-
-
October 19, 2020 at 5:05 pm
Lucka
SubscriberHi there,
I am a mechanical engineering student. I have already completed the transient structural analysis of a reluctance electric rotor and now I need to optimize its topology but without touch the electromagnetic field optimization. I've added axcess material to the original geometry and i want to lightweight the rotor as much as possible so that i can reach the preset nominal rotational speed and avoid the material yield. That's the reason why I chosed Global Von Mises Stress for Definition of Response Constraint, but i can't obtain any results. I was hoping that the software would have limited the excess material leaving just tiny bridges to sustain the reluctance caves. Can you kindly help me?
I attach some screenshots of what i've done
Thanks
Lucka
October 22, 2020 at 8:29 pmJohn Doyle
Ansys EmployeeWhat happens if you try to minimize compliance as the objective and add a response constraint to minimize the mass and include the max stress limit as a supplemental response constraint? Also, try taking out the maximum amount of mass that you would allow to be removed and rerun the static stress analysis (as a test). nAlso, what is the max stress in the minimum material condition? Perhaps your stress limit needs to be adjusted.nOctober 26, 2020 at 10:50 amLucka
SubscriberThank you for the answer. I did what you suggested and the software works but removes too little material. In the Topology Density solution i can check that it did just 5 iterations (meanwhile the maximum number of iterations in the Analysis Settings is 500). My stress limit should be ok beacause the rotor is structurally oversized (if i return to the static stress analysis after the topo optimization the Safety Factor is bigger then 15). If you need more informations, please don't hesitate to ask.nNovember 17, 2023 at 2:02 pmKalyani Deshmukh
SubscriberHello,
I did a modal analysis of a damper-mass system. Then I did topology optimization for damper design for a natural frequency. I referred this video Topology Optimization of a Bell Crank Using ANSYS Mechanical - Part II - YouTube for tutorial but for natural frequency. I am having problems with the reverse engineering because the two dampers are acting as a body and I can't select a face in the new modal analysis. I am guessing I did something wrong with the optimization region.
Â
This is the topology solution I am getting:
Â
The mass has disappered. I did add a new body in the spaceclaim of the reverse engineering modal analysis. But I'm facing a few problems:
- I can't split the geometry with damper members and body separately. The materials for both of them are different so they have to be separate.
- I can't mesh the damper elements.
- When I apply fixed support to the top face of the dampers, the body gets selected (because of problem 1).Â
I am expecting a result like this -Â
Â
But I am getting a problem with meshing. Can you please also provide a link to a good in depth meshing course? Thanks!
Â
Â
Viewing 3 reply threads- The topic ‘topology optimization problems’ is closed to new replies.
Ansys Innovation SpaceTrending discussionsTop Contributors-
3467
-
1057
-
1051
-
918
-
896
Top Rated Tags© 2025 Copyright ANSYS, Inc. All rights reserved.
Ansys does not support the usage of unauthorized Ansys software. Please visit www.ansys.com to obtain an official distribution.
-

Ansys Assistant
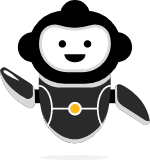
Welcome to Ansys Assistant!
An AI-based virtual assistant for active Ansys Academic Customers. Please login using your university issued email address.

Hey there, you are quite inquisitive! You have hit your hourly question limit. Please retry after '10' minutes. For questions, please reach out to ansyslearn@ansys.com.
RETRY