How does DC in *CONTACT influence the way the friction coefficient transitions between static and dynamic values?
Tagged: ls-dyna, LS-DYNA Suite, R12, structural-mechanics
-
-
January 25, 2023 at 7:34 am
FAQ
ParticipantSynopsis: The dynamic friction coefficient has no effect unless the decay coefficient DC is also defined. DC serves to smoothly transition from FS to FD over a range of velocities. If DC=0, your net friction coefficient will simply be FS. DC governs the transition from the static friction coefficient to the dynamic friction coefficient, as a function of relative velocity. As points of reference, if … DC*|Vrel| = 0.7, then the friction coefficient is halfway between FS and FD DC*|Vrel| = 4, then the friction coefficient is essentially equal to FD. Full explanation: VREL is the relative velocity of the contacting bodies at the contact point. It is computed by LS-DYNA and has units of velocity. In order for the exponent to be dimensionless, the parameter DC also has units – the inverse of velocity. Contact interaction can involve sticking (when VREL=0) or sliding (when VREL is non-zero). When this interaction is treated numerically with a Coulomb-like friction law we must be able to smoothly transition between the static and dynamic friction coefficients – the exponential involving DC and VREL accommodates this. Please look at the relation for MU and note that it yields FS when VREL=0 – this correctly corresponds to the sticking case. Now, when DC*abs(VREL) reaches a value of about 4.0 the exponential drives the second term down so that MU is within just a couple percent of FD – this corresponds to sliding. When DC*abs(VREL) is between these values we are in the transition state and MU is a combination of FS and FD. There is no “correct” value for DC; its value is the responsibility of the analyst, who must ask himself “above what relative velocity do I consider something to be sliding?”. Using this critical value of VREL the analyst then selects a value of DC, using rule of thumb stated above, such that, DC*abs(VREL) = 4.0. In this way, when VREL attains the critical value we have MU nearly equal to FD.
-
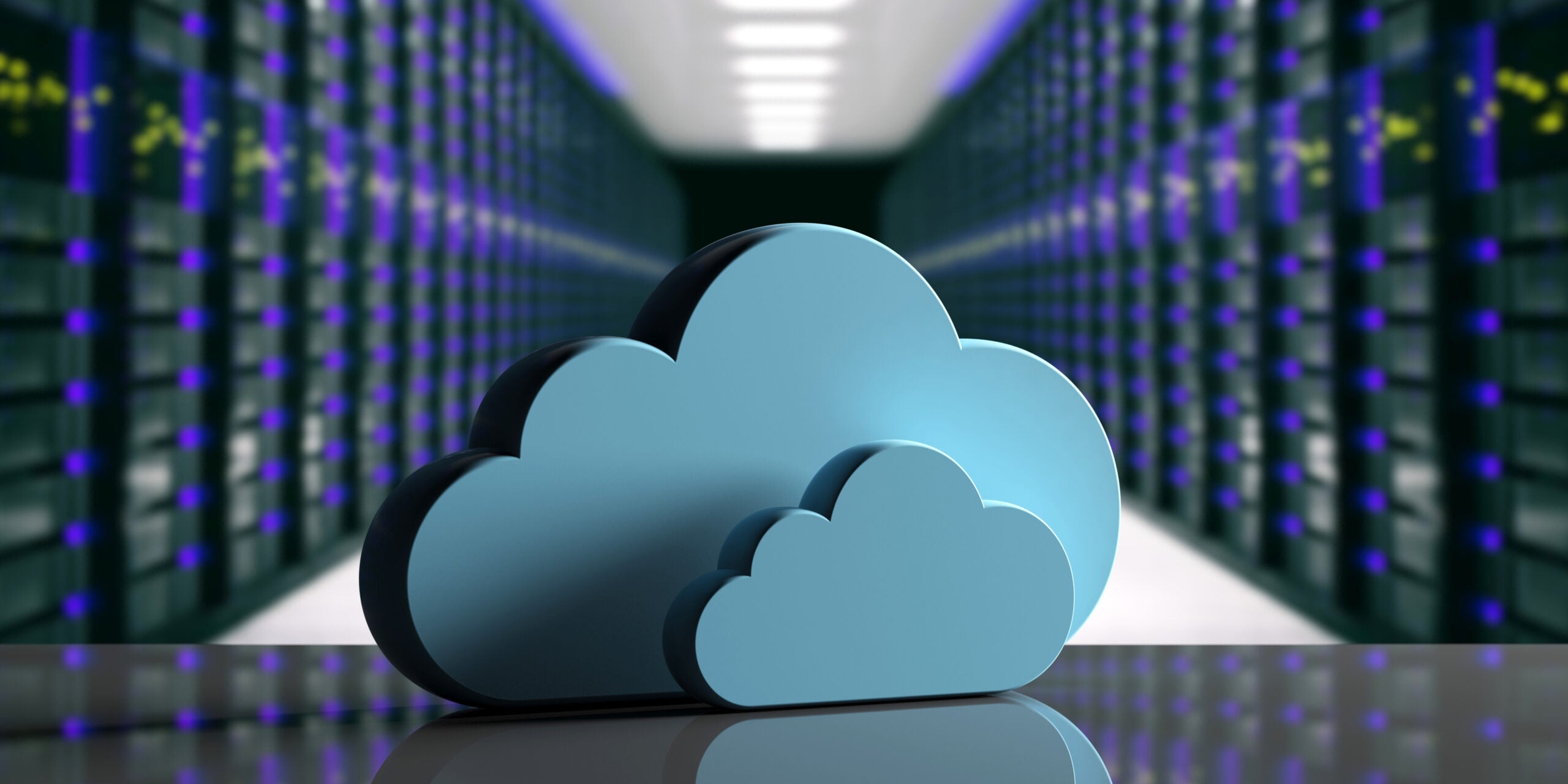
Introducing Ansys Electronics Desktop on Ansys Cloud
The Watch & Learn video article provides an overview of cloud computing from Electronics Desktop and details the product licenses and subscriptions to ANSYS Cloud Service that are...
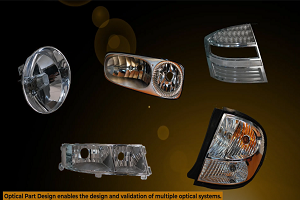
How to Create a Reflector for a Center High-Mounted Stop Lamp (CHMSL)
This video article demonstrates how to create a reflector for a center high-mounted stop lamp. Optical Part design in Ansys SPEOS enables the design and validation of multiple...
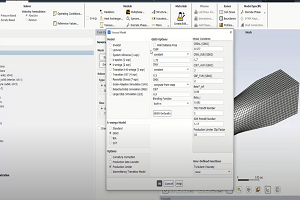
Introducing the GEKO Turbulence Model in Ansys Fluent
The GEKO (GEneralized K-Omega) turbulence model offers a flexible, robust, general-purpose approach to RANS turbulence modeling. Introducing 2 videos: Part 1Â provides background information on the model and a...
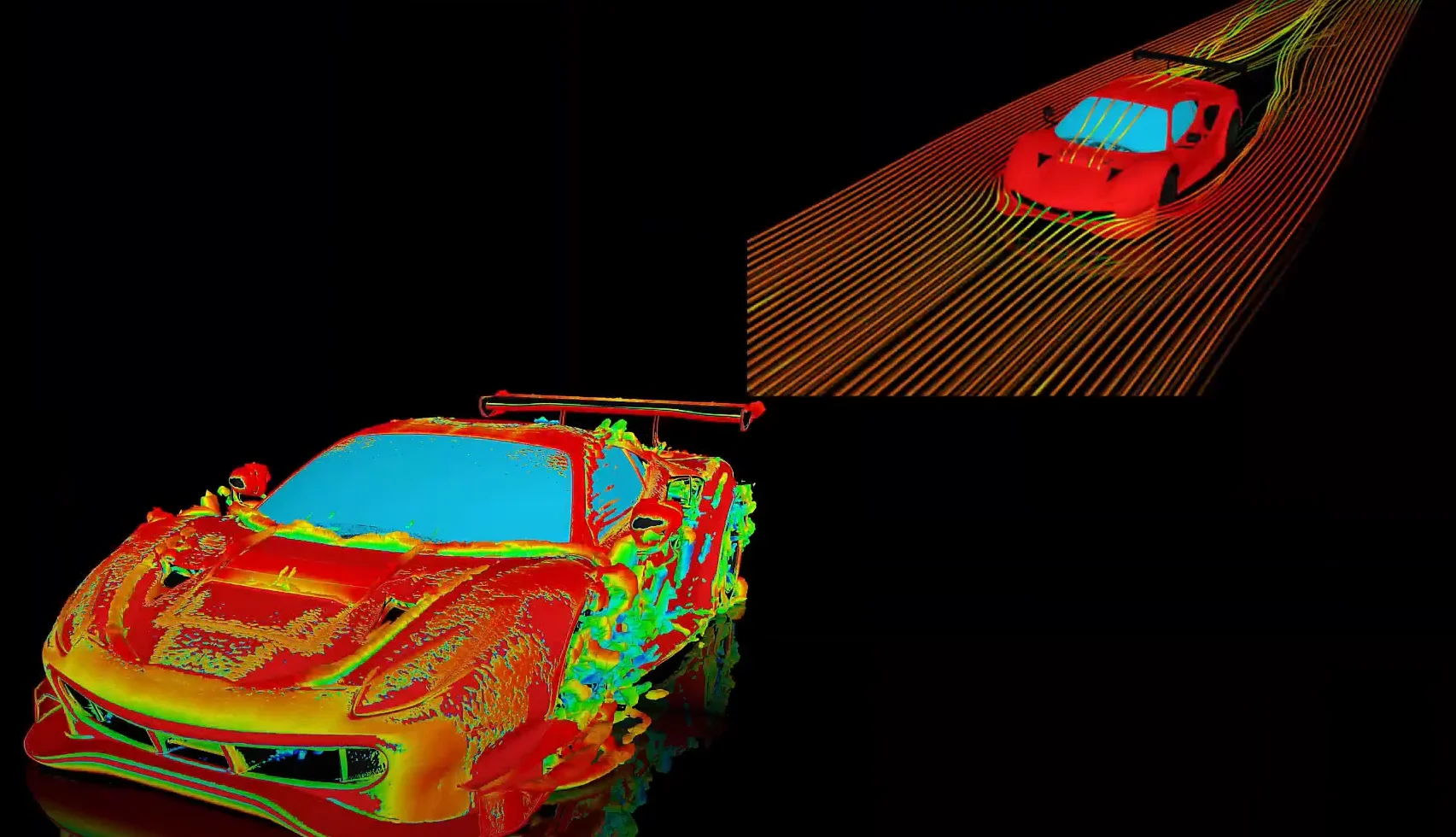
Postprocessing on Ansys EnSight
This video demonstrates exporting data from Fluent in EnSight Case Gold format, and it reviews the basic postprocessing capabilities of EnSight.
- How do I request ANSYS Mechanical to use more number of cores for solution?
- How to deal with “”Problem terminated — energy error too large””?”
- How to restore the corrupted project in ANSYS Workbench?
- Contact Definitions in ANSYS Workbench Mechanical
- There is a unit systems mismatch between the environments involved in the solution.
- How to transfer a material model(s) from one Analysis system to another within Workbench?
- How to obtain force reaction in a section ?
- How can I change the background color, font size settings of the avi animation exported from Mechanical? How can I improve the resolution of the video?
- The LS-DYNA equivalent of *MODEL_CHANGE card (in ABAQUS). Which keywords can be used to introduce(activate)/delete(deactivate) elements in the middle of a calculation (at user-specific time/load steps).
- How to resolve “Error: Invalid Geometry”?
© 2025 Copyright ANSYS, Inc. All rights reserved.