-
-
December 29, 2020 at 4:42 am
Snow1Runner
SubscriberHello,
Recently I've been working on modeling the structural deformation of a set of "laminated glass" that is experiencing a pressure load on one face and should be deforming against a set of standoffs that should prevent this deformation. For simplicity of the discussion, the laminated glass isn't bonded and can slide wrt each other.
I believe my simulation case is very similar to this other post (/forum/discussion/2013/defining-rigid-body-and-contact). In summary, I have followed the same suggestions that Peter gives in this post but I believe that my final results are incorrect. To validate this, I have modeled the deformation without the standoffs. For this case, there is a maximum deflection of around 5.4 mm which is in line of what I would expect for the loading and material properties.
December 29, 2020 at 1:24 pmpeteroznewman
SubscriberArraynI cannot look at your archive, because I don't have an IcePak license installed. If you want me to look at an archive, you must delete all analysis systems except for one Static Structural analysis that shows the problem you describe above. Also, before you create an Archive, delete the Results and delete the Mesh. Your file was 1.4 GB which delayed my response as I waited for that to download before I found the problem above.nYou say Since there is gap of around 1.3 mm from the back of the glass to the standoffs. I would expect the glass to initially deform until it hits the standoffs. and you also say For all of the contacts I have ... and interface treatment to Adjust to Touch. Does that include the contact that has the 1.3 mm gap? Do you understand that using Adjust to Touch eliminates the 1.3 mm gap from the simulation? If you did not understand this, that would explain why you are not seeing the glass deform.n
December 30, 2020 at 10:28 pmSnow1Runner
SubscriberArrayArraynHi Peter, nApologies for the late response. I am not sure why it's requiring an Icepak license since I have no work associated with that. I created a new document from scratch that should prevent this issue from happening and I believe I have deleted all of the files not related to the structural simulation, reducing the file size. My .wbpz file should be below. nWith respect to the Adjust to touch setting, you are indeed correct and I had misunderstood the way this setting behaved. I have changed this setting to Add Offset, no ramping with 0 m offset. These are the results from that simulation. nIt seems like I'm on the right track but I would still expect the glass to contact the standoffs which in this case they are not. nLooking forward to your feedback from my files and please let me know if now you can view them. n
December 31, 2020 at 6:03 pmpeteroznewman
SubscribernI recommend you go back to SpaceClaim and add two planes through the center to slice the geometry down to 1/4 size. That will speed up the meshing and solving time. In Mechanical, you must add the appropriate symmetry Displacement boundary conditions: X = 0 on the faces normal to X and Y = 0 on the faces normal to Y.nIn SpaceClaim, you can also create a New Component, Glass1 that has all the Glass1 pieces in it. Go to the Workbench tab and use the Share button. Repeat for Glass2. Now you don't need any bonded contacts.nRather than Frictionless contact between a body and 96 faces on the glass, make a Named Selection for the 96 faces on the ends of the pins, and a named selection for the 96 faces on the glass, then you can make the Frictionless contact more efficient because it will only mesh the tips of the pins and not the whole rigid body.nAny model that has a Frictionless, Frictional or Rough Contact should add a Contact Tool under the Connections folder and Generate Initial Contact Results to make sure the contact is Near Open.nUnder Analysis Settings, you must turn on Large Deflection.nDecember 31, 2020 at 11:29 pmpeteroznewman
SubscriberI suppressed one layer of glass so that it would mesh and solve faster.nHappy New Year!nJanuary 9, 2021 at 12:16 amSnow1Runner
SubscriberArraynHi Peter, nHappy New Year!nThank you very much for all of your help. I've been running several simulations with your suggestions and files shared and everything has been working successfully. nI've been meaning to run an analysis to see the effect of the standoff height on the total deformation but on SpaceClaim, it seems like I can't modify the standoff height using the Pull function. Do you experience this on your document? nI have re-downloaded the file you shared and I still can't modify the geometry of the standoffs. nRegards! nJanuary 9, 2021 at 5:06 ampeteroznewman
SubscribernThere are two components called Glass1 and Glass2. Glass2 is the Active Component, so only bodies in that component can be edited.nRight Click on Geom at the top and select Activate Component. Now Geom is the Active Component and you can edit the standoffs with the Pull tool.n
Do you know how to use the Selection tool to select all 96 faces with one click?n
Viewing 6 reply threads- The topic ‘Rigid and flexible body interaction’ is closed to new replies.
Ansys Innovation SpaceTrending discussionsTop Contributors-
2979
-
970
-
857
-
755
-
599
Top Rated Tags© 2025 Copyright ANSYS, Inc. All rights reserved.
Ansys does not support the usage of unauthorized Ansys software. Please visit www.ansys.com to obtain an official distribution.
-

Ansys Assistant
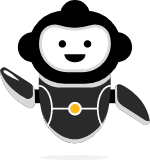
Welcome to Ansys Assistant!
An AI-based virtual assistant for active Ansys Academic Customers. Please login using your university issued email address.

Hey there, you are quite inquisitive! You have hit your hourly question limit. Please retry after '10' minutes. For questions, please reach out to ansyslearn@ansys.com.
RETRY