For strain rate dependent materials, I am using Johnson Cook Strength model. What would be the failure models I should use?
-
-
January 25, 2023 at 7:34 am
FAQ
ParticipantThe failure model that is simple and easy to use is plastic strain failure model. Material will fail when the effective plastic strain reaches its maximum. The other failure model is Johnson-Cook failure model. In Explicit Material library in Engineering Data, we have the material property data of both Johnson-Cook strength and Johnson-Cook failure models for the typical materials such as Copper (CU-OFHC), Steel (Steel 4340), and Iron (Iron-ARMCO). The reference paper of the Johnson-Cook failure model can be found from the material reference section: “Fracture Characteristics of Three Metals subjected to various strains, strain rates, temperatures and pressures” – Johnson GR, Cook WH, J Eng Mech Vol 21, 1985 Basically, authors have done torsion and Hopkins bar impact tests to find these material property values. The Johnson-Cook failure model contains 3 terms with 5 constants. The first term is the effect of the ratio of pressure/von Mises stress, which can be associated with the stress triaxiality. The second term is the effect of the strain rate. The third term is thermal softening. If you are not concerned with thermal softening, you can ignore the 3rd term and only need to find 4 constants. If you are only concerned with the strain rate dependence, you only need to define 1 constant D4 by curve-fitting the failure strain with the non-dimensional strain rate. If you are also concerned with the increase of material failure with increasing ratio of pressure/stress, you need to curve-fit the experimental data to get the constants D1, D2, and D3. D1, D2, and D3 may not necessarily have the same sign. One or two of them could be negative numbers because the increase of the pressure/stress ratio decreases the material failure strain.
-
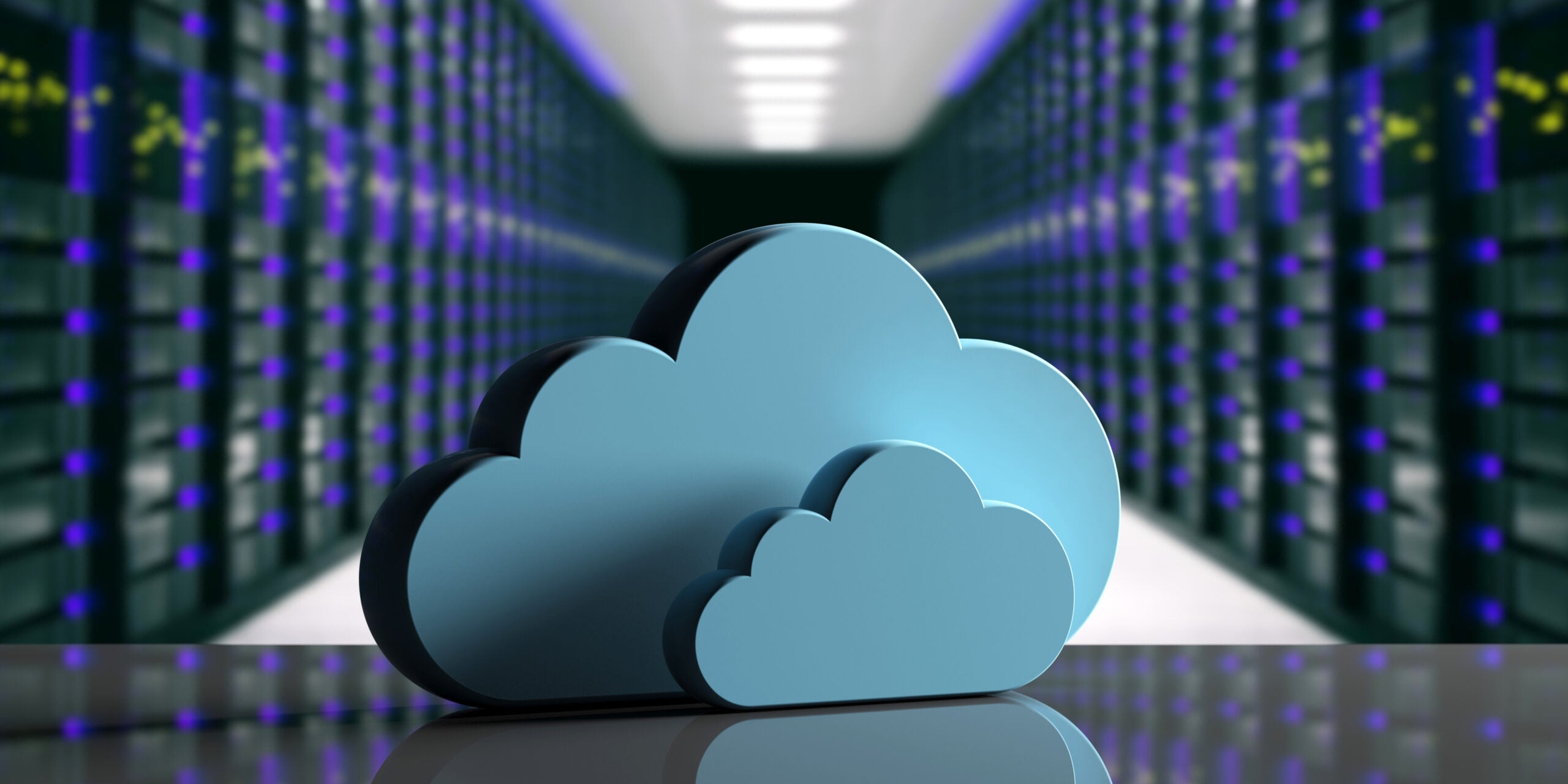
Introducing Ansys Electronics Desktop on Ansys Cloud
The Watch & Learn video article provides an overview of cloud computing from Electronics Desktop and details the product licenses and subscriptions to ANSYS Cloud Service that are...
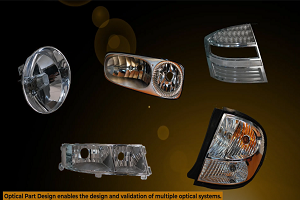
How to Create a Reflector for a Center High-Mounted Stop Lamp (CHMSL)
This video article demonstrates how to create a reflector for a center high-mounted stop lamp. Optical Part design in Ansys SPEOS enables the design and validation of multiple...
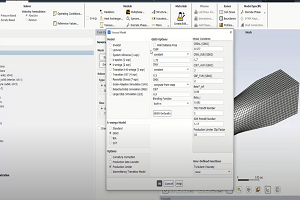
Introducing the GEKO Turbulence Model in Ansys Fluent
The GEKO (GEneralized K-Omega) turbulence model offers a flexible, robust, general-purpose approach to RANS turbulence modeling. Introducing 2 videos: Part 1 provides background information on the model and a...
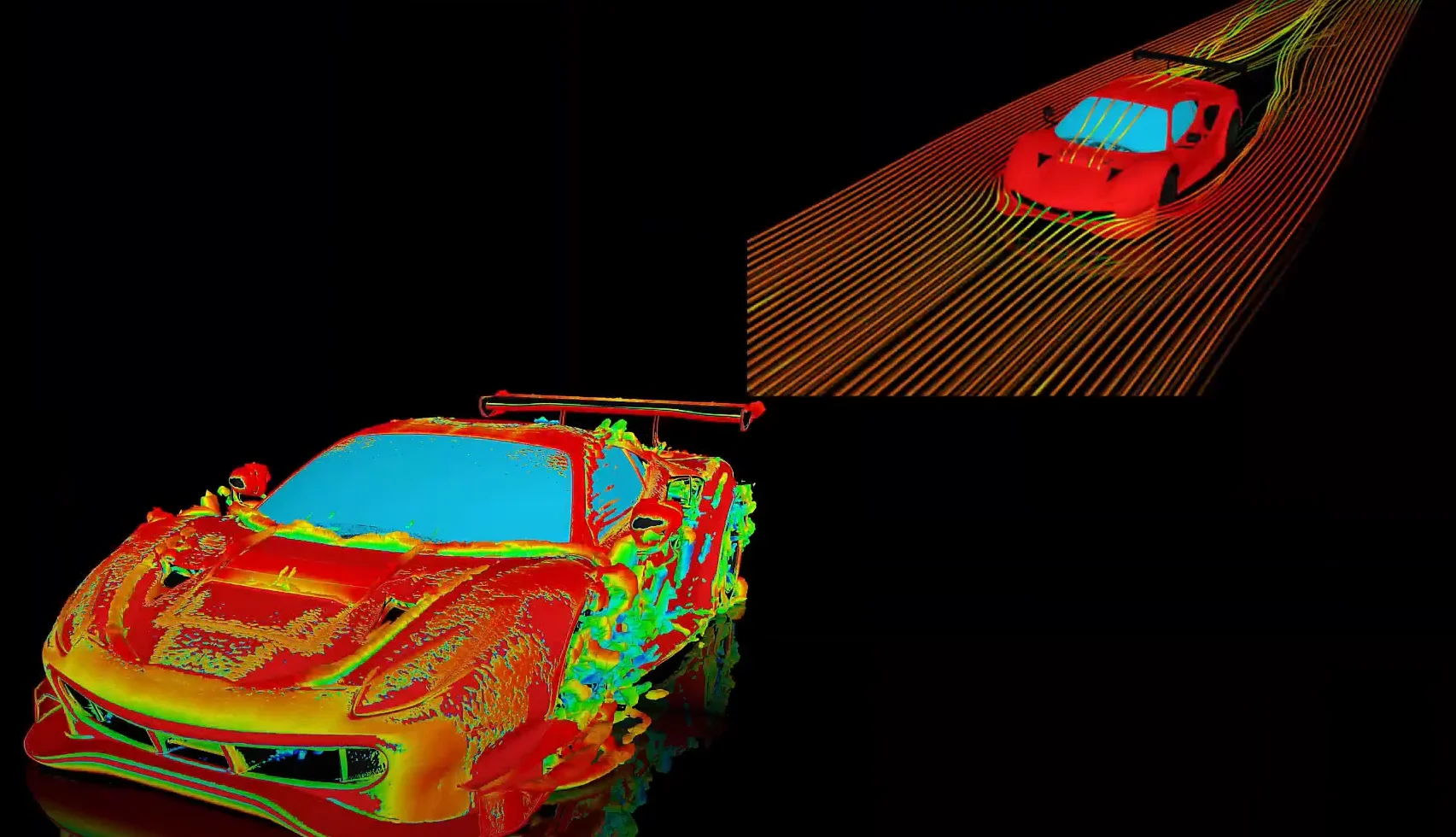
Postprocessing on Ansys EnSight
This video demonstrates exporting data from Fluent in EnSight Case Gold format, and it reviews the basic postprocessing capabilities of EnSight.
- How do I request ANSYS Mechanical to use more number of cores for solution?
- How to restore the corrupted project in ANSYS Workbench?
- How to deal with “”Problem terminated — energy error too large””?”
- Contact Definitions in ANSYS Workbench Mechanical
- There is a unit systems mismatch between the environments involved in the solution.
- How can I change the background color, font size settings of the avi animation exported from Mechanical? How can I improve the resolution of the video?
- How to transfer a material model(s) from one Analysis system to another within Workbench?
- How to obtain force reaction in a section ?
- How to change color for each body in Mechanical?
- How to resolve “Error: Invalid Geometry”?
© 2025 Copyright ANSYS, Inc. All rights reserved.