-
-
April 12, 2022 at 10:02 am
oguzhanb
SubscriberHello,
I want to do a simulation for vibration of the composite beam (I will review for deformation values on determined an axis) by importing/using the temperature values on ANSYS Workbench. It will be a coupled analysis, but I cannot use the SOLID226 elements for strong/direct composite coupled analysis (ACP-Coupled Transient). I can do only Transient Thermal - Transient Structural coupling by SOLID279 and SOLID186 elements. I checked and this result is not satisfy with my theoretical results. If I can use the SOLID226, or I can obtain the direct coupling results, it will be good for me.
If I can do an assumption with quasi-isotropic material assignment, there will be no effect for orientation of the layers and stiffness values. Therefore, I don't want to use this assumption.
Can you give me suggestion about my problem?
Thank you.
April 14, 2022 at 7:47 pmSean Harvey
Ansys Employee
Thanks for your inquiry! So you are correct that the solid226 does not support the layered composite coming from ACP. I know this is unfortunate, but one thing you could do is not use ACP and set it up as follows.. If you were to model the solid composite with n layers of composite, you can specify each layer to have the 9 orthropic constants at the APDL level. It means you would have to use another tool to get the stiffness based on the ply angles. In Mechanical, using the Coupled Field Transient system, you would go to geometry and build a solid model of n solids where the thickness of each solid is the thickness of the layer of the composite. With shared topology the mesh/nodes would be shared.
You assign the orthotropic material properties to the solids in mechanical.
Under geometry use element orientation to set the angle so we capture the proper layer angle.
Since the modeling of the composite is done on solid layer by layer, it will capture the full stiffness terms we are used to in composites A,B,D, E matrices so coupling would be included here and not the smeared representation.
Please let me know your thoughts or if further clarification is necessary.
Regards Sean
April 16, 2022 at 4:33 amoguzhanb
Subscriber
Thank you for your good idea. I was excited when I saw this solution and tried it right away. As you said, I only used element orientation for proper layer angle and assigned to the new oriented coordinate systems for each body. The results look better when compared to my old simulation results , but they are still not exactly the same with my theoretical values. I know there may be many possibilities and situations here but I still wonder why. Is it possible for me to see composite A, B, and D matrices after receiving the simulation results? Thus, it will be possible for me to compare the stiffness matrix, which is the result of the analysis, and the theoretical stiffness matrices.
Regards Oguzhan
April 18, 2022 at 3:48 pmSean Harvey
Ansys Employee
Glad this helped. Unfortunately, we cannot show the ABD matrices from the solution as you request. As a double-check, one can use ACP. If you build a stackup or sublaminate, you can use the analysis tab to report the stiffness and compliance matrices. This would be a double check against your theoretical, but it is not that your model is using these because you are not using this in the workflow. I point this out because if you had a mistake in your theoretical, you could have this 2nd method to check with. If you have a stack up or sub-lamiante, there is the analysis tab, you pick it.
Now one thing that can affect is the aspect ratio, so I am not sure the ratio of thickness to Length and width to make sure you are not too large. So maybe that is one item you can change.
Another item is the integration scheme. On keyoption(6) you can change from full integration to URI. So see if changing this can get you closer.
Please keep in mind that depending on what theoretical basis you are using, the simulation may vary because of the theoretical underlying assumptions such as transverse shear deflections, small strain assumptions, etc. I just wish to point this out because I have worked on several cases with professors trying to match and sometimes it came down to the transverse shear stiffness assumptions.
Please let me know if I can help further.
Regards Sean
-
July 16, 2023 at 7:36 am
Md_Salem
Subscriberhello Sean,
I am trying to attach some piezo solid to a composite c-channel beam, (as shown in the picture), ,as you know, it is not possible to model the beam with ACP as we are doing coupled field analysis. The good thing about my model is that I don't need layers ( I can use just one orthotropic layer), but the difficult thing about the geometry of the c-channel itself. The properties of the composite materials are compatible with the axes of orientation for the web of the beam , but not in the same directions for the flanges, and the worst thing is the chamfered part between the flanges and web. Do you have any idea about how to modulate such a beam in the correct manner?
Â
Â
July 16, 2023 at 12:50 pmpeteroznewman
SubscriberMake two rectagular coordinate systems to define the material axes for the orthotropic material, one for the large face and one for the flanges.
Make two cylindrical coordinate systems to define the material axes for the cylindrical blend faces, where the origin will be at the centerline of each blend.
-
July 17, 2023 at 6:10 pm
Sheref haddad
SubscriberMany thanks, peteroznewman,
I tried to make a local cartesian coordinate system for each face (slice them first), even for the curved surface, and then assemble them in one body .
I compared the results for 1st 20 modes of this concept model and another ACP model for the same material, and the results were identicalÂ
Regards
Â
Viewing 4 reply threads- The topic ‘Composite Thermal induced Vibration Coupled Analysis by ACP’ is closed to new replies.
Ansys Innovation SpaceTrending discussionsTop Contributors-
3792
-
1388
-
1188
-
1095
-
1015
Top Rated Tags© 2025 Copyright ANSYS, Inc. All rights reserved.
Ansys does not support the usage of unauthorized Ansys software. Please visit www.ansys.com to obtain an official distribution.
-

Ansys Assistant
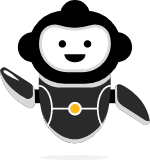
Welcome to Ansys Assistant!
An AI-based virtual assistant for active Ansys Academic Customers. Please login using your university issued email address.

Hey there, you are quite inquisitive! You have hit your hourly question limit. Please retry after '10' minutes. For questions, please reach out to ansyslearn@ansys.com.
RETRY