-
-
February 15, 2022 at 11:37 am
smm9886
SubscriberHello everyone,
I am trying to establish an FSI simulation of blood flow inside a flexible aorta and coronary artery model in ANSYS 2022R1. I am receiving the highly distorted element error in the first or second system coupling iterations. I am wondering what are some strategies that I can overcome this error? Below is a recap of my FSI model.
Domain size has an order of magnitude of ~30 [cm] and the artery wall thickness is 1-5 [mm].
In Transient structural: Artery wall of linear elasticity of 1 [MPa], Poisson's ratio of 0.49, and density of 1000 [kg/m3]. I applied Quadratic meshes with ~500k-1000k nodes and ~300k-700k elements.
In Fluent: Laminar flow of fluid with density of 1060 [kg/m3], and dynamic viscosity of 0.0035 [Pa.s]. I set the fluid walls as the system coupling. I applied Quadratic meshes with ~500k-1000k nodes and ~300k-700k elements.
In System coupling: I tried Time steps from 0.001 [s] to 0.0001 [s].
I can provide more detail if necessary. Thank you for taking the time to consider my question.
February 15, 2022 at 9:07 pmcrumberg
SubscriberI am doing something of a similar nature, but I'm an intermediate user so take this with a grain of salt. Unfortunately, troubleshooting ANSYS is a pain and excessive distortion can be caused by a number of things. Here are a few thoughts:
1) How is the artery constrained? I would play around with fixing the ends, fixing the outer surface of the vessel, applying a surface pressure to the outside of the vessel, and/or embedding the vessel in a gel-like material to see how the system responds.
2) Check the solver output. Error messages and warning messages are often more specific than those shown in the Mechanical message window.
3) Check your mesh and your contacts. In my experience, ANSYS can be picky about which mesh sizes/shapes work. Finer mesh is not always better. You can also play around with turning adaptive mesh on/off
A more experienced user may have better feedback for you, but I would probably start with these steps for troubleshooting your model.
February 16, 2022 at 4:31 ampeteroznewman
SubscriberBefore you run your FSI model, run a Static Structural model with a simple pressure load on the wall of the artery to determine the pressure at which the solution fails.
Then change the artery to use a Hyperelastic material model and follow the advice in my video. I expect the Static Structural model will run to a much higher pressure. If that is true, try rerunning the FSI.
February 16, 2022 at 9:32 amsmm9886
SubscriberThank you, for your reply.
1) My model has one inlet and three outlet boundaries. I assigned the Fixed BC to all of them. If I assigned a fixed BC to the outer surfaces of the artery walls, could they still deform? Wall compliance effects and impacts on the blood flow are essential for my studies. Formerly, I have applied a constant pressure of say 1 [kPa] on the outer surfaces of the artery wall. It did help the ANSYS solver to run for some more time steps (in contrast to the case without the constant pressure on the walls), though eventually, it failed again due to the highly distorted element error.
2) I will (my ANSYS now is running a model).
3) I could see some tiny mesh elements at the sinuses of Valsalva. Last night, I could try to increase the mesh elements sizes by applying a Mesh sizing feature. So far that I am writing this message, the ANSYS solver is still running the solution without the highly distorted element error yet.
Grazie from Italia!
February 16, 2022 at 9:48 amsmm9886
SubscriberThank you, for your message. Your video is concise and helpful, and I highly recommend other people take 10 minutes of their time to watch the video.
I have tried several meshing scenarios and time step sizes (I control the time step in System Coupling not in the Transient Structural; can I control it in Transient Structural as well?!). My ANSYS solver at the moment is occupied by another simulation. All in all, I am very curious to try your suggestions particularly 1) Hyperelastic material 2) u-P element, and 3) reduced integration elements.
This is my first time hearing about Keyops. Could you please briefly tell me how I can get to know about my element types? For example, you said it could be SOLID185. I am using Transient structural and Fluent solvers.
Grazie!
February 16, 2022 at 12:18 pmpeteroznewman
SubscriberIn the Transient Structural solver, a file called Solve.out is created that has information about the element types used in the simulation. You can see that in Mechanical in the Solution Output folder. If you have linear solid elements, it will be a SOLID185.
In Mechanical, under Analysis Settings, enter a 3 on the Identify Element Violations line shown below. A Named Selection is automatically created that shows you where the highly distorted elements are.
If the element violations are are close to the three Fixed Supports, then you should delete those and create three Remote Displacements with Behavior set to Deformable, and all six DOF set to 0.
I don't know the details of how a FSI system coupling runs the Transient Structural solver.
February 16, 2022 at 7:09 pmcrumberg
Subscriber1) Applying a fixed support to the 4 exposed cross section faces as you described makes sense. Fixing the outer faces would not work as a permanent solution for the reason that you pointed out (you would lose most of your vessel compliance) but it could be used as a troubleshooting step. Alternatively, you could set the material to steel and see if it runs. The idea is that if it fails under these conditions, there may be a problem with the geometry itself. This is not the most likely reason for the large deformation error, but it is easy to eliminate.
Since your model ran for more iterations when an external pressure was present, this may be a clue to check your materials and vessel wall thickness. In my experience so far, accurate estimates of material properties for human vessels may be hard to come by in research literature. I have seen analyses of rat aortas. Regardless, I would try double checking material properties and wall thickness. If the problem persists, you might try adding a gel chamber or other supporting structure around the vessel with the justification that the vessel is not isolated in vivo. This brings up another thought that you probably already considered: material properties are not necessarily isotropic in the blood vessel. I believe that the collagen of the tunica adventitia is oriented longitudinally while the tunica media provides circumferential support. The stiffness of the vessel also changes significantly from maximum stiffness near the aortic arch to maximum elasticity far away from the arch. The material definitions provide some advanced but easy-to-use options that should allow you to model this if you feel that this is relevant to your model.
3) Totally understand. The time it takes the solver to run is one of my least favorite aspects of troubleshooting in ANSYS. Troubleshooting the mesh can be a major pain. I would suggest also taking a look at the mesher element shapes and seeing if they make sense for your geometry.
(Greetings from Indiana! How's the weather in Italy?)
February 18, 2022 at 11:59 amsmm9886
SubscriberMany thanks, for your prompt replies to my questions. It seems my elements are SOLID 186, 187. I could learn a bunch of possible solutions that might help me to overcome the highly distorted element error. I am trying to apply them one by one, though it is too time-consuming to run an FSI model.
Out of curiosity, is it normal to take 2 weeks to run an fsi model with a workstation of 16-core and 32 GB ram? I am reading about it on the internet, it seems I shall switch to a modal-transient analysis rather than a fully transient one. I will be happy if you can please tell me something about this.
Grazie mille!
February 18, 2022 at 12:17 pmsmm9886
SubscriberDear y21 I am grateful for your prompt and thorough replies to my questions. I am trying to apply the aforementioned strategies to my model to see if it can help me to overcome the highly distorted element error. This is a very time-consuming process; I am not sure if there is something wrong with my numerical setup, but this is taking more than a week to run my models on my computer with 16 cores and 32 GB of RAM. I have tried the Steel structure as the arterial wall and my simulations were running without interruptions for 1 week (when the internet connection in my department has been lost and Ansys failed to process further and aborted due to licensing management error). All in all, I am still trying to modify the mesh to get an optimized model. And, I also think the same that I shall consider defining new materials compatible with nature. However, I could see many numerical simulations of arteries with linearly elastic walls (say E =1 MPa, Nu=0.49). This is making me try to run my primitive models with linear elastic walls. (I am located in Ancona in the middle of Italy. We won't experience that sort of freezing winters that northern parts do (Fortunately)) Grazie tante!
February 18, 2022 at 9:27 pmcrumberg
SubscriberThe time involved for running solutions is the part I hate the most about trying to debug ANSYS models. Still, I rarely have a solution take more than an hour and my computer is only 4 cores with 16GB RAM. I would venture to say that most of my runs either fail or solve within 15 minutes for models under 100K elements. There may be some ways to speed up your process. Sorry if this sounds basic, but I would check to make sure that distributed computing is turned on so that you can make use of multiple cores. The caveat is that, at least in my experience, memory reference errors can sometimes result from distributed computing so you may have to reduce the number of cores used for solving if that becomes a problem. Also, when I am trying to troubleshoot parts of the model other than the mesh, I will sometimes use a low or medium resolution adaptive mesh to try to keep my number of elements under a certain level. (If you're using the student version of ANSYS, this may not apply to your case because the solver won't even attempt to run if you have too many elements in your model due to license restrictions.) Also, if you're solving using a remote connection to a university computer, there can be delays from multiple users attempting to use the software at the same time. My university prioritizes on-campus computers over off-campus VPN connections and it helps if I work during early mornings or late evenings when fewer students are trying to access the system. Even if you are using a local installation on a university computer, heavy use on a shared license might cause delays. I think it would definitely be worth contacting your IT department for recommendations. If all else fails, running a scaled down version of you model on a free student license on your home PC should let you experiment with your model much more quickly to experiment with various model parameters.
March 13, 2022 at 6:12 pmRameez_ul_Haq
SubscriberCan I just ask here that why do you need to couple the Fluent to the Transient module? Can't this be done by simply coupling the Fluent to the Static module? Is the structure doing any rigid body motion or something?
March 22, 2022 at 12:27 pmsmm9886
SubscriberMy fluid domain is passing through some elastic walls. The fluid flow pressure deforms the elastic walls and vice versa. Do you think I can couple my time transient flow domain simulation with static structural? Please let me know your opinion about it. Grazie!
Viewing 11 reply threads- The topic ‘Fluid structure interaction highly distorted elements’ is closed to new replies.
Ansys Innovation SpaceTrending discussionsTop Contributors-
3427
-
1057
-
1051
-
896
-
892
Top Rated Tags© 2025 Copyright ANSYS, Inc. All rights reserved.
Ansys does not support the usage of unauthorized Ansys software. Please visit www.ansys.com to obtain an official distribution.
-

Ansys Assistant
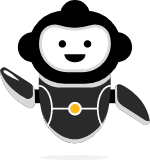
Welcome to Ansys Assistant!
An AI-based virtual assistant for active Ansys Academic Customers. Please login using your university issued email address.

Hey there, you are quite inquisitive! You have hit your hourly question limit. Please retry after '10' minutes. For questions, please reach out to ansyslearn@ansys.com.
RETRY