-
-
February 17, 2021 at 11:06 pm
mcgrat25
SubscriberI am modelling the blockage/sealing of a 'leak' within a water pipe using the insertion of elastomer particles into the pipe, which the find their way to the leak and 'plug' it. To do so, I am employing the macroscopic particle model (MPM), given that I have come across multiple descriptions of it being able to account for the blockage of fluid volume (I've seen images in guides published by Ansys showing its use to simulate the blocking of filter elements). A pressure differential between the inside of the pipe (which is at 2 bar gauge - assigned as a boundary condition to the main/larger pipe outlet) and leak/atmosphere (assigned as 0 bar to the second, smaller outlet) 'attracts' the particle towards the leak. An image of my simulation so far can be seen below, with a 6mm diameter particle being forced into the vicinity of the 5mm circular leak:
February 18, 2021 at 5:07 pmSurya Deb
Ansys EmployeeHello, nYou might want to check the MPM Wall Deposition options. You can set a high value for the Minimum Drag Force for Particle Detachment .nYou can also check the velocity criterion for the wall deposition. Please check the following link.nArrayAnother technique could be to make the coefficient of restitutions for wall collisions very high. This will induce significant loss of energy for the MPM particle once it hits the wall. So a combination of these 2 techniques can ensure that the MPM does not lose contact with the wall thus ensuring a tight seal.nBut, you will need to test this out first. Also make sure that the drag forces are being estimated correctly on the MPM surface. Please have atleast 20 to 30 fluid cells resolving the MPM particle.nI hope this helps.nRegards,nSDnFebruary 18, 2021 at 5:19 pmSurya Deb
Ansys EmployeeJust a small correction, make the coefficient of restitution low and not high for the wall-particle collisions.nMarch 2, 2021 at 5:38 pmmcgrat25
SubscribernTo use the 'particle deposition options' within mpm for this simulation, I want to assign only the 'leak' area of the model wall (the extrusion poking out at the top) as an area where the particle can be deposited. This is because the real world particles only 'deposit' when they are forced to deform into regions under high-pressure differential (such as leaks) - i.e. when hitting the rest of the pipe wall, they would simply 'bounce' off. nIn order to do so, the I method can see would be to create a new 'body' (which forms a singular 'part' alongside the main pipe body) for the leak, with 'deposition' only being set for this area. However, a potential issue I have encountered is the fact that the guide for the MPM model within 'help' for Ansys states that it cannot be used for 'mesh interfaces'. nAs a follow-up question, does a 'mesh interface' refer to any boundary between separate bodies within Ansys within this context, or does it specifically refer to the boundary condition 'mesh interface'? Or is essentially the two - i.e. all boundaries between geometric 'bodies' must have the 'mesh interface BC applied to them. If this is the case, does this mean MPM cannot be used in simulations containing separate bodies?nThanks again for your help.nViewing 3 reply threads- The topic ‘Boundary conditions to simulate volume blockage within the macroscopic particle model (MPM)?’ is closed to new replies.
Ansys Innovation SpaceTrending discussionsTop Contributors-
3427
-
1057
-
1051
-
896
-
892
Top Rated Tags© 2025 Copyright ANSYS, Inc. All rights reserved.
Ansys does not support the usage of unauthorized Ansys software. Please visit www.ansys.com to obtain an official distribution.
-

Ansys Assistant
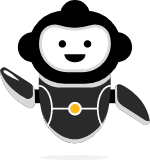
Welcome to Ansys Assistant!
An AI-based virtual assistant for active Ansys Academic Customers. Please login using your university issued email address.

Hey there, you are quite inquisitive! You have hit your hourly question limit. Please retry after '10' minutes. For questions, please reach out to ansyslearn@ansys.com.
RETRY