-
-
January 25, 2023 at 7:34 am
FAQ
ParticipantIn materials that undergo extremely large deformations, such as soft foams, an element may become so distorted that the volume of the element is calculated as negative. This may occur without the material reaching a failure criterion. There is an inherent limit to how much deformation a Lagrangian mesh can accommodate without some sort of mesh smoothing or remeshing taking place. A negative volume calculation in LS-DYNA will cause the calculation to terminate unless ERODE in *CONTROL_TIMESTEP is set to 1 and DTMIN in *CONTROL_TERMINATION is set to any nonzero value in which case the offending element is deleted and the calculation continues (in most cases). Even with ERODE and DTMIN set as described, a negative volume may cause an error termination. Some approaches that can help to overcome negative volumes include the following: Simply stiffen up the material stress-strain curve at large strains. This approach can be quite effective. Sometimes tailoring the initial mesh to accomodate a particular deformation field will prevent formation of negative volumes. Again, negative volumes are generally only an issue for very severe deformation problems and typically occur only in soft materials like foam. Reduce the timestep scale factor. The default of 0.9 may not be sufficient to prevent numerical instabilities. Avoid fully-integrated solids (formulations 2 and 3) which tend to be less stable in situations involving large deformation or distortion. (The fully integrated element is less robust than a 1-point element when deformation is large because a negative Jacobian can occur at one of the integration points while the element as a whole maintains a positive volume. The calculation with fully integrated element will therefore terminate with a negative Jacobian much sooner than will a 1-point element.) Use the default element formulation (1 point solid) with type 4 or 5 hourglass control (will stiffen response).Preferred hourglass formulations for foams are Type 6 with hourglass coef = 0.1 if low velocity impact Type 2 or 3 with hourglass coef. = 0.1 if high velocity impact. The hourglass type and hourglass coefficient may warrant modification based on observed hourglass modes and on reported hourglass energy in matsum Model the foam with tetrahedral elements using solid element formulation 10 although this approach may give an overly stiff response. Increase the DAMP parameter (foam model 57) to the maximum recommended value of 0.5. Use optional card B of *CONTACT to turn shooting node logic off for contacts involving foam. Use *CONTACT_INTERIOR. A part set defines the parts to be treated by *CONTACT_INTERIOR. Attribute 4 (DA4 = 5th field of Card 1) of the part set defines the TYPE of *CONTACT_INTERIOR used. The default TYPE is 1 which is recommended for uniform compression. In version 970, solid formulation 1 elements can be assigned TYPE=2 which treats combined modes of shear and compression. If *MAT_126 is used, try ELFORM = 0. Try EFG formulation (*SECTION_SOLID_EFG). Use only where deformations are severe as this formulation is very expensive. Use only with hex elements.
-
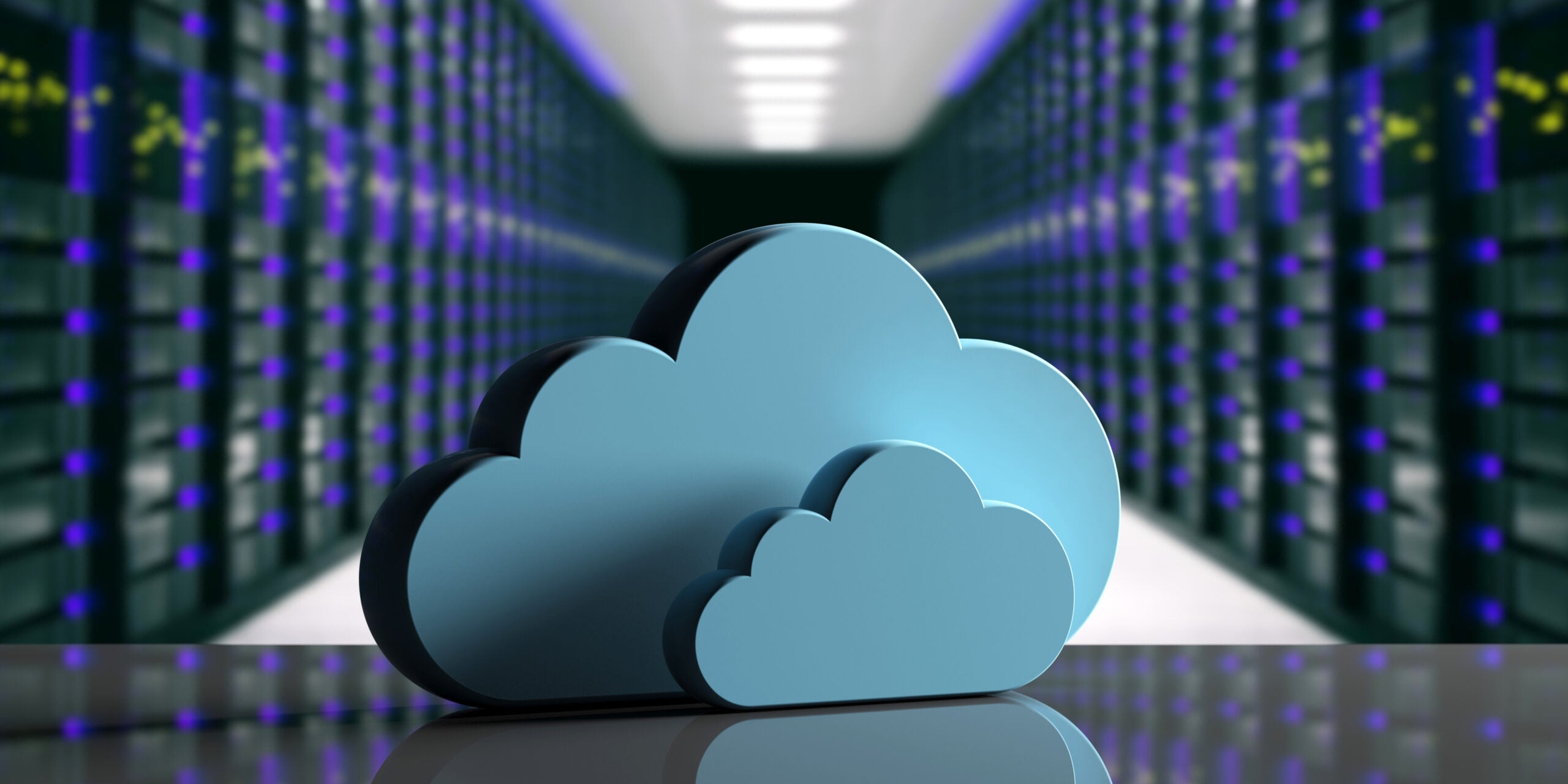
Introducing Ansys Electronics Desktop on Ansys Cloud
The Watch & Learn video article provides an overview of cloud computing from Electronics Desktop and details the product licenses and subscriptions to ANSYS Cloud Service that are...
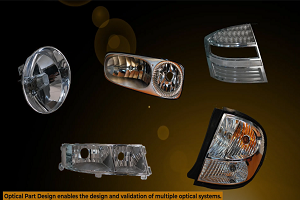
How to Create a Reflector for a Center High-Mounted Stop Lamp (CHMSL)
This video article demonstrates how to create a reflector for a center high-mounted stop lamp. Optical Part design in Ansys SPEOS enables the design and validation of multiple...
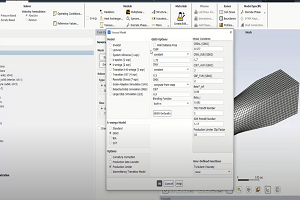
Introducing the GEKO Turbulence Model in Ansys Fluent
The GEKO (GEneralized K-Omega) turbulence model offers a flexible, robust, general-purpose approach to RANS turbulence modeling. Introducing 2 videos: Part 1 provides background information on the model and a...
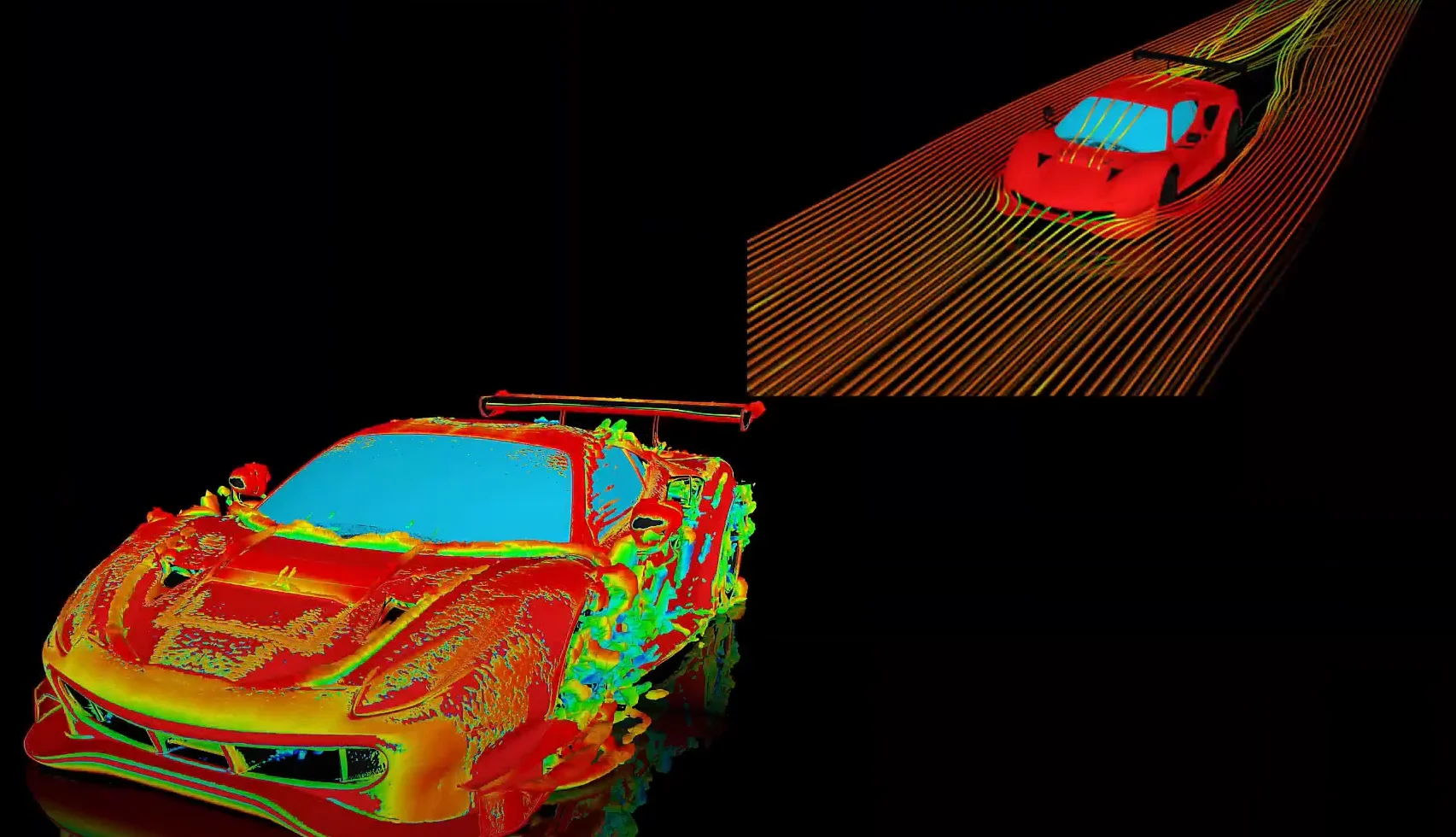
Postprocessing on Ansys EnSight
This video demonstrates exporting data from Fluent in EnSight Case Gold format, and it reviews the basic postprocessing capabilities of EnSight.
- How do I request ANSYS Mechanical to use more number of cores for solution?
- How to restore the corrupted project in ANSYS Workbench?
- How to deal with “”Problem terminated — energy error too large””?”
- Contact Definitions in ANSYS Workbench Mechanical
- How can I change the background color, font size settings of the avi animation exported from Mechanical? How can I improve the resolution of the video?
- There is a unit systems mismatch between the environments involved in the solution.
- How to transfer a material model(s) from one Analysis system to another within Workbench?
- How to obtain force reaction in a section ?
- What is the reason for this error message when mesher fails – “A software execution error occurred inside the mesher. The process suffered an unhandled exception or ran out of usable memory.”?
- How to change color for each body in Mechanical?
© 2025 Copyright ANSYS, Inc. All rights reserved.