Tagged: ls-dyna, LS-DYNA Suite, lsdyna, R13.x, structural-mechanics
-
-
March 17, 2023 at 8:59 am
FAQ
ParticipantContact between beam elements can be modeled through CONTACT_AUTOMATIC_GENERAL. This accounts for the contact thickness (offset) due to the cross section of the beam elements. However, regardless of the actual shape of the cross section, the contact algorithm assumes that the beams have a cylindrical shape. The diameter assumed depends on the beam formulation. For ELFORM=2 and 3, the contact algorithm sets the diameter equal to the square root of the area specified in the *SECTION card. For ELFORM=1, 4, 5, and 9, the contact algorithm sets the diameter equal to the first cross-sectional dimension specified in the SECTION card or equal to D1 in the INTEGRATION_BEAM card. The contact thickness, i.e. assumed beam diameter in this case, can be adjusted through the parameters SST and SFST of the CONTACT card, as described in the LS-DYNA Manual Vol I. CONTACT_AUTOMATIC_GENERAL is a single-surface contact, which means it only has a slave side. Therefore, the parameters MST and SFMT have no effect. Furthermore, SFST is ignored if SST is nonzero except in the case of Mortar contact. Note that the diameter assumed for the contact thickness has no bearing on the actual cross-sectional properties specified for the beam element; it only affects the location of the contact surface. Alternatively, beam-to-beam contact can be modeled with an automatic Mortar contact. This is invoked by appending the suffix MORTAR to either AUTOMATIC_SURFACE_TO_SURFACE or AUTOMATIC_SINGLE_SURFACE and it is a segment-to-segment penalty-based contact. It assumes a faceted representation of the beam lateral surface. For a beam element the contact surface is represented by 14 faceted segments encapsulating a cylinder with the same length and volume as the beam element itself. This implies that all beam elements are assumed to have a circular cross section for the contact. The contact thickness can be adjusted with the aid of parameters SST and SFST, and also MST and SFMT if the surface-to-surface contact is used. The Mortar contact is the recommended contact type for implicit analysis, but it is also supported in explicit analysis.
-
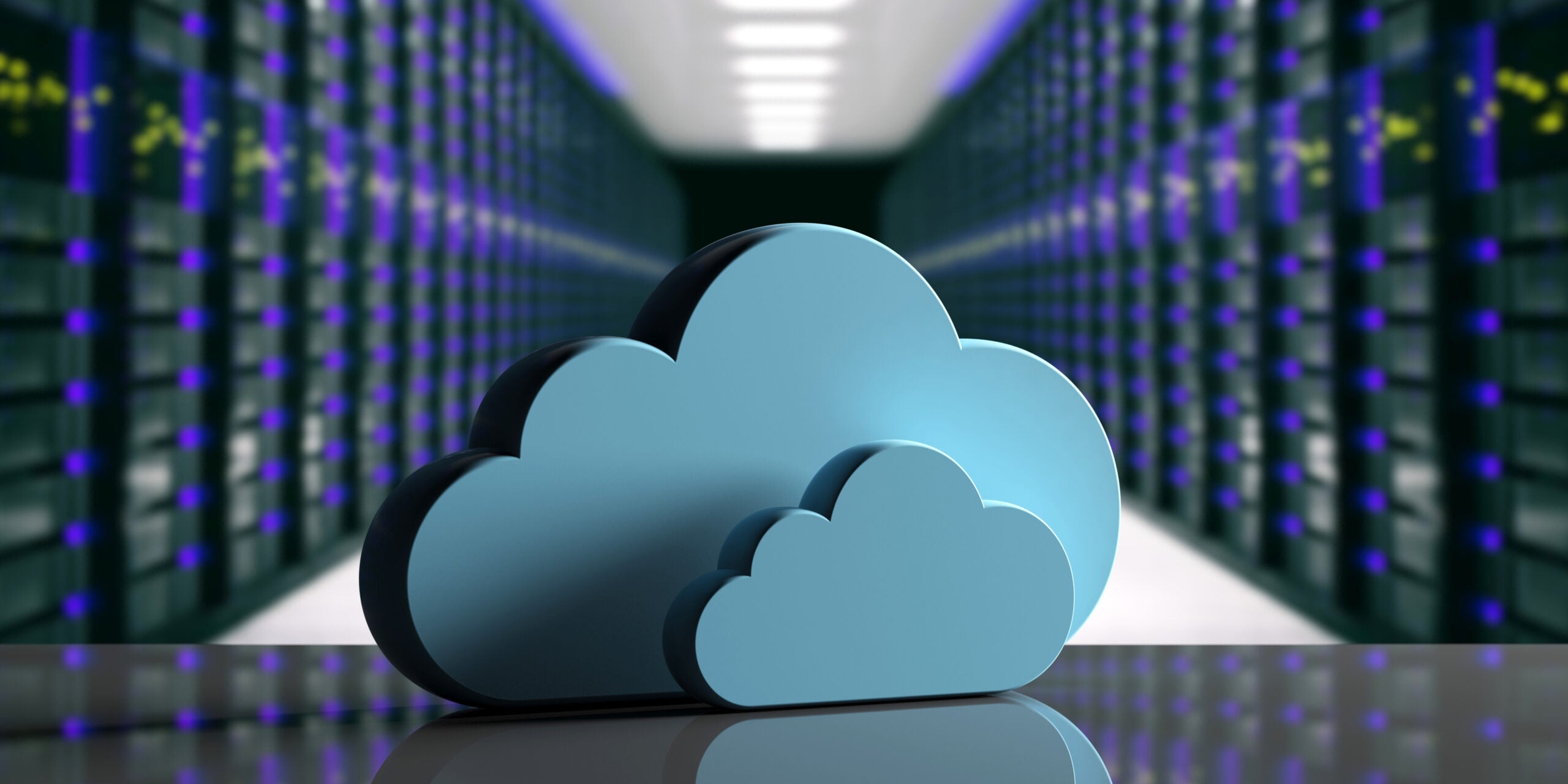
Introducing Ansys Electronics Desktop on Ansys Cloud
The Watch & Learn video article provides an overview of cloud computing from Electronics Desktop and details the product licenses and subscriptions to ANSYS Cloud Service that are...
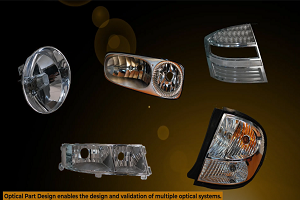
How to Create a Reflector for a Center High-Mounted Stop Lamp (CHMSL)
This video article demonstrates how to create a reflector for a center high-mounted stop lamp. Optical Part design in Ansys SPEOS enables the design and validation of multiple...
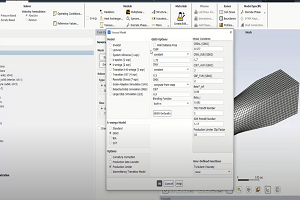
Introducing the GEKO Turbulence Model in Ansys Fluent
The GEKO (GEneralized K-Omega) turbulence model offers a flexible, robust, general-purpose approach to RANS turbulence modeling. Introducing 2 videos: Part 1 provides background information on the model and a...
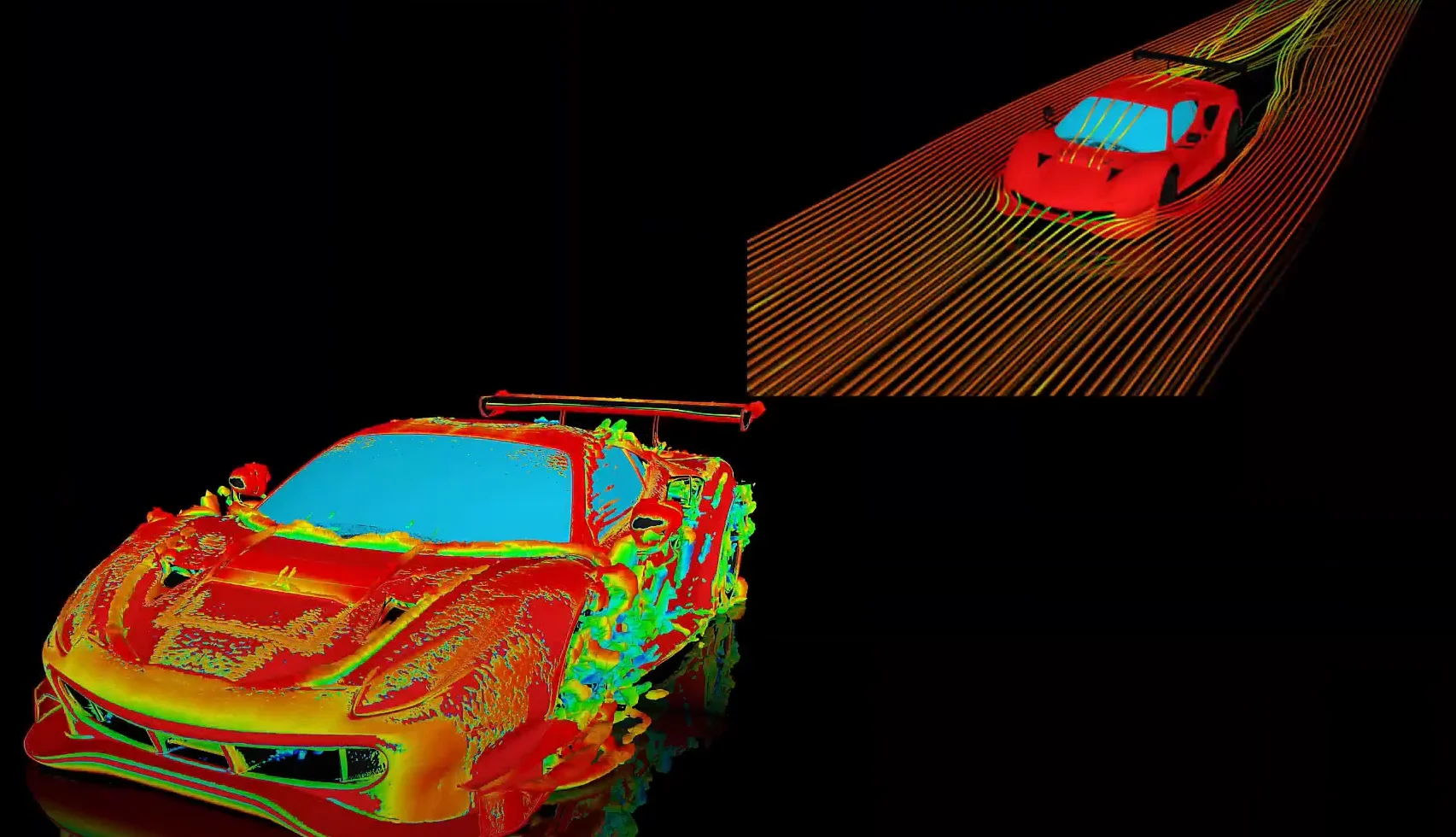
Postprocessing on Ansys EnSight
This video demonstrates exporting data from Fluent in EnSight Case Gold format, and it reviews the basic postprocessing capabilities of EnSight.
- How do I request ANSYS Mechanical to use more number of cores for solution?
- How to restore the corrupted project in ANSYS Workbench?
- How to deal with “”Problem terminated — energy error too large””?”
- Contact Definitions in ANSYS Workbench Mechanical
- How can I change the background color, font size settings of the avi animation exported from Mechanical? How can I improve the resolution of the video?
- There is a unit systems mismatch between the environments involved in the solution.
- How to transfer a material model(s) from one Analysis system to another within Workbench?
- What is the reason for this error message when mesher fails – “A software execution error occurred inside the mesher. The process suffered an unhandled exception or ran out of usable memory.”?
- How to obtain force reaction in a section ?
- How to change color for each body in Mechanical?
© 2025 Copyright ANSYS, Inc. All rights reserved.