-
-
June 5, 2023 at 7:04 am
FAQ
ParticipantWhen you’re using explicit time integration, there is no magic cure for long run times associated with simulating very small geometries over relatively long periods of time. Mass-scaling carries a burden of having to confirm that the addition of nonphysical mass does not significantly affect the results (see FAQ KM 2040217). A similar burden exists when time-scaling is employed. Time-scaling is a technique where the loading rate is increased and thus the simulation time is shortened in order to reduce the required number of timesteps. Make sure that your timestep is not being controlled by only a few small or stiff elements by searching in the d3hsp file for the string “smallest”. If there are only a few controlling elements, you can remesh in the vicinity of those elements or perhaps make them rigid. Though it’s rather obvious, run only as long as is necessary. This means in the case of a drop simulation, assigning an initial velocity to the dropped object and placing it a very small distance from the landing surface. After impact, run only long enough to get the results you need. Be aware that for lengthy simulations where the number of timesteps goes above half a million or so, you’d be well advised to use a double precision executable of LS-DYNA to minimize error due to roundoff. Running double precision carries with it a CPU penalty of around 30%. Automatic explicit/implicit switching may be an option. Using this technique, the user can specify time windows in which implicit time integration is used as opposed to explicit time integration. An advantage of implicit time integration is that timesteps are not tied to element size and can thus be much larger. Of course, an implicit timestep is also much more expensive in terms of CPU calculations. Further, not all LS-DYNA features and materials are implemented for implicit analysis at this time (though most are).
-
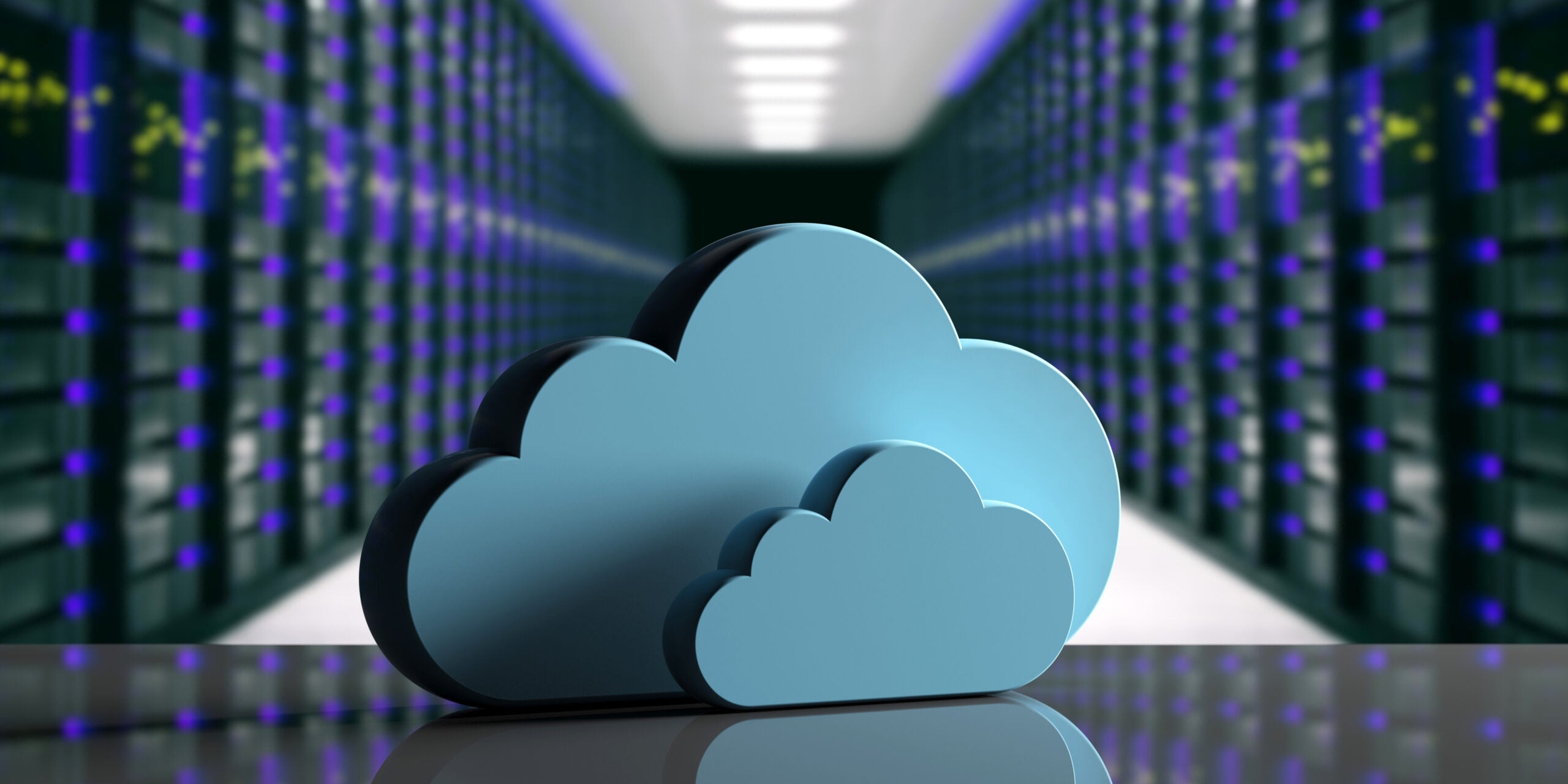
Introducing Ansys Electronics Desktop on Ansys Cloud
The Watch & Learn video article provides an overview of cloud computing from Electronics Desktop and details the product licenses and subscriptions to ANSYS Cloud Service that are...
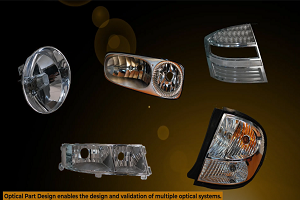
How to Create a Reflector for a Center High-Mounted Stop Lamp (CHMSL)
This video article demonstrates how to create a reflector for a center high-mounted stop lamp. Optical Part design in Ansys SPEOS enables the design and validation of multiple...
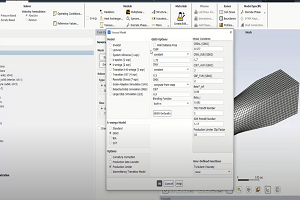
Introducing the GEKO Turbulence Model in Ansys Fluent
The GEKO (GEneralized K-Omega) turbulence model offers a flexible, robust, general-purpose approach to RANS turbulence modeling. Introducing 2 videos: Part 1 provides background information on the model and a...
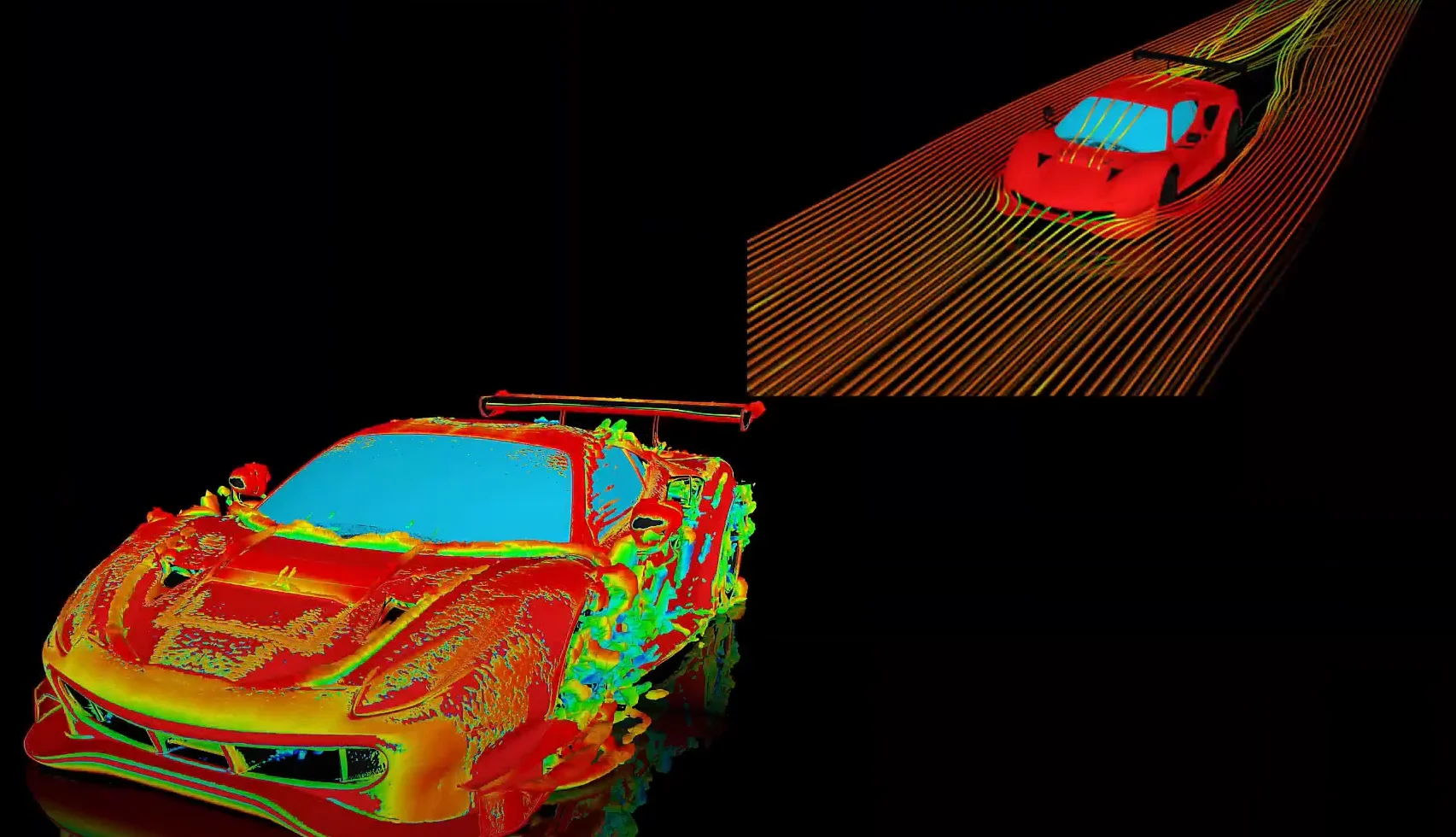
Postprocessing on Ansys EnSight
This video demonstrates exporting data from Fluent in EnSight Case Gold format, and it reviews the basic postprocessing capabilities of EnSight.
- How do I request ANSYS Mechanical to use more number of cores for solution?
- How to restore the corrupted project in ANSYS Workbench?
- How to deal with “”Problem terminated — energy error too large””?”
- Contact Definitions in ANSYS Workbench Mechanical
- How can I change the background color, font size settings of the avi animation exported from Mechanical? How can I improve the resolution of the video?
- There is a unit systems mismatch between the environments involved in the solution.
- How to transfer a material model(s) from one Analysis system to another within Workbench?
- How to obtain force reaction in a section ?
- What is the reason for this error message when mesher fails – “A software execution error occurred inside the mesher. The process suffered an unhandled exception or ran out of usable memory.”?
- How to change color for each body in Mechanical?
© 2025 Copyright ANSYS, Inc. All rights reserved.