TAGGED: preprocessing
-
-
October 21, 2020 at 12:06 pm
Rameez_ul_Haq
SubscriberLoad and BC:
October 22, 2020 at 11:23 amAniket
Forum ModeratorAnsys staff can not download files on the student portal, so if you want to reach a larger audience to get answers from, please insert the images inline. (You have done that already)nYes, you should model the plates with gap between them so that those with shell thickness effect will touch each other. Also for high stresses near support try modelling non linear material model.n-AniketnHow to access Ansys help linksnGuidelines for Posting on Ansys Learning ForumnOctober 22, 2020 at 1:43 pmRameez_ul_Haq
SubscriberSo this means every time I have to input a frictionless or frictional contact, I always have to input a gap between them in the geometry? And I should also open the shell thickness effect when working with them, otherwise the frictionless or frictional contact will not work?nI actually donot want to model material non-linearity, I want to know if the stresses near those regions are actually quite higher than in the other parts of the structure, in reality (assuming these stresses donot surpass the yield strength of material), or these stresses are occuring due to constraint equations employed for fixed joint in Ansys solver, and may not actually be present in the reality. Or they are happening because of some other reason? Is that a solver error near the fixed joint, or those will happen in the reality as well?nOctober 22, 2020 at 5:47 pmpeteroznewman
SubscriberInsert a Contact Tool under the Connections folder and Evaluate Initial Contact Status. You should always do this anytime you have frictional or frictionless or rough contact.nIf the contact status shows as Open or Far Open, then the parts will pass through each other.nIf the contact status is Closed or Near Open, then the parts will not pass through each other (but will have a tiny amount of penetration).nOctober 22, 2020 at 7:05 pmAniket
Forum ModeratorTo establish contact, it is not absolutely necessary to have the gap, best way to check it at start is to insert a contact tool (https://ansyshelp.ansys.com/account/Secured?returnurl=/Views/Secured/corp/v201/en/wb_sim/ds_Contact_Tool.html) before solving the model and check status. You can then adjust the offset so that contacts are touching.nIf you are not modelling material nonlinearity, for given increase in the strains beyond elastic limits, stresses will rise a lot, unrealistically. So if your model is bound to show unrealistic stresses in highly strained areas of your model.nnOctober 23, 2020 at 11:23 amRameez_ul_Haq
SubscriberThank you for enlightening me about the contact tool.nAnd I also understand what you are trying to convey about the stresses, but I think you didn't exactly undestand my query. It is about the post processing for the stress near the hole (where deformable fixed joint is attached).nPlease observe the following figure, taken from google for stress concentration near the holes.nnNow, have a look at the stress I am getting near the hole, where deformable fixed joint is attached.nRIGHT PLATE:n
nLEFT PLATE:n
As it vividly appears that there is a difference between the stress distribution and concentration between the two cases. Now I want to actually know that why is there is a difference between them? Is Ansys producing accurate results, or there is some kind of an error which is expected to be seen near the holes since there are some contraint equations involved on the nodes of these holes due to fixed joint. Is it because of bearing stress? (but there is no bearing load applied on the holes). Is the fixed joint causing any bearing load, since only half of the holes are experiencing these high stresses and the other half is not. Are the stresses artificial because of low quality mesh elements near the holes? How can we judge? n[Assume the yield strength of the material is mush greater than the stresses produced in ANSYS near these fixed joint holes on the plates].nI am actually a fresh engineer trying to make judgements on these stresses.n
October 25, 2020 at 3:22 ampeteroznewman
SubscriberTwo thick plates that should be stacked on one another are represented as existing on the same plane in your midsurface model below. This is a significant source of error in the model.nThe improperly configured contact elements do not transfer load at the ends of the plates. This generates an erroneously large moment at the joint, which is another major source of error in the model.n
Fix these errors before you spend any time looking at the stress around the holes.n
October 26, 2020 at 5:22 pmRameez_ul_Haq
SubscriberI re-conducted the analysis for these two geometric environments;nGEOMTERIC CONDITION 1: Distance between the two surfaces is equal to 1 mm (with the thickness of each plate of 2 mm).nnFrictionless contact between them (with no shell thickness effect).n
Results:n
nnGEOMETRIC CONDITION 2: gap between the plates equal to 2 mm.n
nFrictionless contact between them with shell thickness effect 'ON'.n
Results:n
n
nIf we turn on the shell thickness effect, how does it effect my results? Will there be an affect on moment transfer between the two surfaces if shell thickness effect is turned on or off? The only difference I see is this that the target and the contact faces which are given the frictionless contact cannot cross each other, rather with the shell thickness effect on or off, doesn't matter.nSecondly, the contact side of frictionless contact is, in both cases, seen to be highlighted in gray, which says that the status is inactive. What does this mean and why does it happen? Will it affect my solutions?nIn the first geometric condition, the faces are 'NEAR', while for the second geometric condition, the faces are 'SLIDING'. How does the ANSYS decide it is far, near or sliding. How does it make a difference, i mean in the numerical calculations and the results? What does 'Number Contacting' and 'Real Constant' mean?nLastly, as you have already mentioned that if the frictionless contact works, then the forces and moments transfer occuring in the joints will be less. This is proven by the above study and shown in the figures. However, again the highly stressed area for the second geometric condition is on one side of the holes, on both the plates. This confuses me. I want to post process these results to know if it is actually going to happen in the reality or this is just a numerical glitch happening due to constraint equations applied on these holes.nI would be grateful to you if you can also briefly explain why would a big distance between the surfaces which are connected using a fixed joint, can cause a big moment transfer between them? nThank you.nn
October 29, 2020 at 12:01 pmpeteroznewman
SubscribernI like that you ask detailed questions. I don't like it if the post is too long. I will answer questions more quickly if the post is shorter. nGEOMTERIC CONDITION 1: You should have left this out of the post. In some ways, it is more wrong that the original post with the two sheets on the same plane. This is halfway interfering which is still wrong. I have no other comments on this.nGEOMTERIC CONDITION 2: This is the correct spacing, and as you found, contact works with the shell thickness on.nDESIGN DISCUSSION: If I had to design a joint to connect two parts like this with two bolts, I would have a longer overlap and space the bolts along that overlap, not across the width. If I could use four bolts, they would be across the width and along the overlap.nNUTS AND BOLTS: The physical system has a nut and bolt. Torque on the nut and bolt creates tension in the bolt shank, which clamps the two plates together. The clamping forces are orders of magnitude larger than the forces and moments passing through this joint due to the 100 N applied load. Also, there is a washer under the nut and bolt that spreads the clamping force over a large area under the bolt head and nut.nSIMULATION DISCUSSION: Before you build a model, you have to decide what to idealize and how much simplification to do. Those decisions depend on what is important to capture in the results. nIf the area of interest is in some other location far from the joint, then the model only needs to transmit the forces and moments through the joint. Two fixed Joints do this. So would Bonded Contact of the overlap. In this case, don't look at the stress in the joint, because the joint has been idealized to such an extent as to make the stress around the holes to be irrelevant.nIf the area of interest is the nuts/bolts/holes, then don't use fixed Joints in the model. Include the nuts and bolts and use bolt pretension to clamp the overlapped pieces together. The stress pattern in the plates will be very different once the clamping force is included.nBENDING MOMENT DIAGRAM: This is simple to draw for a straight cantilever beam such as you have. The small bend at the end of your model could be left off since the force is perpendicular to the length of the beam. Draw a bending moment diagram for this model. At the point where the hole centers are, calculate the bending moment. That is what the fixed Joints have to transmit and they do so by applying forces and moments to the edges of the holes. Please reply with the bending moment diagram for this cantilevered beam problem.nOctober 29, 2020 at 2:33 pmRameez_ul_Haq
SubscriberThank you answering. You mentioned this statement, ''The stress pattern in the plates will be very different once the clamping force is included''. You mean only in the vicinity of the bolt/nut and pre-tension right? Not in the all of the plates, right? When we apply a pre-tension, is the applied boundary conditions also supposed to resist these pre loads on the bolts? Since you have also pointed out that there are washers, in reality, to spread out the pre applied tension, should we model washers too with the nut and bolt inside ANSYS to analyze the spreading this pre tension, or application of only the pretension inside ANSYS with only nut and bolt is going to be enough? Like if an analysis is desired to check the region of the nut/bolt properly like it will fail or not or how the stresses are distributed in that region.nThe bending moment graph is given below for this problem.nOctober 30, 2020 at 7:40 amRameez_ul_Haq
Subscriber, there is one more thing which baffles me.nSince the extreme left side of the right plate is moving upside, and this has a frictionless contact with the left plate, so this means the right plate is transferring a force (and maybe a moment) to the left plate in the +Z direction. And for the joints, they are transferring the forces and moments in the other direction. How can you say that having a frictionless contact between these two plates will actually decrease the amount of transfer of forces and moments in the fixed joints? nThe region you see, marked in black, below i think will have a local bending moment. nnAt the same time, the region on the left plate which is experiencing the upward force due to frictionless contact, is seen to be overall deforming in -Z direction. What is your opinion on this?
November 4, 2020 at 5:22 pmRameez_ul_Haq
SubscriberArray, waiting for your reply nNovember 17, 2020 at 11:24 amRameez_ul_Haq
Subscriber,still waiting for your thoughts on this one.nNovember 23, 2020 at 2:57 ampeteroznewman
SubscribernBelow is an idealized example to help you think about this problem. It consists of two overlapped sheets, spanning a 100 mm total cantilever length. Instead of a bolt, I have used a spherical joint shown as the vertical red line on the right. The left plate has a fixed support at the left end. The red vertical line on the left can be considered the frictional contact, but is implemented as a joint. There is a 10 mm overhang between the spherical joint on the right and the joint on the left representing contact of the bottom plate to press against the top plate.nI applied a -1 N force in the Y direction at the right end of the plate so the reaction force at the fixed end on the left is +1 N in the Y direction.nBut the forces in the joints are much higher. The tension in the joint on the right is 6 N while the contact force at the tip of the overhang is 5 N.nIf the 10 mm overhang was reduced, the forces would go much higher. Imagine the distance is reduced to the diameter of a bolt head and there is no overhang. Then the forces would get very large indeed.n
Viewing 13 reply threads- The topic ‘Frictionless support not working.’ is closed to new replies.
Ansys Innovation SpaceTrending discussionsTop Contributors-
3139
-
1007
-
918
-
858
-
792
Top Rated Tags© 2025 Copyright ANSYS, Inc. All rights reserved.
Ansys does not support the usage of unauthorized Ansys software. Please visit www.ansys.com to obtain an official distribution.
-
The Ansys Learning Forum is a public forum. You are prohibited from providing (i) information that is confidential to You, your employer, or any third party, (ii) Personal Data or individually identifiable health information, (iii) any information that is U.S. Government Classified, Controlled Unclassified Information, International Traffic in Arms Regulators (ITAR) or Export Administration Regulators (EAR) controlled or otherwise have been determined by the United States Government or by a foreign government to require protection against unauthorized disclosure for reasons of national security, or (iv) topics or information restricted by the People's Republic of China data protection and privacy laws.
Please Login to Report Topic
Please Login to Share Feed
Edit Discussion
The Ansys Learning Forum is a public forum. You are prohibited from providing (i) information that is confidential to You, your employer, or any third party, (ii) Personal Data or individually identifiable health information, (iii) any information that is U.S. Government Classified, Controlled Unclassified Information, International Traffic in Arms Regulators (ITAR) or Export Administration Regulators (EAR) controlled or otherwise have been determined by the United States Government or by a foreign government to require protection against unauthorized disclosure for reasons of national security, or (iv) topics or information restricted by the People's Republic of China data protection and privacy laws.

Ansys Assistant
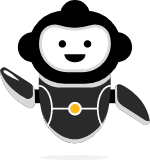
Welcome to Ansys Assistant!
An AI-based virtual assistant for active Ansys Academic Customers. Please login using your university issued email address.
Ansys Commercial Customers: Go to AnsysGPT
Your chat history is not stored
Hey there, you are quite inquisitive! You have hit your hourly question limit. Please retry after '10' minutes. For questions, please reach out to ansyslearn@ansys.com.
RETRY