Ansys Learning Forum › Forums › Discuss Simulation › General Mechanical › How to Activate/Deactivate elements or change model in Ansys Mechanical? › Reply To: How to Activate/Deactivate elements or change model in Ansys Mechanical?
July 15, 2021 at 7:20 am
Subscriber
As described above, I like to model a thermal cycling condition where my PCB will heat -> cooldown -> reheat again. In reality, deformation after three cycles will definitely be different from after just one cycle of heating and cooling. In ANSYS Static Structural, I added the following temperature points to my thermal condition.
However, the deformation after cooling down is the same as when it was heating up.
This led me to look into the ekill and ealive commands which supposedly should deactivate all the elements and reactivate them (reactivated elements should have zero strains) before proceeding to solve the next step. But, I still get the same values for deformation.
What else can I possibly attempt to reach the desired outcome I want to see? Thanks!
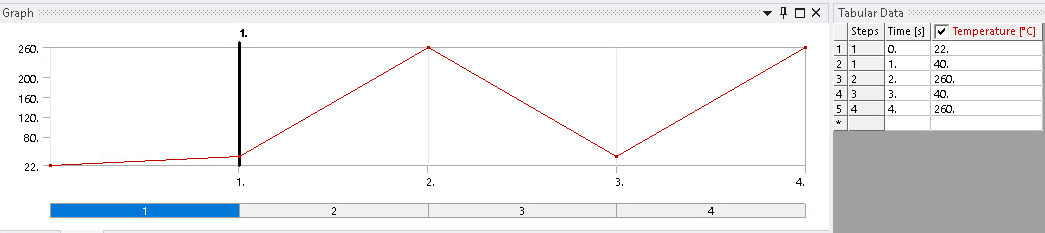
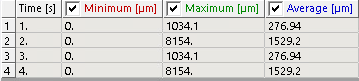
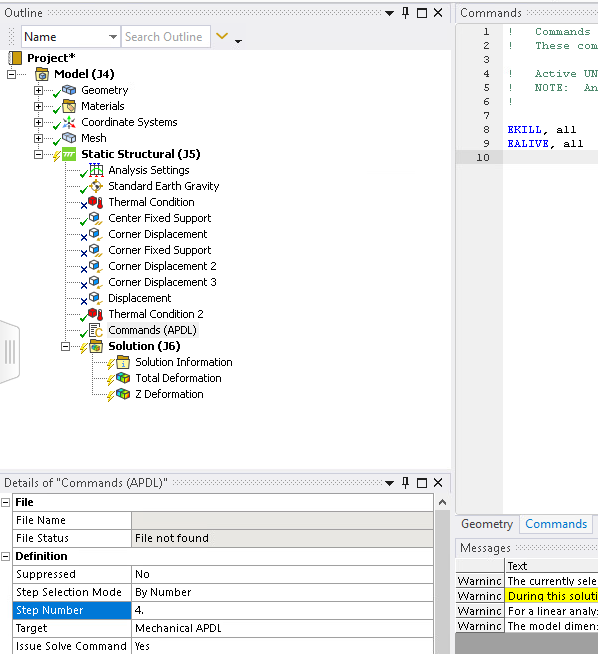