-
-
January 17, 2021 at 2:21 pm
jvancappellen
SubscriberHi,
I am having some problems with a simulation in where I deform an initial flat plate into a double curved plate. My goal is to validate analytical membrane and bending strain calculations that I did. But without a working simulation this is not possible.
The problem is that my simulation won't converge for the displacements that I apply at the plate. I am using a material model with a stress-strain curve up to 100% strain. The displacements are applied by imposing a constraint on every node into x-y-z direction. These displacements are applied over 10 seconds. And should give the desired shape. However, the simulation does not converge at a certain point.
I am using the arclength method to solve the simulation and large deflection is turned on.
The nodal constraints are applied with an APDL which gives the nodal displacement in every direction, I don't have any other boundary conditions applied. Underneath you can see the mesh that I am using, the dimension of the plate are approx. 4500x500mm with 12mm thickness.
January 18, 2021 at 10:58 amAshish Khemka
Forum ModeratornnCan you please share a snapshot of the error message or the exact error you see?.Regards,nAshish KhemkanJanuary 18, 2021 at 1:20 pmjvancappellen
SubscribernThanks for your reply! The error message that I get is the following:nThe equivalent total strain that I'm seeing is the following:n
While my displacements are imposed linear, see the following figure;n
I think that the displacement that I impose in y-direction is too large. But the material model that I'm using is going up to 150% strain and this isn't reached.. nI just looked into the element moments and these are really large at certain places of the plate, I don't really know why though. See the figure underneath with the elemental moment sum. n
Thanks in advance for your reply! I can also show a visualization of the nodal displacement vectors that I applied if that's helping. nKind regards.n
January 18, 2021 at 6:18 pmAshish Khemka
Forum ModeratornnYou can let your solution proceed further by increasing the number of equilibrium iterations. To do this add a command under the Analysis Settings branch:nnUse the Command Object and add the following command:nnneqit,100By default 25/ 26 iterations are used and using the above command will increase the number of iterations to 100.Regards,nAshish KhemkanJanuary 18, 2021 at 10:36 pmjvancappellen
SubscriberHi ArraynYour suggestion did not help. nHowever, I somehow came to check the element type that I am using. I've never defined to use shell181 elements because I thought that it was the default shell element. The only commands I had used before in the preprocessor were:nnKEYOPT,1,1,0nSECTYPE,1,SHELLnSECDATA,12,,,15nnNow I've added: ET,matid,181nAnd my simulation finally works. Now I am really curious about what is the default shell element? I can't find it anywhere unfortunately, maybe it is somewhere in the files on my PC?. I always thought that the default was shell181 whenever you create a flat geometry with a certain thickness.. Hopefully you can give me answer to this.nKind regards,nJoostViewing 4 reply threads- The topic ‘Double curved plate simulation’ is closed to new replies.
Ansys Innovation SpaceTrending discussionsTop Contributors-
3462
-
1057
-
1051
-
918
-
896
Top Rated Tags© 2025 Copyright ANSYS, Inc. All rights reserved.
Ansys does not support the usage of unauthorized Ansys software. Please visit www.ansys.com to obtain an official distribution.
-

Ansys Assistant
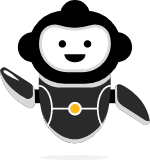
Welcome to Ansys Assistant!
An AI-based virtual assistant for active Ansys Academic Customers. Please login using your university issued email address.

Hey there, you are quite inquisitive! You have hit your hourly question limit. Please retry after '10' minutes. For questions, please reach out to ansyslearn@ansys.com.
RETRY