Tagged: 18.2, contact, General, mechanical, structural-and-thermal, structural-mechanics
-
-
August 25, 2023 at 12:16 pm
Solution
ParticipantThere is always mesh discretization issues with contact between curved surfaces. In general, curved contact and target surfaces can be well approximated by linear (lower order) or quadratic (higher order) contact and target elements when the mesh is sufficiently refined. However, in certain circumstances this is not the case; for example, when linear elements are used or when the midside nodes of quadratic elements do not lie exactly on the initial curved geometry. Thus, in some contact applications, using a faceted surface in place of the true curved geometry can significantly affect the accuracy of contact stresses. These issues are minimal if the meshes on the two surfaces match. Contact matches enable to match mesh nodes between topologically disconnected solids within a specified tolerance. In attached WB file, contact status is shown with the contact matches used to match the nodes on contact surface Similar contact status result can be obtained for a coarse mesh using Geometry correction option in the details of the contact. The geometry correction option was implemented to help resolve these issues for non-matching meshes. The Smoothing option in the geometry correction enables you to improve the accuracy of circular edges (2D) and spherical or revolute surfaces (3D) by evaluating the contact detection based on the exact geometry instead of the mesh. In attached WB file, please check the contact status for the system with geometry correction “smoothing” enabled. If you set the contact and target correction options to “smoothing” in the Details Windows of the contact, the non-matching mesh results should closely agree with the mesh matching results.
Attachments:
1. 2051816.zip
-
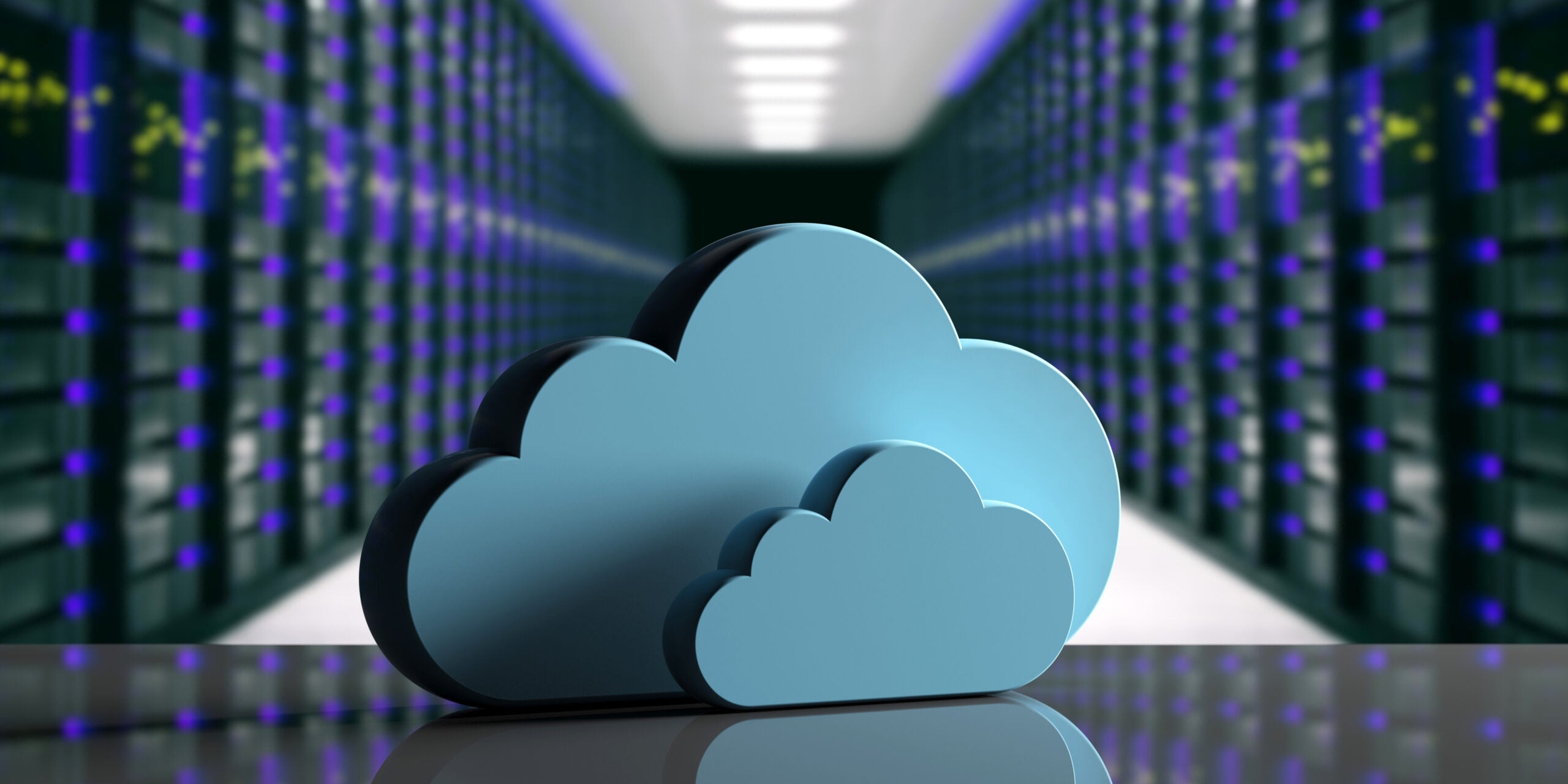
Introducing Ansys Electronics Desktop on Ansys Cloud
The Watch & Learn video article provides an overview of cloud computing from Electronics Desktop and details the product licenses and subscriptions to ANSYS Cloud Service that are...
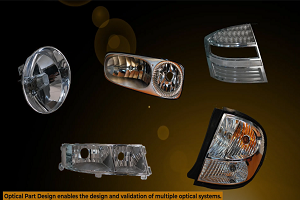
How to Create a Reflector for a Center High-Mounted Stop Lamp (CHMSL)
This video article demonstrates how to create a reflector for a center high-mounted stop lamp. Optical Part design in Ansys SPEOS enables the design and validation of multiple...
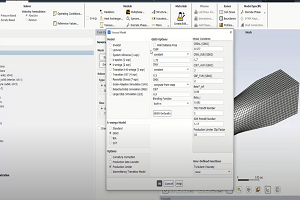
Introducing the GEKO Turbulence Model in Ansys Fluent
The GEKO (GEneralized K-Omega) turbulence model offers a flexible, robust, general-purpose approach to RANS turbulence modeling. Introducing 2 videos: Part 1Â provides background information on the model and a...
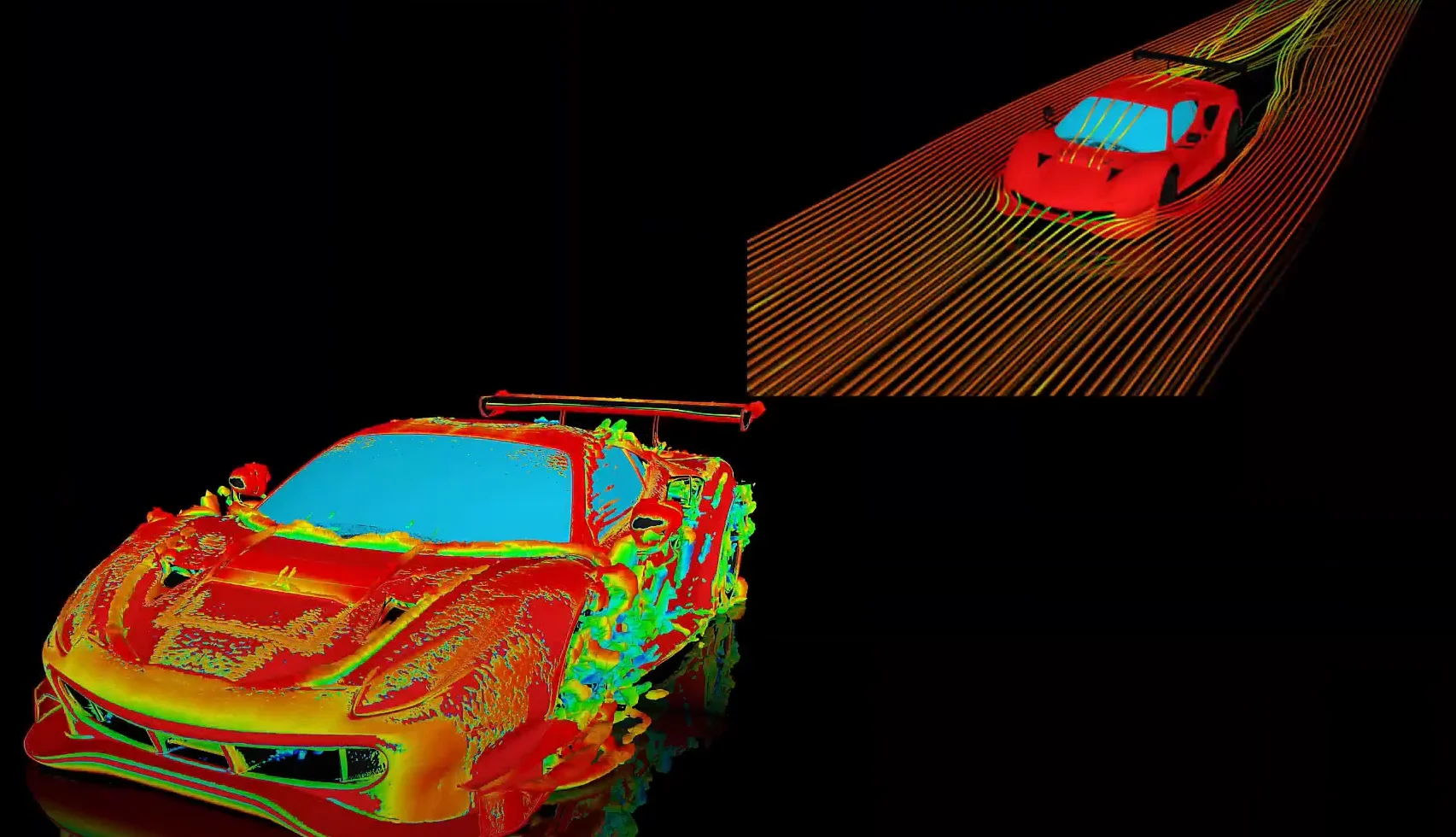
Postprocessing on Ansys EnSight
This video demonstrates exporting data from Fluent in EnSight Case Gold format, and it reviews the basic postprocessing capabilities of EnSight.
- How to reduce contact penetration?
- How to decide which side should be Contact and which should be target in Contact definition?
- What is the difference between secant and instantaneous coefficients of thermal expansion (CTE)?
- Does ECAD trace mapping support more than one type of trace material (usually copper) in the same layer?
- How to use the Newton-Raphson residuals option under Solution Information?
- How to plot stresses of a beam connection in Workbench?
- How can I understand Beam Probe results?
- How to find total heat flowing through a surface in Mechanical?
- Difference Between Environment Temperature and Reference Temperature in Mechanical
- How can I apply a controlled rotation in ANSYS Mechanical
© 2025 Copyright ANSYS, Inc. All rights reserved.