POLYFLOW: 3d contact – Interpolation schemes are limited to linear for velocities, constant for pressure
Tagged: 16, fluid-dynamics, General, polyflow
-
-
March 17, 2023 at 8:58 am
FAQ
ParticipantIn a 3D contact problem, after defining the boundary conditions (free surface and contact conditions) and selecting Lagrangian Remeshing method, the only interpolation options are “Linear velocities, constant pressure”. Is this true for the contact problem? When can I use other schemes such as mini-element or quadratic velocities? Is this limitation to have a realistic solution time for 3d contact problems? When one has a linear interpolation for the velocity, we have the same number of unknowns for the velocity and coordinates. In other words, there is a velocity vector for each node and the node moves with that velocity. If another interpolation would be selected for the velocity, there would be more velocity vectors than available nodes. For several simulation cases, this does not make any trouble, e.g. for steady extrusion flows. However, for contact simulations, this could have some consequences: a typical side effect indeed would be that one may have a non-zero velocity in the middle of a face while there would be no corresponding node motion. In other words, it means an entry or exit of material. Furthermore, in contact simulations, contact is detected only at actual mesh nodes where a velocity can be indeed cancelled via the mechanism of penalty. If one has a concave border, one could easily imagine a situation where all nodes are detected in contact but the central velocity would perhaps never see the contact. In summary, having an equal number of material nodes and velocity vectors is the best option.
-
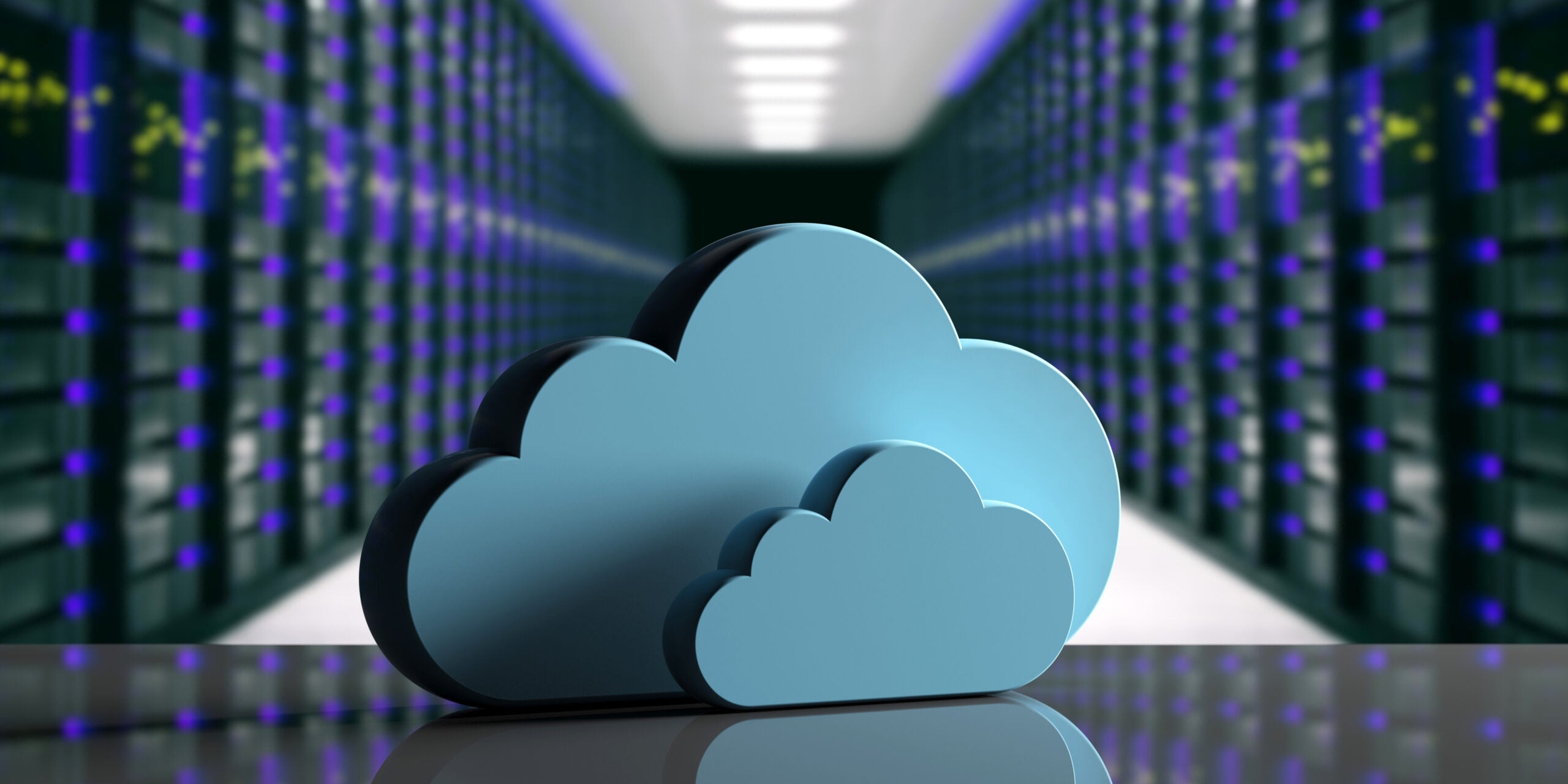
Introducing Ansys Electronics Desktop on Ansys Cloud
The Watch & Learn video article provides an overview of cloud computing from Electronics Desktop and details the product licenses and subscriptions to ANSYS Cloud Service that are...
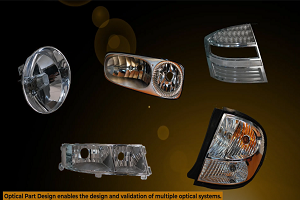
How to Create a Reflector for a Center High-Mounted Stop Lamp (CHMSL)
This video article demonstrates how to create a reflector for a center high-mounted stop lamp. Optical Part design in Ansys SPEOS enables the design and validation of multiple...
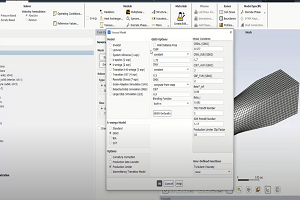
Introducing the GEKO Turbulence Model in Ansys Fluent
The GEKO (GEneralized K-Omega) turbulence model offers a flexible, robust, general-purpose approach to RANS turbulence modeling. Introducing 2 videos: Part 1 provides background information on the model and a...
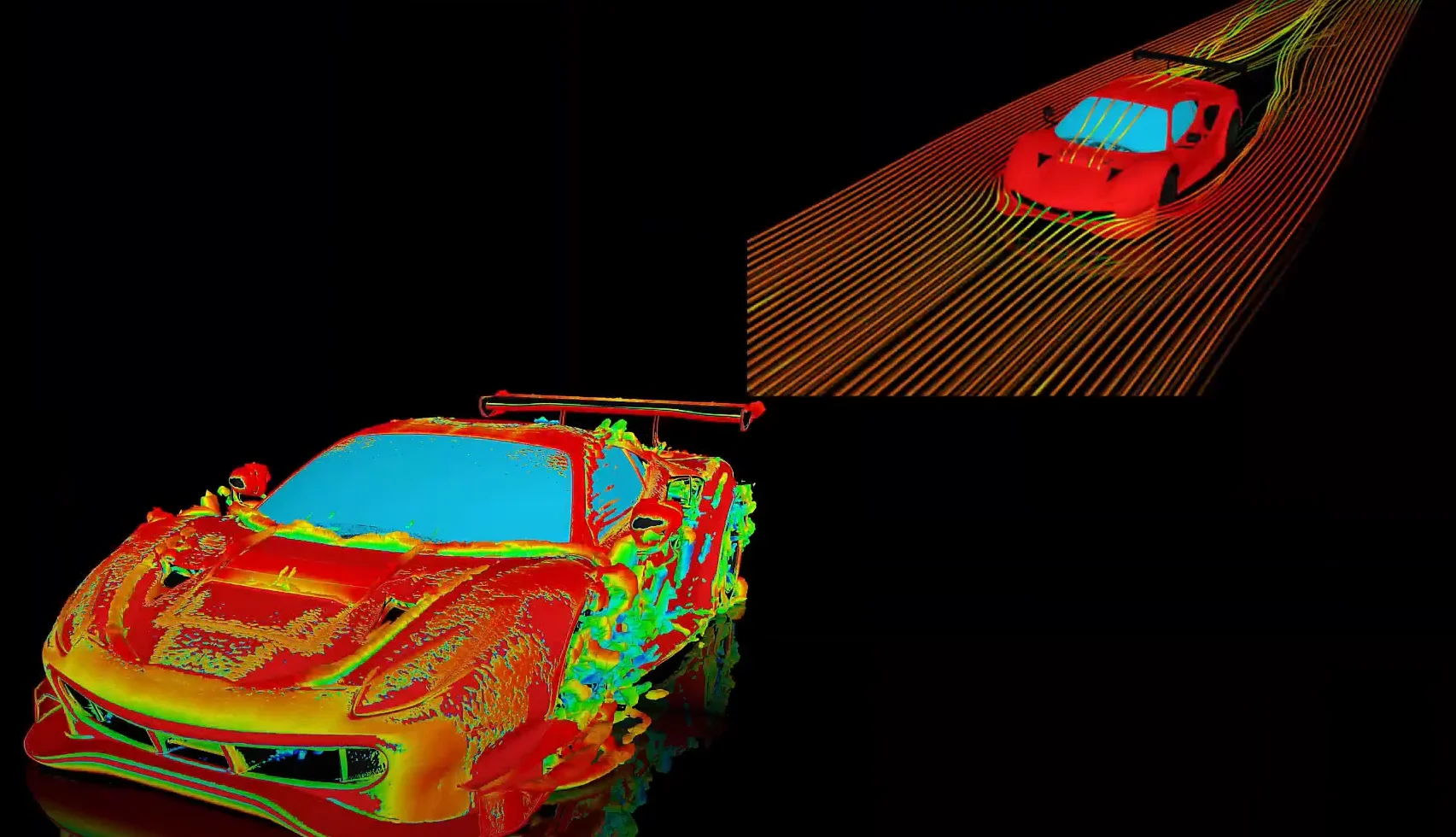
Postprocessing on Ansys EnSight
This video demonstrates exporting data from Fluent in EnSight Case Gold format, and it reviews the basic postprocessing capabilities of EnSight.
- How to overcome the model information incompatible with incoming mesh error?
- Skewness in ANSYS Meshing
- What are the requirements for an axisymmetric analysis?
- Ansys Fluent GPU Solver FAQs
- Is there a way to get the volume of a register using expression ?
- How to create and execute a FLUENT journal file?
- What are pressure-based solver vs. density-based solver in FLUENT?
- What is a .wbpz file and how can I use it?
- How to get information about mesh cell count and cell types in Fluent?
- How can I Export and import boxes / Systems from one Workbench Project to another?
© 2025 Copyright ANSYS, Inc. All rights reserved.