What is the order followed while adding layers for the multi-layer shell conduction model ( MLS ) in Fluent ?
-
-
March 17, 2023 at 1:11 pm
Solution
Participant1) The Multi-layer shell ( MLS ) conduction model is used to simplify different layers of a thin surface ( viz. heat shield) into a single baffle and model all the different layers for shell conduction ( thickness, material ) 2) The order followed for addition of layers will be: i. If external surface boundary surface ( i.e. mesh on only one side of the surface ) ii. If internal baffle surface ( i.e. mesh on both sides of the surface ) 3) For a surface with mesh on both sides ( baffle surface ), a wall will be created by the Fluent solver on the side with positive normal orientation of that surface. The other side becomes a wall shadow surface. 4) The orientations of surface normals can be checked in Fluent meshing>display mesh. Layers will be added away from the mesh in the pattern as shown in the attached resolution document. Layers will always be added starting at a wall zone and moving toward the partner wall-shadow zone. 5) For the MLS model, make sure the wall side of the surface is towards the desired position/orientation while adding layers for different materials and thickness. This is the requirement for layers propagated from wall to wall-shadow. If this is not possible, then the normals of the surface can be re-oriented in meshing, or more conveniently, the layers for the MLS model can be added in the reverse fashion, i.e. first layer3, then layer2 and then layer1 (see attached resolution document for more detail)
Attachments:
1. KM#2052286.pdf
-
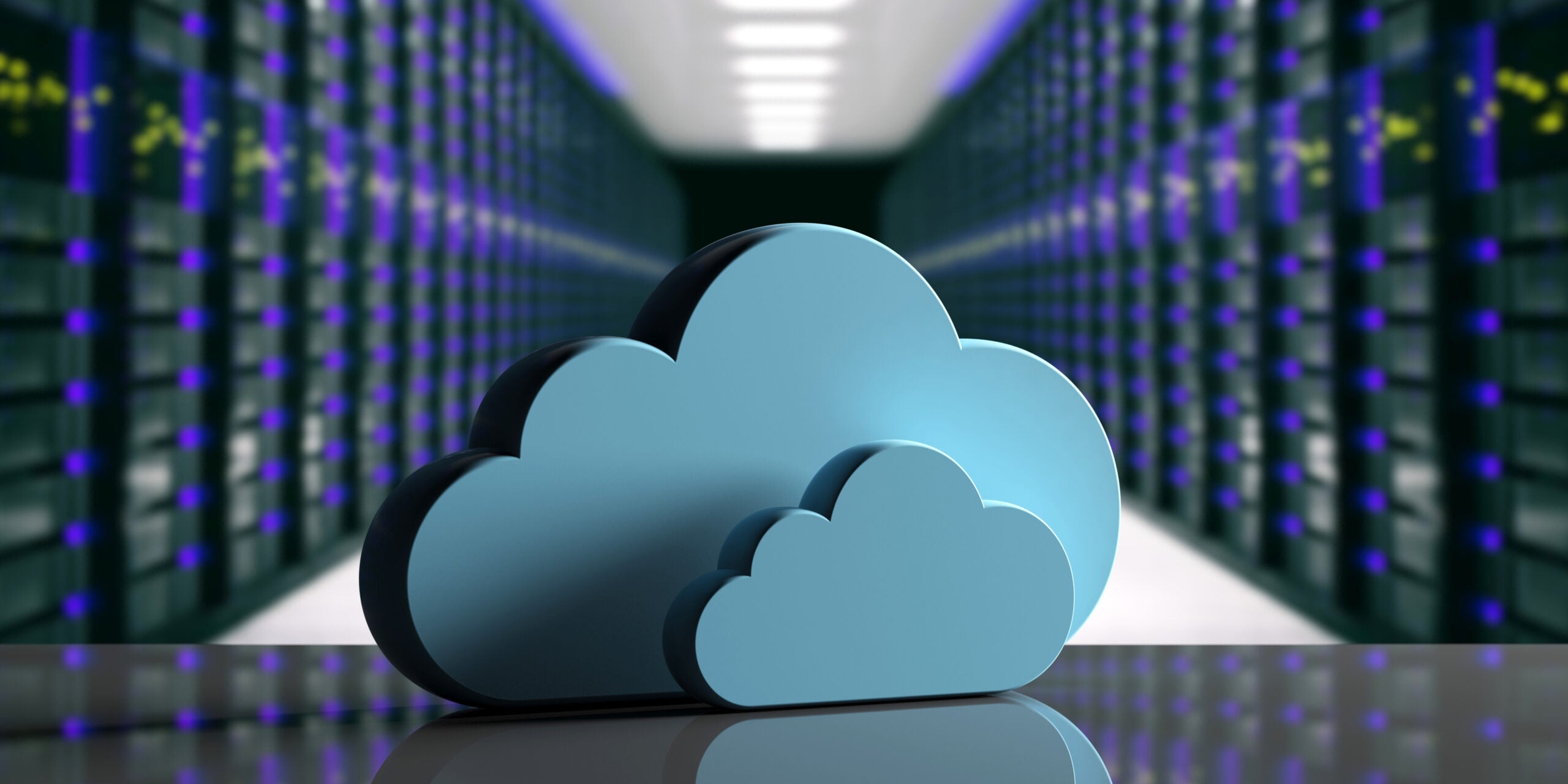
Introducing Ansys Electronics Desktop on Ansys Cloud
The Watch & Learn video article provides an overview of cloud computing from Electronics Desktop and details the product licenses and subscriptions to ANSYS Cloud Service that are...
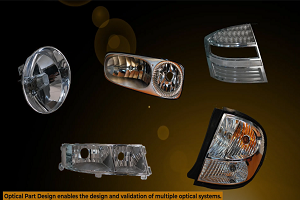
How to Create a Reflector for a Center High-Mounted Stop Lamp (CHMSL)
This video article demonstrates how to create a reflector for a center high-mounted stop lamp. Optical Part design in Ansys SPEOS enables the design and validation of multiple...
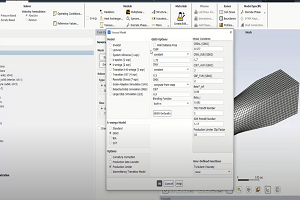
Introducing the GEKO Turbulence Model in Ansys Fluent
The GEKO (GEneralized K-Omega) turbulence model offers a flexible, robust, general-purpose approach to RANS turbulence modeling. Introducing 2 videos: Part 1Â provides background information on the model and a...
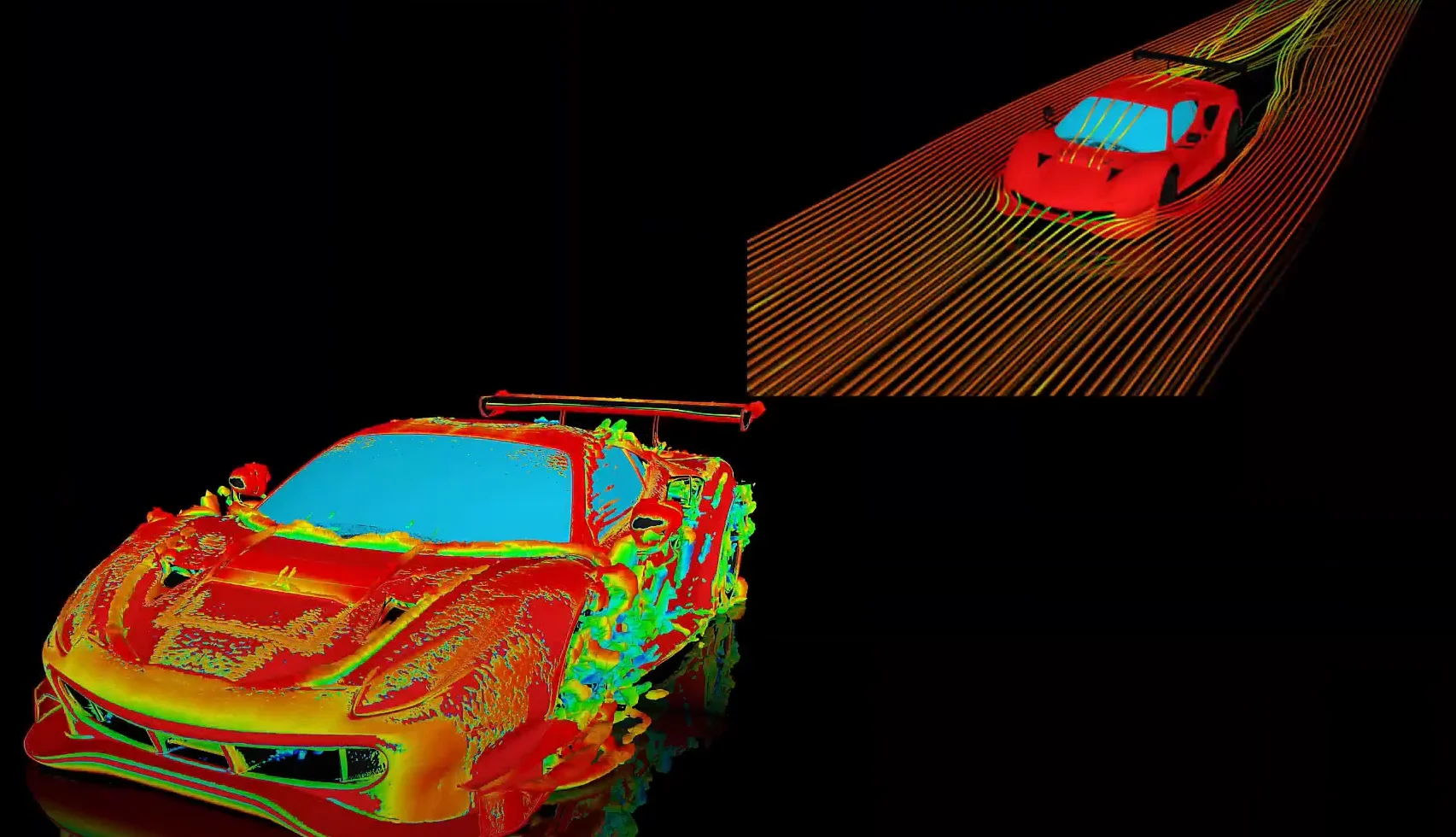
Postprocessing on Ansys EnSight
This video demonstrates exporting data from Fluent in EnSight Case Gold format, and it reviews the basic postprocessing capabilities of EnSight.
- Defining heat transfer coefficient (HTC)
- Thermal Analysis of a Radiator Using Ansys Fluent
- Simulating Battery Pack Cooling System Using Ansys Fluent
- How to solve the warning: “Warning: zone of type interior found between different solids!”
- How to add comments to journal file so that I will know what each entry does?
- In ANSYS Fluent, when the energy equation is enabled and viscous heating is enabled, must pressure work also be turned on?
- How to use Thin Walls with Thermal boundary conditions?
- ANSYS Fluent: Overview of the Mapped Interface Technique for CHT Simulations (18.2)
- ANSYS Fluent Student: Conjugate Heat Transfer in a Heat Sink
- What is the difference between internal and external emissivity?
© 2025 Copyright ANSYS, Inc. All rights reserved.