-
-
February 4, 2021 at 1:10 pm
Fernando Torres
SubscriberHi, having issues in running 2d cutting simulation in ls dyna. LS Run immediately declares 'finished (error termination)' in red. Screenshots attached. Thanks for your help!
February 4, 2021 at 7:24 pmReno Genest
Ansys Employee.Hello Fernando,
Do you have a messag file or a d3hsp file in your C:LSDYNAprogram folder after you try to run? Do you see any warning or error message in those files?
Also, when you click on run on LS-Run, does the LS-DYNA output window appears (see below)?
Are you able to run other models? Can you download a model here and run it?
Reno.
.February 4, 2021 at 8:25 pmFebruary 5, 2021 at 5:40 amFernando Torres
SubscriberThanks Array , yeah it was contact issue. Sorted it out. Thanks for your help.
btw trying to add mat_193 (drucker prager) to plane strain case. In documentation "they" say that model's height should change in z axis and for plane strain "they" say planar geometry should lie in x-y plane. So does it mean that I can't use dp formulation for 2d cases? Thanks.
February 5, 2021 at 4:54 pmReno Genest
Ansys Employee.Hello FernandoTorres,
You should be able to use *MAT_193 with 2D plane strain solids (*SECTION_SHELL ELFORM=13). If you look in the user manual volume II (material models), you will see at the beginning of the document a list of all material models with numbers and letters at the end. For *MAT_193 it looks like this:
The "0" in between brackets means that *MAT_193 is available for 3D solids and 2D solids including plane strain:
And as you mentioned, you need to set up your geometry in the X,Y plane and the infinite thickness (plane strain) is in the Z direction.
You will find more information about 2D analyses here:
https://ftp.lstc.com/anonymous/outgoing/support/FAQ/2d_general_condensed
Reno.
.February 5, 2021 at 6:52 pmFebruary 5, 2021 at 9:38 pmReno Genest
Ansys EmployeeHello Array,
Which version of LS-DYNA are you using? I am able to run *MAT_193 in 2D plane strain with the latest Dev version or with the latest production version R12. You should try using the latest version (R12).
Reno.
February 6, 2021 at 4:56 pmFernando Torres
Subscriber.Hi rgenest , I'm using version 11 and I checked that it allows mat_193 for tshell elements. So I tried to add tshell (section) to workpiece but upon execution it's giving the following errors. I know we specify a thickness while setting the section as shell but there is no card for thickess in tshell. How to make it work? Thanks a lot!
.February 8, 2021 at 4:43 pmReno Genest
Ansys EmployeeHi Array,
Thick shell elements (*ELEMENT_TSHELL and *SECTION_TSHELL) are 3D elements like solid elements; they have a thickness of their own (by the position of the nodes) and so you do not have to specify it on the section keyword.
If you are trying to do a plane strain model with 2D solid elements, you need to use *ELEMENT_SHELL with *SECTION_SHELL and ELFORM=13. Shell elements do not have a thickness and so you have to specify it on the *SECTION_SHELL keyword. For the case of plane strain, the thickness is assumed to be infinite in the z direction. In other words, you only model a flat geometry (no thickness) in 2D in the X-Y plane and the ELFORM=13 will assume infinite thickness. This is good to model something that is very thick.
Reno.
February 8, 2021 at 5:36 pmFernando Torres
SubscriberHi Array , thanks a lot!. In autodyn I specified the failure criteria as critical strain limit with dp material model. How to define that failure criteria in ls with dp ? Thanks
February 8, 2021 at 5:44 pmReno Genest
Ansys EmployeeHi Array,
I am not familiar with the Drucker-Prager material model, but it looks like there is a failure surface shape parameter (RKF) and a yield function (see remark 4 under *MAT_193 in the LS-DYNA user manual).
An alternative would be to use *MAT_ADD_EROSION on top of *MAT_193 and use a strain failure criteria. Have a look at the manual for more information.
Reno.
February 10, 2021 at 6:04 pmFernando Torres
SubscriberHi Array , Thanks for moving my rusted machinery (my ls analysis). It worked (it started to calculate solution) finally. However it says "minimum time step reached" and it terminates. I've seen the manuals but to be honest I don't want to get into formal dense definitions of things (coz may be I'm unable to understand them). Please let me know the "exact" solution to this and how to restart an analysis simply. Thanks. (I know I'm stretching this discussion a little bit but as you know the context of the analysis, it saves me time than opening a new discussion). I appreciate your help. Thanks!
February 10, 2021 at 7:02 pmReno Genest
Ansys EmployeeHi Array,
The size of the elements dictates the time step and if you have one element that gets highly distorted and becomes very thin during the simulation, than it will control the time step and the time step will be very small because of the thin (small dimension) side of the element. The "minimum time step reached" is controlled by DTMIN on *CONTROL_TERMINATION.
You could try using larger elements to begin with; the time step will be larger and the simulation time will be less.
You can look at the results (D3PLOT) and see if some elements get highly distorted and thin during the simulation. Make sure to have enough D3PLOT to see what is happening. You can set the D3PLOT output frequency on *DATABASE_BINARY_D3PLOT.
Also, if you set a reasonable failure strain with *MAT_ADD_EROSION, the distorted elements should get deleted before the minimum time step is reached.
At last, I recommend you do some tests on a simple geometry such as a cube and use large elements so that the simulation runs quickly. Once you get the hang of it, you can start using a real geometry.
Reno.
December 6, 2021 at 5:46 pmViewing 13 reply threads- The topic ‘LS DYNA — Finished (Error Termination)’ is closed to new replies.
Ansys Innovation SpaceTrending discussionsTop Contributors-
3477
-
1057
-
1051
-
940
-
912
Top Rated Tags© 2025 Copyright ANSYS, Inc. All rights reserved.
Ansys does not support the usage of unauthorized Ansys software. Please visit www.ansys.com to obtain an official distribution.
-

Ansys Assistant
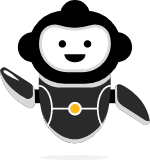
Welcome to Ansys Assistant!
An AI-based virtual assistant for active Ansys Academic Customers. Please login using your university issued email address.

Hey there, you are quite inquisitive! You have hit your hourly question limit. Please retry after '10' minutes. For questions, please reach out to ansyslearn@ansys.com.
RETRY