Tagged: aim tutorial, discovery-aim, structures
-
-
September 26, 2022 at 10:00 am
Solution
ParticipantThis example is taken from Cornell University’s ANSYS AIM Learning Modules
Learning Goals
The purpose of this tutorial is to showcase, in a relatively simple situation, where simple beam theory is no longer as valid as it is in the limit of a long and slender beam geometry. In some commercial codes, simple one-dimensional cubic beam elements for bending deflection, do not capture shear deflection when the beam is no longer slender. Alternatively in ANSYS, if shear deflection is accounted for in the 1D element formulation, results for the beam’s tip deflection will not agree with tip deflections predicted by simple Euler-Bernoulli beam theory. Again, attempts to capture this effect by using more elements will ultimately fail. Either the necessary physics is not contained in the element formulation or it is and the results are compared to simpler theory. Either way, using more elements captures “no more” of the solution than does a coarser discretization.
This tutorial is meant to highlight where it is relatively straightforward to apply 3D FEA and resolve a correct solution, which contradicts analytical treatment with simple formulae such as bending tip deflection =
Problem Specification
Consider a fixed-end, aluminum cantilever I-beam point-loaded at its tip as shown in the figure below. We will be solving for directional deformations and normal stresses in this tutorial.
P = 1000 lbf, L = 24 in, c = 4 in
The cross-sectional area and second moment of inertia are A = 9.45 in^2 and I = 112.3 in^4 respectively. These values correspond to the I-beam cross-section shown in the next figure along with a fully three-dimensional solid model of the beam for purposes of visualization. Use the following material properties for the aluminum beam:
Young’s Modulus = 1e7 psi, Poisson’s Ratio = 0.33
Pre-Analysis
You are told that experiments have been performed that confirm that the tip deflection under the load is approximately
Generally, in long, slender beams, the transverse displacement due to pure bending dominates when compared with the accompanying shear deflection. In relatively short beams, however, displacement contributions from shear can be large enough as to be non-negligible compared with those from pure bending. In the present case, the shear contribution is no longer a “small percentage” of that from bending:
where the relevant shear area is approximately the area of the beam web only. This is as prescribed in most Mechanics of Materials textbooks because any load applied to the flanges tend to deform the flanges locally and do not contribute to the deflection of the neutral axis. You can see this if you attempt to perform this analysis and distribute the end load over the entire cross sectional area including the flanges.
Assuming shear modulus (G) = 3770 ksi:
Bending deformation= 0.0041033 in
Shear deformation = 0.0030557 inHere the bending deformation alone varies enough from the total deformation to question whether the difference might be a discretization error when , in fact, it is due to a difference in physical modeling assumptions. To perform a proper validation of any numerical results post-mortem, one must know what theory is embedded within the finite element model.
When the beam is long and slender, transverse displacement due to bending is the dominant contribution to the tip deflection and the pure bending stress component is the dominant normal stress component acting at the wall fixture:
What to Expect
Performing the three-dimensional analysis results in tip deflections in agreement with theory including the shear deformation but does not render normal stresses at the wall given by simple beam theory. Below are the hand calculations for comparison in the Verification and Validation section of the tutorial:
Geometry
Analysis-of-cantilever-beam-with-I-cross-section.zip
The video below shows the steps necessary to import the provided geometry into Discovery AIM.
Mesh
In this tutorial, we will be using Physics-Aware Meshing. Physics-aware meshing helps automate and simplify your problem setup. With physics-aware meshing, the computational mesh is generated automatically based on the solution fidelity setting and the physics inputs.
Physics Setup
In this video, you will learn how to:
- Assign material to the I-beam
- Assign support and force to the I-beam
Also, in this video you will notice that the load is applied to the central web. The reason behind this is to focus on the deflection that occurs across the entire span of the I-Beam. This tutorial isn’t concerned with the deflections that occur to the top and bottom flanges. The problem focuses on the increasing impact which shear deflection has on shorter, non-slender beams. This shear causes a difference between the analytical Euler-Bernoulli solution and the 3D finite element model.
Results Evaluation
In this video, you will learn how to view normal stress and displacement.
Verification and Validation
“Verification and validation” can be thought of as a formal process for checking results. Validation consists of assuring oneself that the solution is, in fact, correct. This consists of making sure the discretization error is minimized by performing a convergence study to assure oneself that the results are insensitive to the chosen mesh. This can be done by adding Size Controls on the Mesh Task.
Once this is accomplished, one needs to compare the converged results with experimental data or directly applicable theory. In this case, we have experimental results for the deflection and simple Euler-Bernoulli theory for comparison with the stress results. The deflection results are obtained within the uncertainty of the measured tip deflection:
Performing the three-dimensional analysis results in tip deflections in agreement with theory including the shear deformation but does not render normal stresses at the wall given by simple beam theory. Below are the hand calculations from (one-dimensional) Euler-Bernoulli beam theory and the predictions for the normal stress at the fixed wall obtained from a fully three-dimensional analysis that includes Poisson effects from the dimensions in the cross section. Recall, from calculation in the Pre-Analysis section, the normal stress at the wall due to bending deformation alone is 854.9 psi whereas that predicted by the FEA analysis is more than double at 1816 psi.
The Euler-Bernoulli theory predicts normal stresses in the absence of out=of=plane stresses (which are presumed negligibly small. Here the out-of-plane ZZ component of stress is predicted to be approximately 816 psi, i.e on the order of normal stresses due to bending alone. These substantial out-of-plane stresses result in Poisson effects on the normal wall stress, increasing its value substantially.
-
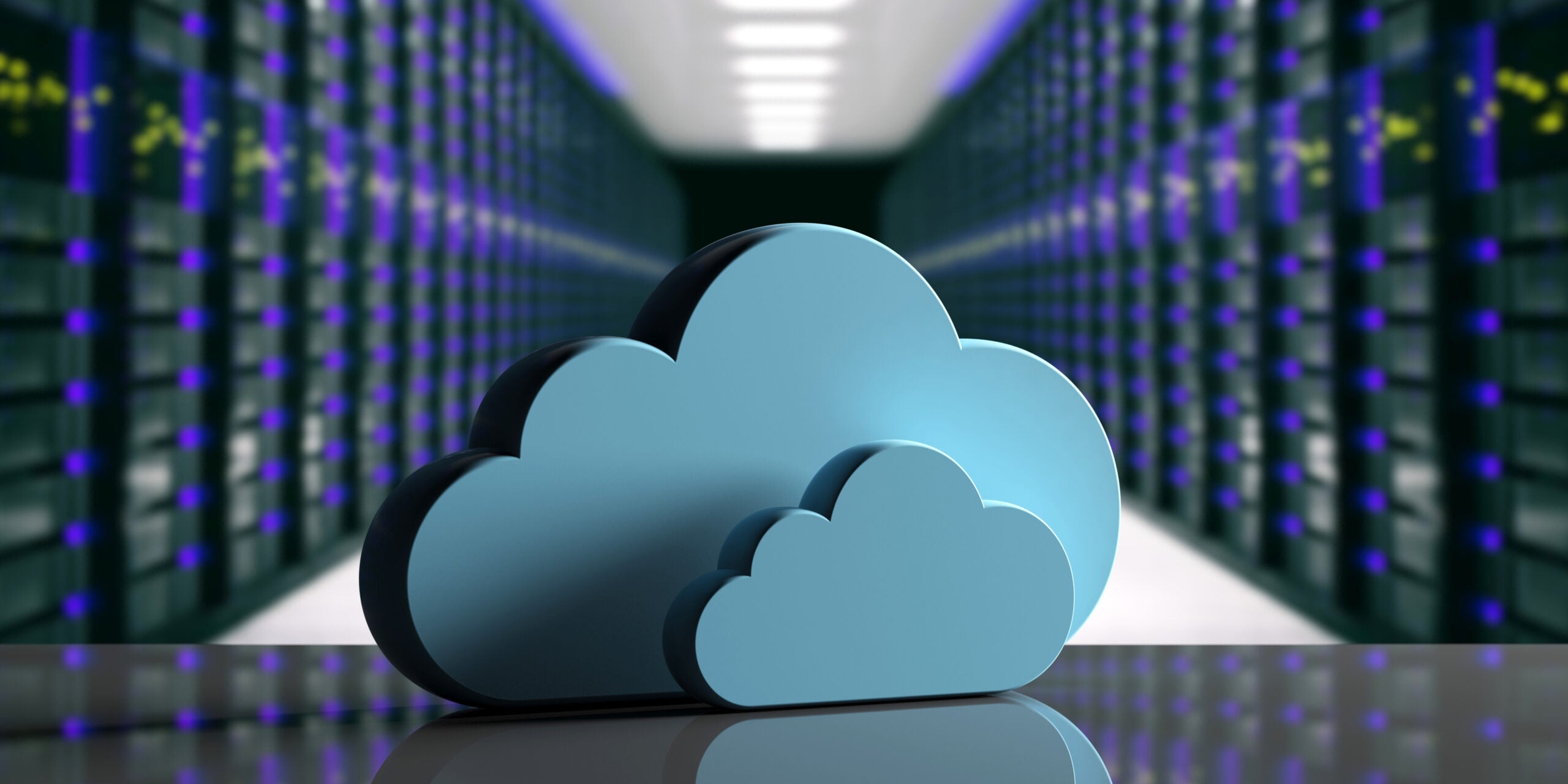
Introducing Ansys Electronics Desktop on Ansys Cloud
The Watch & Learn video article provides an overview of cloud computing from Electronics Desktop and details the product licenses and subscriptions to ANSYS Cloud Service that are...
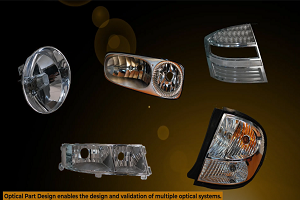
How to Create a Reflector for a Center High-Mounted Stop Lamp (CHMSL)
This video article demonstrates how to create a reflector for a center high-mounted stop lamp. Optical Part design in Ansys SPEOS enables the design and validation of multiple...
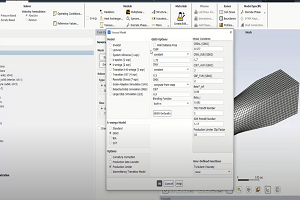
Introducing the GEKO Turbulence Model in Ansys Fluent
The GEKO (GEneralized K-Omega) turbulence model offers a flexible, robust, general-purpose approach to RANS turbulence modeling. Introducing 2 videos: Part 1 provides background information on the model and a...
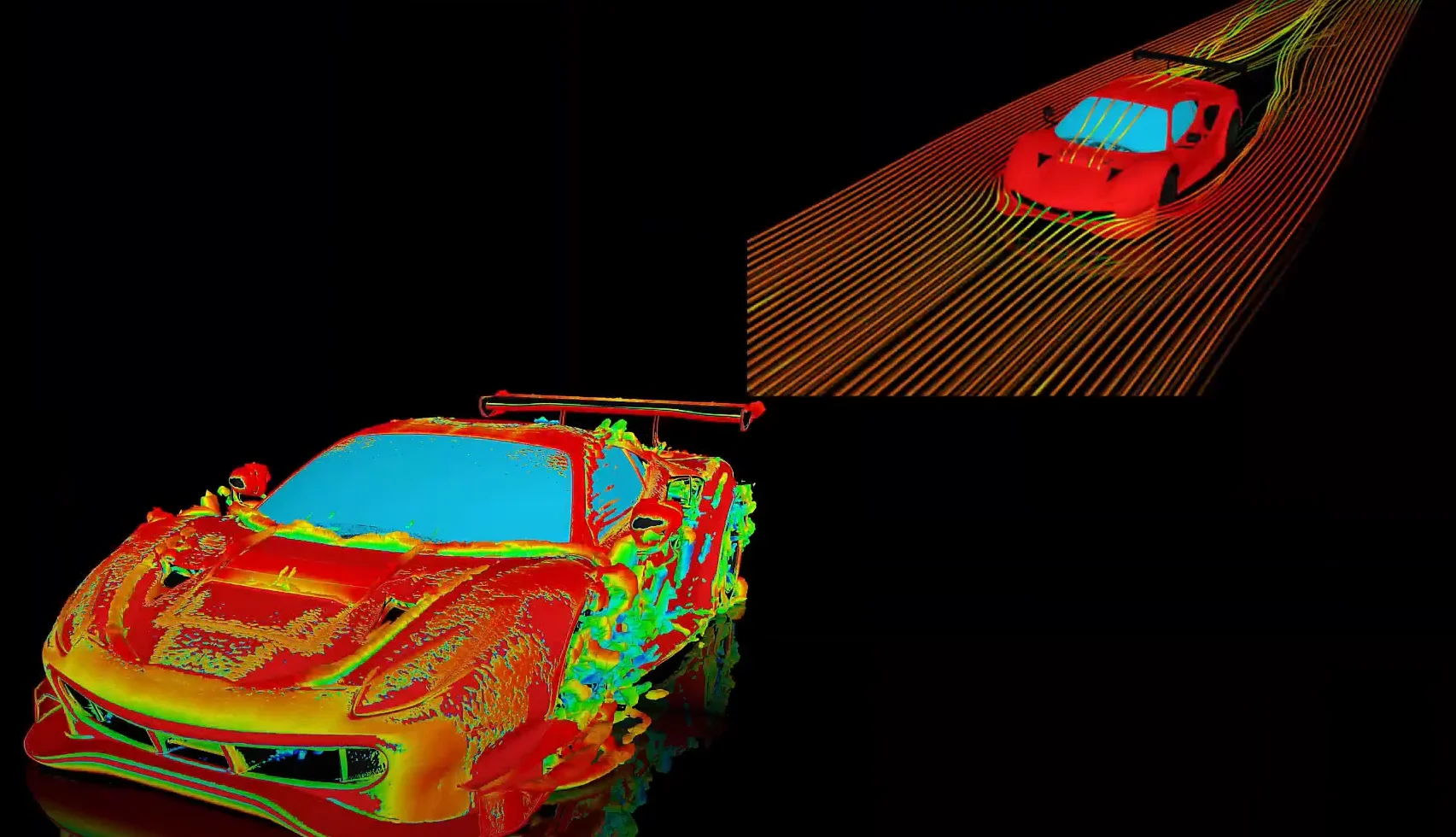
Postprocessing on Ansys EnSight
This video demonstrates exporting data from Fluent in EnSight Case Gold format, and it reviews the basic postprocessing capabilities of EnSight.
- Discovery Live: How to change units
- Discovery AIM tutorial – Analysis of cantilever beam with I cross-section
- Discovery AIM – Scaling deformation contour results
- Discovery AIM tutorial – 3D Finite-Element Analysis of a Bike Crank
- Discovery AIM tutorial – Structural Analysis of Plate with Hole
- FAQ: Missing Areas of the User Interface in Discovery Live
- How to setup a Parameter Study
- Discovery SpaceClaim: Getting Started Tutorials
- Creating a Helical Geometry in SpaceClaim
- Convert 2D Drawings to 3D Models in Minutes with SpaceClaim
© 2025 Copyright ANSYS, Inc. All rights reserved.