Tagged: ansys-fluent, boundary-conditions, dpm
-
-
June 6, 2022 at 8:33 am
FAQ
ParticipantThe flow rates of DPM particles and gas that are initially supplied to any 2D case are assumed to correspond with those that would apply if the model were 1m deep. Massflows can be scaled by changing the Depth under Boundary Conditions >Reference Values. Changing the depth will scale the massflows internally, so that the reported quantities correspond to the new scaled massflow.
EXAMPLE: If an equal mass of particles and fluid (each with densities set to 1000 kg/m^3) are injected. If I start with Depth set to 1m, a volume integral monitor of DPM concentration might show 64 kg. If I then change the reference depth to 0.5 m, and restart the run the volume integral monitor immediately drops to 32 kg. In each case, the DPM mass matches the mass of injected gas that I get from doing a volume integral of Density. The area average concentrations of DPM particles stay the same, however.
-
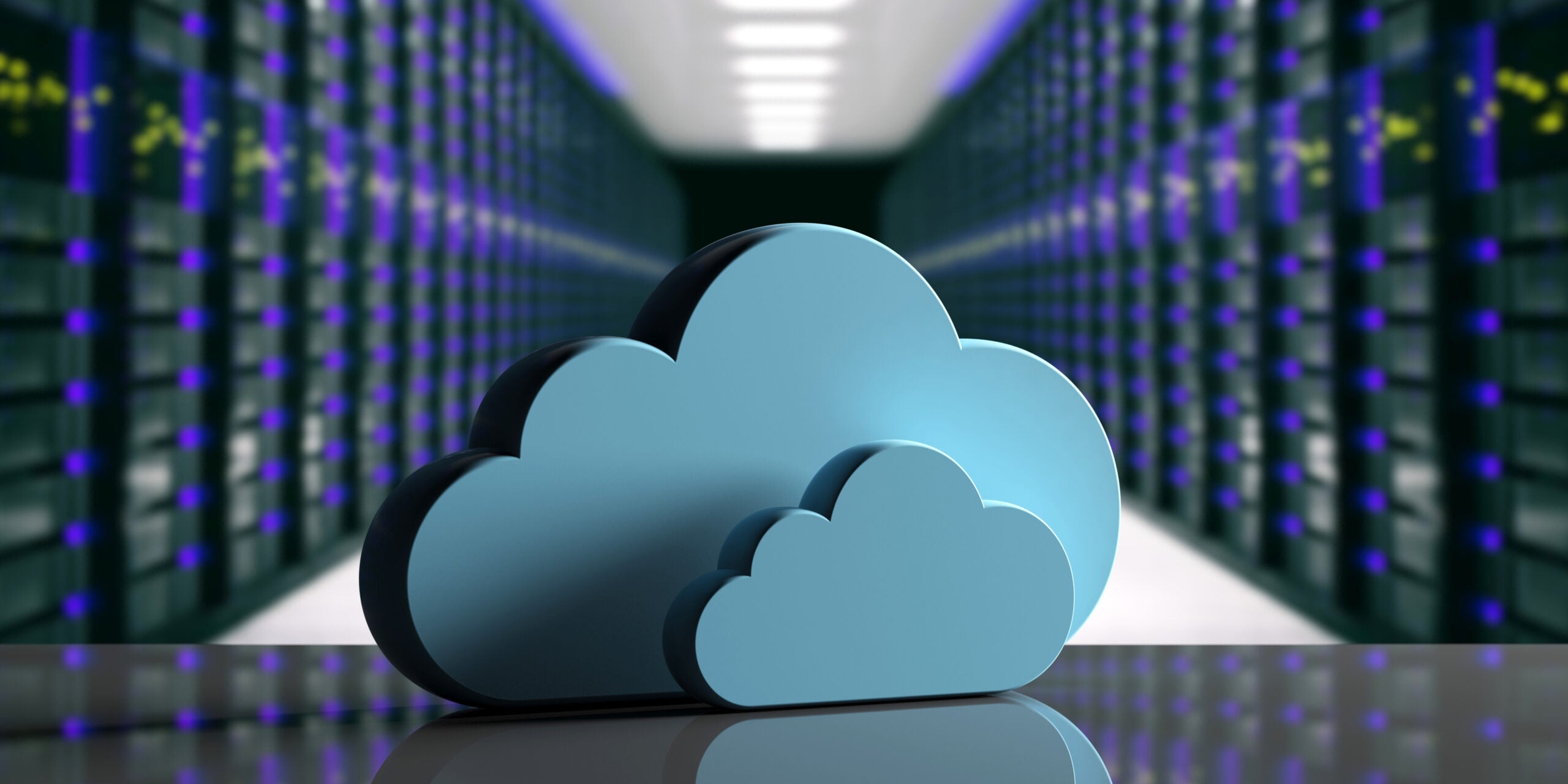
Introducing Ansys Electronics Desktop on Ansys Cloud
The Watch & Learn video article provides an overview of cloud computing from Electronics Desktop and details the product licenses and subscriptions to ANSYS Cloud Service that are...
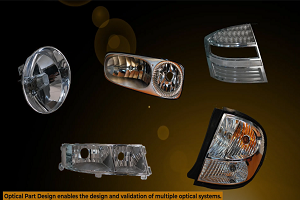
How to Create a Reflector for a Center High-Mounted Stop Lamp (CHMSL)
This video article demonstrates how to create a reflector for a center high-mounted stop lamp. Optical Part design in Ansys SPEOS enables the design and validation of multiple...
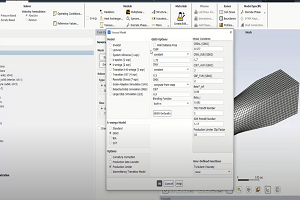
Introducing the GEKO Turbulence Model in Ansys Fluent
The GEKO (GEneralized K-Omega) turbulence model offers a flexible, robust, general-purpose approach to RANS turbulence modeling. Introducing 2 videos: Part 1Â provides background information on the model and a...
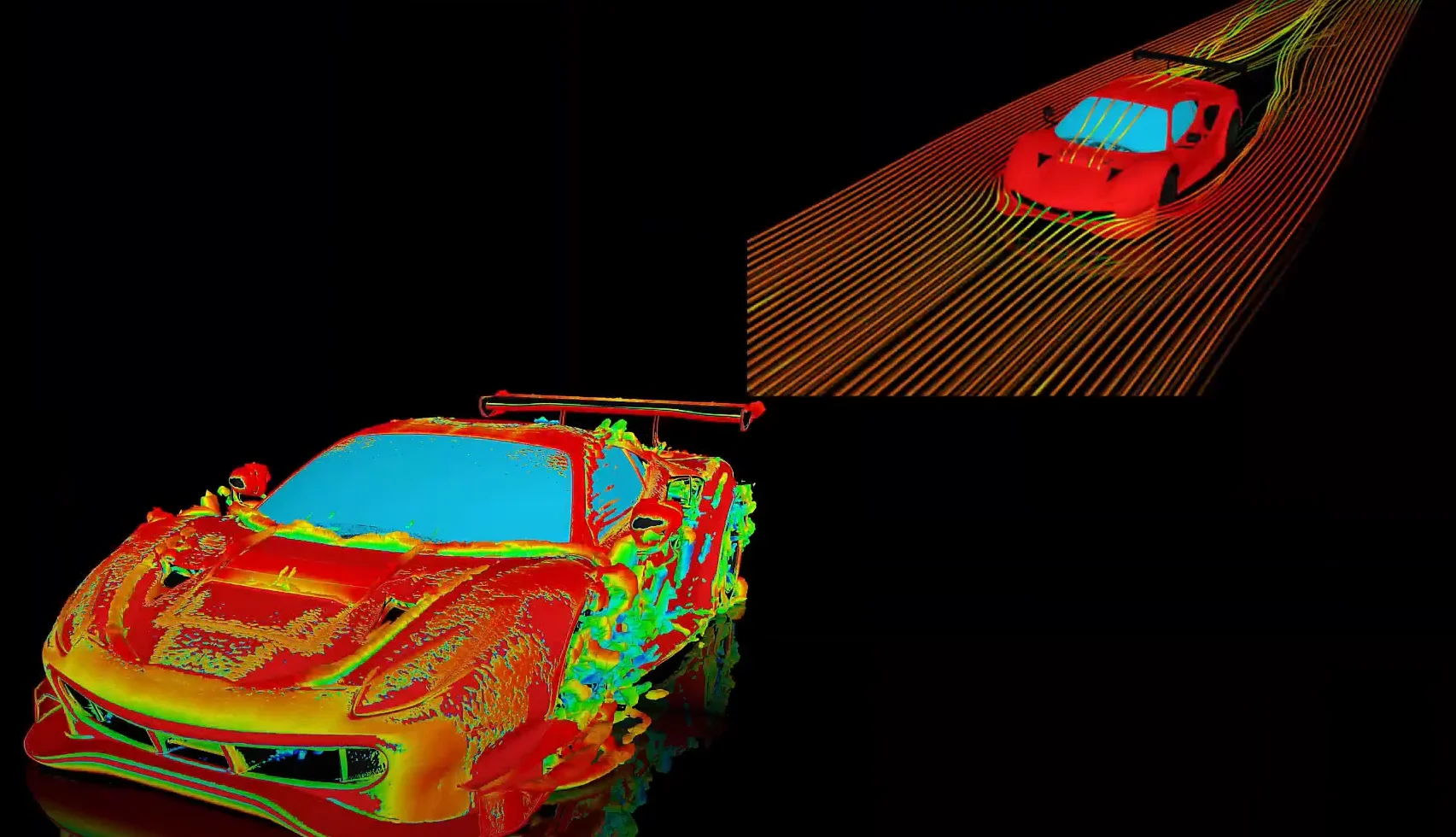
Postprocessing on Ansys EnSight
This video demonstrates exporting data from Fluent in EnSight Case Gold format, and it reviews the basic postprocessing capabilities of EnSight.
- Solver message during DPM calculation: “number of stepsize underflows during particle integration step is x”. What does it mean and how to get rid of it?
- What is the difference between the VOF model and the Eulerian model?
- ANSYS Fluent – Eulerian & Mixture Multiphase Models & Applications – Tips and Tricks
- ANSYS Fluent: Efficient Modeling of Spray Breakup using VOF-to-DPM Transition
- What is the superficial velocity in multiphase flows?
- Mixing Tank Modeling in ANSYS Fluent
- Hydrodynamics and Wave Impact Analysis
- ANSYS Fluent: Describing Cavitation in a Centrifugal Pump
- What do “incomplete” DPM particle tracks mean?
- How do I use porous media in a multiphase flow?
© 2025 Copyright ANSYS, Inc. All rights reserved.