-
-
April 19, 2022 at 5:14 pm
Edwin1211
Subscriber- Hello, I need help to stimulate the healing process of a current of air that flows inside a metal pipe.
- The pipe is heated by external electrical resistance. Heat is generated in the resistance by joule heating, absorbed by the pipe through primary radiation, conducted through the pipe wall, and then transferred to the air stream. Attached you will find a representation of the process.
-Both the tube and the resistance are insulated by three layers of material to reduce heat leakage to the outside.
-I can run the simulation in Fluent by specifying a heat flux on the pipe wall or the wall temperature. I also know how to specify the flow of electricity through a resistor in Fluent. However, I am not sure how to generate the mesh and how to define the boundary conditions for this problem.
Q1A - 1B - 1C) Do I need to mesh the space between the resistor and the pipe? If so, do I need to specify a material for this gap, for example, air? What boundary conditions would be advisable to use for the space in between?
Q2) When I set up the S2S radiation model, does it consider the internal and external faces of the pipe?
Q3A - 3B - 3C) What boundary conditions would be recommended for the air flowing through the pipe? Would mass flow input and pressure output be fine, or would it be better to use velocity input and output? If none, what conditions would you recommend?
Could you help me with this please? :)
Thank you.
April 20, 2022 at 1:33 pmRob
Forum ModeratorYou need to mesh anything you want to involve in the calculation: the mesh makes the domain in Fluent. No mesh and it's void (ie nothing). In this case I'd cheat and use a solid zone to represent the coil region and avoid using radiation models. Your approach is potentially more accurate but the computational overhead is going to be very high. Are you interested in the flow temperature or the coil?
April 21, 2022 at 1:26 amEdwin1211
SubscriberHi Rob, thanks for your fast reply.
I am interested in both the flow temperature and the coil as I would like to see what is the effect of different coil geometries on the flow temperature inside the pipe.
Could I ask you to elaborate more on your idea of using "a solid zone to represent the coil region and avoid using the radiation model"? It sounds like a good way to run initial simulations where we only focus on the internal fluid
Thanks Rob
Edwin
April 21, 2022 at 12:23 pmRob
Forum ModeratorOK. The gap between the coil and surround will need to be meshed, as may the coil. That's going to be computationally expensive in that you'll need a lot of cells. If you can mimic the coil with a (solid) pipe you save the cell count. Do you know the heat output of a given coil such that you can apply that as a boundary condition to the model?
April 21, 2022 at 4:28 pmEdwin1211
SubscriberHi Rob,
Yes, I know the heat output of a given coil
April 25, 2022 at 3:10 pmRob
Forum ModeratorOK, if you model the coil as a "pipe" you can skip the coil bit. Then you can either have a volume heat source, or start the model at the "pipe" surface as a heat flux.
May 4, 2022 at 3:01 pmEdwin1211
SubscriberThat is very helpful. Thanks
Viewing 6 reply threads- The topic ‘Joule Heating in Fluent – External Resistance’ is closed to new replies.
Ansys Innovation SpaceTrending discussionsTop Contributors-
3367
-
1050
-
1047
-
886
-
831
Top Rated Tags© 2025 Copyright ANSYS, Inc. All rights reserved.
Ansys does not support the usage of unauthorized Ansys software. Please visit www.ansys.com to obtain an official distribution.
-

Ansys Assistant
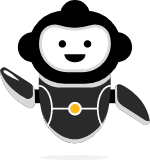
Welcome to Ansys Assistant!
An AI-based virtual assistant for active Ansys Academic Customers. Please login using your university issued email address.

Hey there, you are quite inquisitive! You have hit your hourly question limit. Please retry after '10' minutes. For questions, please reach out to ansyslearn@ansys.com.
RETRY