Tagged: aim tutorial, discovery-aim, structures
-
-
September 26, 2022 at 10:00 am
Watch & Learn
ParticipantThis example is taken from Cornell University’s ANSYS AIM Learning Modules
Problem Description
This problem is taken from: Prantil, V. C., Papadopoulos, C. and Gessler, P. D., Lying by Approximation: The Truth About Finite Element Analysis, Morgan and Claypool (2013). Consider a stepped shaft under an applied axial load, P. A stress concentration is apparent at the step where the cross-sectional area is discontinuous. The cross section is circular.
So the problem becomes amenable, let’s consider a relatively small fillet placed at the step to reduce the stress concentration to a finite value.
The pressure load on the smaller cross-section is 1000 psi. Calculate the axial stress concentration factor and compare it to the formula provided in Roark’s Formulas for Stress and Strain, Warren C. Young and Richard G. Budynas, 2002.
Learning Goals
The purpose of this tutorial is to showcase the simplest stress concentration and demonstrate that it can be resolved in 2 or 3 dimensions. Simple one-dimensional elements (i.e. simple axial bar elements) that capture constant stress within an element are insufficient to capture stress concentrations, even when many elements are used. That is to say, when the necessary physics is not contained in the element formulation, so-called h-convergence or using more elements captures “no more” of the solution than does a coars(er) discretization. This tutorial is meant to highlight where it is relatively straightforward to apply FEA and resolve a solution correctly that belies analytical treatment with uniaxial formulae (such as axial_stress = P/A).
Pre-Analysis
It is recommended that you make some back-of-the-envelope estimates of expected results before launching into your computer solution. Here:
for which the following formula for the axial stress concentration factor, K, holds (Roark’s Formulas for Stress and Strain, Warren C. Young and Richard G. Budynas, 2002):
We’ll compare the above axial stress concentration factor to the value obtained from Discovery AIM.
Geometry Creation
This problem could be simulated in either 2D or 3D by employing the proper geometric assumptions and boundary conditions. Since Discovery AIM provides a 3D capability, there are several simplifications that must be made to the geometry. When the shape is drawn, we want to create a quarter symmetric model of the geometry so that proper supports can be added to the model that do not over constrain the model. By creating these one dimensional supports, we allow the body to be subjected to the forces of the problem while preventing any rigid body translation and/or rotation of the body in space.
The following video shows how to create the quarter symmetric model of stepped shaft.
Mesh
In this video, you will learn how to generate hexahedral mesh for the geometry
Physics Setup
This video shows how to specify fixed support, symmetry constraints and pressure load on the model.
Results Evaluation
In this video, you will see how to evaluate Equivalent Stress and Displacement Magnitude.
Verification
In the pre-analysis, the maximum stress was calculated. To verify that our simulation was accurate, a comparison must be made. In order to view the maximum stress of the simulation, Stress YY was evaluated which can be seen in the previous step.
The table below compares the calculated and simulated values for maximum stress in the stepped shaft. There is a less than 5% difference between the finite element calculation and the simulation result.
Calculated Value Simulated Value Percent Difference 1376 psi 1310.6 psi 4.75%
-
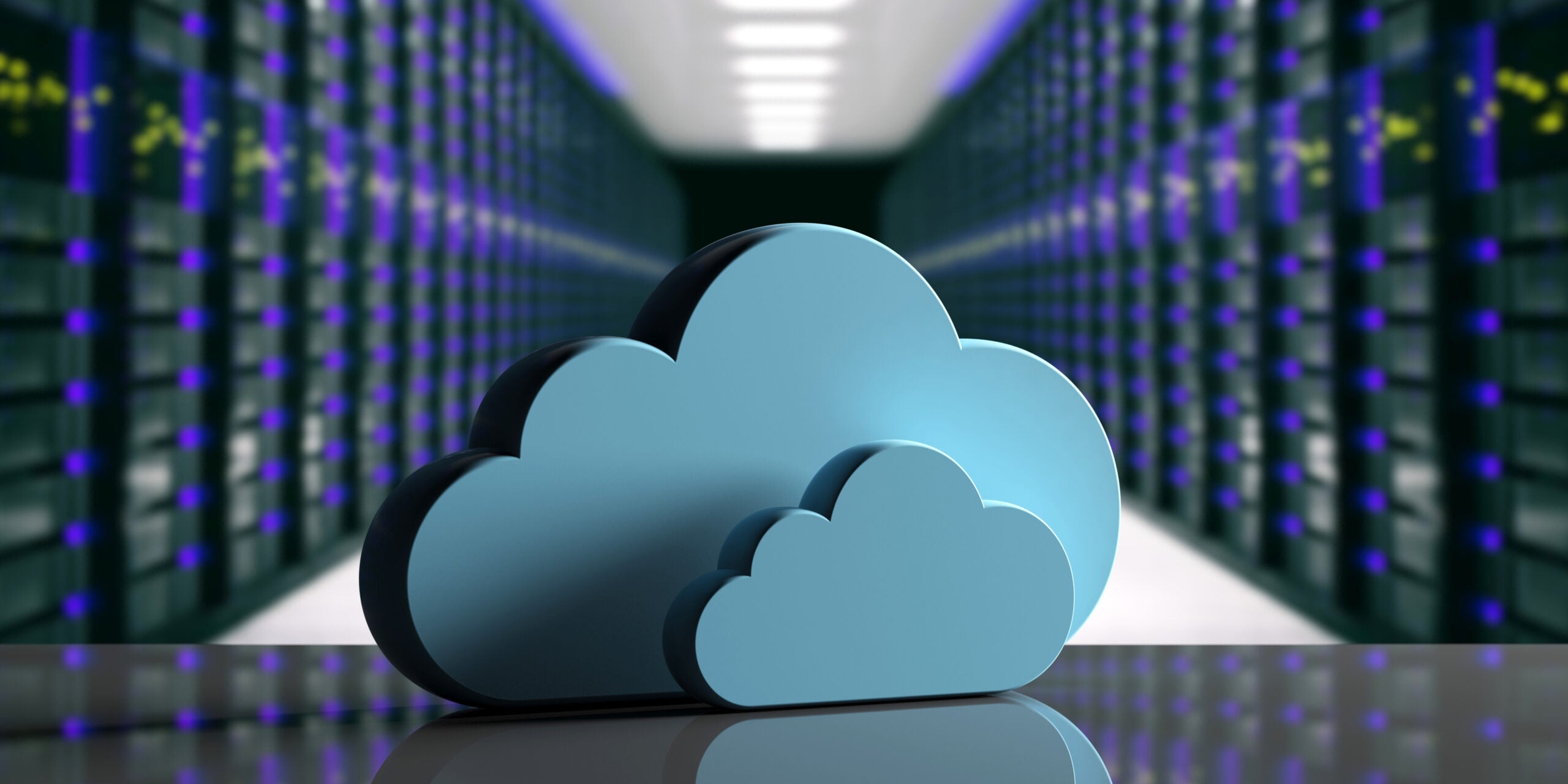
Introducing Ansys Electronics Desktop on Ansys Cloud
The Watch & Learn video article provides an overview of cloud computing from Electronics Desktop and details the product licenses and subscriptions to ANSYS Cloud Service that are...
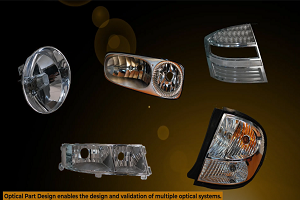
How to Create a Reflector for a Center High-Mounted Stop Lamp (CHMSL)
This video article demonstrates how to create a reflector for a center high-mounted stop lamp. Optical Part design in Ansys SPEOS enables the design and validation of multiple...
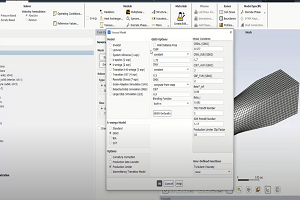
Introducing the GEKO Turbulence Model in Ansys Fluent
The GEKO (GEneralized K-Omega) turbulence model offers a flexible, robust, general-purpose approach to RANS turbulence modeling. Introducing 2 videos: Part 1 provides background information on the model and a...
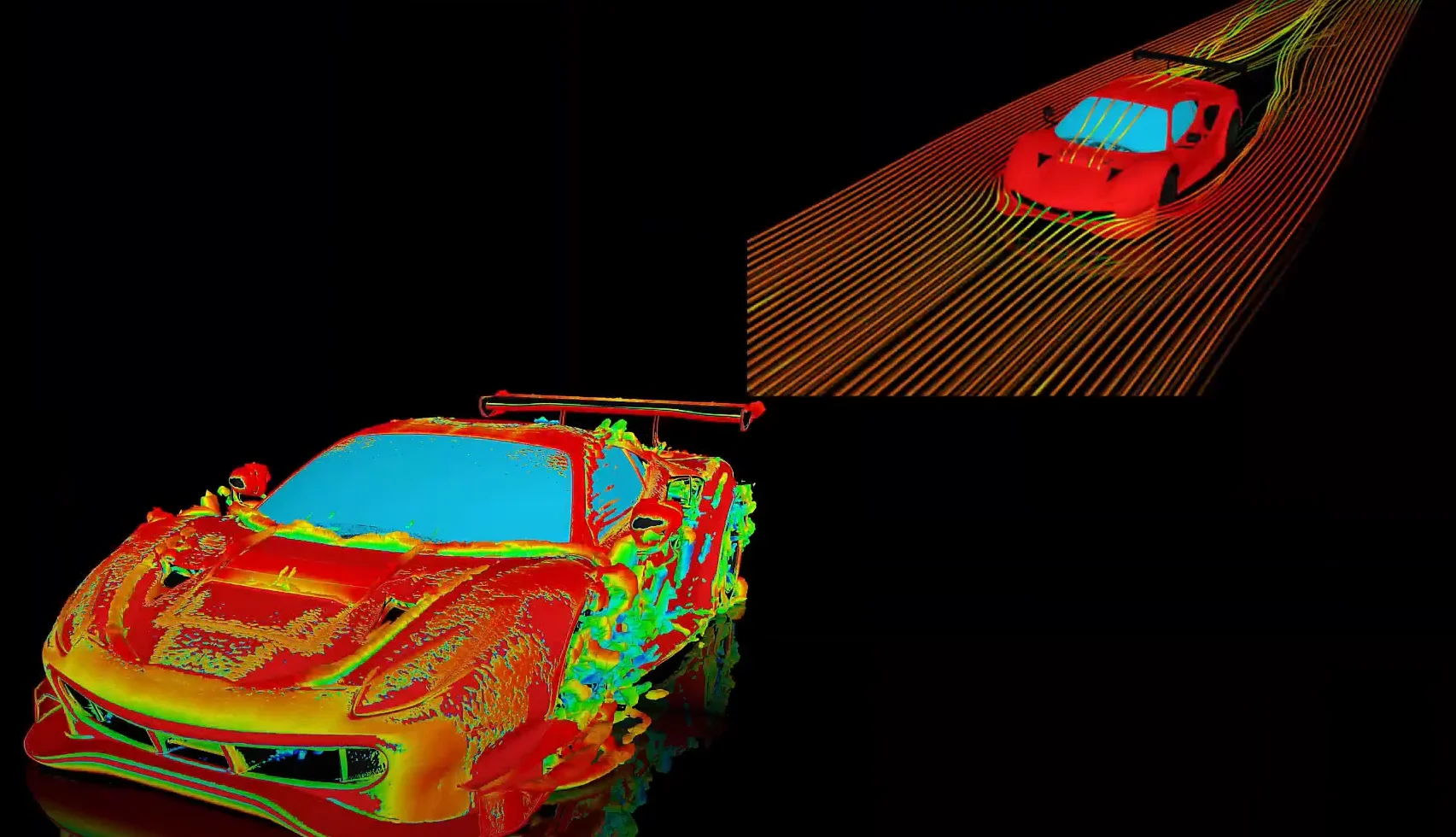
Postprocessing on Ansys EnSight
This video demonstrates exporting data from Fluent in EnSight Case Gold format, and it reviews the basic postprocessing capabilities of EnSight.
- Discovery Live: How to change units
- Discovery AIM tutorial – Analysis of cantilever beam with I cross-section
- Discovery AIM – Scaling deformation contour results
- Discovery AIM tutorial – 3D Finite-Element Analysis of a Bike Crank
- Discovery AIM tutorial – Structural Analysis of Plate with Hole
- FAQ: Missing Areas of the User Interface in Discovery Live
- Discovery SpaceClaim: Getting Started Tutorials
- How to setup a Parameter Study
- Creating a Helical Geometry in SpaceClaim
- Convert 2D Drawings to 3D Models in Minutes with SpaceClaim
© 2025 Copyright ANSYS, Inc. All rights reserved.