For Compressible simulations conducted with the high speed model, CFX gives an error message that suggests setting the expert parameter “highspeed wf mach threshold to 0.1. What does this parameter do ? What is its default value? The error is below: Parallel run: Received message from slave —————————————– Slave partition : 6 Slave routine : get_TWFTFC Master location : End of Continuity Loop Message label : 009100015 Message follows below – : +——————————————————————–+ | ****** Notice ****** | | The non-dimensional near wall temperature (T+) has been clipped | | for calculation of Wall Heat Transfer Coefficient. | | | | Boundary Condition : Default Domain Modified Default | | T+ clip value = 1.0000E-10 | | | | If this situation persists and you are using the High Speed Model, | | consider enabling Mach number based blending between low speed and | | high speed wall functions. You can do so by specifying a Mach | | number threshold as follows: | | | | EXPERT PARAMETERS: | | highspeed wf mach threshold = 0.1 # default=0.0 (off) | | END | +——————————————————————–+
Tagged: 15, cfx, compressible, compressible-flow, fluid-dynamics, General, Modeling/Setup Advice
-
-
January 25, 2023 at 7:16 am
FAQ
ParticipantWhen the high speed model is activated in CFX, the turbulent wall functions are calculated differently. This change affects the profile that is assumed for the non-dimensional near wall temperature (T+). CFX wall functions are designed for extremely high speed flows (Ma>3), so the near wall temperatures that are calculated may need to be blended with low speed values in instances where the flow speeds are considerably lower than Ma = 3 The warning indicates that the flow is in this regime. Sometimes, the high speed model is inappropriately set and should be deactivated. In other cases, the T+ error messages occur because the flow is still developing and will eventually disappear. The default setting for the recommended parameter, “highspeed wf mach threshold” is 0. At this value, the parameter instructs CFX to use high speed wall functions whenever the High Speed Model is active. Increasing the value of this parameter results in the use of a blended wall function. The near wall temperature calculation and the effects of flow velocity Can be found in the CFX Help Documentation at: // Theory Guide // 2. Turbulence and Wall Function Theory // 2.8. Modeling Flow Near the Wall // 2.8.1. Mathematical Formulation // 2.8.1.1. Scalable Wall Functions. There are no references to the expert parameter, but the underlying theory behind the high speed wall functions is described.
-
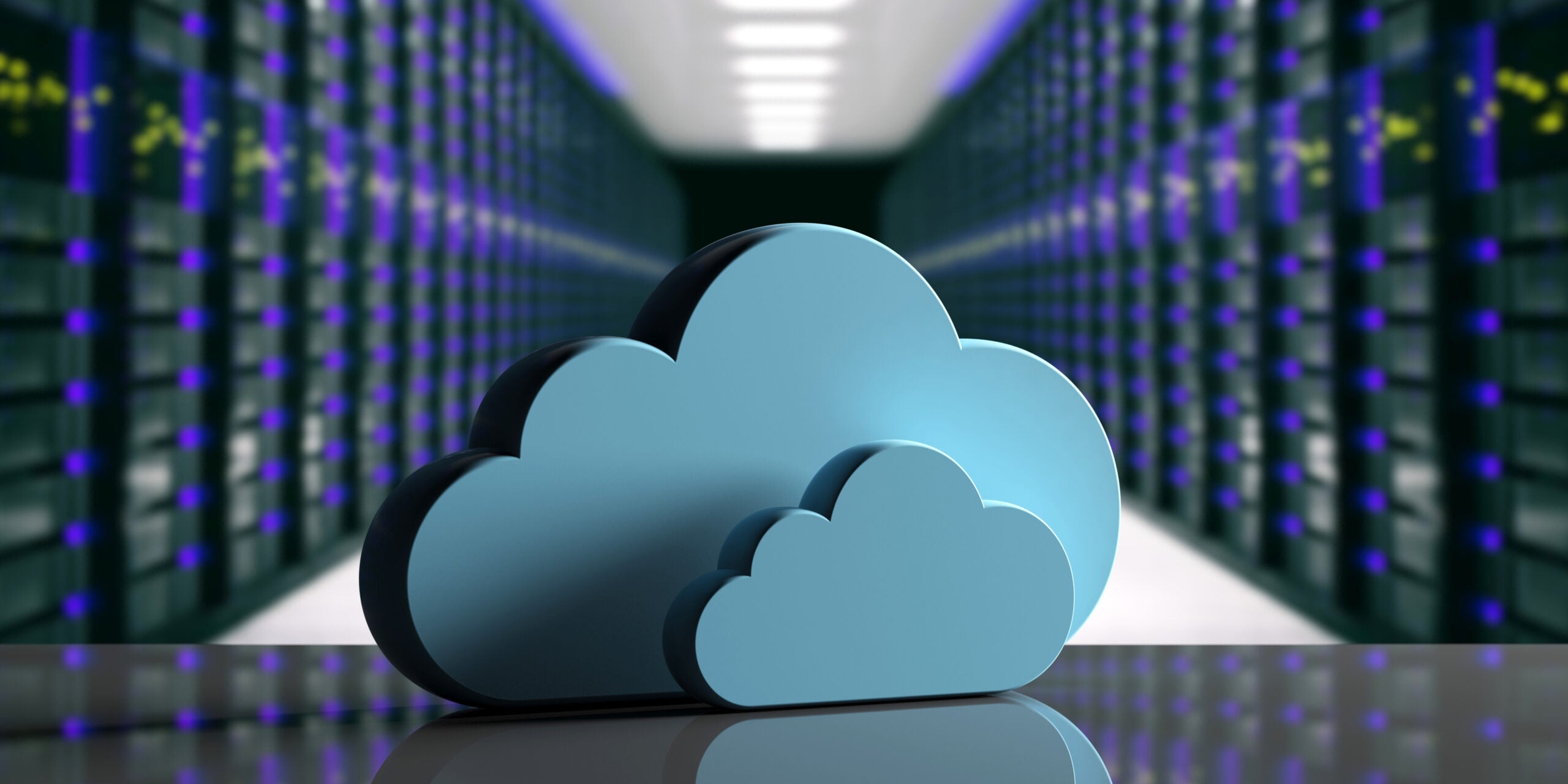
Introducing Ansys Electronics Desktop on Ansys Cloud
The Watch & Learn video article provides an overview of cloud computing from Electronics Desktop and details the product licenses and subscriptions to ANSYS Cloud Service that are...
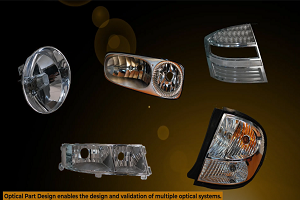
How to Create a Reflector for a Center High-Mounted Stop Lamp (CHMSL)
This video article demonstrates how to create a reflector for a center high-mounted stop lamp. Optical Part design in Ansys SPEOS enables the design and validation of multiple...
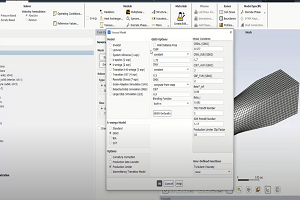
Introducing the GEKO Turbulence Model in Ansys Fluent
The GEKO (GEneralized K-Omega) turbulence model offers a flexible, robust, general-purpose approach to RANS turbulence modeling. Introducing 2 videos: Part 1 provides background information on the model and a...
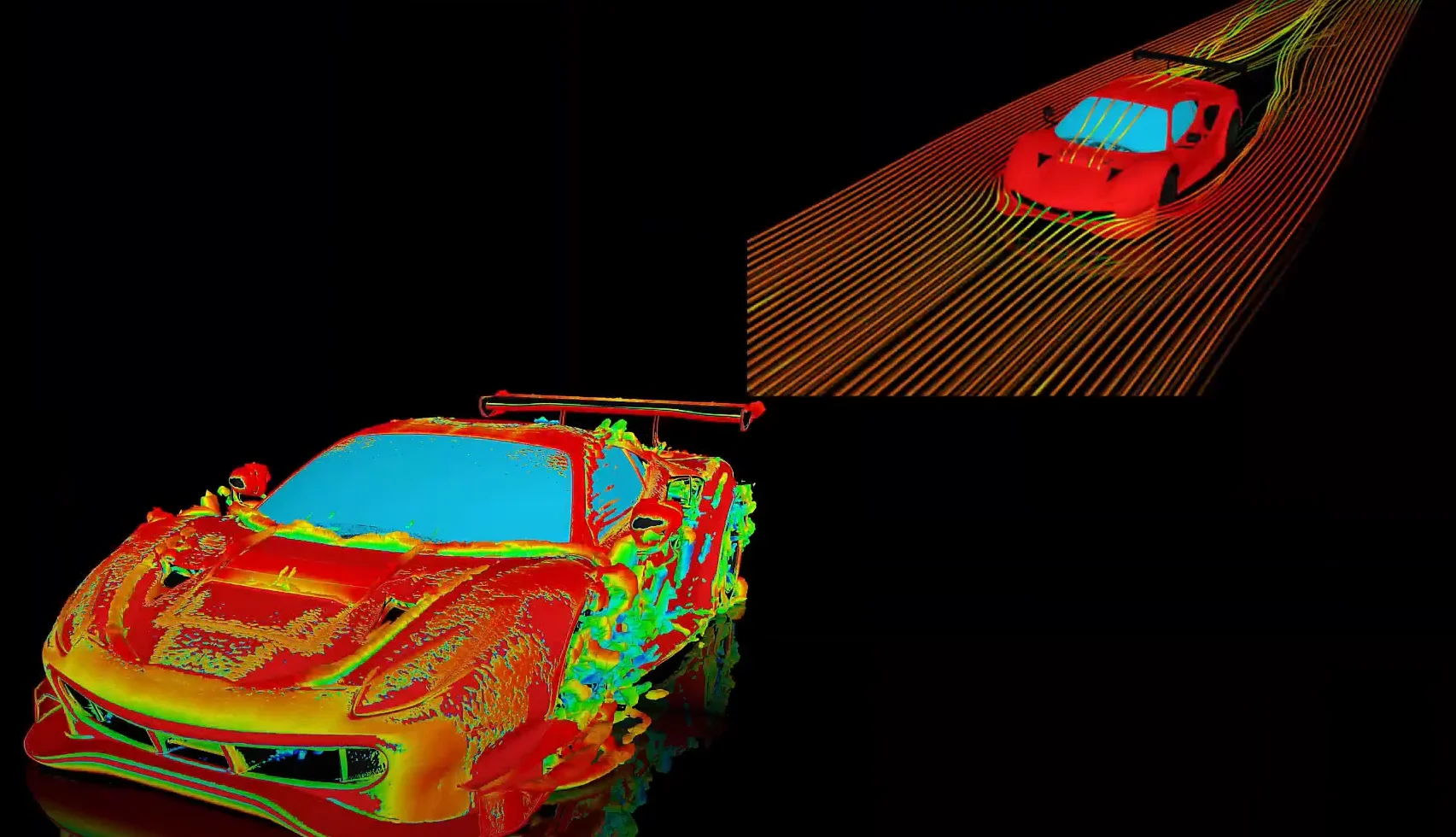
Postprocessing on Ansys EnSight
This video demonstrates exporting data from Fluent in EnSight Case Gold format, and it reviews the basic postprocessing capabilities of EnSight.
- How to overcome the model information incompatible with incoming mesh error?
- Skewness in ANSYS Meshing
- Is there a way to get the volume of a register using expression ?
- What are the requirements for an axisymmetric analysis?
- Ansys Fluent GPU Solver FAQs
- How to create and execute a FLUENT journal file?
- What are pressure-based solver vs. density-based solver in FLUENT?
- What is a .wbpz file and how can I use it?
- How to get information about mesh cell count and cell types in Fluent?
- How can I Export and import boxes / Systems from one Workbench Project to another?
© 2025 Copyright ANSYS, Inc. All rights reserved.