-
-
August 5, 2020 at 1:08 am
Afrah
SubscriberHi,
I'm running a simple SMART simulation with an edge crack and noticed that the number of substeps used changes the results I get for the SIF. Using a small number of substeps decreased the average SIF along the contour and using a large number increased the average SIF. I thought that the number of substeps had to do with the convergence of the solution so I'm confused as to why its affecting the SIF so much. A follow up question is how I can then choose the number of substeps needed to get accurate results. I would appreciate any suggestions or advice!
FYI, my specimen is 20mmx20mm with a 1 mm thickness and I am applying a stress of 65 MPa to the top surface. There is a fixed support on the bottom surface. My initial, minimum, and maximum number of substeps is 60,40,100.
August 6, 2020 at 3:28 pmDavid Weed
Ansys EmployeeHi Afrah, is this for static or fatigue crack growth?
August 10, 2020 at 4:15 pmAfrah
SubscriberHi David, this is for static crack growth
August 13, 2020 at 3:04 amDavid Weed
Ansys EmployeeHi Afrah First, I'll address the role of the number of substeps or time step size for SMART static crack growth. For static crack growth, the number of substeps should be set by the user such that in two or three substeps, the SIF/Jint threshold value is reached. Once static crack growth begins, the time step values set under "Step Controls for Crack Growth" in the details of the SMART crack object should take over. Furthermore, in order to utilize the SMART step controls, under Analysis Settings you need to set Auto Time Stepping to 'On'. Otherwise, if you explicitly control the number of substeps, the SMART step controls will never be triggered. This in turn will lead to widely different results for let's say 10, 50, or 100 substeps for the same analysis. In general, setting the substep controls for static crack growth differs from fatigue crack growth in that for fatigue crack growth you explicitly set the number of substeps to calculate a given number of delta_a values (and you turn off Auto Time Stepping). One technique that users employ is to first carry out a fracture analysis without SMART (just a regular quasi-static analysis) in order to determine at what pseudo time the critical SIF/Jint value is reached. This will then give them an idea of what size to make the initial time step so that this threshold is reached in just a couple of time steps. Then, you simply use that initial time step value in your actual SMART crack growth analysis while setting Auto Time Stepping to 'On'.
In general, make sure that the mesh is refined enough around the crack area to yield reasonable results. It may help to first perform a mesh convergence study without without SMART. There are some relevant sections on fracture meshing in the Mechanical User's Guide: section Performing a Fracture Analysis -> Fracture Meshing and in section Troubleshooting -> Problem Situations -> Fracture Meshing Problems.
I hope that this helps. If anything can be clarified, please let me know.
August 19, 2020 at 6:56 amAfrah
SubscriberThank you so much David for your answer, that makes a lot of sense! Just to clarify, let's say I've turned off SMART and run multiple simulations and found that KI = KIC when some arbitrary value of stress is applied. In my quasi-static simulation with SMART activated, if I wanted to run my simulation for x number of seconds (during which time my stress is being applied linearly), I would want to make sure that at a time, t = x / (# of initial substeps), the critical stress will be applied within a few substeps ?
Again, thank you so much for your time!
August 20, 2020 at 4:36 pmDavid Weed
Ansys EmployeeHi Afrah If time t is the point at which KIC is reached w/o SMART, then set the time step size to get there in a few delta t's (it may help to think in terms of time steps rather than substeps since you'll be dealing with time, in general; in the Analysis Settings you can define Step Controls by Time rather than Substeps). This should be set independent of the total time of the simulation (which you denoted as 'x'); solely take into account the time 't' where KIC is reached. When you run SMART and KIC is reached within a few time steps, then the SMART time step controls should take over until the final time 'x' of the simulation.
Viewing 5 reply threads- The topic ‘How do the number of substeps affect SIF results using SMART crack growth?’ is closed to new replies.
Ansys Innovation SpaceTrending discussionsTop Contributors-
3367
-
1050
-
1047
-
886
-
837
Top Rated Tags© 2025 Copyright ANSYS, Inc. All rights reserved.
Ansys does not support the usage of unauthorized Ansys software. Please visit www.ansys.com to obtain an official distribution.
-

Ansys Assistant
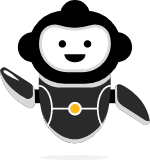
Welcome to Ansys Assistant!
An AI-based virtual assistant for active Ansys Academic Customers. Please login using your university issued email address.

Hey there, you are quite inquisitive! You have hit your hourly question limit. Please retry after '10' minutes. For questions, please reach out to ansyslearn@ansys.com.
RETRY