How can I control the rate of mesh size away from the surface in ICEM CFD Tetra ? For instance, I have a surface with mesh size 2 and a volume mesh size of 16. What is the best way to control the way tetra size increases from 2 through to 16 away from the surface?
Tagged: 17.2, fluid-dynamics, icem-cfd, meshing, Tetra/Prism
-
-
March 17, 2023 at 8:58 am
FAQ
ParticipantThere are two mesh controls in ICEM that can be used to control the transitioning of the mesh away from the surface: 1) A Tetra Size Ratio can be specified for each surface. This controls the rate of growth of the mesh away from the surface. It acts like a radius of influence, extending the surface mesh control further into the domain, but still allowing the minimum size of 2 at the surface. 2) There is also a Tetra Width parameter that can be specified for surfaces. This parameter can be used to delay expansion around objects where a lot of resolution is required due to wakes or other turbulent structures, or for mechanical stresses. The number entered for “Width” on a given surface is the number of volume elements immediately off the surface that have a size of 2. Beyond that, the mesh will expand at the given Tetra size ratio until the maximum size of 16 is reached. NOTE: The Octree mesher will not obey the Tetra Size Ratio or Width controls. Its expansion ratios are dictated by the Octree meshing algorithm. You will need to run the Delauney mesher on the smoothed Octree mesh in order to get a mesh with the specified sizings.
-
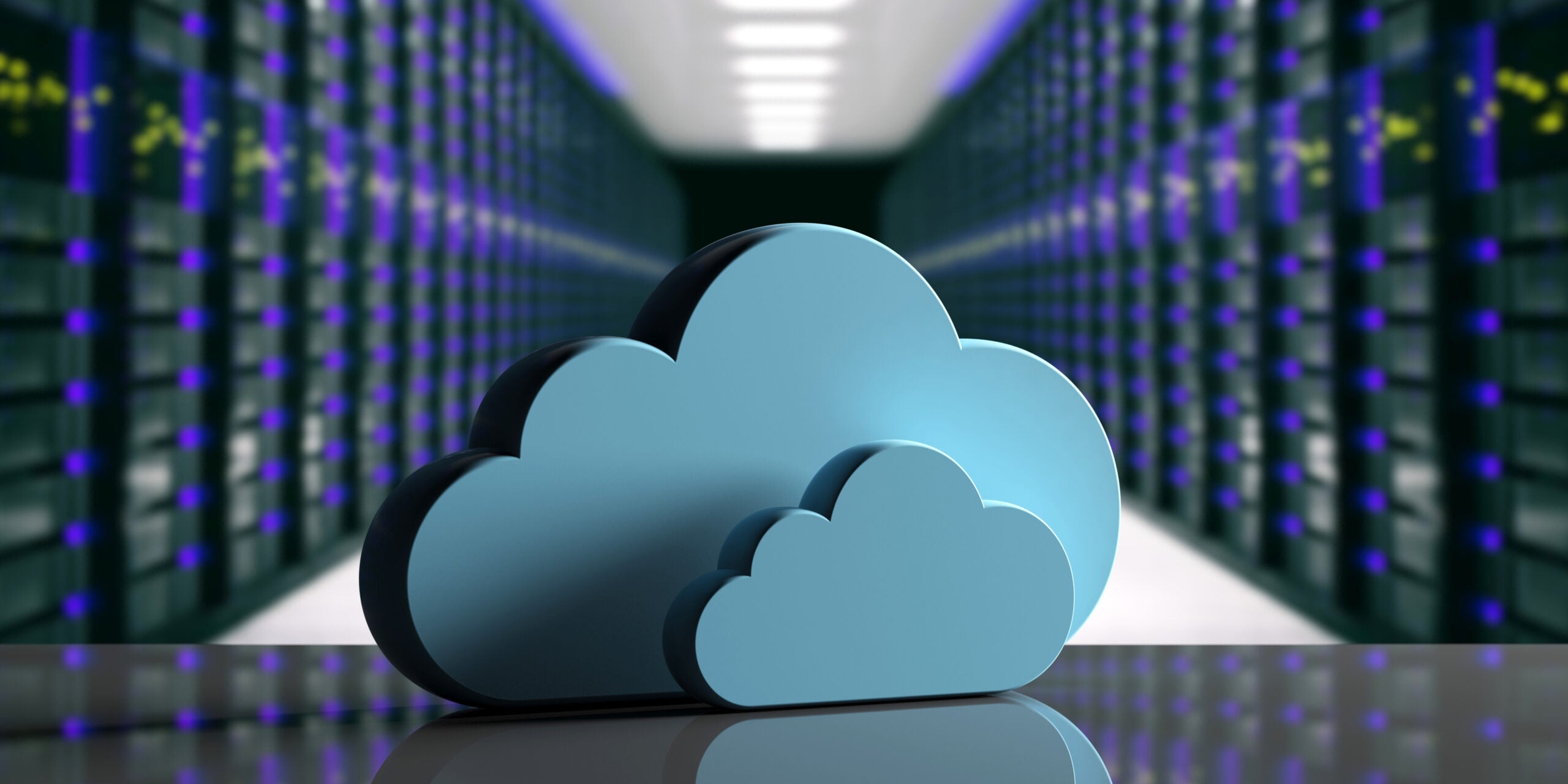
Introducing Ansys Electronics Desktop on Ansys Cloud
The Watch & Learn video article provides an overview of cloud computing from Electronics Desktop and details the product licenses and subscriptions to ANSYS Cloud Service that are...
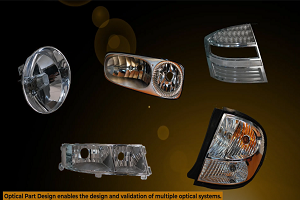
How to Create a Reflector for a Center High-Mounted Stop Lamp (CHMSL)
This video article demonstrates how to create a reflector for a center high-mounted stop lamp. Optical Part design in Ansys SPEOS enables the design and validation of multiple...
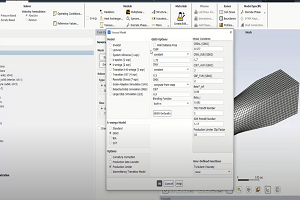
Introducing the GEKO Turbulence Model in Ansys Fluent
The GEKO (GEneralized K-Omega) turbulence model offers a flexible, robust, general-purpose approach to RANS turbulence modeling. Introducing 2 videos: Part 1 provides background information on the model and a...
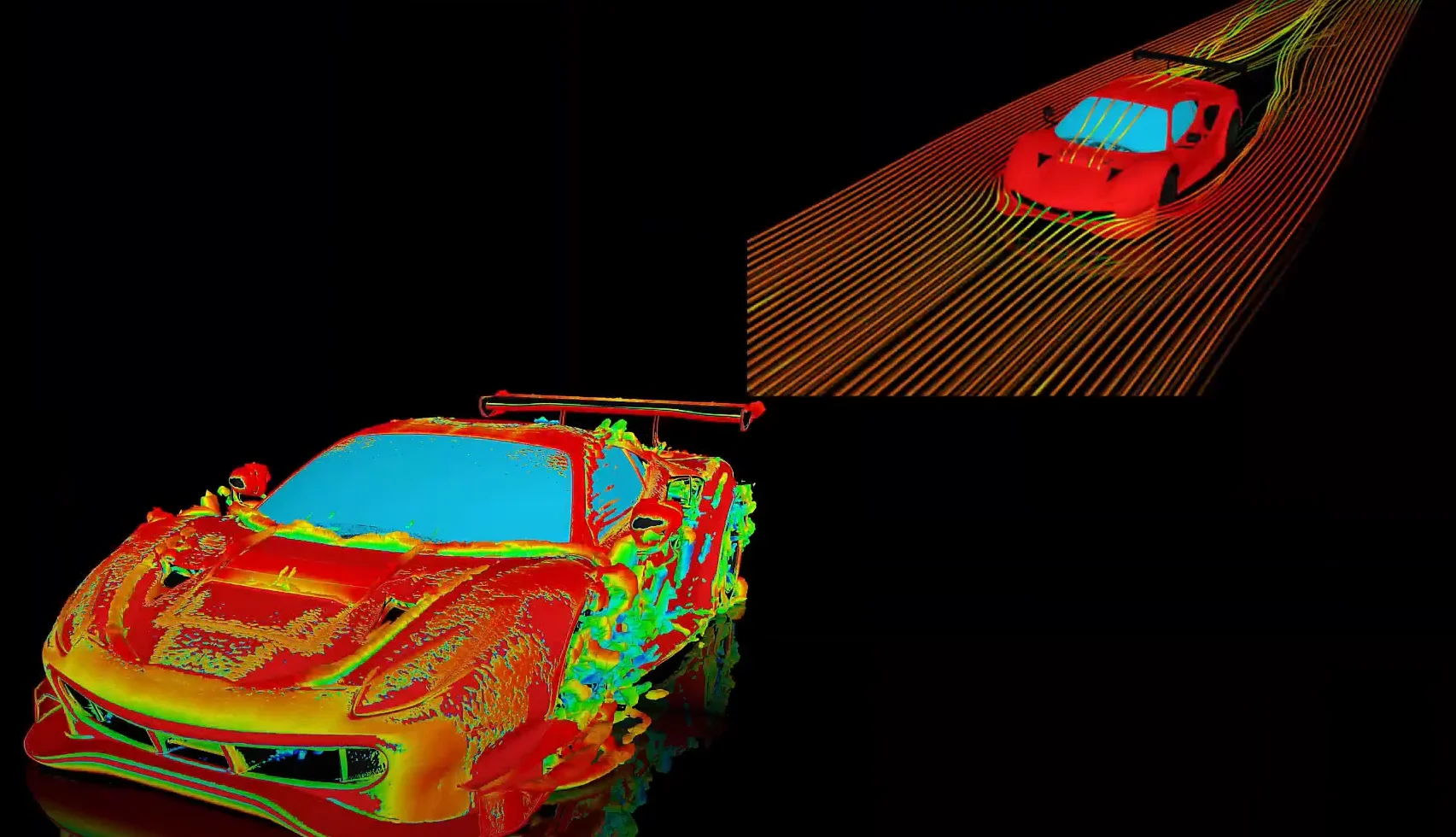
Postprocessing on Ansys EnSight
This video demonstrates exporting data from Fluent in EnSight Case Gold format, and it reviews the basic postprocessing capabilities of EnSight.
- How to overcome the model information incompatible with incoming mesh error?
- What are the requirements for an axisymmetric analysis?
- Skewness in ANSYS Meshing
- How to create and execute a FLUENT journal file?
- Is there a way to get the volume of a register using expression ?
- What is a .wbpz file and how can I use it?
- What are pressure-based solver vs. density-based solver in FLUENT?
- How can I Export and import boxes / Systems from one Workbench Project to another?
- Ansys Fluent GPU Solver FAQs
- How to get information about mesh cell count and cell types in Fluent?
© 2025 Copyright ANSYS, Inc. All rights reserved.