-
-
October 22, 2021 at 7:31 pm
ssagar
SubscriberI am running a tensile test at a strain rate of 0.00001 s-1. It is very slow. I am modeling a tensile test with SPH Form 12 in LS-DYNA which works out to a speed of 0.00001 s-1 x 12 mm (gage length). Now this is very slow and it is taking ages to run...like 967 days, 3 hrs and 34 minutes and 32 seconds!!
Can anyone assist with decreasing this time to a reasonable timeframe. I am using a High Performance Computer (HPC) system and they set my termination time for 4 days so I have a time constraint.
My experience is that for FEA, it is comfortable to mass scale without changing the accuracy by much, as long as the KE is less than 10% of the Total Energy. However, given the Kernel Function used in SPH has relation to the mass of particles for momentum and continuity requirements, I am almost certain that the answer will be altered significantly, but I can be wrong.
Please advise anyone,
Thanks
SS
October 25, 2021 at 1:53 pmRam Gopisetti
Ansys Employeedo you know Form 12 of SPH works only with the MPP runs ( MSMPI , Intel MPI, PMPI)? and said to have significant computational cost in solving the model.
What is your end time of your tensile test ?
you can use form 7,8 as an alternative to avoid tensile instability (for solids like materials).
Cheers, Ram
October 25, 2021 at 3:07 pmssagar
SubscriberThank you Ram Yes, I am running Double Precision MPP Version. Thanks, I realized it has significant computational cost.
I just want the specimen to be displaced in the x direction by 12 mm so end time = Distance/Velocity = 12/ (12x.00001) = 100,000 s. This is using a strain rate of 0.00001 s-1 and gage length of 12 mm.
I tried Form 8 as well, the Total Lagrangian but same long time to solve.
Do you know how to reduce the run time?
FEA: Mass Scaling but not sure for SPH as computation takes mass of particles into consideration.
Pulling metal: Inconel 718
Thanks Sugrim
October 29, 2021 at 6:08 pmJim Day
Ansys EmployeeThere is no reason to run it for 100,000 s. You can still get quasi-static response, if that's what you're seeking, at a much faster loading rate. It's common practice to "time scale" in this manner to get a shorter run time.
October 31, 2021 at 5:06 pmssagar
SubscriberThank you jday, interestingly, though, MAT_107 does not converge at the faster loading rate. I already tried using a faster loading rate, however my study involves using SPH (form 8 and 12) to determine the effect of strain rate on the stress vs strain curve of Inconel, and using a reference strain rate, epsilon dot zero of .001 ms-1 (as per my experimental). Any time I increase the strain rate beyond 0.001 s-1, the plasticity algorithm in MAT_107 collapses the curve as soon as the material reaches yield.
Mat_107 is used as my specimens also have different initial temperatures.
A screenshot has been added for clarity.
Apart from the material model failing at faster loading rate, the metal I am simulating is affected by the strain rate.
Any advise on what else can be done to reduce the run time.
Thanks
SS
November 1, 2021 at 5:36 pmJim Day
Ansys Employee100,000 seconds = 28 hours. I don't think you mentioned the explicit time step size, but forget about running for 100,000 seconds as a means of circumventing the warnings as that would likely entail running billions of time steps. If your material misbehaves when using a reasonable loading rate (run duration of no more than 1 to 10 seconds, for instance), the trouble is almost assuredly bad input. Check and recheck your units. All your input must use a consistent unit system.
Also, run a double precision executable of LS-DYNA and use a recently released version and not one that is several years old.
If you get stuck, create a one-element model using your mat 107 input and run some trials. That may cast some light on things.
November 17, 2021 at 7:37 pmssagar
SubscriberThank you jday. I ran the tensile tests for 10 s-1 and 100 s-1 strain rates and got very good results. However, as I indicated, its taking long to complete 1 s-1. using a gage length of 12 mm, this works out to 12 mm/s speed. Changing this to consistent units, the input in LS-DYNA is 12/1000 mm/ms. If I want to move 12 mm on x direction, I will have to give a time of 1000 ms or 1 s. Now, I changed to Form 8 now so its not as computationally demanding as Form 12. But its still taking very long. Also, at the point of the ultimate tensile strength, it is giving an error that the velocities are too high (some form of instability) when using a timestep factor of 0.6 to 0.9.
If I lower the timestep factor, to lets say 0.1, it will take 1139 hours to run!!!. I dont have that much time.
Can you kindly assist.
Also, the target is to simulate 0.001 s-1. But the simulation time in explicit analysis is way too long. How to get over this? Time scaling will affect the stress/strain curve for most metals as these depend on the strain rate.
Thanks Sugrim
November 17, 2021 at 11:00 pmJim Day
Ansys EmployeeWhy do you think you need SPH to run your simulation? Why not use regular Lagrangian elements and run an implicit analysis?
November 29, 2021 at 5:11 pmssagar
Subscriberjday My supervisor wants 2 particle-based numerical models to be built for validation. I read on a paper that time scaling can be used for SPH, that does not adversely affect the results. The paper is cited as "Villumsen, M. F., & Fauerholdt, T. G. (2008). Simulation of metal cutting using smooth particle hydrodynamics.LS-DYNA Anwenderforum, C-III,17." in Google Scholar. What I was not sure about was how did the authors perform the time scaling. It seems from pg 18, that time scaling is quite feasible that resulted in an order of 30x time reduction.
Is it possible to indicate how the authors performed the time scaling on their SPH model?
Thank you again Sugrim
November 29, 2021 at 6:48 pmJim Day
Ansys EmployeeI suggested time-scaling in my reply on October 29. Time-scaling, as I know the term, entails loading the model at a faster rate and therefore completing the analysis in less time. This appears to be the approach used by the authors of the paper.
December 23, 2021 at 8:06 pmssagar
SubscriberThank you jday My professor is not too happy with increasing the loading rate as this affects the stress/strain curve. Would have been more scientific if something like mass scaling in FEA was made useful for reducing analysis time. For now, I simulated as low as 1 s-1 strain rate and some errors begin to pop up. Is it the accumulation of errors that may cause some kind of non convergence running long analysis?
I am not sure if I can publish a paper saying that I increased the rate of loading to reduce the wall time without being asked, so does the loading rate affect the mechanical properties of the metal.
Please let me know your thoughts.
Thanks S.S.
October 18, 2023 at 5:59 amamit kumar
Subscriberbro have you solved this problam of low strain rate taking long time to run simulation . if you solved so please tell me i am also facing same problam.
Viewing 11 reply threads- The topic ‘How to decrease the run time for an SPH analysis in LS-DYNA.’ is closed to new replies.
Ansys Innovation SpaceTrending discussionsTop Contributors-
3792
-
1388
-
1188
-
1090
-
1015
Top Rated Tags© 2025 Copyright ANSYS, Inc. All rights reserved.
Ansys does not support the usage of unauthorized Ansys software. Please visit www.ansys.com to obtain an official distribution.
-

Ansys Assistant
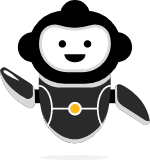
Welcome to Ansys Assistant!
An AI-based virtual assistant for active Ansys Academic Customers. Please login using your university issued email address.

Hey there, you are quite inquisitive! You have hit your hourly question limit. Please retry after '10' minutes. For questions, please reach out to ansyslearn@ansys.com.
RETRY