-
-
January 30, 2021 at 8:11 pm
mkalel
SubscriberHello, I am new to the fluent solver. I am trying to make a simulation of air flowing through the nozzle. My problem is, I am trying to track the particle in the pipe which is attached to the nozzle. Every time i run the simulation, I am getting the zero escaped mass value. I tried to create a file for escape mass.
Monito-Report File -New- create-DPM report- Escaped mass
same thing I did for injected mass
I am getting the zero value when i run the simulation for every parameter like escaped mass, injected mass.
Also how to track the particle in each section of the pipe. I mean if i divided the pipe in suppose 10 section. How can i track the particle in every section?
i have uploaded the pic of my model and some setup i did.
Please help me. I really appreciate your help.
I made one inlet and two outlet. I am not sure if I should make two outlet. The overall process is the incoming fluid (dark blue) region enters the stationary nozzle(green) and hits the long hot tube pipe( sky blue) which is rotating. is my inlet and outlet are in right position ?
February 1, 2021 at 4:32 pmKonstantine Kourbatski
Ansys Employeewell, this is unsteady simulation, so particles (or particle parcels to be more precise) may have not reached out the outlet yet. Display particle tracks and see where they are in the domain.nFebruary 1, 2021 at 6:47 pmFebruary 2, 2021 at 12:44 ammkalel
SubscriberI ran the simulation on steady state. And I realized that the injection particle/injection are not reaching to the other end to the outlet. May be thats why i am getting zero value for escaped mass. So, What should I do, so that the particle can reach to the other end(outlet) with provided velocity and able to track the particle ( no. of trap, no. of escape, no. of injected)? nParticle size- 0.000128 m. nvelocity- 4 rpmnmaterial- ash solidnmass rate- 0.16375 kg/snnot sure about start time and stop time.nShould I run this model on Steady state or Transient state?.nn
February 2, 2021 at 5:34 ammkalel
SubscriberI need to send the particle from the inlet to the outlet and tracked them to find out how much got Trapped and escaped. How Can I do that.? Since they are not reaching to the outlet. So Is there any way, I can able to send the particle further to the outlet and able to track them in the different sections of the pipe?.Thanks,nMukeshnnFebruary 3, 2021 at 11:51 amRob
Forum ModeratorThe question isn't how to send them to the outlet, but why aren't they getting there. What is the flow velocity in the domain? Which way is gravity defined? nFebruary 4, 2021 at 6:02 pmFebruary 5, 2021 at 11:08 amRob
Forum ModeratorPlot the particle tracks, if flow is in the x-direction and gravity is in y do they settle? nFebruary 5, 2021 at 11:28 amFebruary 5, 2021 at 2:13 pmKonstantine Kourbatski
Ansys Employeeis it steady or unsteady tracking you are doing? If you are doing unsteady tracking, then the particles will propagate with time, so you need to run the simulation long enough for particles to along the entire domain. You can estimate this knowing velocity and domain size.nIf you do steady tracking, you can simply increase the number of DPM steps to force the particles to travel throughout the entire domain.nFebruary 5, 2021 at 2:35 pmmkalel
SubscriberI m using the steady tracking . I already increase the DPM steps from 50000 to 100000, still getting the same result. nFebruary 5, 2021 at 3:09 pmKonstantine Kourbatski
Ansys Employeethen the question is what's happening physically in the region where particles terminate. E. g. particles can be trapped indefinitely in a recirculation zone which they never escape. Velocity contours and velocity vectors on the plane cuttings through the domain along the tube would be helpful.nFebruary 6, 2021 at 6:52 amFebruary 8, 2021 at 11:18 amRob
Forum ModeratorI'm not sure I follow. Do you want to slice the domain to track particle position at each plane? nFebruary 8, 2021 at 8:21 pmmkalel
Subscriberyes. I wanna see how many particle every slice of domain trapped .nnFebruary 8, 2021 at 8:43 pmmkalel
SubscriberAlso, for my previous question of incomplete flow.nI ran the steady simulation with 100000 number of DPM steps. I tried to visualize physically what going on inside the region where the particle disappear . For that I did the steady tracing with velocity contour and velocity vector on the plane . The pictures from the results are below. Can somebody tell me what going wrong on the region? why they all are getting trapped in a very short distance after coming out from the nozzle and not reaching to the outlet? nI set the Boundary condition - (trap) on the wall of big cylinder and set the angular rotation of 4 rpm. n
February 10, 2021 at 2:13 pmKonstantine Kourbatski
Ansys Employee2nd picture explains why: see the recirculation zone just past the pipe expansion. This is where particles get trapped and get churned indefinitely. You should analyze and understand why the flow field is what it is. nMarch 7, 2021 at 2:37 ammkalel
SubscriberThank you, Kostya for your helpful comment . nYes, I can see that there is a backflow too but I am still not clear about why the particles are getting trapped in that reason(recirculation zone ). Is there some wrong with the boundary condition on the wall which I had setup a trap and made the wall rotating? Is there something wrong with the meshing? Is there something wrong with the design of the nozzle? Is there any suggestion you guys can help me to overcome this problem?n I will appreciate your helpnMarch 7, 2021 at 3:33 amYasserSelima
Subscribernsome particles get stuck in the vortex and they hit the tube and get trapped. And many of them go past the backflow, but the centrifugal force because of the circulation, pushes them towards the tube and they get trapped as well. nIf you want them to reach the outlet, change the settings to reflect on the large tube.n
March 7, 2021 at 4:11 ammkalel
SubscriberI appreciate your very very helpful comment.nYes, but my project is about showing the better distribution of the particle on that larger tube (31m) after it comes out from the nozzle but I don't want all of them to get trapped in the very first section. If I change the setting of the larger tube wall to reflect, I am afraid of having almost all lot of particles escaping out from the outlet. I was hoping to see a few of the particles escaping from the outlet after it completing the path and having a better distribution of the particle in every divided section of the larger tube.nnMarch 7, 2021 at 4:38 amYasserSelima
SubscriberSo, what you reached is a conclusion ... all the particle got trapped in the first section of the tube which could be returned to the centrifugal force. But you need to confirm this conclusion. Use lower density particles and see if they can go further. nOr, make another injection somewhere after the nozzle, and you should see the particles getting trapped after few meters as well.nnProbably injecting particles that have density very close to the fluid would do what you want. Try! nMarch 7, 2021 at 5:12 ammkalel
SubscriberThis is really helpful. Thank you again for your comment nI definitely want to try the particle with lower density. I will definitely let you know about the results. nSorry I was not clear in the earlier comment. My project is about Optimization of a Nozzle. nThis nozzle design which I was running simulation above is the original design of a company. But they want me optimized it and compare it with the original one.nSo, I have designed an optimized nozzle and run the simulation with the same boundary condition and the used same particle but It runs well with that optimized nozzle( make it to the outlet) but I don't know why the same condition doesn't work with this one. Maybe I am wrong with selecting the particle. I will run the simulation again with different particles.March 7, 2021 at 5:16 amYasserSelima
SubscriberGood Luck, and let us know how did it gonViewing 22 reply threads- The topic ‘problem tracking on inner wall of pipe- DPM (transient phase)’ is closed to new replies.
Ansys Innovation SpaceTrending discussionsTop Contributors-
3472
-
1057
-
1051
-
934
-
902
Top Rated Tags© 2025 Copyright ANSYS, Inc. All rights reserved.
Ansys does not support the usage of unauthorized Ansys software. Please visit www.ansys.com to obtain an official distribution.
-

Ansys Assistant
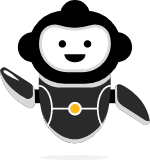
Welcome to Ansys Assistant!
An AI-based virtual assistant for active Ansys Academic Customers. Please login using your university issued email address.

Hey there, you are quite inquisitive! You have hit your hourly question limit. Please retry after '10' minutes. For questions, please reach out to ansyslearn@ansys.com.
RETRY