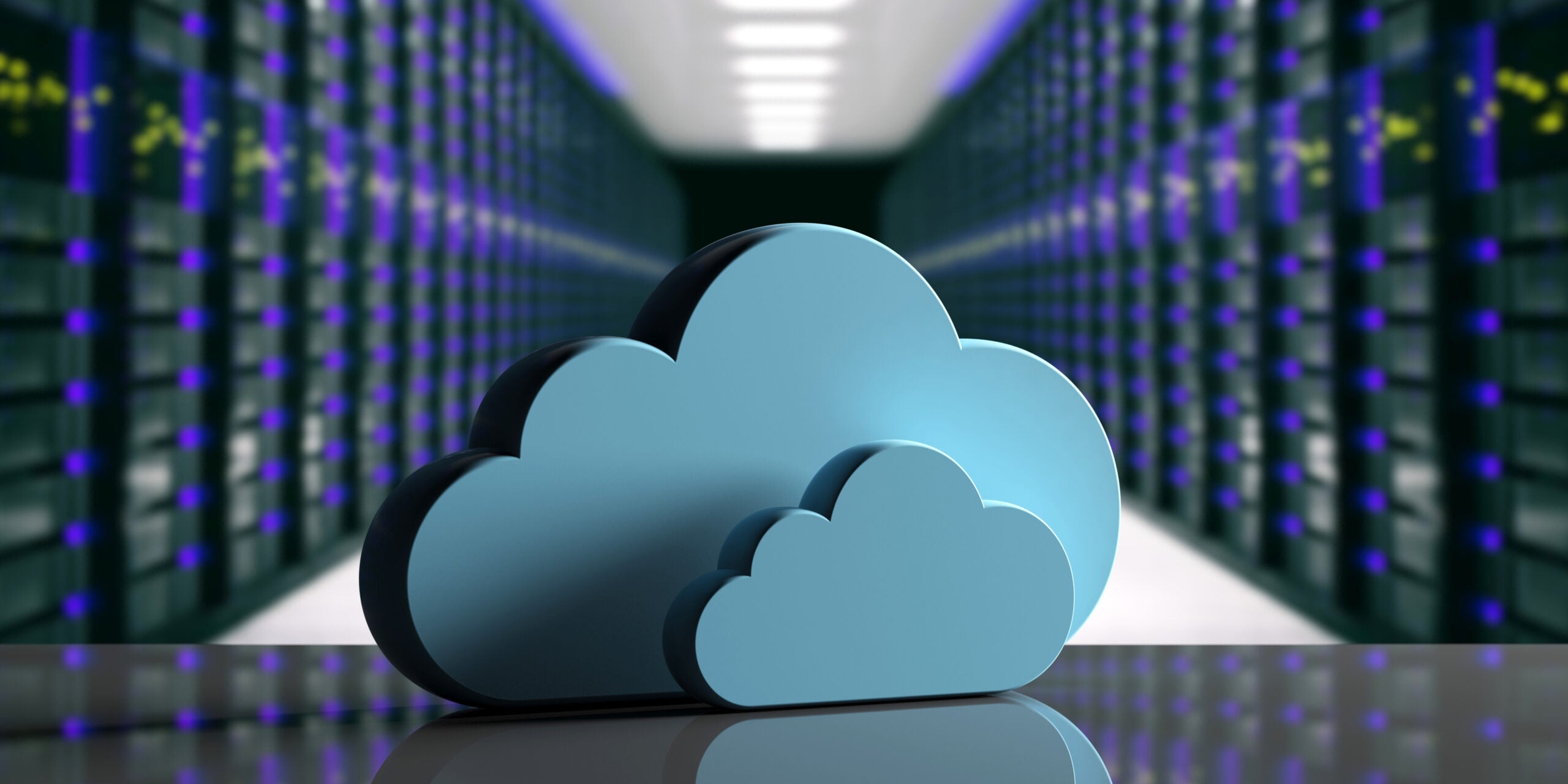
Introducing Ansys Electronics Desktop on Ansys Cloud
The Watch & Learn video article provides an overview of cloud computing from Electronics Desktop and details the product licenses and subscriptions to ANSYS Cloud Service that are...
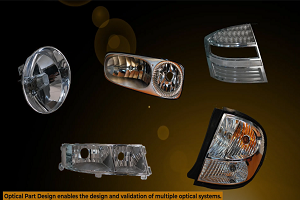
How to Create a Reflector for a Center High-Mounted Stop Lamp (CHMSL)
This video article demonstrates how to create a reflector for a center high-mounted stop lamp. Optical Part design in Ansys SPEOS enables the design and validation of multiple...
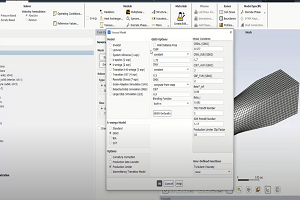
Introducing the GEKO Turbulence Model in Ansys Fluent
The GEKO (GEneralized K-Omega) turbulence model offers a flexible, robust, general-purpose approach to RANS turbulence modeling. Introducing 2 videos: Part 1Â provides background information on the model and a...
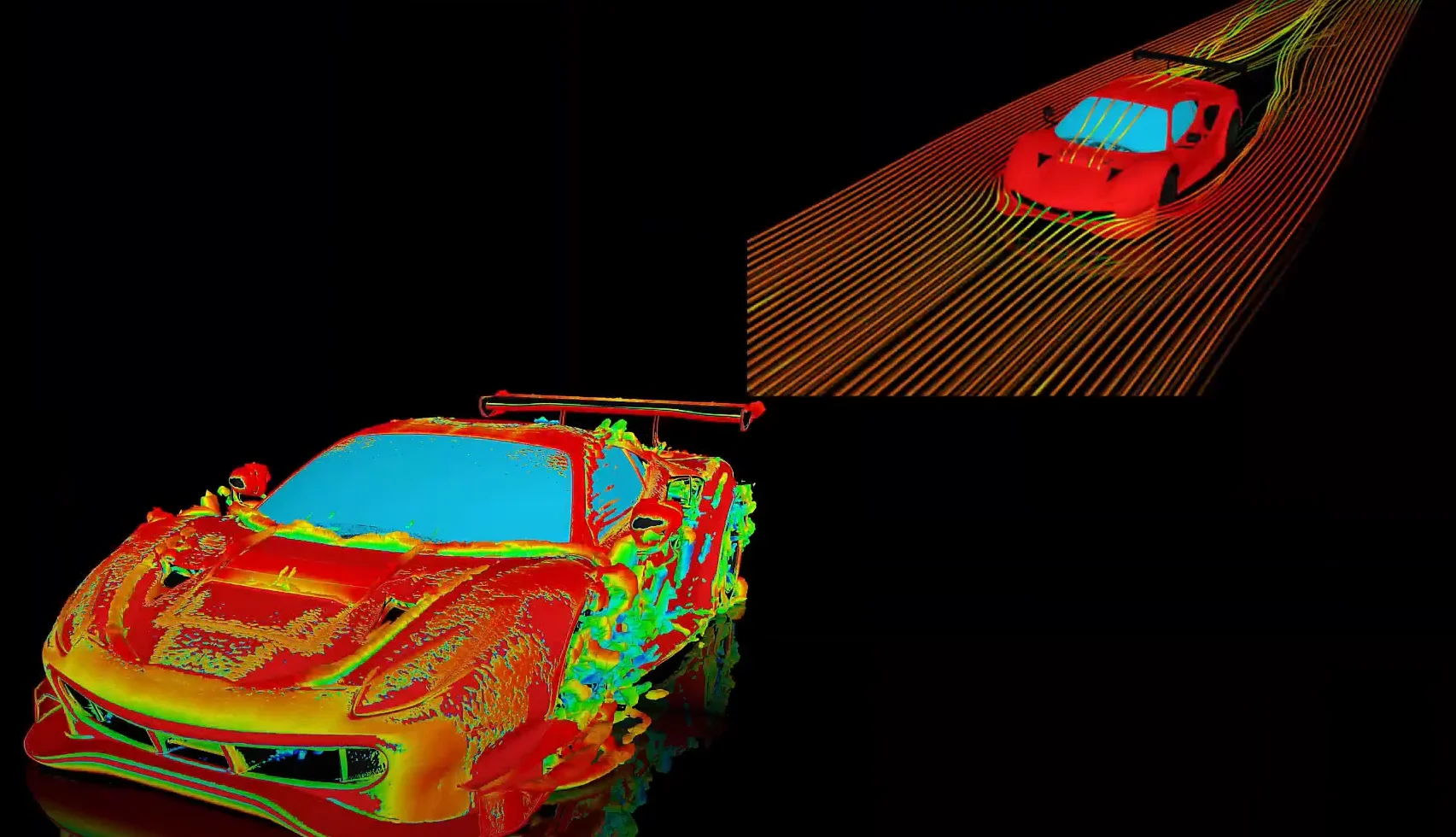
Postprocessing on Ansys EnSight
This video demonstrates exporting data from Fluent in EnSight Case Gold format, and it reviews the basic postprocessing capabilities of EnSight.
- How to overcome the model information incompatible with incoming mesh error?
- Skewness in ANSYS Meshing
- What are the requirements for an axisymmetric analysis?
- Ansys Fluent GPU Solver FAQs
- Is there a way to get the volume of a register using expression ?
- How to create and execute a FLUENT journal file?
- What are pressure-based solver vs. density-based solver in FLUENT?
- What is a .wbpz file and how can I use it?
- How to get information about mesh cell count and cell types in Fluent?
- How can I Export and import boxes / Systems from one Workbench Project to another?
© 2025 Copyright ANSYS, Inc. All rights reserved.