Ansys Learning Forum › Forums › Discuss Simulation › General Mechanical › Creating Variable Thickness Core in Ansys ACP › Reply To: Creating Variable Thickness Core in Ansys ACP
July 21, 2021 at 7:11 pm
Ansys Employee
Hello @dtomas´╗┐
Here are some ideas to explore.I would still stick with two halves and then they can be bonded contact in Mechanical.
Set the thickness of the core to be larger, then use aGeometry Cut-off Selection Rule at the middle section (mid plane) to trim.If you were to extrude from the OML inward, the mesh may overlap using a solid model, but you can try with shells to see if you can get the core thickness as desired.Also see the cut off geometry in the solid model to cut the extruded elements.
You can also follow procedure 4.4. Analysis of a Mapped Composite Solid Model in the ACP Help where an existing mesh is used. The layup is then mapped and in this case your layup core material.This is a newer technique which works well when we have trouble extruding the shells to create the desired solids models.
You can also mesh the skin in ACP, mesh the core as a stand alone via the Mechanical Model, then use model assembly as shown below and bonded contact to glue the skin to the core.The disadvantage here is that you won't be able to post-precess the core in ACP, but this is not a big deal since you have likely an isotropic foam, and you can use the scalar failure theories of Von Mises, Max Shear, Max Principal, etc.You don't need the more complex orthotopic failure theories of ACP.This method is the easiest of the 3 to try. Also, you don't need to split the wing top/bottom since you will just model the core as is, not split.
Hope this helps, please provide some feedback. Thank you!
Regards Sean
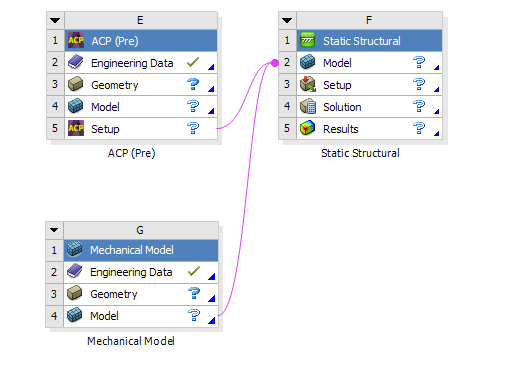
Set the thickness of the core to be larger, then use aGeometry Cut-off Selection Rule at the middle section (mid plane) to trim.If you were to extrude from the OML inward, the mesh may overlap using a solid model, but you can try with shells to see if you can get the core thickness as desired.Also see the cut off geometry in the solid model to cut the extruded elements.
You can also follow procedure 4.4. Analysis of a Mapped Composite Solid Model in the ACP Help where an existing mesh is used. The layup is then mapped and in this case your layup core material.This is a newer technique which works well when we have trouble extruding the shells to create the desired solids models.
You can also mesh the skin in ACP, mesh the core as a stand alone via the Mechanical Model, then use model assembly as shown below and bonded contact to glue the skin to the core.The disadvantage here is that you won't be able to post-precess the core in ACP, but this is not a big deal since you have likely an isotropic foam, and you can use the scalar failure theories of Von Mises, Max Shear, Max Principal, etc.You don't need the more complex orthotopic failure theories of ACP.This method is the easiest of the 3 to try. Also, you don't need to split the wing top/bottom since you will just model the core as is, not split.
Hope this helps, please provide some feedback. Thank you!
Regards Sean
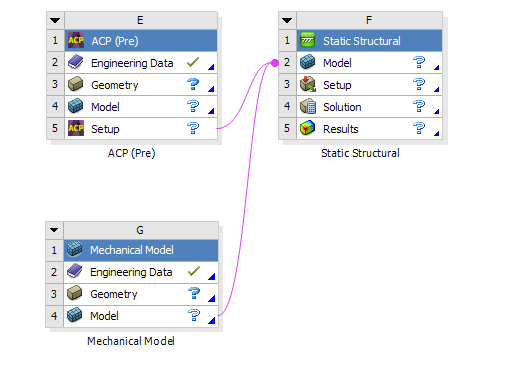