Tagged: Aerospace, cinvestav, guest article, SCADE, scade rapid prototyper, scade suite, scade test, student
-
-
August 7, 2024 at 9:12 am
Solution
ParticipantGuest Article – Student – Cabin Pressurization Control System with SCADE
This article is a guest contribution from Cinvestav. It was written by a student group as part of Masters-level, semester long SCADE academic program course.
It explains the design and simulation of a system that controls the cabin pressure of an aircraft with a model-based design approach with Ansys SCADE. This article explains the design made from the system requirements, verification, coverage, and finally some scenarios of a simulation made of a control panel.
If you are an academic and are interested in teaching an engineering curriculum backed by Ansys tools, please have a look at our Ansys Funded Curriculum page.
Summary
Cabin pressurization is a critical system for every aircraft unit, in order to keep a safe and comfortable cabin pressure.
In this context, Ansys Scade was used to model the entire system and control the cabin pressure through the regulation of the aircraft’s inflow and outflow valves. To achieve safe control, the CPCS can operate in one of the following modes: Auto, Manual, and Emergency. Each of these modes calculates the pressurization rate command, which is sent to a designed aircraft model in a closed loop with the CPCS. Finally, a Rapid Prototyper of a cockpit panel control is implemented in the simulation.
CPCS
OPERATION
The CPCS controller sends a pressurization rate command to the aircraft, where the pressurization rate is converted into the opening of the adjustable outflow valves. Additionally, a rapid depressurization command is sent from the CPCS controller to the aircraft, indicating whether an emergency valve will be fully opened or not, allowing air to enter and pressurize the cabin.
The CPCS operation modes can be one of the following:
- Auto. In this mode the pressurization rate is calculated by a PI controller.
- Manual. In this mode the pressurization rate is equal to the command entered by the user in the control panel.
- Emergency. In this mode the outflow valves close and the emergency valve opens.
If the cabin altitude exceeds the maximum allowed altitude of 15,000 ft, the CPCS automatically enters Emergency mode. It remains in Emergency mode until the cabin altitude drops below the release threshold of 10,000 ft, at which point it returns to the mode selected by the user.
The CPCS also measures the differential pressure between the aircraft’s altitude and the cabin altitude. If the measured differential pressure exceeds the maximum allowed differential pressure of 6.5 psi, the CPCS notifies the user to reduce the aircraft’s altitude and, therefore, the differential pressure.
FEATURES
The maximum value of the pressurization rate command is dictated by the physics of the valves and the cabin, as well as other physical parameters like temperature, with these values set at 500 fpm for the outflow valves and 3000 fpm for the emergency valves.
In Auto mode, the altitude that the controller will maintain is referred to as the target altitude. The CPCS maintains the cabin altitude at 8,000 ft when the aircraft’s altitude is above this altitude. Otherwise, the target altitude is the aircraft’s altitude.
The system has two alarms: one for rapid depressurization emergencies and another for differential pressure. It also displays the cabin altitude, aircraft altitude, and the pressurization rate command.
Design
REQUIREMENTS
Some examples of implemented requirements are the following:
For behavior:
CPCS_HLR_BE _04
: If rapid depressurization is measured, then CPCS shall be automatically and immediately in EMERGENCY mode.For cabin pressure control:
CPCS_HLR_CPC_03
: When CPCS mode is in AUTO, cabin pressure shall be automatically regulated to maintain the target altitude provided.For target altitude:
CPCS_HLR_TA_01
: When CPCS mode is in AUTO and aircraft altitude is below RegularCabinAltitude, target altitude shall be aircraft altitude.CPCS_HLR_TA_02
: When CPCS mode is in AUTO and aircraft altitude is above RegularCabinAltitude, target altitude shall be RegularCabinAltitude.For rapid depressurization:
CPCS_HLR_RD_01
: CPCS shall immediately activate rapid depressurization if cabin altitude is above MaxCabinAltitude.For differential pressure:
CPCS_HLR_DIFF_01
: CPCS shall display an alarm on the control panel if measured differential pressure has exceed the MaxDiffPressure.Parameters:
CPCS_HLR_PAR_01
: RegularCabinAltitude: 8000 ft.CPCS_HLR _PAR_02
: MaxCabinAltitude: 15000 ft.CPCS_HLR _PAR_03
: MaxDiffPressure: 6.5 psi.CPCS_HLR _PAR_04
: ReleaseEmerAltitude: 10000 ft.MODEL
Call Graph
- CPCS
- CPCS Controller
- CPCS
- DiffMeasurement
- FtoM
- FtoPsi
- PressRateRegul
- RapidDepress
- Aircraft
- AircraftModel
- InflowTurbinePressure
- Valves
- ValvesRegulator
- System
- SystemSimul
- CPCS Controller
SystemSimul
SystemSimul
is the root operator, which contains the closed loop architecture of the CPCS with the aircraft. The CPCS sends the pressurization rate and rapid depressurization commands to the aircraft. The aicraft then calculates the new cabin altitude and sends this data back to the CPCS, completing the feedback loop.CPCS
The CPCS controller has a state machine for the operating modes. Each mode controls the pressurization rate command output. At the same time, the
DiffMeasurement
operator and theRapidDepress
functions work at any mode.DiffMeasurement
The
DiffMeasurement
function operator calculates the differential pressure and activates the alarm if it is above the max diff pressure.FtoM
This function operator converts the input value feet to meters. This models the equation:
$$M = 0.3048 ft$$
FtoPsi
The
FtoPsi
function operator converts the altitude in feet to its corresponding pressure value in psi. This is mathematical expression:$$14.7 \times \left(1 – \frac{0.0065 \times M}{288.15} \right)^{5.2561}$$
First, the altitude in feet is converted to meters to then execute the above equation.
PressRateRegul
PressRateRegul
node operator is a band limited close loop feedback PI controller. The integral and proportional constants were calculated for a critically dumped answer. Thelibilnear
library, contains the integral operator.The next table shows all the parameters used in
PressRateRegul
operator.RapidDepress
RapidDepress
node operator controls the rapid depressurization alarm. As mentioned before, if the cabin altitude exceeds the max cabin altitude, alarm will be activated till the cabin altitude drops below the release emergency altitude threshold.AircraftModel
AircraftModel
node operator manipulates the input pressurization rate command and rapid depressurization and outputs the corrected cabin altitude, outflow valve opening and safety opening.ValvesRegulator
The ValvesRegulator function operator translates and converts the pressurization rate command and the rapid depressurization alarm into the valve opening, within a range of 0 to 1.
InflowTurbinePressure
InflowTurbinePressure
function operator calculates and outputs the inflow pressurization rate in feet per minute that comes from the turbine.Valves
Valves
node operator calculates the new cabin altitude in accordance to the valves opening coming from theValvesRegulator
operator.VERIFICATION
Tests
Two records were created to include all the requirements needed. The first record includes the CPCS Behavior, where the scenario includes some tests for the operating modes, the target altitude and the manual pressurization rate.
In the second record, emergencies scenarios were included to verify the function of the emergency mode for the rapid depressurization, as well as for the max differential pressure.
CPCS_Behavior scenario:
## inputs SSM::set PressRateManual 150.0 SSM::set AircraftAltitude 35000.0 SSM::set ModeSel Auto # CPCS_HLR_BE_01 # When the system starts, CPCS shall be in Auto mode SSM::cycle 1 SSM::check Mode Auto SSM::cycle 1 # CPCS_HLR_BE_03 # When the Manual is selected, CPCS shall be immediately in Manual mode SSM::set ModeSel Manual SSM::cycle 1 SSM::check Mode Manual SSM::cycle 1 # CPCS_HLR_CPC_01 # When CPCS is in Manual. cabin pressure shall be regulated by manually recording # the pressurization rate in the cabin control panel SSM::set PressRateManual 200.0 SSM::check PressRateCmd 200.0 SSM::cycle 1
Emergencies scenario:
# Take the cabin altitude close to EmergencyAltitude (15000.0 ft) SSM::cycle 43 # CPCS_HLR_RD_01: CPCS shall immediately activate rapid depressurization if cabin altitude is above EmergencyAltitude # CPCS_HLR_BE_04: If rapid depressurization is measured, then CPCS shall be immediately and automatically in Emergency mode # CPCS_HLR_RD_03: CPCS shall immediately open the safety inflow valve to pressurize at 3000 fpm if rapid depressurization is active SSM::check RapidDepress true SSM::check Mode Emergency SSM::check SafetyOpening 1.0 SSM::cycle 2 # CPCS_HLR_BE_05 # When CPCS is in Emergency and the cabin altitude is below ReleaseEmerAlt # CPCS shall return to Auto SSM::set ModeSel Auto SSM::check CabinAltitude {x-> x < 10000.0} SSM::check Mode Auto SSM::cycle 1 # CPCS_HLR_DIFF_01: CPCS shall display an alarm in the control panel if measured diff pressure exceeds MaxDiffPressure # CPCS_HLR_DIFF_02: CPCS shall display the values of the measured diff pressure and cabin altitude SSM::set AircraftA1titude 50000.0 SSM::check DiffPressureAlarm true SSM::check DiffPressure {x-> x > 6.5} SSM::cycle 1
Coverage
SIMULATION
To demonstrate the application of the CPCS, a Rapid Prototyper was designed using SCADE. This prototyper allows connections between inputs and outputs and the manipulation of these signals in simulation of the root operator SystemSimul. The prototyper displays a cockpit control panel with some of the required values and measurements, enabling users to observe the response of the CPCS to different situations.
On the upper right side of the control panel are the mode selector, manual pressurization rate, and aircraft altitude, simulating the barometer sensor. On the lower right side, there are two counters: one for the differential pressure and another for the cabin altitude.
On the upper left side, there is an LED alarm for rapid depressurization and another LED for maximal differential pressurization. Below these alarms, there is a graph of the altitudes: in green, the cabin altitude, and in blue, the aircraft’s altitude, each with its own altitude marker. At the bottom, there is a graphical representation of the valve openings, with black indicating fully closed and white indicating fully open.
Next are some situations to proof the correct operation of the CPCS.
Scenario 1 – Depressurizing
In this context, mode is Auto, the aircraft is near 35,000 ft, and the cabin altitude is 8,000 ft. The graphic shows the regulation of the cabin altitude with the PI control, making the form of a critically dumped control.
Scenario 2 – Pressurizing
In this situation, mode is Auto and the cabin altitude is getting low to stay at the same aircraft’s altitude.
Scenario 3 – Max diff press
In this situation, the aircraft’s altitude is set to nearly 45,000 ft, while the cabin altitude remains at 8,000 ft. The pressure difference exceeds the maximum expected 6.5 psi. The pilot should then decrease the aircraft’s altitude.
Scenario 4 – Rapid depressurization
In this scenario, the mode is manual, and the manual pressurization rate is set at 420 fpm. When the cabin altitude exceeds the maximum cabin altitude of 15,000 ft, the rapid depressurization alarm is activated, and the safety valve opens.
MBD and SCADE
Incorporating Model-Based Design (MBD) into my project has been instrumental in transforming the development process. By leveraging MBD principles, I created detailed system models that accurately represented my design. These models enabled me to simulate and analyze the system’s behavior comprehensively before physical implementation.
Throughout the testing and validation phases, MBD facilitated rigorous testing against my models, ensuring that the final system met all requirements and specifications. This iterative process of model refinement based on testing feedback was essential in achieving a robust and reliable solution.
Integrating SCADE Suite and SCADE Rapid Prototyper into my project has been vital in applying Model-Based Design (MBD) principles effectively. SCADE Suite provided a robust environment for creating detailed system models using graphical block diagrams. This allowed me to develop complex logic and control algorithms visually, ensuring accuracy and reliability from the outset.
With SCADE Rapid Prototyper, I was able to simulate and validate the behavior of my designs in real- time. This capability was essential for early detection of design flaws and optimization of system performance before physical implementation.
About the authors
Isaac Hernandez and Alejandro Pardo Ordaz are Embedded Systems students in Guadalajara, Mexico. They developed this model and article as part of a course on Programming and Design based on Embedded Systems Modeling.
Bibliography
- Gregory N. Brown & Mark J. Holt. The Turbine Pilot’s Flight Manual. Third edition, Aviation Supplies & Academics Inc.: 2012.
- David Wyatt & Mike Tooley. Aircraft electrical and electronic systems. Second edition, Routledge: 2018.
- Ian Moir & Allan Seabridge. Aircraft sytems: mechanical, electrical and avionics subsystems integration. Third edition, John Wiley & Sons, Ltd: 2008.
-
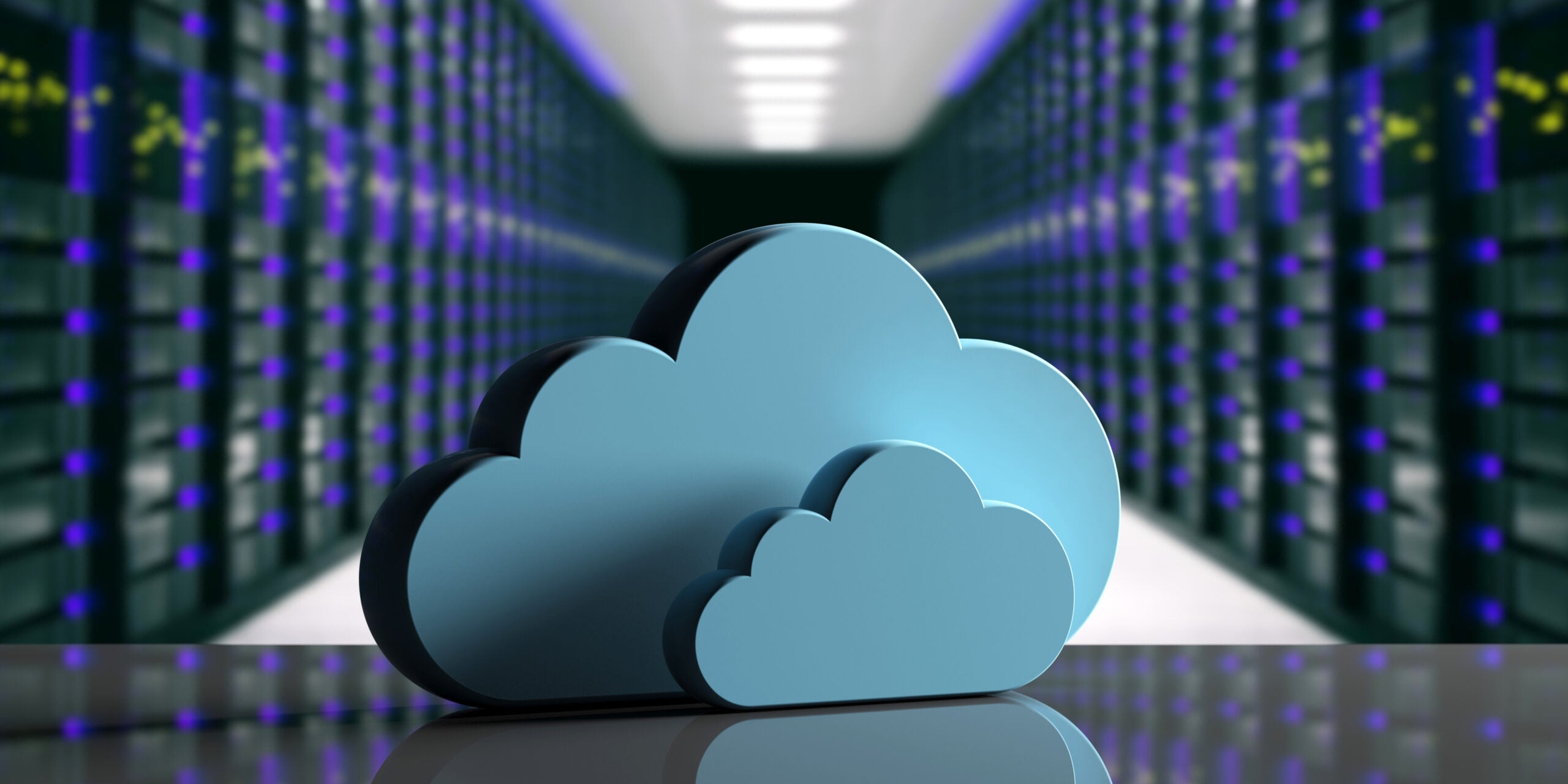
Introducing Ansys Electronics Desktop on Ansys Cloud
The Watch & Learn video article provides an overview of cloud computing from Electronics Desktop and details the product licenses and subscriptions to ANSYS Cloud Service that are...
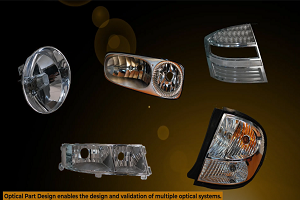
How to Create a Reflector for a Center High-Mounted Stop Lamp (CHMSL)
This video article demonstrates how to create a reflector for a center high-mounted stop lamp. Optical Part design in Ansys SPEOS enables the design and validation of multiple...
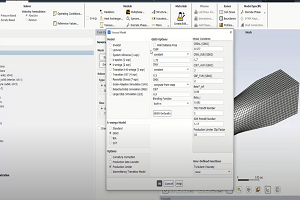
Introducing the GEKO Turbulence Model in Ansys Fluent
The GEKO (GEneralized K-Omega) turbulence model offers a flexible, robust, general-purpose approach to RANS turbulence modeling. Introducing 2 videos: Part 1Â provides background information on the model and a...
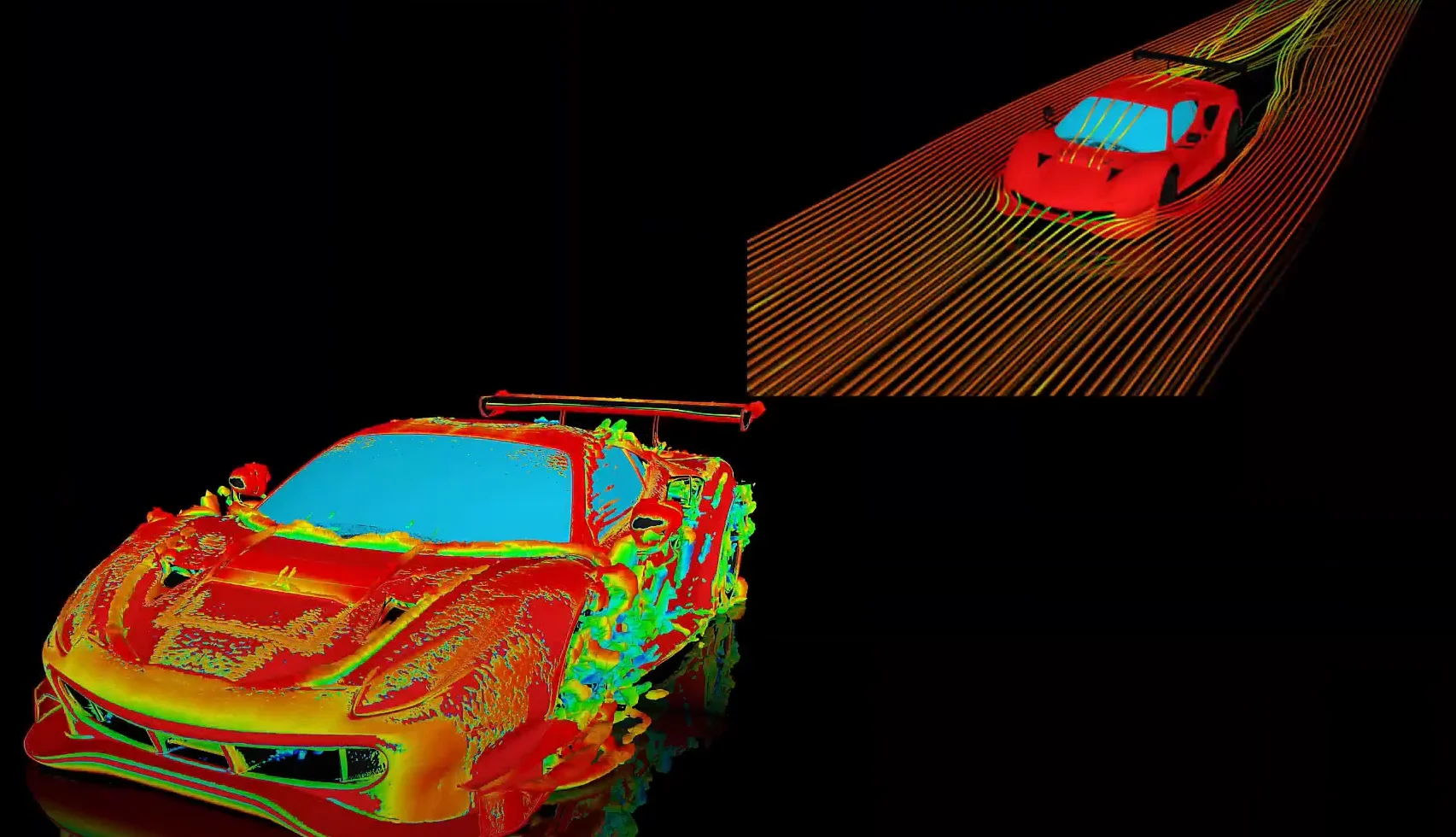
Postprocessing on Ansys EnSight
This video demonstrates exporting data from Fluent in EnSight Case Gold format, and it reviews the basic postprocessing capabilities of EnSight.
- Scade One – Bridging the Gap between Model-Based Design and Traditional Programming
- Scade One – An Open Model-Based Ecosystem, Ready for MBSE
- Scade One – A Visual Coding Experience
- How to Verify a Model on Host with SCADE Test? (Part 4 of 6)
- Using the SCADE Python APIs from your favorite IDE
- Introduction to the SCADE Environment (Part 1 of 5)
- How to integrate multiple SCADE models into one executable
- Scade One – Democratizing model-based development
- How to Generate Code with SCADE Display (Part 6 of 6)
- ANSYS SCADE – Map Iterator – Comparison Function: C and SCADE Methods Comparison (Part 4 of 4)
© 2025 Copyright ANSYS, Inc. All rights reserved.