-
-
October 15, 2021 at 9:20 am
Haiquan
SubscriberHello
I am performing a ¼ model simulation to calculate the extraction force of grommet as shown below. I perform both implicit static and explicit quasi-static in order to compare the result.
The explicit has end time of 0.1s which makes the simulation a quasi-static simulation. I also check the hourglass and kinetic energy, it is OK. The explicit simulation setting is shown below.
I compare the force results between implicit(5N) and explicit(9N), explicit result has much higher extraction force even I have used hex dominant mesh.
I also found that the grommet in static case has been pulled out of the steel(that is why we see a force drop in the curve), but for explicit case, we don’t see this(force still increases). Both cases use 8mm displacement load in the same location.
I also use simple cases(tension, compression, shear) to check the difference. The results have good agreement between implicit and explicit except the simple case of compression with connection. Using different connection will have different result, the contacts case is more close to implicit result, the body interaction case is stiffer.
My question is why the response is stiffer in explicit case? What can we do to obtain similar results between implicit and explicit?
I attach my case with ANSYS 2020 R1 if you are willing to check. My explicit solver is Autodyn. Mooney-Rivlin parameter: C10=0.45822Mpa, C01=0.18055Mpa, D1=0.01Mpa-1
Thank you in advance !
October 19, 2021 at 5:34 pmChris Quan
Ansys EmployeeFirst of all, Static Damping is designed to remove kinetic energy of the entire model and have the model in the static equilibrium. So the Static Damping should be set to 0 in your model. Otherwise it will stop the grommet motion. That's why you won't observe the grommet pulled out of steel.
I would suggest trying Multizone meshing method to mesh the grommet. HEX dominant creates the HEX mesh on surfaces but the interior mesh quality is not very good, which could make the material exhibiting more rigid deformation. If tetra elements are used, I would suggest using Nodal Based Strain (NBS) element formulation as Tet Integration in Solver Controls to avoid any volume locking and shear locking.
In the compression tests, if contacts have been fully defined under Contact Regions, you don't need to have Body Interactions. If Body Interaction is used instead of Contact Regions, you may change the Sliding Contact from Discrete to Connected to see if it improves the results.
October 22, 2021 at 9:31 amHaiquan
SubscriberThank you very much for your comments ! As you have mentioned, the root cause is the static damping! I set an unrealistic static damping which made the explicit pulling force much higher. Now I got more close result and I also observed the grommet was pulled out of the steel(a force drop in the curve now!).
But I found another issue in my ┬╝ model(symmetry condition has been set in bothX and Y), in an explicit quasi-static simulation, action force and reaction force should be equal.
I run a full model as shown below, action force and reaction force are equal, these is no issue in a full model. I am confused about result in 1/4 model.
October 29, 2021 at 2:15 amHaiquan
Subscriberany comment about the unbalance force issue in a 1/4 model? Thank you !
Viewing 3 reply threads- The topic ‘Comparison between implicit and explicit results for quasi-static simulation’ is closed to new replies.
Ansys Innovation SpaceTrending discussionsTop Contributors-
3492
-
1057
-
1051
-
965
-
942
Top Rated Tags© 2025 Copyright ANSYS, Inc. All rights reserved.
Ansys does not support the usage of unauthorized Ansys software. Please visit www.ansys.com to obtain an official distribution.
-

Ansys Assistant
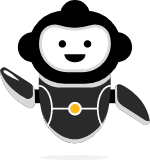
Welcome to Ansys Assistant!
An AI-based virtual assistant for active Ansys Academic Customers. Please login using your university issued email address.

Hey there, you are quite inquisitive! You have hit your hourly question limit. Please retry after '10' minutes. For questions, please reach out to ansyslearn@ansys.com.
RETRY