-
-
December 15, 2020 at 2:08 pm
heloisehml
SubscriberHello,
I put in place a simulation where a 25mm diameter punch must go through a composite plate (10*10mm).
I put the velocity of the punch to 0.0006mm/s and the end time to 60seconds because that is how it goes in real life. The problem is that I don't know why it takes forever to solve. I am new to Ansys so maybe my settings are wrong. I am desperately seeking for help.
the composite sample is on a steel plate that is used for support which has a 32mm diameter hole in its center.
Thank you in advance for your help.
December 15, 2020 at 11:07 pmpeteroznewman
Subscribern1) Configure the CAD so that the punch is touching the sample.n2) Speed up the velocity by 1000 times.n3) Reduce the end time by 1000 times.n4) It looks like your composite material has only 1 element through the thickness. That is unacceptable. You need tens of elements through the thickness.nDecember 16, 2020 at 3:58 amdjtan
SubscriberThis is more like quasi-static simulations since the speed is so low and the time duration is quiet large, explicit will take a long long long time to solve it, ninstead what u can try is to increase the velocity and reduce the time nI've come across this yesterday and it very helpful (sorry i don't know how to insert a hyperlink)nnThis is more like quasi-static simulations since the speed is so low and the time duration is quiet large, explicit will take a long long long time to solve it, ninstead what u can try is to increase the velocity and reduce the time nI've come across this yesterday and it very helpful (sorry i don't know how to insert a hyperlink)nne nDecember 16, 2020 at 1:03 pmheloisehml
Subscriber@heloisehml 1) Configure the CAD so that the punch is touching the sample.2) Speed up the velocity by 1000 times.3) Reduce the end time by 1000 times.4) It looks like your composite material has only 1 element through the thickness. That is unacceptable. You need tens of elements through the thickness./forum/discussion/comment/100471#Comment_100471
But isn't changing the velocity and end time changing the whole simulation thus giving me the wrong results? It is normal the meshing only shows one layer but i did put some (16 of carbon and 1 Honeycomb) - I don't know why it shows one layer.nDecember 17, 2020 at 6:13 pmpeteroznewman
SubscribernRun a series of simulations where you change the velocity and end time by a factor of 100, 1000, 10000, 100000.nPlot the Total Energy and the Kinetic Energy on each simulation.nWhen Kinetic Energy is a very small percentage of the Total Energy, the simulation is very close to quasi-static.nWhen Kinetic Energy is a significant percentage of the Total Energy, then the simulation is no longer quasi-static.nJuly 10, 2023 at 8:36 pmViewing 5 reply threads- The topic ‘Explicit dynamics simulation takes too long to solve’ is closed to new replies.
Ansys Innovation SpaceTrending discussionsTop Contributors-
3407
-
1057
-
1051
-
896
-
887
Top Rated Tags© 2025 Copyright ANSYS, Inc. All rights reserved.
Ansys does not support the usage of unauthorized Ansys software. Please visit www.ansys.com to obtain an official distribution.
-

Ansys Assistant
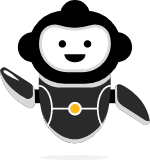
Welcome to Ansys Assistant!
An AI-based virtual assistant for active Ansys Academic Customers. Please login using your university issued email address.

Hey there, you are quite inquisitive! You have hit your hourly question limit. Please retry after '10' minutes. For questions, please reach out to ansyslearn@ansys.com.
RETRY