-
-
June 28, 2021 at 11:08 am
Rameez_ul_Haq
SubscriberI am having this problem which conducting a non-linear static structural analysis. The solution is not converging and this problem (as mentioned in the question's title) keeps on occurring. I don't know if that is an error or a warning. Should I be concerned about this message in the solver output file? How to solve it?
June 28, 2021 at 1:14 pmEmperor
Subscriber
I often had this problem in my contact analysis. Most of the time it was a contact that became very degenerate. If it does not converge you can display the Raphson newton residuals and see where you have a problem. Once the contact is detected, you can then correct it in several ways: change the contact stiffness; change the contact detection to nodal to target (by default it is set to gauss points), increase the mesh density on your contact area.
I also learned that in a good nonlinear static calculation you should always check the penetration, this one must be small in front of the dimensions of the structure.
( I am still a trainee on the ANSYS tool and I am still developing my skills to debug the errors, surely someone more experienced will have a better answer)
Hoping this helps you
Best regards
June 28, 2021 at 1:44 pmRameez_ul_Haq
Subscriberthank you for your reply.
I still don't know if that is an error or that is a warning. So what I understood from your comment is that the NR-Residuals should be high in the region where the contact elements has very high penetration. If this is the case, then we can be sure that the analysis is not converging because of that high penetration within those contact elements. Let me know if I understood you correctly or not.
Still but I am unaware that why should the high penetration in the contact region initially (or even when the solver is running) could be a problem. What is the link between penetration and solver not converging?
,if you could enlighten us with your views on this one, that would be extremely helpful.
June 28, 2021 at 2:23 pmEmperor
Subscriberthe penetration can be high without the Newton-Raphson residuals being displayed because they are only displayed in the case where the calculation does not converge. In the case where a penetration problem (contact) causes the calculation not to converge, the Newton-Raphson residuals will be displayed. A calculation can converge with a high penetration depending on the size of your structure. You are free to validate the converged calculation with the displayed penetration rate.
If it is only a warning, in my opinion you can ignore it, but if it is an error the residuals will guide you.
I have worked on a model where the penetration is high at the beginning (it is common on models with joints) the warning message is displayed at the beginning but it is not an error. It is just a step to consider for the resolution of the penetration.
Always check the penetration at the end of the converged calculation and make sure that it is not too large for the size of your structure.
June 28, 2021 at 7:59 pmRameez_ul_Haq
Subscriber,I am still unsure why should the solution might not converge within some contact elements if the penetration is too high. What is the criteria which decides if the penetration is too high or not for the solution to converge in that region. Is there a way to alter that criteria to obtain convergence in that contact region. Why should we always check if the penetration at the end of converged solution is too large relative to the size of the structure if the solution has already converged.
,help from you (in terms of concepts) would extremely appreciated as well :)
June 28, 2021 at 11:12 pmpeteroznewman
SubscriberIf you request NR Residual Force plots they are stored in N files (where N is the number typed into the NR Residual Plots line) that you can view anytime you pause the solution or when the solution terminates by failing to converge or reaching the end time. If the solution converged to the end, you generally don't spend any time looking at the NR Residual Force plots.
Contact has a penetration convergence tolerance. If there is too much penetration, the solver will continue to iterate until the penetration tolerance is met. If the penetration tolerance is not met, and the solver has run out of allowable iterations, then the solution has failed to converge. There are at least three approaches to correct this failure.
1) You can relax the convergence tolerance and accept a larger penetration.
2) You can increase the stiffness of the contact, which will drive the penetration to lower values.
3) You can allow more iterations.
This is very general advice and there are many other considerations and approaches that can help get the solution to an acceptable end time.
June 29, 2021 at 7:50 amRameez_ul_Haq
Subscriberthank you clearing things out here.
How can we increase the number of allowed iterations specifically for the contact penetration convergence tolerance, so that it is met?
And how can we be sure that the convergence is not happening because the contact penetration convergence tolerance is not met? Should the NR-Residuals in that contact region should be an indication that it is not met? Or are there any other indications as well to tell us in which regions is the contact penetration causing a convergence problem?
What if I completely remove the criteria for contact penetration convergence tolerance? Should that be an issue in terms of accuracy of the results? Is there a way to completely get rid of it?
June 29, 2021 at 5:06 pmpeteroznewman
SubscriberYou increase the number of allowed iterations by using the APDL command NEQIT,100 to allow 100 iterations.
You know that contact penetration tolerance is not being met because of the warnings in the solution output like the title of this post.
You can relax the contact penetration convergence by typing in a value of allowable penetration tolerance.
June 30, 2021 at 7:51 amRameez_ul_Haq
Subscriber,What about increasing the normal stiffness? I read in a document somewhere for ANSYS that increasing the normal stiffness might make the global stiffness matrix ill-conditioned and hence might cause convergence difficulties (but at the same time decrease the penetration). On the other hand, decreasing the normal stiffness can make it easier for the global stiffness matrix and for convergence, but the results might not be as accurate then.
But you said that increasing the normal stiffness in a contact can actually solve the convergence problem because it decreases the penetration. It is somewhat opposite of what the document writes. Can you please elaborate this as well, I would be glad :)
[Willing to share the source for the document, if needed].
June 30, 2021 at 10:30 ampeteroznewman
Subscriber#2 above said increasing stiffness can reduce penetration, which was the area of concern. You have also read elsewhere that too high a value of stiffness can cause convergence problems. That is why there is option #1 and option #3 to help convergence. There are also many other parameters and changes in the mesh to help convergence. The proper action depends on the specific model and your requirements. In some models, I have reduced stiffness to help convergence, but I was willing to accept more penetration. In other models I have increased stiffness to improve accuracy because the default penetration tolerance was too large. Then there were models that had convergence problems with contact where I didn't change the normal stiffness at all, but used a better mesh or some of the other parameters.
June 30, 2021 at 10:45 amRameez_ul_Haq
Subscriber,ohh okay, understood. Thank you sir for helping us :)
June 30, 2021 at 11:23 amRameez_ul_Haq
Subscriber,just one more thing. For example I am not concerned about the contact stresses occurring on the contact faces between two bodies, then increasing the convergence tolerance or decreasing the contact normal stiffness (where both the options will have a larger penetration), so still that would be a problem? I mean where can the results become kind of ''less accurate'' by applying these two measures? I mean the force transfer happening between the two bodies still won't change right? So by applying the St. Venant's principle, I can easily depend on the results far away from the contact and they will still be ''accurate'', right?
Plus, what is the program controlled default value for the penetration tolerance?
June 30, 2021 at 11:43 ampeteroznewman
SubscriberIf the penetration you see is acceptable and this contact patch is not in an area of concern for stress or positional accuracy, then it is fine to allow higher penetration to fix a convergence problem. The example where the penetration tolerance was too large was an interference fit problem: a post in a hole that is smaller in diameter than the post. There are textbook equations to predict the stress of that geometry. The default normal stiffness may leave too much penetration and result in a few percent error in the value of stress compared with the theoretical result. The solution is either to reduce the penetration tolerance to a specific value or increase the normal stiffness. I expect that under-the-hood, the solver is simply increasing the normal stiffness and checking if the penetration tolerance is met.
St. Venant's principle is useful for stress, but it is not useful for rigid body rotations. Say you have a 2 m long beam that has a hinge on one end and a rotation stop that is only 0.02 m away. That rotation stop is a frictional contact, but because the motion of the tip of the beam is 100 times greater than the motion of the contact point with the rotation stop, a small penetration at the stop is magnified by a factor of 100 at the tip. Since the penetration is not real, but an artifact of the solution, it is important in that model (like the interference fit) to ensure that the penetration is very small. Yes, that will cause extra iterations to occur to reach this small value, but that is necessary in this example. In other cases, the penetration may not matter.
I don't know what the program controlled default value is for penetration tolerance, but it's not going to be a fixed value, because that wouldn't work when the geometry the solver is given can be measured in meters or microns. It is likely a value computed from the local stiffness. Just like in the Normal Stiffness, you can enter a Factor to increase or decrease the automatically computed value, or you can enter a value in distance units.
June 30, 2021 at 5:21 pmRameez_ul_Haq
Subscriberthank you so much sir for the detailed clarification. Means alot :)
Just a basic question (and I guess you definitely would had answered it in some other posts), when should we use a bonded connection between two faces in connection (like glue in reality) when I can directly use the shared topology which wouldn't result in any penetration convergence problems, so why would I even go for a bonded contact?
June 30, 2021 at 10:42 pmpeteroznewman
SubscriberThis post has some description: /forum/discussion/5598/difference-between-bonded-contact-and-node-merge
It includes a broken link. I have brought many broken links to the attention of the staff here: /forum/discussion/27032/many-broken-links#latest
Bonded contact is useful if you want to study failure of the interface between layers.Search for Cohesive Zone Model.
If all you want is to have the load transfer from one layer to the next, then shared topology allows the two layers to share nodes at the interface.
Here is another post on Bonded Contact vs. Shared Topology (like Node Merge but better). /forum/discussion/2284/contact-or-shared-topology
Don't forget your own discussion: /forum/discussion/24622/difference-between-shared-topology-and-bonded
That is where you should have posted this question because this reply is completely off-topic for the title of this current discussion, which is all about Frictional Contact. Try to keep your follow-up questions on-topic. If you have an off-topic question, open a new discussion (or find a relevant old discussion).
July 1, 2021 at 9:02 amRameez_ul_Haq
Subscriber,absolutely right sir. My mistake. Although i always ask questions in the relevant discussions which I or someone else has opened.
Title of the current discussion implies frictional contact? I was thinking what we have discussed in this thread was generic; the ideas can be applied to any contact like bonded, frictional, no separation etc.
July 1, 2021 at 10:11 ampeteroznewman
SubscriberBonded contact does not move nodes to reduce penetration, it simply holds the nodes where they are and does no iteration. It is linear.
Frictional, frictionless and rough contact moves nodes to reduce penetration and requires iteration to do that. It is nonlinear.
July 1, 2021 at 10:57 amRameez_ul_Haq
Subscriber,So what you meant to say is that the initial penetration between the contact and target faces will remain constant throughout the analysis for bonded and no-separation?
But there is an option for normal stiffness and penetration tolerance as well in the bonded/no separation contacts, isn't it? Why is that so then?
July 1, 2021 at 12:04 pmpeteroznewman
SubscriberYes, in bonded contact, the relative position of the contact and target nodes is held fixed, if the formulation is MPC, which is my favorite. In MPC contact there is no normal stiffness, since it is a displacement constraint equation. When you change the formulation to MPC, the line items for Stiffness and Penetration disappear. If you are using Bonded Contact to join non-congruent meshes of a single part of a single material, where there is no physical bond in the part, but the solid body was sliced for meshing reasons, you don't want any change in stiffness across the interface, so there is no need to change the normal stiffness. That would be a good place to use the MPC formulation, but you don't have to because the calculation of the default normal stiffness is to use the stiffness of the materials being bonded.
Imagine you have two parts that are adhesively bonded, so there is a significant change in stiffness at the interface, but you don't want to go to the trouble of meshing that adhesive material and making a thin layer of elements to represent the adhesive. Don't you see how useful it would be to type a stiffness value into the bonded contact to represent the flexibility of the adhesive? In that case, you would not use a formulation of MPC. Use one of the other ones that allow the stiffness value to be set deliberately lower than the two materials on either side of the bond.
July 1, 2021 at 4:49 pmRameez_ul_Haq
Subscriber,makes so much sense. Thank you. Can we also expect a penetration if I use any other formulation than the MPC?
Moreover, I can also use a simple spring between the two faces as well, right? (Instead of using the contact between them at all).
July 1, 2021 at 10:26 pmpeteroznewman
SubscriberI don't know about the penetration of bonded contact using other formulations, I only use MPC.
Yes you can use a simple spring between two faces, but how are you going to create 121 springs if you have a 10x10 element mesh on each face? Also, how are you going to modify the spring rate of the 21 springs on the edge compared with the 100 spring that are not on the edge? Furthermore, if the 10 elements along the edge are not uniformly spaced, how are you going to modify the spring rate of each individual spring? Bonded Contact does all that work for you automatically.
If you were thinking of using a single spring, you would need a 6 DOF spring elements, but how are you going to assign the rotational stiffness values? Again, Bonded Contact does it all for you.
July 7, 2021 at 8:04 amRameez_ul_Haq
Subscriber,do the value of the normal stiffness actually represent value of stiffness of the glue (that is used to bond the faces of two separate bodies in reality)? If I already somehow know the value of stiffness of the glue, can I use it directly into my bonded contact? What is the default value used by ANSYS for the normal stiffness (or the default factor used by ANSYS)?
Plus, why don't I have an option of tangential stiffness/torsional stiffness within the bonded contact in ANSYS?
(Talking about the formulations except for MPC).
July 7, 2021 at 10:36 ampeteroznewman
SubscriberNot all
July 7, 2021 at 11:07 ampeteroznewman
SubscriberYou asked why there is a Normal Stiffness for Bonded Contact. I don't use the formulations where that is available, I only use MPC for Bonded Contact but I asked you to imagine how you might use Normal Stiffness. The example I gave was to model adhesive. I would not recommend using contact normal stiffness to model adhesive. I would instead put at least 4 linear elements through the thickness of the adhesive and use the material properties of the adhesive to model the stiffness with known material constants. I suggested it would be possible to replace that detailed model with a contact normal stiffness.
Go to ANSYS Help, Mechanical APDL, Contact Technology Guide and read sections 3.9 below is a section from that:
If you input an absolute normal contact stiffness by specifying a negative value for FKN, you can control the units by using KEYOPT(3). By default, the units of the user-specified absolute normal contact stiffness is FORCE/LENGTH^3. You can change the units to FORCE/LENGTH by setting KEYOPT(3) = 1. This KEYOPT(3) = 1 setting is valid only when a penalty-based algorithm is used (KEYOPT(2) = 0 or 1) and the absolute normal contact stiffness is explicitly specified. Using KEYOPT(3) = 1 is not recommended in conjunction with nodal detection options (KEYOPT(4) = 1 or 2) if any midside nodes exist for theCONTA1743-D contact element. (KEYOPT(3) has different meanings in other situations. For more information, see the description of KEYOPT(3) inElement KEYOPTS.) Note that KEYOPT(12) = 5 makes the contact pair become Bonded Contact.
The issue is how will you obtain the stiffness of the adhesive? I expect you would have to experimentally measure that.
Plus, though you can't set this in Mechanical, you set the Real Constant FKT to specify the tangent contact stiffness factor.
July 7, 2021 at 12:22 pmRameez_ul_Haq
Subscriber,yes you are absolutely correct. I was thinking to experimentally measure the stiffness of the glue. But I was not sure about the units to be used. But you cleared it out that what ever the value I enter, the default units to be used will be FORCE/LENGTH^3.
I made the previous comment because I was confused initially because the ANSYS solver is by itself assuming a default stiffness value and using it for the bonded contacts (except for the MPC). I mean like it can assume anything, but the reality might be different. The glue stiffness that the solver is trying to model and thus assuming can be different than the glue that I am using in the reality. So I was a little bit skeptical that the stress/strain results obtained from the ANSYS might be not as correct near the contact if compared to what we see in the reality. Thats why I wanted to input the normal stiffness value by my own which will represent glue in the reality. But at the same time, I didn't want to dive in the trouble to actually model the glue as a separate structural part for obvious reasons.
"Plus, though you can't set this in Mechanical, you set the Real Constant FKT to specify the tangent contact stiffness factor.", means ANSYS is also assuming it initially but in the ANSYS workbench, we don't have an option to actually play with it although with the contact normal stiffness, we can.
July 9, 2021 at 11:45 amRameez_ul_Haq
Subscriber,and sir, also I am going to ask you one more thing to be clarified. For a frictional/frictionless contact, is there an option to completely remove the penetration convergence between the target and contact faces? I mean if the nodes of the target face and contact face come into contact with each other during the solution, then I want them to apply a displacement constrain between those nodes in contact and work as like MPC. Is it possible to do something like this?
August 10, 2021 at 1:18 pmRameez_ul_Haq
Subscriber,welcome back to this thread.
Decreasing the normal stiffness and at the same time decreasing the penetration convergence tolerance is worst to solve an unconvergence problem due to contact, right?
August 10, 2021 at 1:33 pmpeteroznewman
SubscriberIf the convergence is failing for conditions in that contact, then yes, those two changes are in conflict.
Viewing 27 reply threads- The topic ‘There is too much penetration at ‘x’ contact points of the 3D contact elements.’ is closed to new replies.
Ansys Innovation SpaceTrending discussionsTop Contributors-
3472
-
1057
-
1051
-
940
-
902
Top Rated Tags© 2025 Copyright ANSYS, Inc. All rights reserved.
Ansys does not support the usage of unauthorized Ansys software. Please visit www.ansys.com to obtain an official distribution.
-

Ansys Assistant
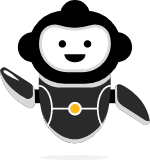
Welcome to Ansys Assistant!
An AI-based virtual assistant for active Ansys Academic Customers. Please login using your university issued email address.

Hey there, you are quite inquisitive! You have hit your hourly question limit. Please retry after '10' minutes. For questions, please reach out to ansyslearn@ansys.com.
RETRY