-
-
April 22, 2022 at 8:35 am
TE_Haf
SubscriberHi,
I am simulating a steady multiphase flow case, consisting of air and sawdust particles, using the ganular mixture model, but the simulation rapidly diverges after approx. 100 iterations.
My Setup: The density ratio is rho_p/rho_f=700, with d_p=1E-6 m and a volume fraction of 10% at the inlet. I am using the Syamlal Obrien Model for the granular viscosity. All other settings are kept the same.
I am using the coupled solver with Presto, QUICK and second-order discretizations, when available. For turbulence I am using the k-omega SST model. I tried it with coupled or SIMPLEC, but for both cases it diverged.
The geometry is the air surrounding a disc (the saw with 150 mm), a curved housing and a suction tube with diameter D=75 mm. The boundary condition on the surface of the disc is defined as velocity inlet, using a velocity profile obtained from a simulation with the real saw geometry. For simplicity, it can be assumed as the tangential velocity of the saw (40 m/s) and a lower radial component of about 10 m/s. The second phase enters the domain through the curved surface of the disc with a thickness of 10 mm, and leaves the domain through the suction tube, where a pressure oulet condition with -700 Pa results in a mean velocity of 20 m/s. The surrounding was set as a pressure inlet with P=0 Pa. Gravity is active in -y direction.
The mesh is refined around the disc, with an element size of 0.4 mm and gets coarser as it gets away from the disc (3 mm). I am using a tetahedral mesh, without prism layers.
The residues stay at a stable level (around 1E-2 to 1E-3) up to approx. 100 iterations where the residue of k and omega just jump to 1E0, 1E4 and up to 1E71, as in the figure:
April 25, 2022 at 3:22 pmRob
Forum ModeratorDepending on the initial condition you may find the model is transient. k-e tends to be more forgiving, but I don't expect k-w to cause any issues.
April 27, 2022 at 7:46 amTE_Haf
SubscriberSo, it must be caused by the mesh, I guess.
Are there any guidelines for the mesh when working with the granular model?
April 27, 2022 at 10:49 amRob
Forum ModeratorOther than it needing to be good quality? Make sure you resolve the flow features and avoid high aspect ratio cells: you may find the phase volume fraction varies along a boundary layer so the "classic" inflation mesh isn't always a good idea.
However, if you're adding sawdust into the mix, why does it leave the domain as opposed to filling it up?
April 28, 2022 at 10:28 amTE_Haf
SubscriberThe Idea behind the simulation is to improve the collection of sawdust by the vacuum cleaner attached to the housing by changing slight changes of the geometry. Ideally, all dust is collected by the vacuum cleaner (pressure outlet with negative pressure)
Checking the simulation as it diverges I see a large fraction of the granular phase on the surface of the disc, much higher than the value that I setted as input (10%). I guess it cannot leave this zone fast enough and agglomerates. Once it reaches higher volume fractions (>63%) the turbulent model cannot deal with it anymore and k just skyrockets and the simulation diverges.
April 28, 2022 at 2:01 pmRob
Forum ModeratorIt's not the turbulence model. When you hit the packing limit the material separates VERY rapidly which tends to cause the solver to fail. So focus on why the saw dust isn't clearing the blade, and check the boundary condition is physically sensible.
April 29, 2022 at 8:24 amTE_Haf
SubscriberI tried to simplify the problem to see if I find what is causing the problem. My mesh is too large (56 Million cells), so that even making changes takes a lot of time.
Instead of my geometry I tried the Tutorial "Chapter 22: Using the Mixture and Eulerian Multiphase Models", which uses a 2D mesh for a tee junction.
It works if I have air bubbles in water, but it also diverges if I have water droplets in air.
I only changed the materials. Boundary conditions were kept the same.
Not sure what the problem could be:
Upward flow
Density ratio
Boundary condition for the water phase
Is there a tutorial for the Eulerian or the Mixture models, where the second phase is heavier than the first phase?
April 29, 2022 at 4:40 pmRob
Forum ModeratorMay 2, 2022 at 8:54 amTE_Haf
SubscriberThanks, I haven't tried that one before.
Unfortunately, it is for a transient laminar case with a patched second phase.
If, instead of the initial distribution of the second phase, I introduce the second phase through the inlet and calculate it as a steady case it also diverges. (I did not use the UDF, because I was not interested in the temperature distribution, only the flow)
What is interesting is that the continuity residue continuously increases.
Checking the phase distribution prior to the floating point exception shows that in some regions it reaches the packing limit (although it was started with a volume fraction of only 0.02). It seems the second phase will not leave the pipe fast enough, although it has some inertia. It works if I decrease the density ratio to 10, for example.
May 3, 2022 at 11:22 amRob
Forum ModeratorAnd as the solid packs it'll block the pipe; or as the pipe blocks the powder packs. That points to there not being enough suction on the system, so what's the next step in the design work? If decreasing the solid density works, what does that suggest about the flow?
May 4, 2022 at 7:53 amTE_Haf
SubscriberIt also works if I reduce the volume fraction at the inlet if I also decrease the under-relaxation coefficients as in the tutorial and use the phase coupled SIMPLE model (continuity residues are high, though).
In summary, if the second phase accumulates in the domain the simulation diverges. A transient simulation only would take longer to reach this condition.
The accumulation is probably caused by a weak flow or reciculation zones. The weak flow can be dealt with increasing the velocity of the phases at the inlet, the pressure at the outlet or decresing the velocity deceleration of the second phase (e.g., decreasing the density, since it flows against gravity).
The recirculation zones suggest problems with the design, but the accumulation of dust was not observed in experiments, the problematic particles are the large ones, which are not present in this simulation and will be dealt with the DPM.
This means, the current setup is too simplified to account for all the transport mechanisms, which would actually carry the second phase before it could accumulate, such as the transient periodicity of the flow due to the rotation of the saw, the translation of the wood plank or even the shape of the dust particles.
May 4, 2022 at 8:56 amRob
Forum ModeratorPretty much. The slight error is that the build up in reality might then blow out as a plug or pulse, in the model you may not see this as the system packs and pressurises it then diverges. Don't combine DPM and Eulerian, the parcels won't see the granular phase and DDPM has a few issues as you reach (and exceed) the packing limit.
Looking at the sawdust, in the experiment is it sticky? How did you translate the dust diameter into Fluent? Ie did you take the wood density & dust particle size or something else? Are the sawdust particles "solid" or "fluffy"? Lots of things to consider. Multiphase as a modelling tool is "simple", but the physics you need to think about aren't: I cover this area for the commercial side of Ansys.
May 4, 2022 at 10:48 amTE_Haf
SubscriberThank you for the tip. My goal is to verify if the dust portion of the particles will affect the velocity of the larger particles. Good to know that it might not work the way I planned.
I guess I could use Einstein's equation to extrapolate a new viscosity for a single-phase fluid and use that for some tests with the DPM.
Based on the observation of larger particles on a microscope I would them hairy, not sticky. The thin hairs/fibers will create some clusters, but these clusters are not very stable and break apart very easily. But, yes, they clump (see image below)
The diameter I used in the simulation was 30 micrometers and is based on 2D projections of the particles, obtained using the QICPIC system (laser-based system) from Sympatec. The resolution of the system is 11 micrometers. It works well for a wide range of sizes, just not the dust particles. There are some publications about sanding, where particle sizes of 2 micrometers were measured (see figure below). The process here is different, and we have a lot of particles in the 100 to 200 micrometers range. Partiles with diameters below 150 micrometers are already considered dust.
Source: https://pubmed.ncbi.nlm.nih.gov/27725491/
As density I use 700 kg/m┬│, close to the density of the particle boards we are using. At 30 micrometers particles are mostly round (at least at the used resolution, with 3 pixels per diameter), it is difficult to say if they are solid or fluffy, but I would guess, based on microscope images of larger particles, that they are kind of fluffy. In the end, the value used in the simulations might be higher than the real density of the particles.
May 4, 2022 at 11:27 amRob
Forum ModeratorAnd "hairy" particles will also have a much higher drag due to the greater surface area. You need to be very careful with material density, diameter and aerodynamic diameter. A ping pong (or tennis) ball is a very good example of what you need to account for.
A viscosity model may work, but be aware that where the dust phase is moving you may not want to slow the larger particles too much. It's complicated, and beyond what I'm permitted to cover on here.
Viewing 13 reply threads- The topic ‘Solid-Gas granular mixture rapidly diverging after 100 iterations’ is closed to new replies.
Ansys Innovation SpaceTrending discussionsTop Contributors-
3477
-
1057
-
1051
-
940
-
902
Top Rated Tags© 2025 Copyright ANSYS, Inc. All rights reserved.
Ansys does not support the usage of unauthorized Ansys software. Please visit www.ansys.com to obtain an official distribution.
-

Ansys Assistant
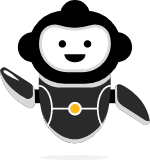
Welcome to Ansys Assistant!
An AI-based virtual assistant for active Ansys Academic Customers. Please login using your university issued email address.

Hey there, you are quite inquisitive! You have hit your hourly question limit. Please retry after '10' minutes. For questions, please reach out to ansyslearn@ansys.com.
RETRY